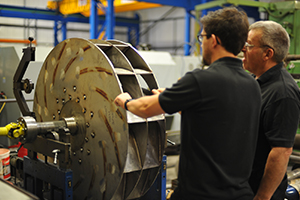
21 March 2024 | WDB Ltd
Dynamic Balancing: An interview with our Production Manager
Balancing your machinery, whether it’s static or dynamic, is key to eliminating common performance problems.
These problems often include vibration, noise, and heat. Eliminating these will consequently extend your machinery’s lifespan, improve accuracy, avoid premature system failure, and unexpected downtime and ultimately save you money.We spoke with our Production Manager, Mem, who explained the importance of dynamic balancing for rotating components of your machinery to result in less downtime and more efficient functioning.
Why is the balancing of rotating components necessary?
All rotating machinery, due to dynamic forces exerted on supporting components, requires balancing. Unbalanced components can produce excessive vibration, resulting in noise, wear and tear of bearings and structural damage. It’s worth noting that vibration will always be part of any machine that rotates, and some vibration levels can be acceptable. Instead of trying to get rid of all vibration, achieving machinery balance as far as possible is what we aim for. Reducing excessive vibration through dynamic balancing ensures the machine is running smoothly, preventing premature system failure.
What are the main benefits of balancing?
Some benefits of balancing include reduced vibration, noise, wear and damage on bearings and associated plant machinery. The efficiency of machinery will also be improved due to less loading on bearings as well as improved reliability, less risk of unexpected breakdown and costly downtime… all saving your money in the long-run.
What types of machinery and industries benefit from balancing services?
Without exception, all rotating machinery benefits from balancing services. To name a few, rotating machinery includes centrifugal fans, electric drive motors, machine spindles (CNC machining center), machine tools, print rollers and agricultural rotating machinery. Industries could therefore include aerospace, motorsport, processing, waste processing and management, energy generation and agriculture.
What are the different types of balancing?
It’s generally understood that static balancing takes the ‘drop’ out from a rotor and is primarily used on narrow discs. However, in some sectors, static balancing is also understood as ‘single plane’ dynamic balancing meaning there is only one correction area or ‘plane’. In terms of dynamic balancing, the machinery must always be rotated at speed to identify unbalance and is corrected using the multiplane correction method. The main difference is that dynamic balancing can also be carried out using a single plane correction area and that the rotor being balanced must be rotated at speed.
What else can cause vibration in machinery?
Unbalance is not the only cause of vibration and if you’ve had your machine balanced and it’s still suffering from excessive vibration, it could be down to a number of reasons. This can include (but isn’t limited to) shaft misalignment, worn bearings, loose structure, a bent, worn or damaged shaft, resonance or electrical frequencies. If your machinery has been balanced but is suffering from excessive vibration, this is where we would recommend vibration analysis to identify and pinpoint the cause of vibration in order to take remedial action.
Get in touch to speak with our team about specialist dynamic balancing services