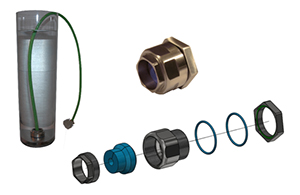
25 July 2019 | Trantec Solids Handling Ltd
Trantec develop new CIP washdown features for their Screw Feeders
For over 23 years, Trantec has risen to many challenges within the powder handling industry.
Recently we were contacted by a customer who needed help with the ‘wash-down’ procedure of their metering feeders used in a food application. With extensive knowledge and expertise in the design and manufacture of metering feeders or screw feeders, Trantec was the obvious choice to assist with their project.
Today’s food hygiene requirements can be challenging, thorough cleaning of equipment and clinically clean contact surfaces are essential to avoid contamination of food and control allergens. Due to the ever-changing demands in Food Hygiene specifications, our customer is required to clean their equipment using a clean in place wash down process. Our powder feeder needed upgrading to meet this challenging specification.
As standard, Trantec’s metering feeders include IP55 rated cable glands, which meant the seal arrangement/insert was not suitable for this type of ‘CIP wash down’ procedure. We needed to source a part that was not only to the IP rating required, but that also fit our machine exactly, we started looking for an alternative cable gland and sealing system for our motors.
During our search, we soon found that this type of cable gland did not exist and for a custom-made part, a premium price and long lead time would ensue. Research on methods of sealing the motor had the same disappointing results. Servo motors for washdown environments come with a premium price tag. Stainless steel motor bodies are expensive and rarely off the shelf components. As Trantec operate a policy of continual design and development, we decided to keep our existing carbon steel servo and enclose it in a stainless steel case and design a cable gland to meet the standards required at a much more sensible price.
The biggest challenge came with designing a cable gland to accept a large, pre-wired D type connector making up a part of the encoder system for the servo motor which drives the auger screw. Trantec has embraced servo technology with our Metering Feeders for over ten years. Servo Motors have a performance way beyond traditional AC motors and exceed DC motors by an ever-increasing factor. Constant torque coupled with precisely controlled rotation and vast speed range makes a servo motor ideal for accurate powder metering and dosing. Trantec also offers machines with traditional AC or DC motors where these better suit a particular application.
Exhaustive tests were conducted on the servo at varying loads to determine the temperature rise and thermal characteristics across the motors operating range. A prototype enclosure was designed then manufactured in our own fabrication shop, and the tests repeated with no significant change in the thermal parameters.
Turning to the cable gland and using the latest CAD technology, Trantec’s experienced design team developed a 3D model of our new cable gland. With a casing made from 316 stainless steel and seal inserts made from blue metal detectable silicone, we then used our CAM (computer aided manufacture) technology to produce prototype parts with our in house CNC machine tools. From concept to prototype in a matter of days, the new cable gland was now ready to be tested.
We took a 5-litre Perspex cylinder and bored a hole in the bottom, the same size as one of the cable holes in our metering feeder. We then fed the cable through the newly developed cable gland and seal arrangement and attached it to the bottom of the cylinder. We then filled it with water and left it. Over a period of 4 weeks, we regularly checked the cable gland and found that it was water-tight. Indicating we were not only successful in achieving a rating of IP65, but we had actually obtained a rating of IP68.
Our customer was happy in the knowledge that they now had a reliable machine that could be ‘washed down’ to their specific requirements, however, they also needed to quickly strip and clean the machine between campaigns. Stopping a machine to change over materials costs money, and downtime must be kept to a minimum, therefore quick release, easy-clean features were included.
As Trantec’s metering feeders are modular in design, we can offer a range of add-on components and configurations to provide ‘tool-less’, strip down. Interchangeable machine parts allow our customers to have two or more component sets. One set can be in operation while the second or third are being cleaned and readied for refit. Significantly reducing downtime due to cleaning, Trantec Feeders can be disassembled and reassembled in less than five minutes by operators.
While modular in design, our feeders are based on Trantec’s core powder metering technology without compromise to quality or build. From fine powders to large pellets, our precision materials dosing technology ensures accurate metering at a constant volume of +1% to + 2% typically, suitable for all industries including, food, pharmaceutical, chemical, plastics and environmental.
For more information, please contact us on 01282 777566 or visit us at www.trantec.net.