Robots Controls Forge Variables and Double Capacity
13 December 2010
Fully automated forging of gas turbine compressor aerofoils, from billet to finished forging, is now being undertaken by Rolls-Royce Inchinnan.
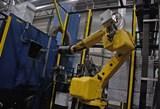
Two fully integrated systems, each with six FANUC Robotics robots, have doubled capacity and removed the inherent variables of the forging process. After illustrating several installations with FANUC Robotics robots working in hot and dusty aggressive environments, similar to forges, Rolls-Royce invested in a single robot to concept several applications. This phase allowed Rolls-Royce to prove that most tasks could be undertaken and the inherent variables of manual forging – consistency of press to press times and heat transfer, DAG (spray die lubricant) cover and volume, and Glass coating (powder form lubricant applied to forging) consistency, tonnage and stroke of press - could be removed. To achieve cost down objectives and remove the variables, the decision was made to develop a fully integrated system to totally automate the process. The business case presented for capital expenditure for total automation was approved on the basis of improved ‘right first time’ – less scrap and doubling of throughput over a 24 x 5 shift basis. The development process illustrated that at the start of a shift an operator would be as fast as the robot but the effect of standing in front of an oven at 1000°C and repetitive actions took their toll with Tack times illustrating a double output from the robot. FANUC Robotics was re-engaged to look at automating the process and developed simulations to allow Rolls-Royce to analyse the process. Each system comprises two key stages in the forging process; pre-forming and final forming taking the product from the billet stage through to a fully finished compressor aerofoil. All equipment was designed, supplied and integrated by FANUC Robotics UK Limited with control of all individual operations, and overall system control managed by the FANUC robot controllers. Loaded trays of pre-glassed billets enter the first stage on a conveyor. A FANUC Robotics M-710iC/50 robot picks up individual billets and places them into a furnace which indexes and presents a hot billet to be removed. The hot billet is then placed in the first die position of a press and the robot releases the billet signalling the press to cycle. When the cycle is complete and the press is open, the robot clamps the sprue and positions the forging into the second die position and again releases the sprue so the press cycle can complete. On cycle completion the robot picks up the forging and places it into a pick up station for the next operation – shot blasting. Tooling at each stage was redesigned specifically for automated operation and Rolls-Royce developed dies to ensure that the forging (or extrusion) was always retained in the bottom die. After the forging is released from the pre-forming press, a smaller robot positioned around the back of the press tool, a FANUC Robotics LR Mate 200iC robot, blows off debris from the dies and spray applies DAG (graphite release lubricant) before the next cycle begins. The DAG operation is key to consistent product quality as excess graphite in the tool can effect the form of the forging. The automation of the DAG process has illustrated a major benefit by ensuring a consistent application. A later addition and part of the systems evolution is the spray application every five cycles of dry ice granules which has been found to be highly effective in removing in process build up of DAG. The shotblasting process is managed by a FANUC Robotics M-20iA robot which picks the forging up and places it under two nozzles that blast sand to clean it. On cycle completion the robot places the billet onto an indexing conveyor that delivers it to the next stage – final forming. An M-710iC robot inverted and mounted on a 3 Mtr linear axis is used to position the forging within the final forming cell which begins with the electro-static application of glassing (release lubricant). The Rolls-Royce development Team found that applying glassing electro-statically eliminated the variables associated with manual glassing and supported the consistency objective. After the glassing operation is complete the M710iC robot takes the forging to the furnace and places it into an indexer and removes a hot forging ready for final forming. The hot forging is placed in the final forming press and the press cycle begins followed by removal on completion. Once again a smaller LR Mate robot is core to achieving consistency at this point by applying DAG automatically after every cycle and dry ice spray after several cycles. The final formed aerofoil is placed into a clipping press by the M-710iC robot and then placed onto a conveyor where it travels through a soak tunnel. On exiting the soak tunnel a FANUC Robotics IR Vision system feeds positioning information to another M-710iC robot which picks up the aerofoil and places it into a tray. Finally when 100 aerofoils have been palletised the full tray is picked up by the robot and positioned into a collection stack to complete the operation. Rolls-Royce is reporting significant benefits from the system - improved efficiency, doubling of capacity, improved quality and improved ‘right first time’. The removal of variables has enabled Rolls-Royce to produce to such a high quality of finish from the multi-stage forge that only a sand blast operation is required. In addition producing a more constant product has resulted in less post forging work required to finish each aerofoil.