What is Magnetic Particle Inspection? All you need to know
16 December 2024
Magnetic Particle Inspection (MPI), also known as Magnetic Testing (MT), is one of the most commonly used non-destructive testing methods for detecting surface and shallow sub-surface defects in welds, castings and forged ferromagnetic materials including steel, cobalt, iron, and nickel.
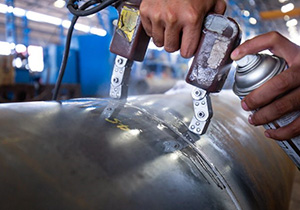
The purpose of MPI is to identify defects in good time in order to prevent premature or unexpected machine failure which can result in accidents, loss of productivity and costly downtime.
What are the benefits of magnetic particle testing?
MPI is one of the most commonly used forms of NDT for a number of reasons:
- Can be performed quickly and portably
- Is relatively inexpensive and doesn’t require stringent pre-cleaning
- Can be performed on large or small objects
- Indication of defects can be seen immediately
- Can be used to inspect components with irregular shapes (crankshafts, connecting rods etc), and on surfaces that have other materials on them
- Identifies surface and near surface defects (areas which concentrate stresses)
- Sensitive enough to detect shallow and fine cracks
There are 2 types of MPI:
1. Dry Magnetic Particle Testing (DMPT): dry particles are dusted onto the surface of the test component as the item is magnetised. This method is well-suited for test materials with rough surfaces
2. Wet Magnetic Particle Testing (WMPT): magnetic particles are suspended in water or oil. This method is more sensitive to flux leakage sites caused by defects than DMPT as the particles are able to be more mobile in this suspended state
How is magnetic particle inspection done?
To perform MPI, the following steps are taken:
- The material being inspected is magnetised
- The magnetic field is transferred through the material. If the current encounters a defect, the magnetic field will be interrupted and spread out from the point of the defect. This is called a ‘flux leakage field’
- Once a defect has been located, particles are then spread over the surface of the material. These particles, either powder form or suspended in liquid as mentioned above, will be drawn to the leakage field. The particles are also often black or fluorescent in colour, making it easier for the inspector to see the defect area
Our MPI service can be used for testing all types of components — from small items such as castings and forgings to inspection on in-service components. We are also able to offer MPI as part of our site services which include vibration analysis (VA) and crack detection (CD) of critical plant machinery. We often carry out VA/CD on impellers for glass furnaces, which assists the Plant’s preventative maintenance program.
Other Press Releases By This Company
- 21/03/2024 - Dynamic Balancing: An interview with our Production Manager
- 12/02/2024 - Correcting unbalance in machinery
- 15/08/2023 - The benefits of Machine Condition Monitoring for rotating machinery
- 16/05/2023 - What is crankshaft balancing?
- 14/04/2023 - What is Dynamic Balancing?