Company details for:
Hi-Rel Group
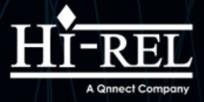
28 Fuller Road,
Harleston,
Norfolk,
IP20 9EA,
United Kingdom
Quick Links:
Products / Services
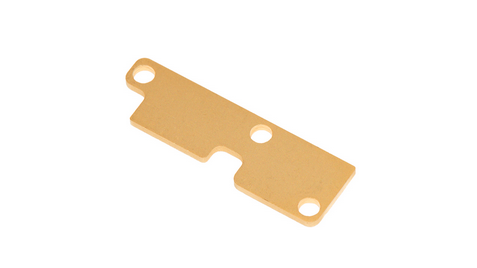
Enabling Components
We are 100% committed to your success, so if there is a component that you need for your particular application and you don’t see it here − please let us know; we are unconventional, thoughtful and willing to always go the extra mile for our customers. At Qnnect, we want you to be able to come to us with all of your hermetic needs and we offer an extensive array of components that you may need to protect your application.
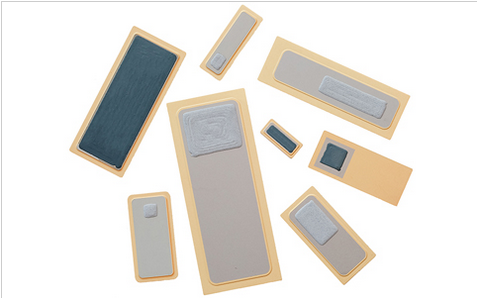
Getter Solutions
For 20 years, Qnnect worked both with its internal development team and its partners to provide superior getter solutions. One such key strategic partnership is with Johnson Matthey, a leading specialty chemicals company. Since 1999, Johnson Matthey and Hermetic Solutions Group have combined their advanced technology capabilities to provide robust offerings consisting of a Johnson Matthey Protelec getter material and a Qnnect hermetic lid.
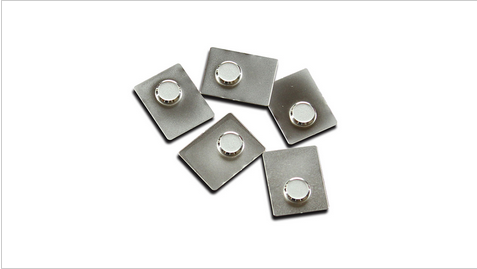
Moisture Getters
Hermetic Solutions Group and Johnson Matthey have been teaming together since 1999 to bring our customers the most robust solutions. Each solution is customized based on application, footprint, RGA analyis and other factors. We work together early in your design process so that whatever moisture issue your electronics face, we customize your exact solutions.
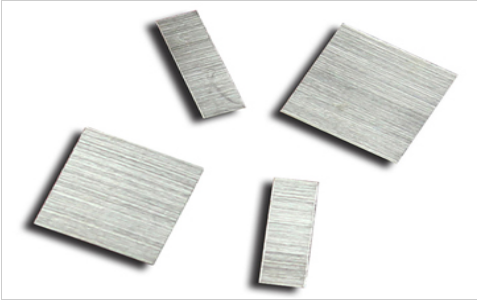
H2 Getters
To address this issue, the Hermetic Solutions Group has developed hydrogen getter solutions in several different formats − a foil getter, as well ink and tablet getters - for multiple product applications and industries. Our offerings are described below, but if you have a unique requirement, please let us know. We work very closely with our customers to develop custom solutions. For additional information on calculating H2 getter absorption capacity, download our white paper from our resources section
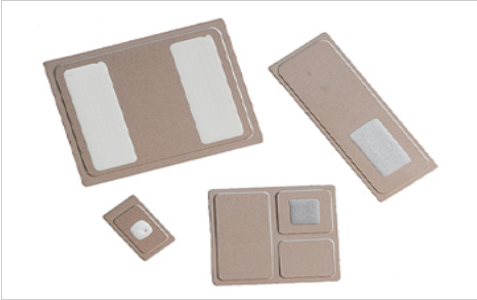
CO2 Getters
If you have a laser application, and your device is experiencing reduced power, your product may have carbon dioxide contamination issue. The Hermetic Solutions Groups provides a number of solutions to help prevent carbon dioxide contamination as detailed below. If you have a unique application, let us know − we’re ready to help develop the right solution for your circumstance.
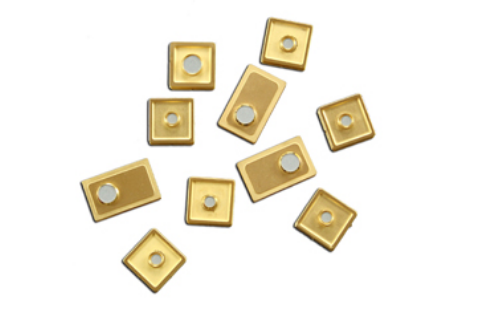
O2 Getters
Hermetic Solutions Group and Johnson Matthey have been teaming together since 1999 to bring our customers the most robust solutions. Each solution is customized based on application, footprint, RGA analysis and other factors. We work together early in your design process so that whatever oxygen issue your electronics face, we customize your exact solutions.
The Hermetic Solutions Group’s CP Getter Series offers an excellent oxygen getter solution as highlighted below.
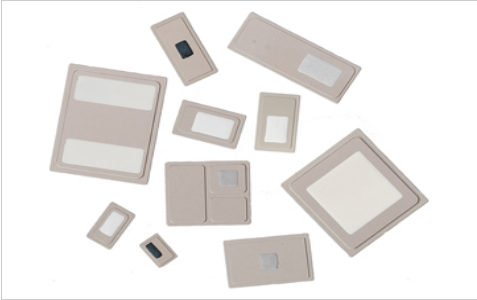
Organics Getters
Hermetic Solutions Group and Johnson Matthey have been teaming together since 1999 to bring our customers the most robust solutions. Each solution is customized based on application, footprint, RGA analysis and other factors. We work together early in your design process so that whatever organics contaminant issue your electronics face, we customize your exact solutions.
Let us know how we can help.
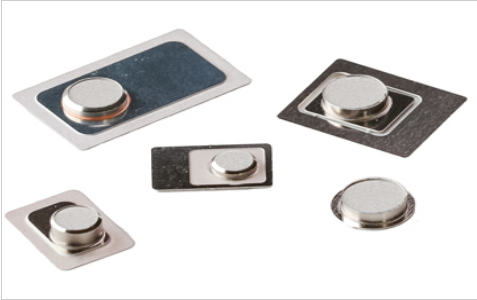
Multiple Contaminant Getters
The Hermetic Solutions Group addresses this reliability hazard by manufacturing products that can adsorb multiple contaminants, as highlighted below. If the products below don’t fully meet your needs, we’re also very happy to work with you to help identify the best solution for your unique situation and application. Please let us know how we can help.
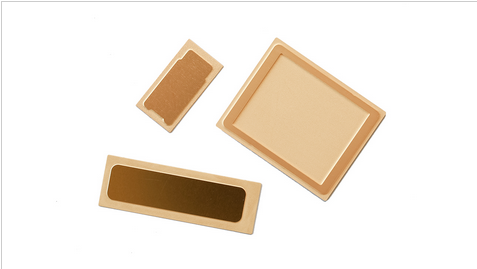
Hermetic Package Lids
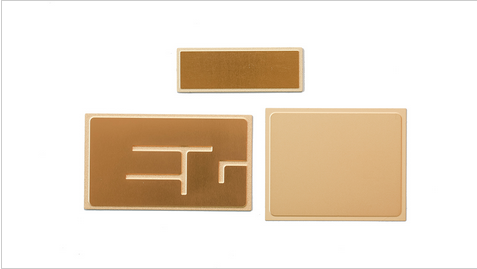
Stepped & Flat Lids
Let's work together and identify the best hermetic lid solution for your lidding process!
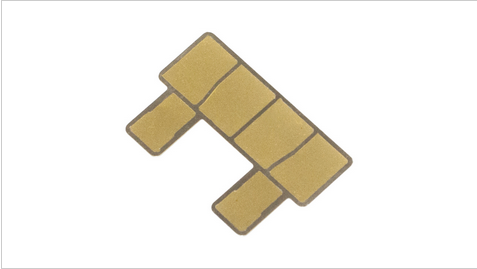
Solder Seal Lids
Solder seal lids from the Hermetic Solutions Group are typically manufactured in Kovar, Invar and alloy 42/45/48. They can be plated with electrolytic and electroless nickel as well as soft electrolytic gold. Flat, stepped, and drawn caps are common configurations and solder options include 80/20 AuSn (most common) but Sn/Ag and Sn/Pb solder is also possible.
Flat lids are typically used for solder seal lids, but stepped lids are also an option. Rapid prototyping is available in small volumes even when no standard tooling exists.
Let us help you identify the best solder seal lid solution for your application, package and hermetic sealing process!
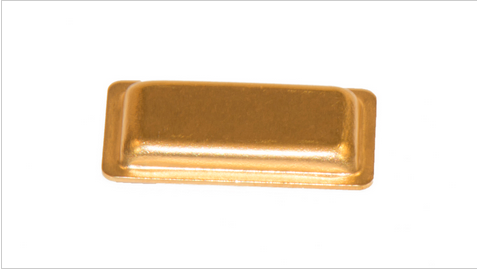
Domed Can Lids
The domed lid protects and covers the circuitry that sits on the surface of the metal platform package. These lids are often sealed with a single projection weld and are commonly made of nickel, although other materials are options. Lid shapes can be custom matched to the shape of the header. At the Hermetic Solutions Group, these domed lids are generally stamped and our customers install/seal them with a resistance welding process.
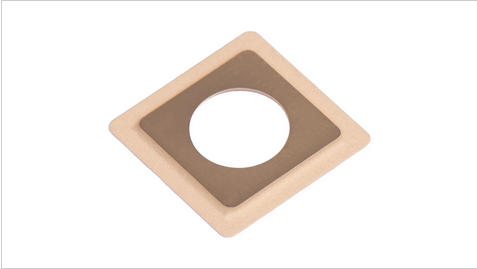
Window Lids
The transparent window media is chosen to match the required transmitted wavelength. Windows are metallized and coated with customer specified anti-reflective coatings. We manufacture window lids to customer designs. Typically, a Ni/Au plated etched Kovar frame is used to support the window which is hermetically sealed often with Au/Sn solder preforms also manufactured by the Hermetic Solutions Group.
Window material options for visible NIR imaging include fused silica (0.185 µ − 2.1 µ transmission range) and quartz (2 µ − 16 µ transmission range). Sapphire, typically used in telecommunications, lasers, SWIR and endoscope applications, is available to support a 0.15 µ − 5 µ transmission wavelength range, while germanium for LWIR/thermal imaging application support a transmission range of 2 µ − 16 µ. Frame material options include Kovar, Invar and Alloy 42/46/48 and these materials can be plated with electrolytic or electroless nickel as well as electrolytic gold. They are manufactured with a chemical etching process in a flat, stepped rectangular. Window lids are typically soldered in place and are available for integration in most sensor and other opto-electronic applications.
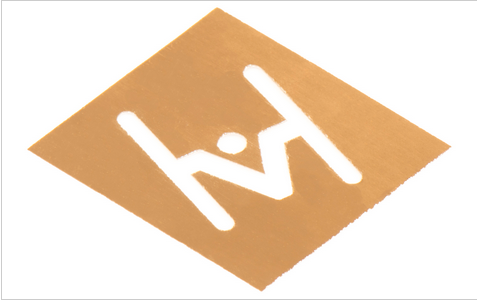
Solder & Braze Preforms
Preforms are excellent solution for attaching electronic circuitry and packaging electronic devices. Preforms deliver good thermal and electrical conductivity as well as provide an interface for electronic connections. Alloy selection and shape geometry/dimension are critical decision points and Qnnect are experts in the intricate physical and chemical requirements for solder and braze preforms and we are well qualified to assist customers select the best material for any application.
We offer more than 40 years of preform manufacturing experience across multiple industries and endless geometries and applications. We understand tight tolerances and are an ideal partner for all of your preform needs.
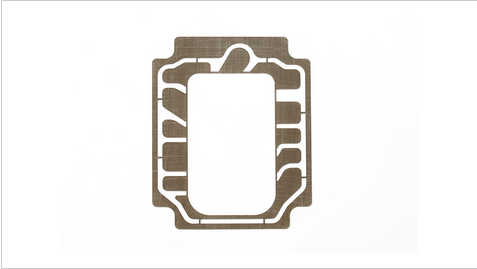
Solder vs. Braze
A device’s application/operating environment will determine whether solder or braze is the best process. At Hermetic Solutions Group, we have decades of experience working with our customers and manufacturing requirements to support both braze and solder preform needs. Our dedicated facility offers competitive leadtimes, extensive material choices and superior customer service.
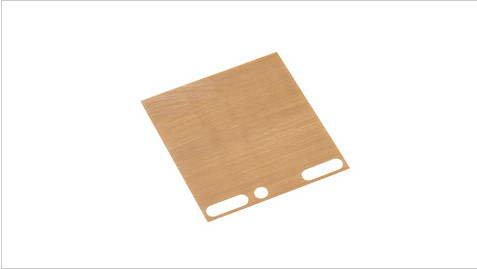
Solder & Braze Materials
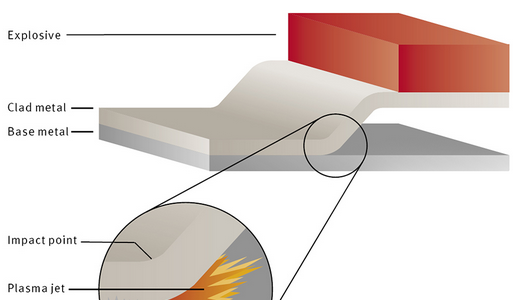
Technical Overview of Explosive Metal Welding
Explosively welded composites may be designed and fabricated to combine desirable properties of very different metals, allowing designers to optimize the composite’s performance for high temperature, cryogenic, high strength, thermal or electrical conductivity, enhanced mechanical properties or corrosion resistance.
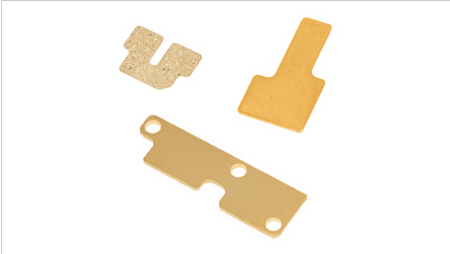
Thermal Management Solutions
Proper material selection is fundamental to an efficient thermal management solution. We offer technically robust, advanced thermal management materials, such as molybdenum/copper (MoCu), copper/molybdenum copper (CMC), and tungsten/copper (WCu). We are also consistently looking for novel materials to support your evolving thermal management needs. Our thermal management products are EDM'd, milled or stamped to precise size and dimensions and then electroplated. Our products consistently exceed customer expectations for quality, workmanship standards (especially corners and edges), plating requirements and ease of use.
Three to five week lead times are typical; however, we also support the need for additional flexibility as required. We provide customers with certification of compliance and certification of analysis documentation and we manufacture with adherence to numerous industry standards - STM-B-488 (Gold), MIL-G-45204C (gold), ASTM −B-689 (electrolytic nickel), AMS-QQ-N-290 (electrolytic nickel), MIL-C-26074E (electroless nickel), and ASTM-B-733 (electroless nickel) J-Std-006.
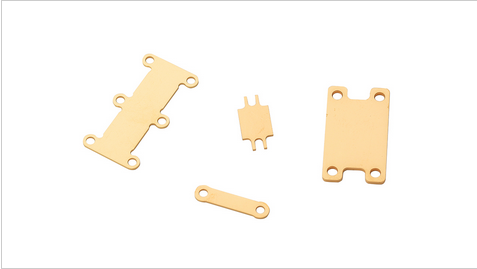
Thermal Tabs
Offering heat sinks, thermal carriers, and thermal tabs, the Hermetic Solutions Group delivers both high quality standard shapes, as well as complex geometries and materials. With decades of experience providing thermal dissipation materials, we consistently meet customer lead-time requirements for these items. Plus our customer service is second to none. If you are looking to partner with a supplier that is consistently looking for innovative solutions to thermal management challenges, look no further than Hermetic Solutions Group!
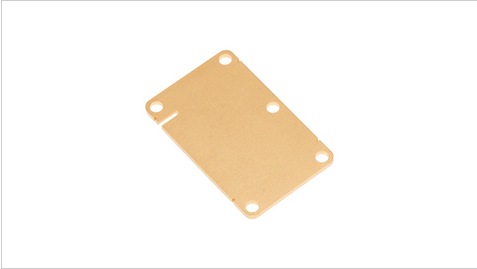
Thermal Management Base Plates
With over 40 years of advanced thermal materials manufacturing experience, Hermetic Solutions Group really understands how critical this support component is in the overall success of critical applications across the defense & aerospace, medical, and industrial markets and is an ideal partner to help with your specific application.
The table below highlights some of our base plate manufacturing capabilities and offerings. Please let us know how we can customize our offerings to meet your needs.
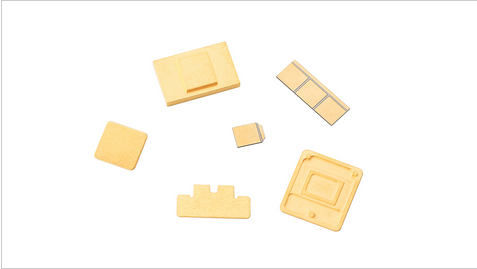
Heat Dissipation Materials
To consistently meet evolving customer requirements and heat dissipation challenges, we use technically robust advanced thermal management materials. Additionally, we seek innovative new materials to help you be one step ahead of these challenges. The reference table shows the most common thermal management materials and we can help you identify the best thermal management solution for your specific application.
We’re happy to assist in your design process and material selection - don’t hesitate to call us.
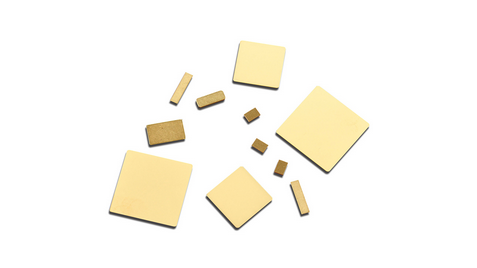
Precision Support Components
Our knowledge of:
Hermetic packaging and interconnect products
Metal manufacturing (stamping, machining, sputtering, etching, brazing, plating, soldering) of simple and complex designs
Glass-to-metal sealing and ceramic-to-metal sealing
Materials (Kovar, aluminum, titanium, stainless CRS, molybdenum, OFHC copper, CuMoCu, as well as ceramics and glass windows)
…makes Qnnect uniquely qualified to address any special metal component requirement you may have for your microelectronics application. Our #1 goal is to help our customers be successful in addressing their technical challenges and meeting their business goals. We'd be honored to help you in this effort.
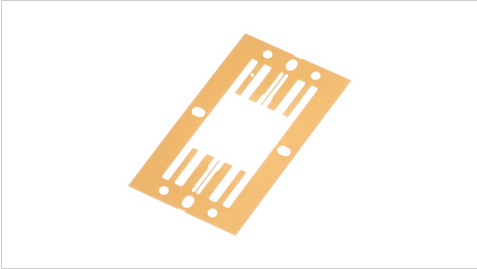
Lead Frames
Utilizing our vast experience in etched metals, suitable for a high- lead density, the Hermetic Solutions Group provides metal lead frames used in the manufacturing of hermetic microelectronic packages.
Typically made of Kovar, lead frames may or may not be plated when finished. They are manufactured with a chemical etching process and are generally attached to glass or ceramic.
With our decades of experience in supporting hermetic packaging performance, we are the perfect partner to help you identify the best solution for your application.
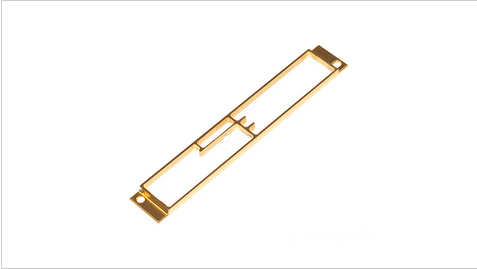
Ring Frames
Ring frames from the Hermetic Solutions Group provide a number of advantages including:
The ability to achieve and maintain very tight flatness tolerances
Maintaining fine surface finish requirements
Support for very complex design and configurations
The Hermetic Solutions Group also manufactures solder and braze preforms that support your ring frame assembly attach process.
Ring frames from the Hermetic Solutions Group can be manufactured in Kovar, Alloy 42, copper and Molybdenum with a wire EDM or CNC milling process. Plating options include electrolytic or electroless nickel as well as soft electrolytic gold. They are generally integrated by soldering or brazing to ceramic.
Let us help you identify the right ring frame solution for your application!
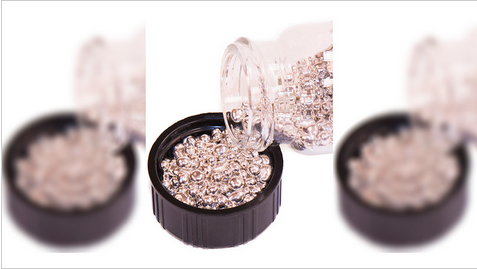
Vapor Deposition Materials
Typical materials include Gold and Silver 99.99% and 99.999% purities, among others with gold and silver coatings. We exercise extreme care in controlling particle size and metal purity and are a recognized partner, within multiple markets, among our thin film coating customers.
With decades of experience in metallurgy and manufacturing, we are an ideal partner to help you meet your design and application requirements.
About us
Renowned for our expertise, we specialise in manufacturing intricate metal components tailored to the industry's unique requirements. Our diverse product range encompasses getters, absorbers, covers, ring frames, thermal management solutions, preforms, and more. With a strong commitment to excellence, we continue to deliver highly specialized and reliable solutions to the microelectronic packaging industry.
Our manufacturing operations are distributed among three specialized facilities: Hi-Rel Products, Hi-Rel Alloys, and Hi-Rel Lids. Each facility has its distinct expertise, focusing on a core specialty within our production process. By combining the strengths of these facilities, we are able to offer customers comprehensive turnkey solutions that deliver high performance and meet their specific needs.
Common Materials Include:
Pure Mo, Cu or W
Laminate materials; CMC, CPC and SCPC
Mo/Cu and W/Cu composites
Metal Matrix Composites: aluminum, copper and silver diamond
PCD − Polycrystalline diamond
MCD − Mono-crystalline diamond
Hi-Rel provides a wide selection of materials that can be utilized for package bases, flanges, and as die sub-mount tabs. Our materials are carefully chosen to meet the demands of high-performance applications, ensuring exceptional material performance, accommodating complex geometries, maintaining tight tolerances, and adhering to the highest-quality standards. We strive to deliver materials that fulfill your specific requirements and exceed your expectations.
Hi-Rel Group Product & Service Offerings
Getter Solutions
Products Include:
- Moisture Getters
- H2 Getters
- CO2 Getters
- 02 Getters
- Organics Getters
- Multiple Contaminant Getters
Products Include:
- Stepped / Flat Lids
- Solder Seal Lids
- Domed Lids & Cans
- Window Lids
- Solder & Braze Preforms
Products Include:
- Thermal Tabs
- Thermal Management Base Plates
- Heat Dissipation Materials
- Thermal Spreaders
Products Include:
- Lead Frames
- Ring Frames
- Vapor Deposition Materials
We're pleased to annouce we'll be exhibiting at ECOC 2023 this October!! Please come and see us on stand 957.
Your feedback is valuable to us!
We are eager to engage with you, whether it's to discuss a specific requirement or to address any general technical or industry-related inquiries you may have. Our team is ready to assist you and provide the information and support you need. We welcome the opportunity to have a conversation and provide the assistance you are seeking. Feel free to reach out to us, and we'll be happy to speak with you.
Images
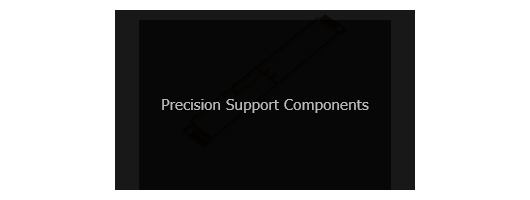
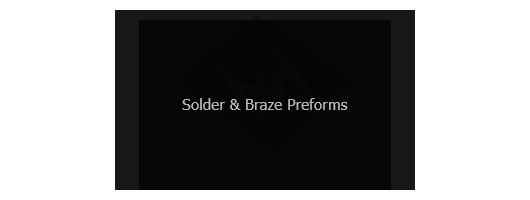
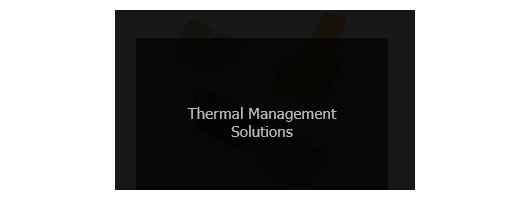

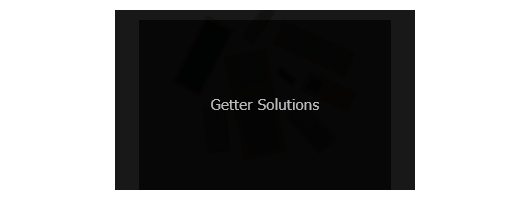

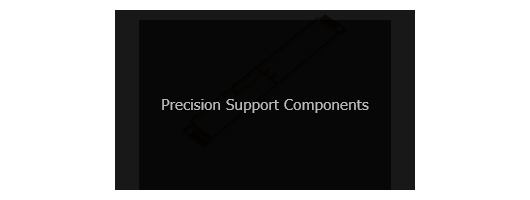
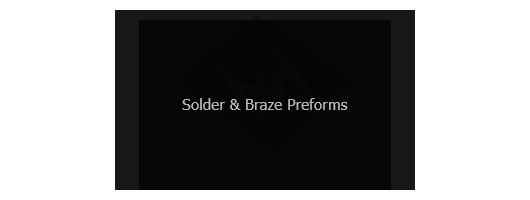
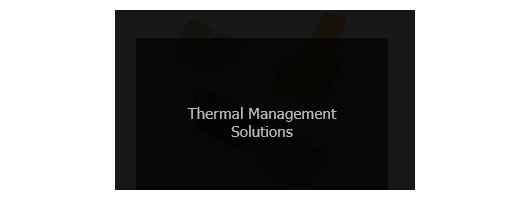

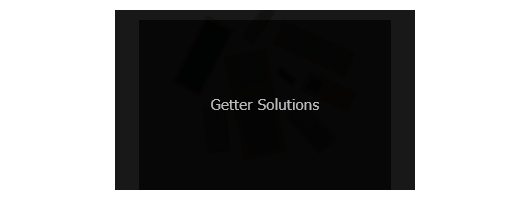

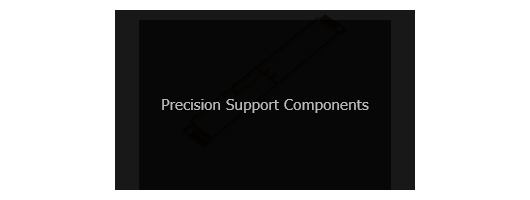
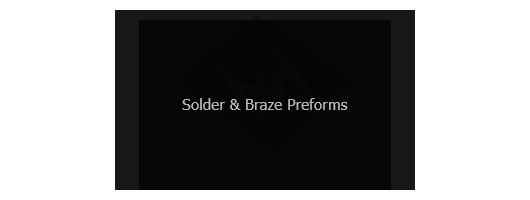
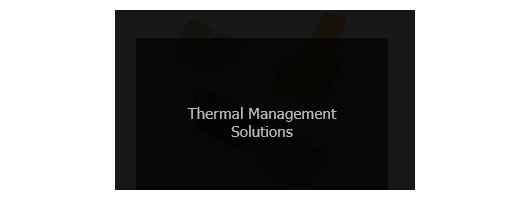

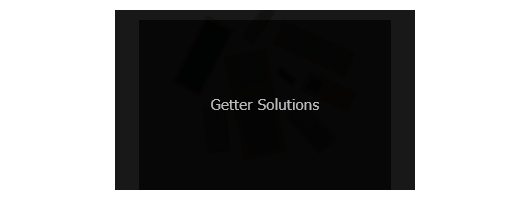
