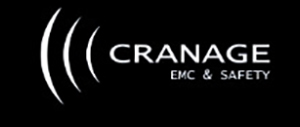
15 October 2024 | Cranage EMC & Safety Ltd
What happens during a product safety assessment at Cranage EMC and Safety?
Depending on the complexity of a product, a full product safety test can take between one to several weeks.
There are many different tests that are performed during a product safety evaluation, and these tests are detailed in a product safety standard that is relevant for the device under test.These tests define how the product is evaluated for product safety to ensure that the product is safe in normal use and fault conditions.
Some of the most common tests include:
1. Dielectric strength test: This test measures the insulation properties of the product by applying a high voltage to the product and checking for any breakdown in insulation. This test ensures that the product has sufficient insulation between different parts of the circuit provided by creepages, clearances or solid insulation.
2. Touch current leakage test: This test checks for any current leakage from the product, which can pose a shock hazard to users. This test ensures that anyone touching or using the product in normal use of fault conditions does not receive an electric shock.
3. Earth bond test: This test ensures that the product's grounding system is properly connected and can safely conduct excess current in the event of a fault. This is tested normally from the inlet or earth point entering the product to parts that are earthed for safety reasons, this is important not just for safety of accessible metal parts but for EMC purposes.
4. Overload test: This test checks the product's ability to withstand overloads without overheating or causing damage. This can involve stressing components such as transformers or even motors ensuring that in these conditions excessive heat generated by these components under test do not cause an electrical or fire hazard
5. Insulation resistance test: This test measures the resistance of the product's insulation to ensure the material used in the construction of the product such as cables have the adequate insulation for the type of circuit.
6. Temperature rise test: This test measures how much the product's temperature rises under normal operating conditions to ensure it does not exceed safe levels. These tests are performed under normal and fault conditions such as cooling fan stopped. Also tests are performed at the maximum declared ambient conditions to ensure the components and surfaces do not exceed the maximum limits.
7. Flammability tests: This test ensures that any material within the product such as enclosures, current carrying insulating parts, terminal blocks etc have the required fire retardancy not to combust or propagate flames. This ensures that any faults that generate heat will not result in a fire.
8. Component evaluation: One example is fuse rupture testing, if a product relies on a fuse for protection then it will need to be assessed for its suitability. This is typically done to determine the point at which a fuse will break or fail when a high level of current passes through it. This type of testing is crucial in ensuring that any over currents within the circuit blow the fuse protecting a potential hazard.
These are just some of the physical tests that Cranage perform in its UKAS laboratory as part of a product safety assessment. Our engineers are also able to perform on-site testing for machinery that is large or in-situ.
Get in touch with our team to discuss your product safety testing, and how we can help you.