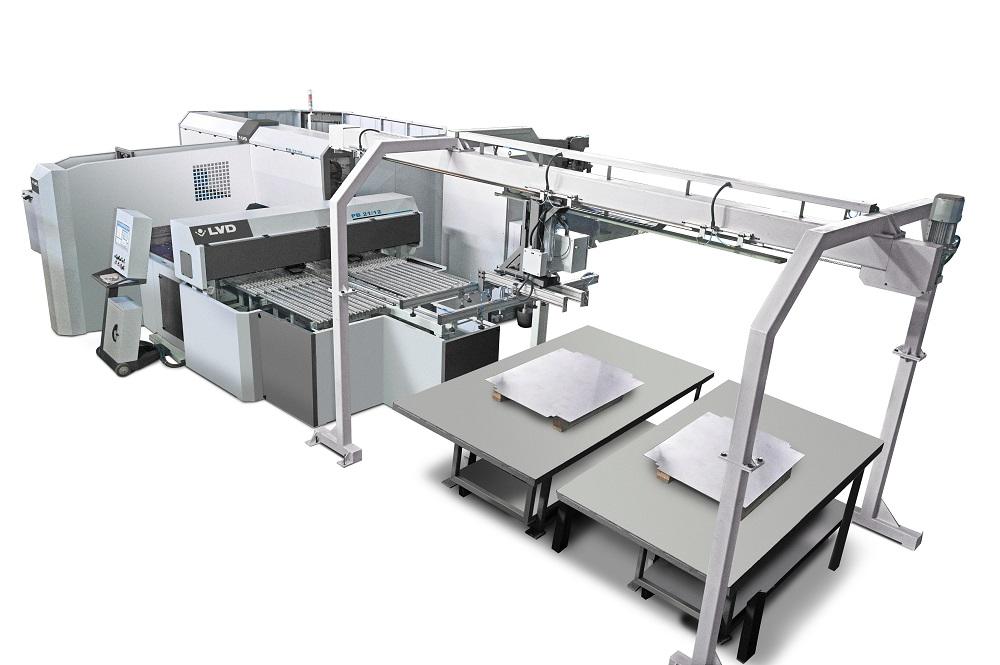
04 February 2025 | Axe & Status Machinery Ltd
The Future of Metal Fabrication: Innovations in Panel Bending Technology
Discover the latest advancements in panel bender technology shaping the future of metal fabrication. Learn about CNC integration, AI-powered solutions, robotic automation, and sustainable designs driving precision and efficiency in the industry
Metal fabrication has come a long way, and the industry continues to evolve at a rapid pace. At the heart of this evolution lies the panel bender, a groundbreaking tool that has transformed how we shape, cut, and bend metal sheets. From small-scale manufacturing to large industrial applications, innovations in panel bending technology are driving the future of precision, efficiency, and versatility in metal fabrication.In this blog, we’ll explore the latest advancements in panel bender technology, its applications, and how these innovations are setting new benchmarks in the metal fabrication industry.
The Basics of Panel Bending Technology
A panel bender is a specialized machine designed to bend metal sheets with extreme precision. It works by applying force to a metal panel, deforming it into a specific shape or angle. Unlike traditional press brakes, panel benders use automated systems to achieve consistent and repeatable results.
Key features of a panel bender include:
Automated Bending Blades: The machine's blades move up and down to bend panels at precise angles.
CNC Programming: Computer Numerical Control (CNC) allows operators to input specific measurements for custom bending projects.
Efficiency: Panel benders streamline the bending process, reducing manual effort and increasing output.
Why Panel Benders Are Essential in Modern Metal Fabrication
The demand for metal bending is growing across industries such as automotive, aerospace, construction, and electronics. A panel bender is indispensable in meeting this demand for several reasons:
Speed and Efficiency
Panel benders significantly reduce the time required to bend multiple panels compared to manual or semi-automated methods. With automation, manufacturers can produce high volumes without sacrificing quality.
Precision and Consistency
A panel bender ensures every bend is accurate, reducing errors and waste. For industries like aerospace, where precision is critical, these machines are a game-changer.
Versatility
Modern panel benders can handle a wide range of materials, from thin aluminum sheets to thick steel panels. This versatility makes them ideal for diverse applications.
Cost-Effectiveness
Although the initial investment in a panel bender may be high, the long-term savings on labor, material waste, and production time make it a cost-effective choice for manufacturers.
Innovations Driving the Future of Panel Bending Technology
With advancements in technology, the capabilities of panel benders are expanding. Here are some of the most exciting innovations shaping the future of panel bending and metal fabrication:
1. CNC Integration for Advanced Automation
Modern CNC panel benders allow manufacturers to program intricate bending sequences, ensuring flawless execution every time. CNC technology reduces the margin for error and enables operators to tackle complex projects with ease. Features such as real-time adjustments and 3D visualization further enhance precision and control.
2. Robotic Automation
Robotic arms are now being integrated with panel benders to fully automate the bending process. These robots can load and unload metal sheets, position them accurately, and handle repetitive tasks, freeing up human operators to focus on higher-value activities. The combination of robotics and panel benders improves workflow efficiency and minimizes downtime.
3. AI-Powered Bending Solutions
Artificial intelligence (AI) is revolutionizing metal fabrication. By analyzing data from past projects, AI-powered panel benders can predict optimal bending parameters, reduce setup times, and prevent material defects. AI also enables adaptive learning, allowing machines to improve their performance over time.
4. Sustainability and Energy Efficiency
Sustainability is a growing concern in manufacturing, and panel bender technology is keeping pace. Newer models are designed to consume less energy while delivering the same, if not better, performance. Manufacturers are also incorporating recyclable materials into their machines, contributing to a greener future.
5. Compact and Modular Designs
Space is often a constraint in workshops and factories. To address this, manufacturers are developing compact panel benders that require less floor space without compromising on capabilities. Modular designs also allow for easy upgrades and customization.
Applications of Modern Panel Benders
The versatility of panel benders makes them suitable for a wide range of applications, including:
Automotive Manufacturing: Creating precision parts for vehicles such as door panels, chassis components, and brackets.
Aerospace Industry: Producing lightweight yet durable components for aircraft.
Construction: Fabricating metal panels for buildings, roofs, and structural reinforcements.
Electronics: Crafting enclosures and panels for electronic devices.
As panel benders become more advanced, their applications are expanding into new industries, further solidifying their role in modern manufacturing.
The Benefits of Investing in Advanced Panel Bending Technology
For manufacturers considering an upgrade to their fabrication processes, investing in the latest panel bender technology offers numerous benefits:
Increased Productivity: With faster cycle times and reduced manual intervention, panel benders boost overall production rates.
Improved Product Quality: Precise bending ensures that products meet the highest standards, enhancing customer satisfaction.
Reduced Labor Costs: Automation reduces the need for skilled labor, lowering operational costs without compromising quality.
Scalability: Advanced panel benders are equipped to handle both small-batch and large-scale production, offering flexibility for growing businesses.
Challenges and Future Trends
Despite their advantages, panel benders face certain challenges, such as high initial costs and the need for skilled operators to manage complex programming. However, ongoing innovations are addressing these challenges, making panel benders more accessible and user-friendly.
Looking ahead, we can expect:
More Affordable Models: As technology becomes mainstream, the cost of advanced panel benders is likely to decrease.
Cloud Integration: Remote monitoring and operation of panel benders via cloud platforms will enable real-time updates and diagnostics.
Customization Capabilities: Future panel benders will offer greater flexibility to accommodate unique designs and materials.
Conclusion
The panel bender is undoubtedly at the forefront of metal fabrication technology, driving efficiency, precision, and innovation. With advancements in CNC programming, robotic automation, and AI, panel bending is becoming smarter, faster, and more sustainable.
As industries continue to demand high-quality, cost-effective solutions, panel benders will remain a cornerstone of modern manufacturing. Whether you’re in automotive, aerospace, or construction, investing in cutting-edge panel bending technology is not just an upgrade—it’s a step into the future.