Motion/machine controller provides economic platform for versatile stone cutting machinery
11 August 2010
An all-in-one machine and motion controller is helping an innovative machine builder to set new levels of performance and economy in the stone cutting sector.
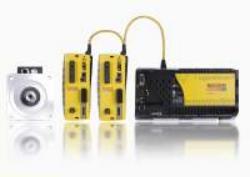
Farnese Australia has been manufacturing stone cutting and polishing machines for 10 years. For its latest product, the Quantum bridge saw, the company switched to an Ethernet-based controller from Baldor. This provides all of the resources required for the real-time interpolated control of four servomotor axes, all of the I/O on the machine, plus an ActiveX interface to the unique Windows user interface that Farnese has developed over many years to simplify stonemasonry. The new Quantum bridge saw provides X, Y and rotational motion for the fast and efficient shaping of stone kitchen and bathroom surfaces, and is believed to set a radically lower price/performance standard compared with existing machines in this market sector. Quantum provides a large cutting area of 3.7 x 2 metres. Four servomotors control the motion of the rotary saw tool - which moves over the worktable on a gantry. Two synchronised axes are used to drive the gantry along the worktable, because of the weight and rigidity of the tool that is required for precision sawing over such a large operating area. The other two axes provide transverse movement along the gantry, and rotational motion of the tool head. The latter axis eliminates any need to reposition the workpiece or tool for changes of cutting direction, and can make angular and circular cuts to radii as small as 10 mm. The four axes employ single-phase Baldor MicroFlex e100 drives driving BSM servomotors. These axes, plus all of the sensors and actuators required on the machine, are controlled by Baldor's all-in-one motion and machine controller, NextMove e100. This controller uses the deterministic real-time Ethernet Powerlink Network. Baldor's controller was selected for three main reasons. The first is economy - as it provides a single-box motion and I/O control solution for this four-axis interpolated machine. The second reason is expandability: Farnese makes a range of cutting and polishing machines and the Powerlink networking standard, and Baldor's controller makes it possible to use the same platform for almost any conceivable new machine or cell - with up to 16 interpolated axes. Baldor's development environment - Workbench - provided the final reason. This no-cost toolsuite is provided with the controller, and includes support for ActiveX, making it easy to interface with Farnese's existing PC/Windows-based user interface. Programming the real-time motion control was made easy by Baldor's Mint language, which offers high-level keywords for the complex movements that Farnese requires, such as angular and circular cuts. Workbench also provides tools that allow Farnese to provide remote support for its machines, allowing diagnostics to be run, drives to be tuned, etc. The user interface is a key feature underpinning Farnese's success in its home markets of Australasia. It makes selection of the right shape cutting process very easy, avoiding much of the risk of operator error. A range of pre-programmed shape cutting sequences are provided to cover common requirements, eliminating the need for skilled operator programming by the kitchen and bathroom surface suppliers that typically purchase these machines. The sequences include ready-to-use templates for the major sink manufacturers, for example. The interface also supports more complex applications, allowing programming using G-code, as well as manual control. Alessandro Farnese of Farnese Australia said "We've used Baldor controllers for many years. The latest Powerlink controller gives us a really versatile platform to help develop our machine building business. There are many performance advantages in this product, but our relationship also benefits greatly from Baldor's strong technical support, and we know that Baldor's worldwide network will help us as we take our next steps and expand internationally." "The NextMove e100 provides a very versatile and economic platform for producing three- and four-axis machines such as those from Farnese Australia," says Jason de Souza of Baldor. "In this case, the multi-axis control capabilities and the I/O that comes as standard provided all the control resources needed, keeping the bill-of-material costs very low. It will also operate standalone, or in conjunction with a PC host, providing great flexibility of application for the small machines sector." Farnese Australia is currently in the process of starting up a manufacturing plant in Vietnam, to help it produce machines for the global market. More information on Farnese Australia and the Quantum machine: http://www.farnese.com.au