Company details for:
Apollo Plastics Ltd
62 St James Street,
Hull,
HU3 2DH,
United Kingdom
Quick Links:
Products / Services

The Design Process
Our team will discuss a wide variety of design cues to commence the process from a discussion or a simple line drawing, a wooden pattern for prototypes through to a finished production tool.
Apollo Plastics pay close attention to detail during the design phase which promotes a reliable high quality final product and a smooth production process. We have the creativity, the knowledge, experience, and the commercial sensitivity to be a strong partner for all aspects of your new product development.
We're always happy to discuss your plastic vacuum moulding requirements. If you have a project to complete or a problem that needs solving please contact us.

Tooling & Materials
Depending on the application and structural properties required we can manufacture in a range of materials, including ABS, HIPS, HDPE, and more. Production tooling includes vacuum and pressure forming, CNC trim fixtures with suction clamping. We can also process specialist moulding materials such as chemical resistant, flame retardant, antibacterial and high strength plastics.
We're always happy to discuss your plastic vacuum moulding requirements. If you have a project to complete or a problem that needs solving please contact us.

Production-Quality Assured
Over 60 years expertise in vacuum forming plastic helps particularly when it comes to material selection and manufacturing, this means that we are able incorporate a diverse range of processes and products. Our stock is 95% recyclable. We have bespoke services ie. cut to size, colours and materials.
We're always happy to discuss your plastic vacuum moulding requirements. If you have a project to complete or a problem that needs solving please contact us.

Multi-Fit Tile Ventilators
Lowline and Cowl is available in terracotta, slate grey, red and brown as standard. We also offer a bespoke colour mataching service.

Specialist Advice on the Design of your Product
With vacuum forming and CNC equipment along with the strength of six decades of experience, you can be assured of the quality at every stage of the process.

Bespoke Tooling Production for Forming
With vacuum forming and CNC equipment along with the strength of six decades of experience, you can be assured of the quality at every stage of the process.

Manufacture & Quality Finishing
With vacuum forming and CNC equipment along with the strength of six decades of experience, you can be assured of the quality at every stage of the process.

Registered BSI EN ISO 9001-2015 Standard
With vacuum forming and CNC equipment along with the strength of six decades of experience, you can be assured of the quality at every stage of the process.
About us
With vacuum forming and CNC equipment as well as six decades of experience, you can depend on quality at every stage.
Your project will start with everything you need:
- Advice on the design of your product from a specialist
- Production of bespoke tooling for in-house forming
- Your final products will be manufactured and finished with quality
- BSI EN ISO 9001-2015 compliance
We have been involved in multiple industries since then, including:
- Caravans & Motorhomes
- Promotional Materials & Events
- Point of Sale
- Construction, Building & Concrete
- Garden
- Medical
- Leisure
- Vehicles
The benefits of vacuum forming are numerous:
- Lower tooling costs - low to medium volume vacuum forming projects are more cost effective than injection moulding
- The choice of colour, finish, and material is wide and flexible
- Prototyping at a low cost
- Trim and hole details can be customised
- Lead-times for product introductions are shorter

Sponsored Links
Trade Associations
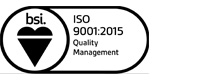