Company details for:
Curtiss-Wright Surface Technologies
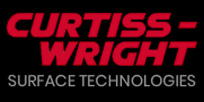
Hambridge Lane,
Newbury,
Berkshire,
RG14 5TU,
United Kingdom
Quick Links:
Products / Services
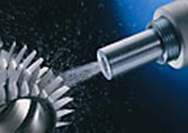
Controlled Shot Peening
Component failure is often related to residual tensile stress induced during manufacture and certain operating conditions. The controlled shot peening process is a cost effective and practical method of replacing tensile stress with beneficial compressive stress which is proven to prevent failures due to:
- Metal fatigue
- Corrosion fatigue
- Stress corrosion cracking
- Intergranular corrosion
- Fretting
- Galling
- Spalling
- Wear
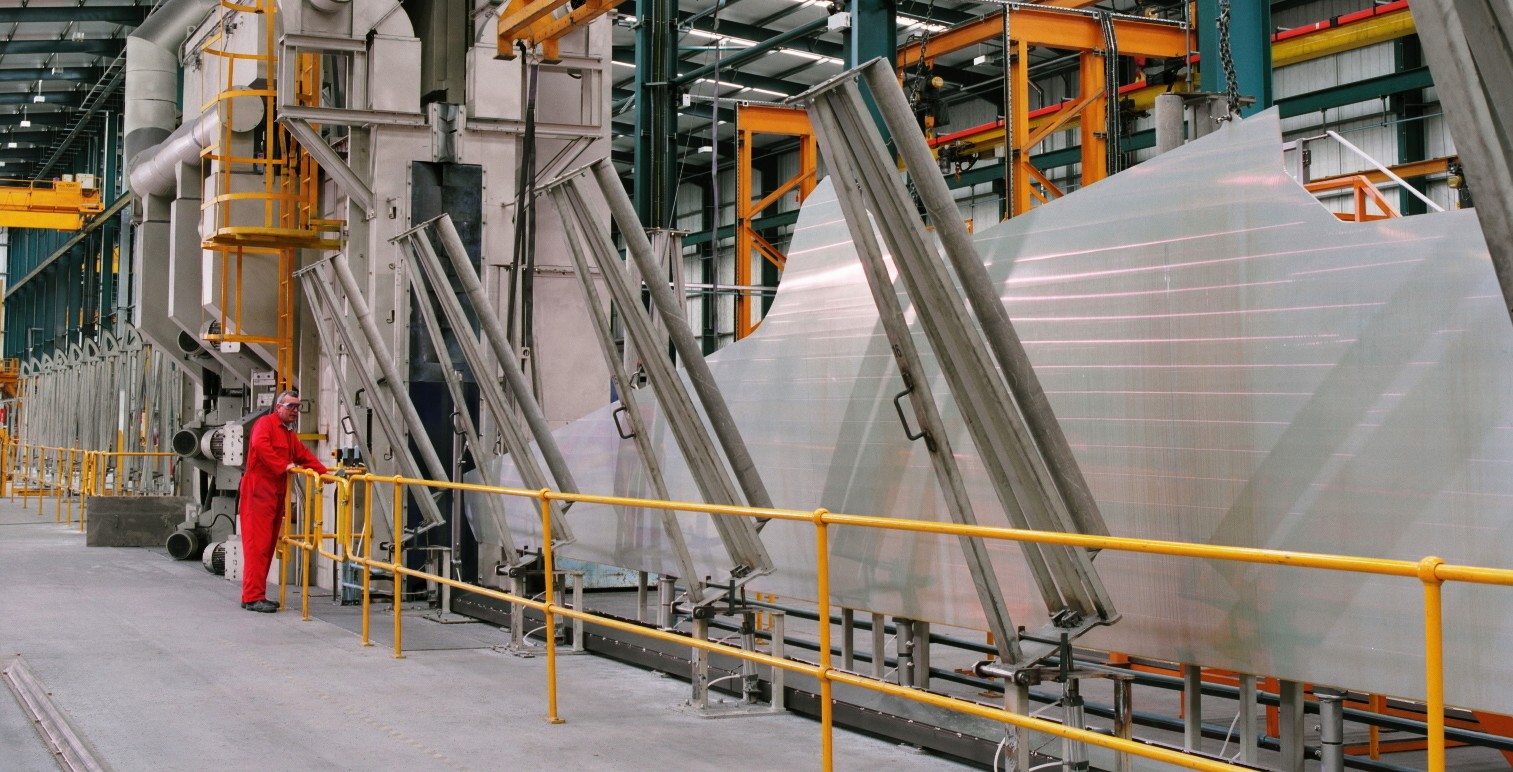
Shot Peen Forming
Varying curvature requirements, material thickness, cut outs, reinforcements and pre-existing distortion can all be processed.
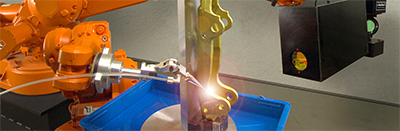
Laser Shock Peening
Laser peening is not a replacement for controlled shot peening, but has additional advantages that can influence which method to use.
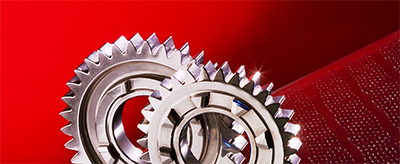
C.A.S.E Isotropic Super Finishing
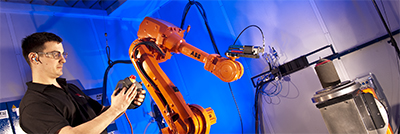
Thermal Plasma & HVOF Spray Coatings
Damaged and worn parts such as gas and steam turbines can be repaired to original specification.

Engineered Coating Services
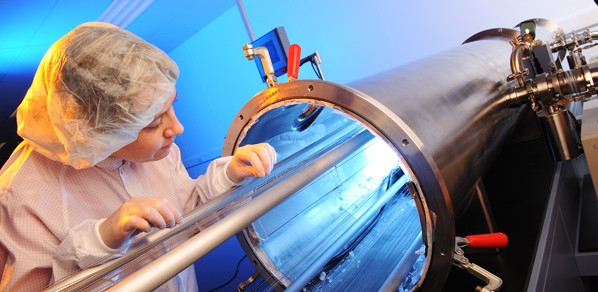
Parylene Conformal Coatings
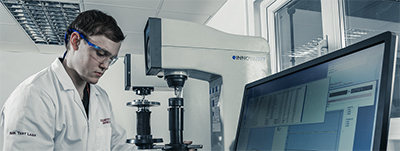
IMR Test Labs − Material Testing Services

Onsite Repair & Overhaul Services

Peentex Surface Texturing & Architectural Finishes
Controlled shot peening has long been associated with engineered surface finishing of metals including steels, stainless steels, aluminium, titanium and copper alloys. It forms an essential part of the manufacturing process used within the engineering industry to improve wear and corrosion resistance and prevent premature fatigue failures.

Peenflex Protective Moulding & Masking
Developed to protect components during our own processing we have now extended this service and produce mouldings directly for our customers.
Using our knowledge and experience, we are able to assess component requirements to produce mouldings to meet customers’ specific needs and reduce unnecessary costs resulting from damage, delays and rework.
All our mouldings are rigorously tested to ensure a high quality of wear resistance enabling them to be recycled many times through the handling stages, and presenting a cost effective solution to damage prevention.
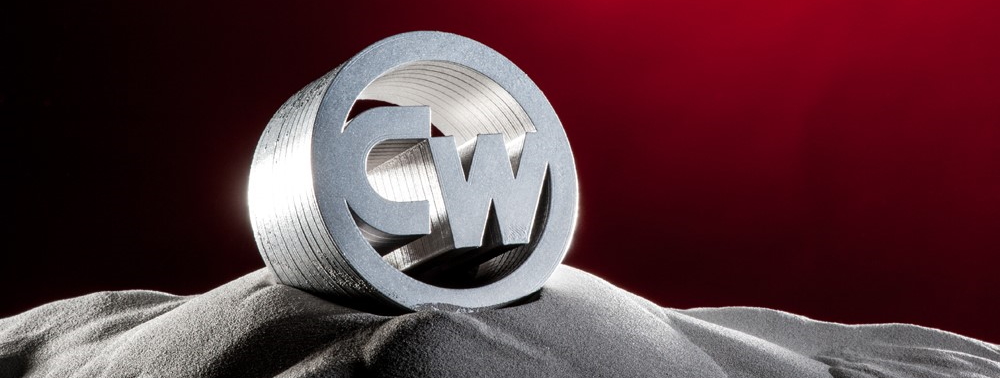
AM (Additive Manufacturing Process)
About us
- Aerospace
- Chemical
- Commercial
- Heavy Automotive
- F1
- Healthcare
- Oil & Gas
- Mining
- Power Generation
- General Engineering
Our key aim is to improve the longevity, quality and performance of those all important components. From protecting aero-engine components from extreme heat and thermal variation to the protection of medical devices from corrosion and high load conditions.
We also have the facilities to treat airframes, wing skins and undercarriages of aeroplanes, storage tanks, pumps, pressure valves, crankshafts, cylinder heads, gears, connecting rods, race tracks, drill collars, pipes, storage vessels, steam & gas turbine components & much more. We are not limited in our ability to deal with a particular shape, size or complexity of a component. Tooling and equipment can be manufactured in-house if required.
With over 70 worldwide facilities and on-site field teams, we have a location within close reach of our customers for faster turnaround and reduced costs. Our dedicated teams will visit your site anywhere in the world at short notice to repair your fixed or large equipment.
Images
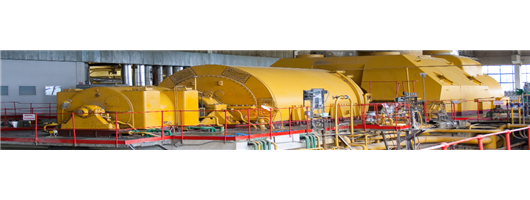
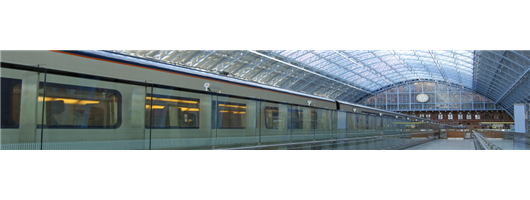
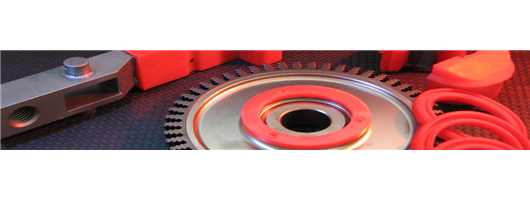
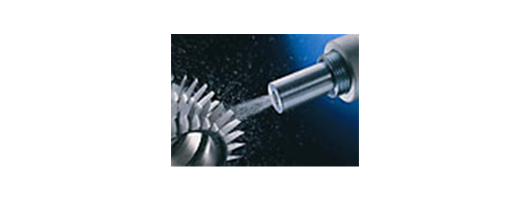
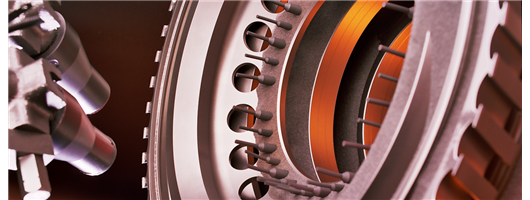

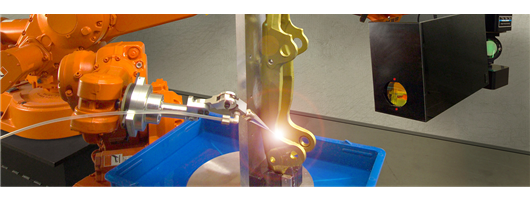
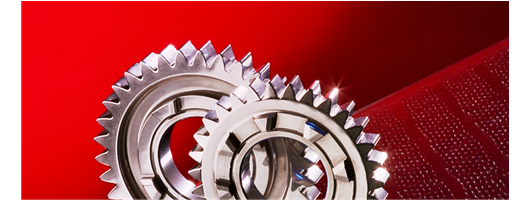
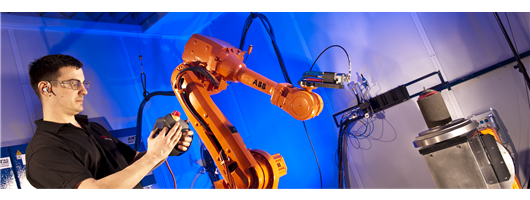
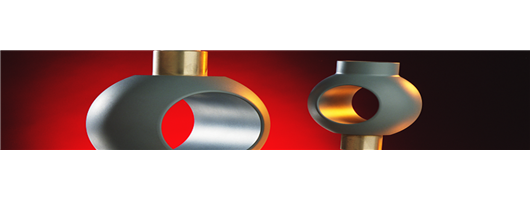
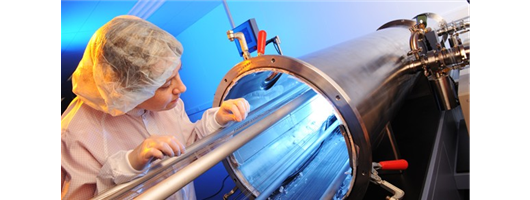
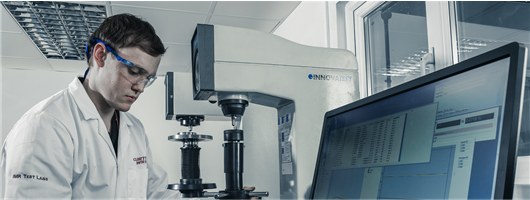
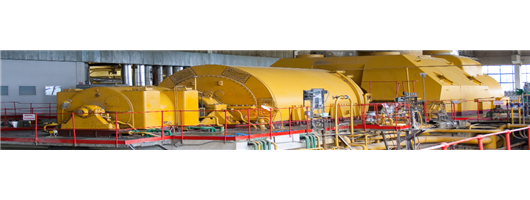
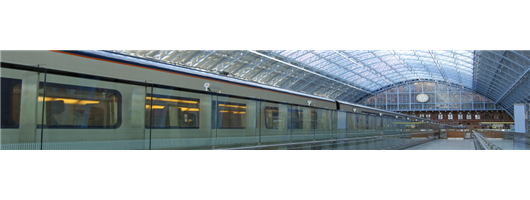
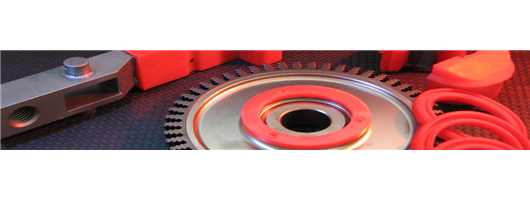
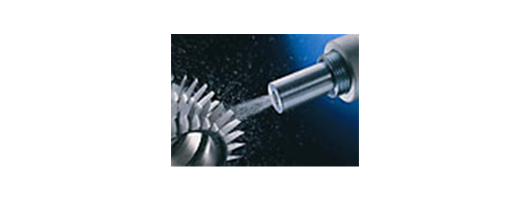
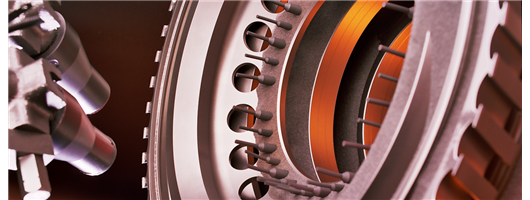

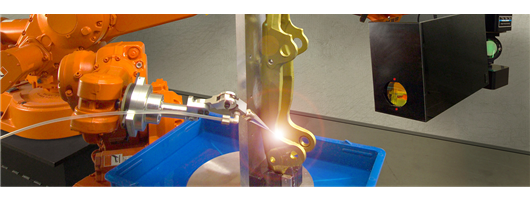
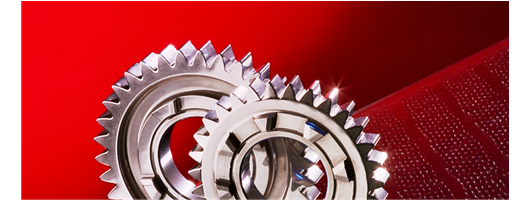
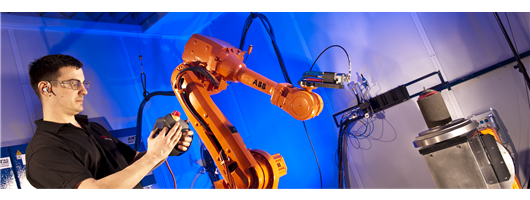
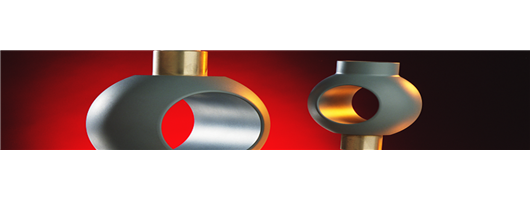
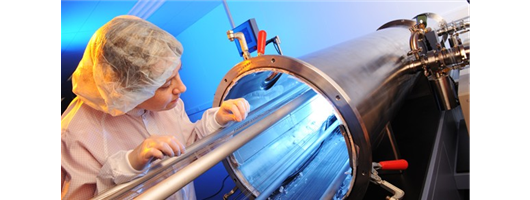
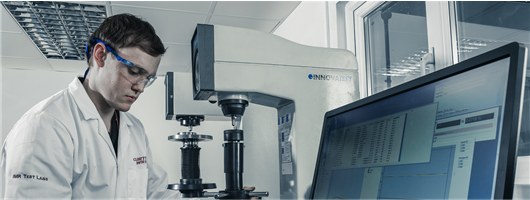
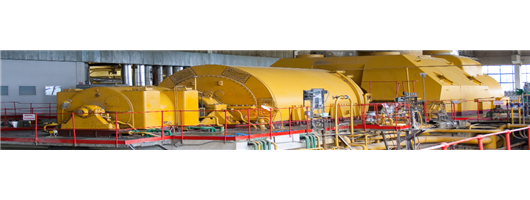
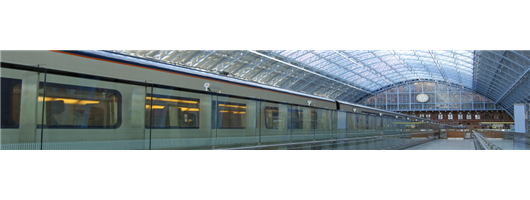
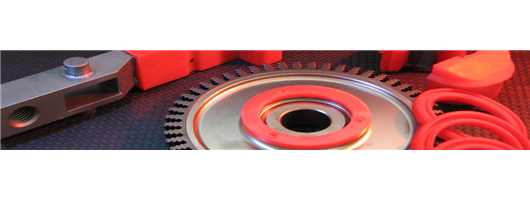
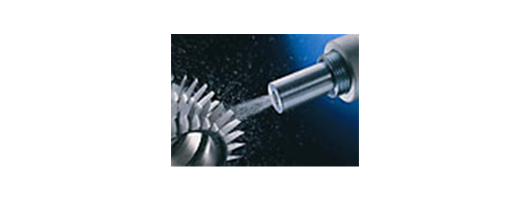
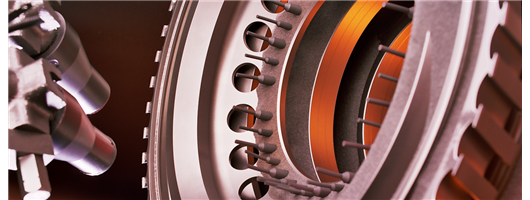

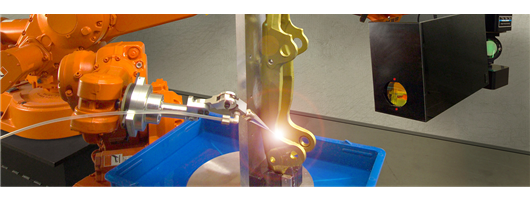
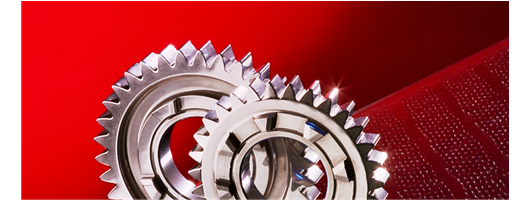
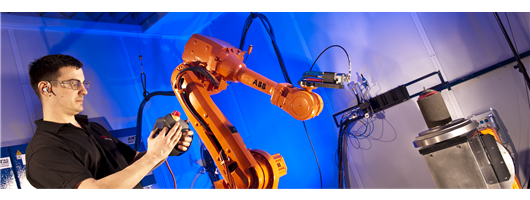
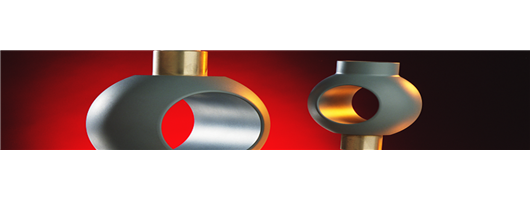
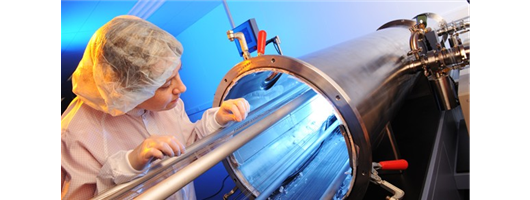
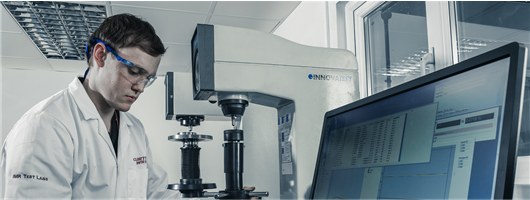