Green consumption vs green supply
30 June 2011
The Department of Energy and Climate Change very recently brought in the new the CRC Energy Efficiency Scheme (formerly known as the Carbon Reduction Commitment), which they say is central to the UK’s strategy for improving energy efficiency and reducing carbon dioxide (CO2) emissions, as set out in the Climate Change Act 2008.
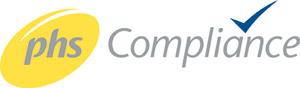
Photovoltaic panels now punctuate our motorways and many organisations invest in solar technology for water heating or power conversion to battery-stored electrical power. This is typically used on a small scale and payback periods are still relatively long, making this form of ‘green’ power supply questionable in terms of financial/commercial viability and hence limited in use, particularly in the UK’s climate.
Meanwhile, on a grander scale, we now have wind generated power thanks to large windfarms either on land or offshore. Many green campaigners champion wind generation and this relatively expensive power trickles onto the National Grid. But it’s not all that ‘green’. The carbon generated in manufacturing and installing each turbine is often overlooked, as is the 100 tonnes of concrete in the foundations of each one. When these turbines eventually reach the end of their life and are decommissioned what will be happening to those previously greenbelt sites, now full of concrete?
This sounds a cynical and damning point of view, but many overlook the real cost and the real impact of so-called green power generation methods in the rush to find and adopt a methodology that comes with good CSR credentials. It’s not that all such technologies are bad or wrong, it’s just a concern that they take the attention and focus from what could potentially have a much bigger impact on reduction of carbon release in the short and medium term; using less power from highly efficient traditional sources.
In other words, before we look outwards we should first look inwards at what we have and what we do.
Changing supply or consumption – where are the greatest CO2 wins?
In the UK our electricity supply should be served at 230V, with a tolerance of plus or minus 10 per cent to take into account local conditions (range of 216 to 253V). This level was set as a result of European Harmonisation in 1995 (see also Statutory Instrument No. 2665 “Electricity Safety, Quality and Continuity Regulations 2002”). However, there is a well-documented national problem of over-voltage and the average electricity supply in the UK is around 242V. Indeed, our records* demonstrate that the actual range varies from just below 200V, up to 260V. Where there is over-voltage there is waste.
Most electrical equipment is rated at 220V and designed to operate happily down to 200V. Electricity supplied at voltage greater than this figure is dissipated in losses as the equipment functions, without enhancing performance. Therefore the common oversupply in delivered voltage is both wasteful in energy terms and financial terms. An example is given in BS7671: “a linear 230V appliance used on a 240V supply will take 4.3 per cent more current and will consume almost nine per cent more energy”. You pay for what you use and you use power at the voltage you are supplied. So it’s very common to be paying for much more voltage than you need or want.
Added to the waste of over-voltage supply is the fact that increased voltage causes heat in the equipment which will shorten its useful life. “A 230V rated lamp used at 240V will achieve only 55 per cent of its rated life” (BS7671). This means that there’s a capital cost to over-voltage supply as machinery and equipment requires replacement more rapidly than if it were used at lower voltage (remember that most can operate comfortably at 200V). This could, for example, impact the rate of depreciation applied to capital assets – something every director would be interested to learn.
By controlling and reducing the voltage distributed around your site you can reduce your power consumption, thus reducing associated carbon emission, saving money on energy usage, reducing equipment maintenance costs and lengthening the life of all equipment on site and improving the return on capital investment. It’s a worthwhile and convincing recipe of benefits!
Voltage Optimisation and other proven techniques
The term for this energy saving technique is Voltage Optimisation (also termed ‘voltage correction’ or ‘voltage reduction’) and this well-established and proven technique yields average energy savings of around 13 per cent. In fact savings of up to 25 per cent are possible. The optimum voltage for a site will depend upon the equipment used on the site and the savings will vary accordingly.
It is true that voltage reduction does not work on all types of load – for example temperature controlled heating will not yield energy saving by controlling voltage supplied – but this technique, pioneered in Japan and now growing in adoption in the UK, is very successful for most sites.
Efficiency savings don’t stop with reducing voltage of power consumed, in fact ‘easy wins’ can be achieved by good maintenance programmes for site equipment and using the most efficient motor drives to power that equipment – inverter drives for example. Air conditioning plant can be a good place to improve power efficiency and positively impact consumption, as can choice of lighting, given its high usage on any site.
It is reported that global lighting emissions account for three times more CO2 than that of aviation and the International Energy Agency claims that a global switch to energy efficient lighting would cut the world’s electricity bill by 10 per cent. As a broad national average, in the UK, lighting makes up around 10 to 15 per cent of electricity bills.
Power Factor Correction (PFC) is another consideration for power efficiency, with the aim of getting what you pay for. The power factor of a system is the ratio of the ‘real power’ flowing to the equipment (the capacity of the circuit) to the ‘apparent power’ (the current and voltage of the circuit). Unity or optimum therefore is ‘one’, or ‘pure power’. However, in most cases the apparent power will be greater than the real power, with KVA going in losses, creating a power factor below ‘one’. Utility suppliers supply volt-amperes but bill in watts and power factors below ‘one’ require more than the minimum volt-amperes necessary to supply the real power (in watts), which increases generation and transmission costs. Buildings often operate at a power factor of around 0.8, showing that power is being wasted; surplus is paid for but lost.
PFC equipment brings the power factor of the site as close to unity (or ‘one’) as possible. Capital expenditure on such equipment can be realised in less than three years, a similar pay-back time to voltage optimisation. Both of these techniques utilise well established technical theory and technology.
Powering a whole hospital wing from waste energy
As an example of the scope and scale of PFC, a good story relates to a hospital that called on our expertise due to a major issue on its development plans to build a new wing. The power factor of the existing site was so low that there was insufficient power supply available to support the new wing. The option the hospital faced was approaching their regional power supplier and funding the delivery of a whole new supply to the site. This would have meant serious capital outlay, not planned for or budgeted for in the development project.
Having assessed the site’s power usage and established how bad the existing power factor was, we used voltage optimisation and PFC to make power savings significant enough that the new wing could be served, effectively being supported by the power that had previously been wasted. Not only did this avoid the major outlay on a new power supply to site, but also meant that the new wing created a negligible running cost in terms of power.
Application of these techniques is still growing but the science behind them is well proven. Another power efficiency enhancement is filtering out electrical harmonics, or current and voltage waveforms at a higher frequency than the main supply. These harmonics are created by non-linear loads such as computer equipment and the effect, termed Total Harmonic Distortion (THD), can cause damage to sensitive equipment and reduce the efficiency of electrical loads. By preventing the generation of harmonics, greater efficiency can be achieved and once again power consumption can be reduced.
In summary
Albert Einstein once said “Why does this applied science, which saves work and makes life easier, bring us so little happiness? The simple answer runs: Because we have not yet learned to make use of it.” For many organisations this is true in terms of electrical efficiency. The technology exists and here we’ve considered just some of the techniques; voltage optimisation, power factor correction and filtering harmonics. Added to this collection are the more straightforward concepts such as good electrical equipment maintenance and choice of low energy lighting, for example. These are so simple to understand and apply that every organisation should be capitalising on these savings.
The key to this argument is that more can be achieved and more saved – both financially and environmentally – by applying known power saving techniques, than by spending time and money on the technology touted as ‘green’. Real green won’t come quick enough from changing supply; it has to come from changing consumption.
*PHS Compliance is the largest provider of periodic installation test reporting and routinely measures and documents incoming supply, assessing around 38,000 sites each year.
Other Press Releases By This Company
- 15/03/2012 - Electrical Wiring Safety Testing – A Matter of Life and Death?
- 15/03/2012 - Regulation, litigation, prosecution - these are worrying times for landlords
- 30/06/2011 - Compliance remedial gap - the danger zone
- 30/06/2011 - ‘Mr Compliance’ launched by PHS at the Facilities Show
- 30/06/2011 - Hotel fire deaths prompt safety warning from Compliance
- 29/06/2011 - Compliance enhances service with new structure
- 28/06/2011 - Workplace safety specialist PHS Compliance renews UKAS accreditation