Robot provides fast solution for delicate life-science assembly task
14 October 2011
Carclo Technical Plastics has successfully achieved production validation for the delicate assembly of a new diagnostic life-sciences product.
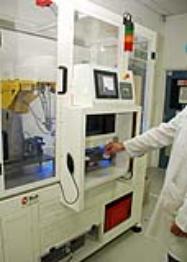
Carclo Technical Plastics has successfully achieved production validation for the delicate assembly of a new diagnostic life-sciences product. An impossible task to perform manually, a small six axis FANUC Robotics robot is used to assemble, and in process check, each component. Specialising in contract manufacture for the medical, optics and electronics industries, Carclo Technical Plastics injection moulds the main body of a multi-compartment cuvette and, adding value for its customer, performs an assembly operation before delivery. Engineered by plastics automation specialists Hi-Tech Automation, a delta configuration robot, the FANUC Robotics M-1ia robot, was selected for the application. Required to handle a weight of less than 5gm, the 1Kg payload M-1ia presented the most suitable solution. Currently the assembly cell has been developed as a stand-alone cell with manual loading and unloading, of the cuvette, to an indexing turntable. As production levels ramp up, the process may be made leaner by integrating the assembly cell with a robotically enabled moulding cell. The component assembled to the moulding is a flexible filter strip delivered to the robot by a feed roller and cutter. A camera positioned in front of the moulding measures the position and size of the filter and feeds back corrective dimensions to the feed roller / cutter to correct when required. Alan Hogan, Manufacturing Engineer at Carclo Technical Plastics, explains, “The FANUC Robotics M-1ia robot does more than just place the filter into the moulding; we use the full flexibility of its six axes to actually manoeuvre the part into place. Additionally the robot’s controller is controlling the whole cell and in particular a seventh axis which controls the dimension of the part. “The vision system is integral to the controller and allows the robot to effectively adapt its programme by controlling the seventh axis. The M-1ia robot allowed Hi-Tech Automation to design a highly compact cell – weighing in at only 17Kgs and just 421mm wide the robot takes up no more room than a human operator working on a conveyor line. A removable stand ensures that the M-1iA is easily integrated into the cell or removed for maintenance. Control of the entire cell is through the FANUC Robotics intelligent R-30iA controller with integrated functions including iRVision, Robot Link and Collision protection. In the event that the robot is integrated into the moulding cell the camera would be located into a housing provided in the robot body to position a camera above the wrist of the M-1ia. FANUC robots are currently used in Carclo’s existing moulding facility in Mitcham, Surrey, where a FANUC Robotics M-10ia demoulds a similar component while two LR Mate robots pack the component into trays. Alan Hogan continues, “We now use six axis robots rather than Cartesian unloaders because they are much more flexible and cost effective. Hi-Tech Automation, in their role of FANUC Robotics Strategic Partner for plastics applications, has come up with some innovative solutions to our needs including the operator pendant we use which makes resetting the arm a simple task requiring minimal robot knowledge.”