As simple as falling off a bike!
13 February 2008
Horne explain the design process for their new thermostatic tap for healthcare applications - the Optitherm.
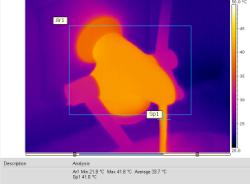
It is said sometimes that the bicycle was the last great invention that everyone understood.
Around 1839 Kirkpatrick Macmillan, widely regarded as the father of the modern, rear-wheel-driven bicycle, is alleged to have pedalled his velocipede “of ingenious design” into Glasgow - to the astonishment of the locals. Later the story emerged of his five-shilling fine for causing the first bicycle accident; and ever since then the world of technology has been getting more complex and out of the reach of the average maintenance technician.
In the same part of the world, the lowlands of south-west Scotland, Horne Engineering has been manufacturing thermostatic mixing valves for nearly a century. Beginning in 1909 Alexander Horne cast steam-trap bodies in his own foundry and later built his own expanding thermostat elements from gutta percha and precision drawn copper tubing. This paved the way for the first thermostatic mixing valves (the semi-blender, as he called it). Although Horne and many other mixing valve manufacturers now use wax-stat technology, 98 years of experience to draw on now gives Horne's engineers a unique insight into what distinguishes a well-engineered and carefully optimised mixing valve from some of the low-tech imports available today.
Indeed, there is a place for modern technology; though many would also say there is a place for specifying dependable and proven technology. Few would argue that electric cars are likely to be commonplace on the roads of the future, but who still has a Sinclair C5? Underfloor heating systems are becoming all the rage, but they are a far cry from the unreliable and uncontrollable systems of the sixties and seventies. The first vacuum cleaners would have found it very hard to compete with a deft pair of hands and a brush and shovel; yet the technology came to maturity during the middle part of last century and we have seen vast sums put into the development of vacuum cleaners in recent years. During this time, MacMillan's humble bicycle has been slowly but surely developing as advances in material technology give us lighter frames and suspension; and ingenious design allows index-shifting gears, hydraulic disc brakes and much more.
With this in mind, Horne has watched the sanitary ware market with interest and the latest developments for panelling systems and touch free taps. They decided to leave the expense and complexity of this embryonic electronic technology in favour of drawing on their depth of expertise to develop a traditional thermostatic tap which provides many hygiene advantages, yet also has the ease of installation and maintenance of the traditional technology. Their latest product, the Horne Optitherm requires no electrical connections; no access behind the panel for servicing and has all the reliability to be expected from Horne. After all, Horne had no wish to compromise a near-century long heritage of building simple but highly refined (and widely regarded as best-in-class) thermostatic controls. Modern polymer technology and computer aided design and manufacture would also be available to allow things that were not possible at sensible cost only a few years ago; yet retaining that elusive quality that any budding technology student – even one from MacMillan's day - could dismantle it to find out exactly how it works (Horne don't recommend this, though).
So how does one go about developing a feather-light, streamlined, index-shifting, drop-handlebarred, yellow-jersey-winning thermostatic tap?
The answer lies in the creation and adherence to a stringent specification. The fulfilment of the specification for the Horne Optitherm was an unforgiving task. From the outset of the project, Horne's new-product development team was convinced that the new tap should exceed the capability of any existing thermostatic tap on the market. It was also quickly realised that to overcome certain criteria, a clean-sheet of paper would be required.
Certain recent legislative requirements also had to be taken into account. For instance, HSE now require that 2 people lift some IPS panelling due to its awkward shape and weight. Hinged panels are a possibility to overcome this, but create their own problems. They tend not to fit as well as they might, and also leave security issues, not to mention the possibility of dirt ingress from the service chase. Bringing the whole tap into the room, complete with its isolation valves, fine-mesh strainers and check-valves seemed the only logical solution. This has the added advantage of compliance with HTM 04-01 Part B, which states that water becoming stagnant in long pipe-runs can be problematic (para 5.9). Bringing the tap into the room minimises the length of the warm water pipe runs.
However the HGN ‘Safe Hot Water and Surface Temperatures’ require that hospitals have no exposed pipework or any surface at more than 42°C within reach of the patient. Bringing the mixing valve and its ancillaries into the room necessitated bringing some of the hot water pipework into the room also. This would cause some serious issues and something would have to be done to prevent this very real danger. To combat this, Horne developed a unique double-entry sleeved spigot arrangement, which prevents the surface temperature from rising near to the hot water service temperature (see photo inset). This has the advantage that the tap fits into one hole in the panel, preventing the situation with traditional bib taps where cleaning cloths and other sundries are stored in the gap formed behind the tap and between the two pipes. It also makes cleaning easier generally.
Moreover, bringing more ancillaries into the room yields some other problems of its own. Strainers and check valves require access, as does the thermostatic mechanism. These parts must not be easily accessible to patients, especially in secure units. However if they are inaccessible to patients, they will necessarily require tools to remove them. Tools generally cause burring or damage to the metal that they interface with and therefore require a smooth and impenetrable cover to protect patients. Unfortunately, this type of cover tends to be impenetrable neither to dirt nor to vandals; and the sight in a public washroom of taps with the centre-caps picked off and the recess filled with disgusting wet sludge is quite a common one. To overcome this problem, the Optitherm was designed such that all of the components requiring maintenance are located under a single bottom cover. This cover is formed from a precision pressure die casting and has no protruding features or dirt-traps. The cover is screwed on tightly at commissioning with a strap-wrench and is therefore impenetrable to anyone without a strap-wrench. Because it is made of metal and not plastic, thermal cycling and creep does not loosen it, and the tap remains secure throughout its life. The lever endcaps were designed in a similar way – these being made in robust 6063 grade aluminium, with an irridescent and attractive colour anodised finish in red and blue. These endcaps are screwed on tightly with a bespoke friction tool, and are therefore also secure from unauthorised hands. These features make for a completely smooth exterior of the tap, which is much more readily cleaned than those previously on the market.
The traditional technology applied by Horne has many attractions over the newer electronic technology, not only in terms of reliability, but also low cost, ease of commissioning and no requirement for multiple trades to install it. However there is an obvious advantage in touch-free technology in terms of reducing spread of HAI. In response to this, Horne introduced a double-lever arrangement (patent applied for). In this implementation, there are a pair of levers on each side of the tap, thus the tap can be turned on using a thumb against the short lever, and turned off using an elbow against the long lever. This means that the cleaned arm never touches the short lever, reducing the spread of infection. Moreover, as the levers move vertically around a horizontal axis, the arm action is more ergonomically comfortable than with standard lever taps and reduces discomfort caused by water dripping down the forearm.
The Horne Optitherm provides a wealth of other features such as separation of hot and cold supplies, thus allowing the use of the Optitherm to provide drinking water where the supplies are potable. This reduces the number of different tap variants required on a ward, while other features like the torque release device on the levers prevents lever breakage at the hands of ham-fisted users or abusers
Whether to go for existing, proven technology, or leap into the future with new technology is a balancing act that many specifiers have to do, not least with regard to taps. It is good to note that in the TMV field at least, one company is still optimising the traditional solutions, while we wait for the new technology to come to maturity.