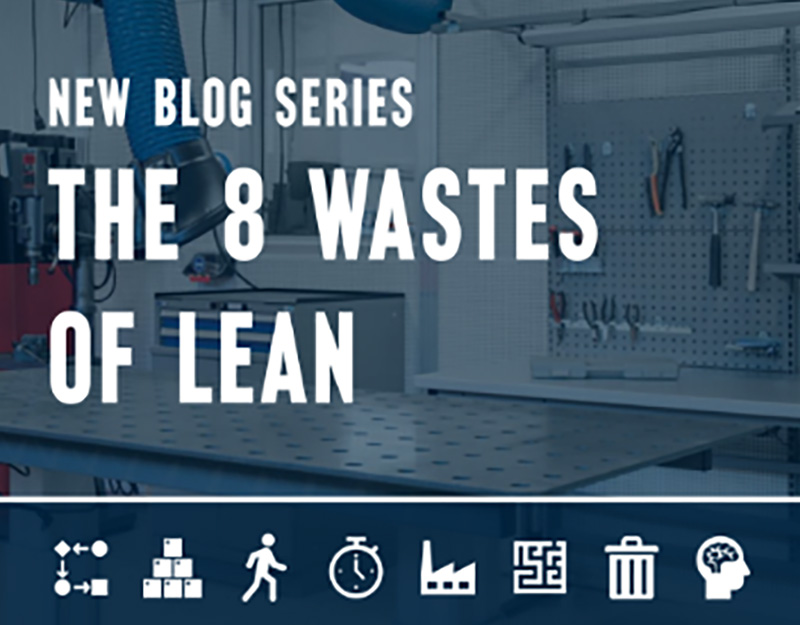
12 February 2025 | Gigant UK
The 8 Wastes of Lean Manufacturing: A Practical Guide to Smarter Workflows
In the fast-paced world of manufacturing and production, waste is the silent thief of time, resources, and profits. Find out more in our 8 Wastes blog series.
In any manufacturing or production environment, waste isn’t just about physical scraps — it’s about inefficiencies that quietly drain your time, resources, and profits. The 8 Wastes of Lean Manufacturing identify key areas where inefficiencies occur.
By understanding and addressing these wastes, businesses can streamline workflows, reduce costs, and create a more productive and organised workspace.
In this guide, we’ll provide an in-depth overview of the 8 Wastes, explain their impact, and show you how to address them effectively. Whether you’re new to Lean principles or looking to refine your current processes, this is your ultimate starting point.
What Are the 8 Wastes of Lean Manufacturing?
The 8 Wastes, also known as "Muda," represent processes or activities that do not add value to the final product. These inefficiencies can appear in workflows, production lines, or even in administrative tasks.
Here’s a breakdown of each waste, its impact, and examples to help you identify it in your operations:
1. Transportation Waste
Transportation waste occurs whenever materials, tools, or products are moved more than necessary within a workspace. This inefficiency often stems from poorly designed layouts or workflows, leading to unnecessary trips between storage, workstations, and other areas.
The effects of transportation waste extend beyond wasted time — it can also increase labour costs, create bottlenecks in production, and even lead to accidental damage to materials during transit.
For example, a production team might unknowingly spend hours each week walking back and forth between a distant storage area and their assembly stations. These repeated trips not only drain productivity but also increase wear and tear on equipment used to move materials. Addressing transportation waste is essential for creating a streamlined and efficient workflow.
Examples of Transportation Waste:
Moving materials long distances between storage and workstations.
Over-reliance on manual handling for transporting heavy or delicate items.
Poorly positioned storage areas that require extra trips during production.