Lab Fit Out – Challenges of Lab Design for Hydrogen Research
12 November 2024
When undertaking a lab fit out project it is preferable to identify any potential challenges as early as possible in the design stage.
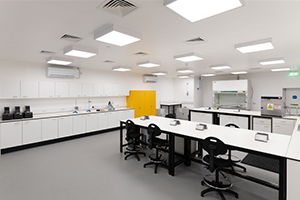
Klick were approached by AFC Energy to upgrade their facility in Surrey where an empty aircraft hangar was to be transformed into 5 technical laboratories.
Their work involves the product development and production of hydrogen energy fuel cells. One initial challenge at the start of the AFC project was to clarify the brief. Klick’s in-depth understanding of LAB DESIGN meant we were able to establish the key requirements for the lab users and highlight any potential issues in order to identify a clear project brief.
Provision of Specialist Gases for Laboratory Fit Out
The use of dangerous materials in the laboratory environment is a particular challenge. As part of AFC’s manufacturing processes they use a range of specialist gases including helium, carbon dioxide and compressed air, also liquid fed and bottle-fed nitrogen, which are considered to be particularly hazardous.
Planning for the provision and connections for these gases formed part of early discussions. The labs are fully sealed and fireproofed which is necessary due to the flammable liquids and equipment AFC use. Klick advised that the facility should be 1/2-hour fire rated, including the glass windows, ceilings & lights, which is a high spec compared to a standard lab.
Laboratory HVAC Requirements for the Fit Out
It was complex to achieve the required environmental balance within the labs.
In general it is best to optimise the design of any HVAC system with a view to minimising the amount of equipment, plant and ductwork required, whilst ensuring an optimum environment is achieved. The AFC labs needed to be fully sealed and it was also necessary to have a system to control LABORATORY VENTILATION and pressure. This required co-ordination with specialist HVAC suppliers and a depth of understanding of the equipment needs of the lab users in order to create ideal laboratory working conditions.
Converting a Building for Laboratory Use
Most old buildings will harbour some latent issues that will complicate the design and construction process. The building selected for the new laboratories at AFC was an outdated aircraft hangar which presented specific challenges. The roof is asbestos which could not be touched or pierced. This meant all services had to run in a new roof cavity and be brought in through the walls. The design necessitated a ‘box within a box’ and the layout was designed based on all services being delivered through the wall cavity. In some cases the location of ducting was critical and the challenge was to avoid specific obstructions around the exterior of the building.
All trades and staff had to briefed to ensure they were aware of the asbestos and compliance with asbestos guidelines.
Managing all the Specialist Trades for the Lab Construction
An additional challenge was co-ordinating so many trades in a relatively small footprint. All trades had to be micromanaged to ensure there was enough space for them to work effectively, avoid any downtime and keep to the programme.
Large mechanical equipment needed to be installed in the roof cavity and to the external areas at the rear. The level of complexity required the contracts management team to draw up a detailed plan regarding any installations or penetrations and communicate this to all trades, to minimise delays on site.
Towards the end of the project when rooms were being finished, we used zonal working to allow multiple trades to work on site simultaneously without disrupting each other. This meant at any one time we could have HVAC engineers, medical gas installers, electricians and floor layers on site at the same time.
The co-ordination of specialist trades such as medical gases or HVAC suppliers and their interface with regular trades, like electricians and plumbers was carefully controlled to allow them to work in tandem with one another.
The Results
In conclusion the original building required a complete upgrade to provide the high spec technical facility necessary for AFC’s work with hydrogen fuel cells.
This was an ambitious project which needed significant input from our design team. Our depth of experience in the field of LAB FIT OUT, which spans over 40 years, has been crucial in co-ordinating this complex project with all the technical features required to support AFC’s business needs.
Feedback from AFC:-
“AFC Energy enjoyed a very positive working relationship with Klick Laboratories. At the initial design stage, they made practical suggestions regarding the layout and lab construction methods in order to achieve all our goals. Klick were eager to clarify our requirements and worked patiently through any grey areas that needed to be defined. The aim was to create a bespoke future ready facility with a controlled lab environment….
Once the brief was finalised Klick took ownership and completed everything efficiently and according to programme. Klick’s team were extremely professional throughout the project and simply got on with the job, they proactively raised any issues for discussion and were flexible in accommodating last minute changes.”
Dan Hamilton, Manager – Failure Analysis, Characterisation, Testing and Simulation, AFC Energy PLC
CLICK HERE FOR CASE STUDY DETAILS
Lab Construction Services Offered by Klick:-
• Mechanical and electrical provision
• Fume extraction
• HVAC
• Specialist gas systems
• Network cabling and data services
• Lighting/Ceilings/Flooring
• Windows/Doors
• Decorating
• Building works
• Furniture & Fittings
• Mezzanine floors
• Partitioning
Other Press Releases By This Company
- 16/12/2024 - Laboratory Furniture – Tips for Selecting the Best Materials
- 26/09/2024 - Laboratory Construction and HVAC Installation Planning
- 03/09/2024 - Lab Design – 6 Top Tips for Laboratory Flexibility