How does social distancing help prevent the risk of spreading germs and viruses?
05 June 2020
Social distancing - a phrase we are all very familiar with by now - but it's more important than ever to consider how this affects your business, and what you need to consider when ensuring a safe working environment for yourself and staff.
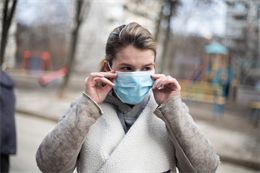
Other measures can be taken to ensure social distancing such as closing or limiting access to public places, having staff work from home, advising the avoidance of non-essential use of transport and prohibit group gatherings.
The World Health Organisation (W.H.O) states that the virus ‘may persist on surfaces for a few hours or up to several days’, which makes high-touch surfaces a particular risk. Consider how your doors open and if they must use a pull handle, then replace them with sanitising door handles that release a virucidal gel upon contact.
Review all other touch points and consider how to convert them to hands free/no touch. Each time a touch point is removed, another risk has been managed away. Using hands-free options when possible, whether that’s installing motion-sensored hand sanitising gel dispensers or knee-operated doors to entrances and exits, paper towel dispensers and waste bins are all methods to reduce the potential for cross-contamination.
Coronavirus spreads quickly. It can live on surfaces for hours and up to several days. Changing rooms are especially high-risk areas due to the often limited space available which can make it even more difficult to maintain social distancing and hygiene practices than in other areas. Introducing multiple single station hands free wash points around the site enables social distancing and promotes more frequent hand washing.
Another way to manage the risk of cross-contamination within the changing room area itself is to spread the distribution of your PPE dispensers so they are at distances greater than two metres around the room. This enable staff to more easily maintain the 2 metre rule. We’ve heard of some innovative approaches to creating space, from moving some PPE dispensers into the hall ways or even converting vacated space into temporary (partial) gowning rooms!
Cleanroom users are familiar with the daily routine of using face masks, goggles, overalls and gloves that provide full body coverage. For our food customers, its worthwhile considering upgrading your PPE for even more body coverage. Some adjustments could include: incorporating gloves sealed to the elbow, full face masks instead of just goggles or supplying a better quality beard snood for everyone to wear. Naturally, increasing the frequency of garment washing will help manage the risk of cross-contamination.
By taking these further measures, you will see a quicker turnover of sterile PPE and reduce the overall risk of infection. The breaks are still needed, smokers still smoke; places where it can be a challenge applying the 2m rule. Consider applying 2 metre markers in communal areas, so the safe distancing is easy to follow and offering additional PPE dispensers so staff can stay protected.
Review how many smokers are on site, and if they can also be safely distanced, temporary shelters may be required. Social distancing can be difficult to practice in production. If changing shifts, creating new space to spread out the production process or reducing the overall amount of furniture isn’t an option, then consider investing in screens to protect staff. We all have to believe this is a temporary measure, so freestanding – or mobile – makes best sense, you can then configure your furniture to create an adaptable space, however things progress.
Other Press Releases By This Company
- 14/02/2023 - Hygienox designed for cleanrooms
- 12/12/2022 - Teknomek End of Year Review
- 11/10/2022 - Vacuum Solutions for Cleanrooms
- 12/09/2022 - Hygienox from Teknomek
- 13/07/2022 - Teknomek: Proud to be ISO 9001 certified since 2013
- 31/05/2022 - Hygienox, from Teknomek: where ISO 14644 comes first
- 16/02/2022 - Don’t hang around!
- 16/02/2022 - Teknomek celebrates appointment of new head of customer service
- 05/10/2021 - “I like to move it, move it”
- 28/05/2019 - Teknomek incorporates Dyson Airblade taps
- 28/05/2019 - Factoring the uncertainties in cleanroom design
- 28/05/2019 - Teknomek’s new tall cupboards elevate hygiene levels
- 15/01/2010 - Teknomek - specialists in bespoke stainless steel fabrications
- 15/01/2010 - Introducing Teknomek