Company details for:
HRS Heat Exchangers Ltd
3 Abloy House,
Hatters Lane,
Watford,
Hertfordshire,
WD18 8AJ,
United Kingdom
Quick Links:
Products
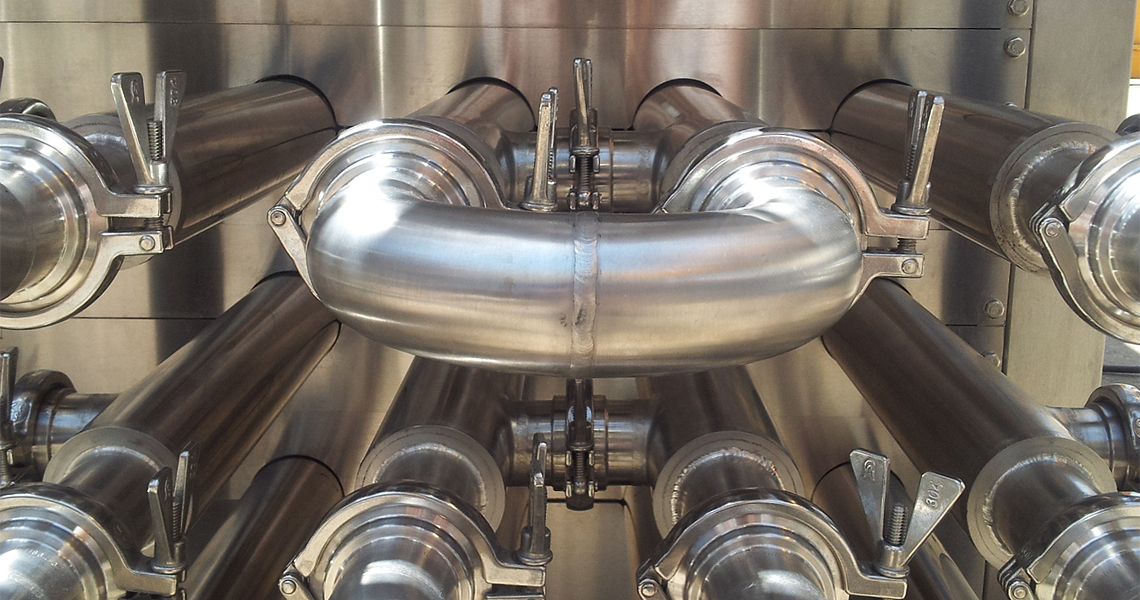
Hygienic Double Tube Heat Exchangers − HRS DTA Series
Bellows are fitted to absorb differential expansion between shell and tube and multiple units can be interconnected for larger applications. Options include frame mounting, insulation and stainless steel cladding.
HRS DTA Series is suitable for viscous products with large particulates in suspension. For high viscosity food products like honey, fruit jams and marmalades, please refer to our Annular Space and Scraped Surface Heat Exchangers product range
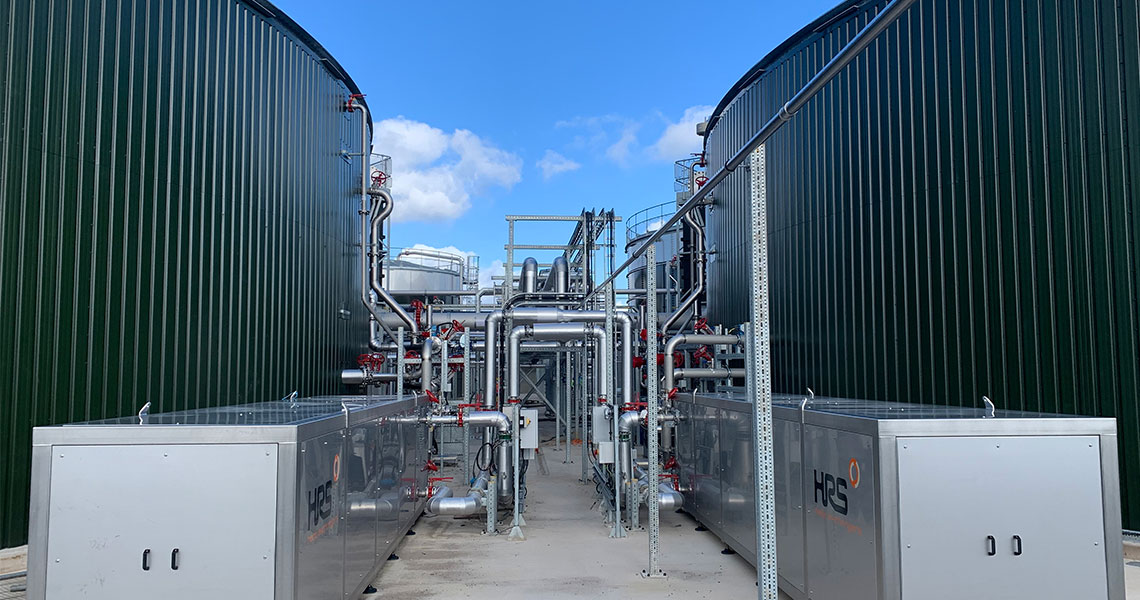
Industrial Double Tube Heat Exchangers − HRS DTI Series
Using our corrugation technology, both heat transfer and efficiency are increased over standard smooth tube heat exchangers. In addition, potential fouling is minimised.
Expansion joint (bellows) is fitted in the shell to allow for differential expansion of the inner and outer tube during operation. Multiple units can be interconnected and have the options of frame mounting, insulated and cladded in stainless steel.
The HRS DTI series is suitable for applications with fluids containing fibres or particles and low-high viscosity fluids.
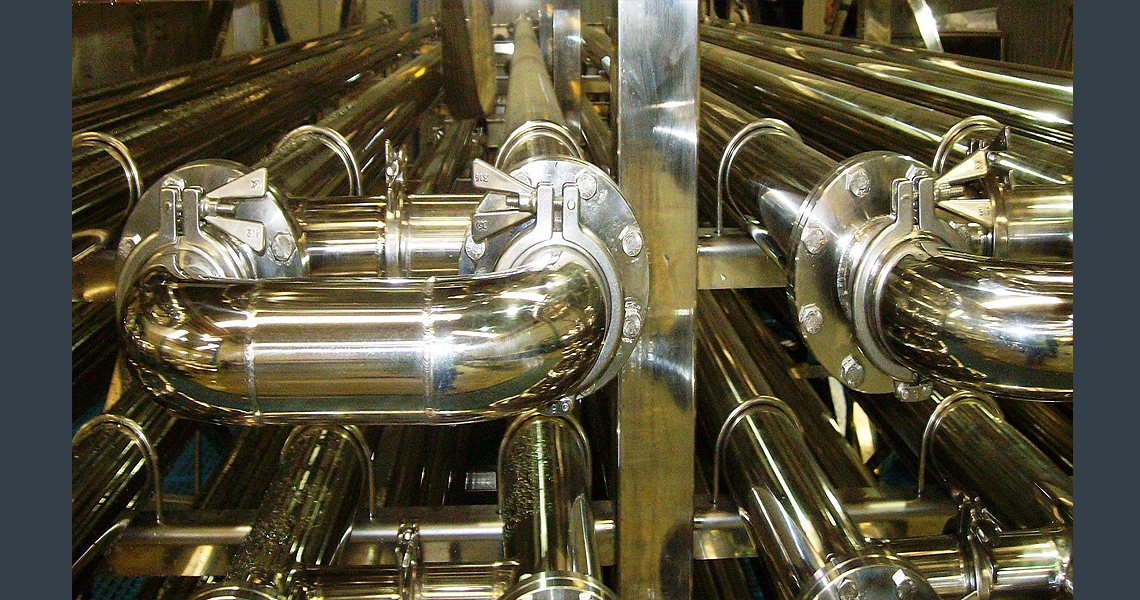
Industrial Double Tube Heat Exchangers with Removable Tube − HRS DTR Series
The tube in tube concentric geometry makes it easy to work with fluids that contain particles, without having to worry about blockages impeding the flow of product. Special corrugated tubes are used to increase heat transfer and reduce fouling, making the DTR Series more efficient than similar smooth tube heat exchanger designs.
For large duties, multiple units can be interconnected and mounted in a frame. Frame plating with thermal insulation can be provided for safety and to prevent heat loss and other options include frame mounting and stainless steel cladding.
Typical applications of the HRS DTR Series include sludge heating/cooling and pasteurisation, digester heating and sludge-to-sludge heat recovery.
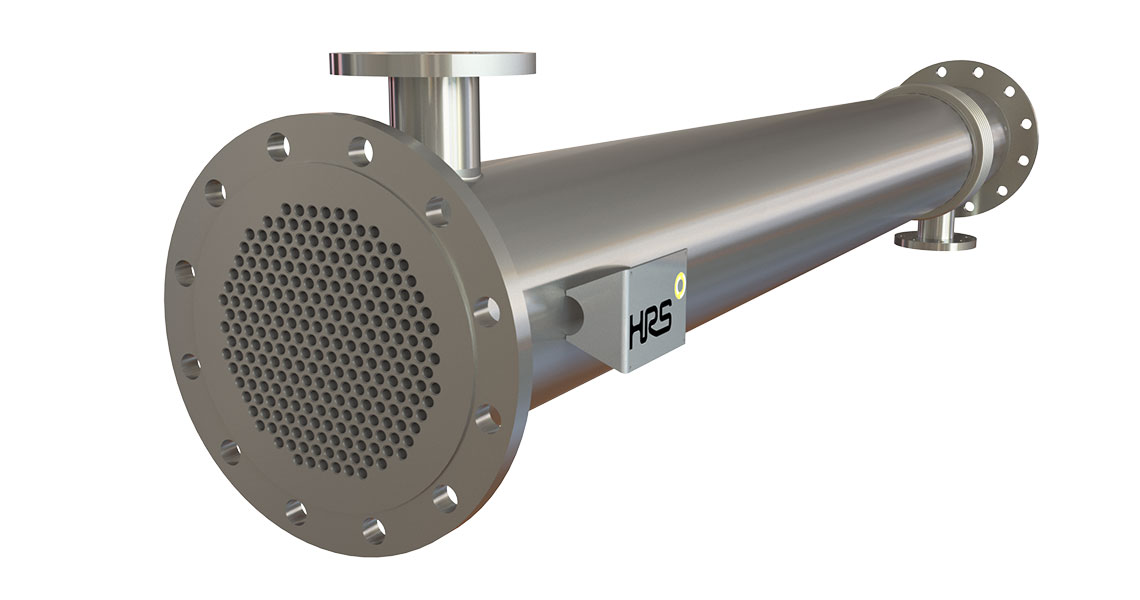
Industrial Multitube Heat Exchangers − HRS C Series
The HRS C Series is suitable for applications with low viscosity fluid, CIP heating and general industrial applications.
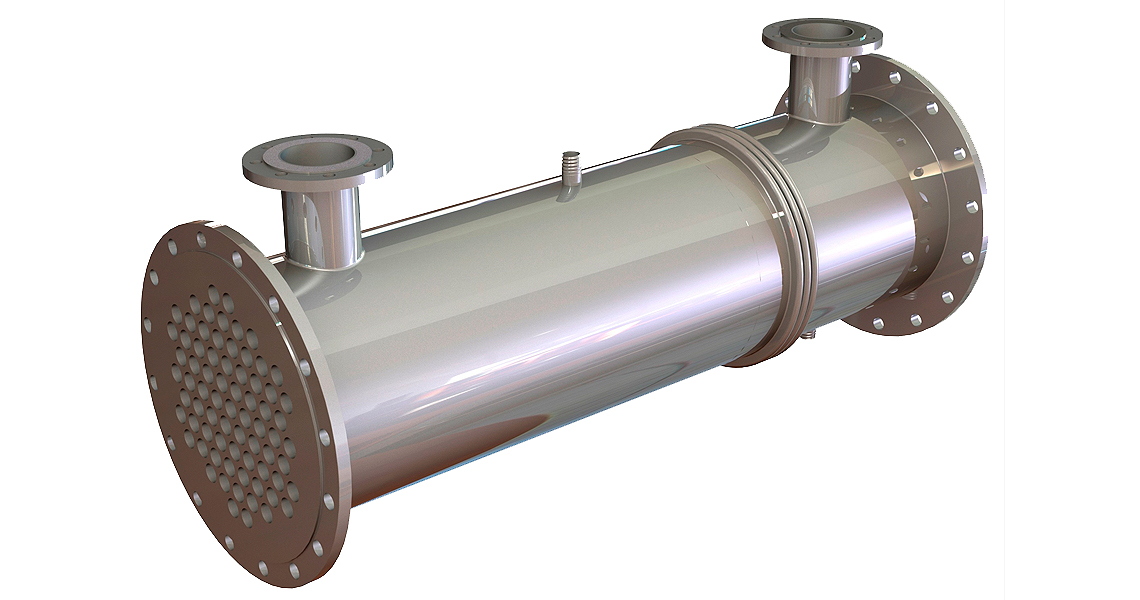
Gas Cooling Heat Exchangers − HRS G Series
Expansion bellows are fitted to absorb the differential expansion between the shell and the inner tubes. Multiple units can be interconnected for larger applications. Options include frame mounting, insulation and stainless steel cladding.
The HRS G Series is suitable for applications such as heat recovery from cogeneration exhaust gases, boiler exhaust gases, industrial exhaust and flue gases.
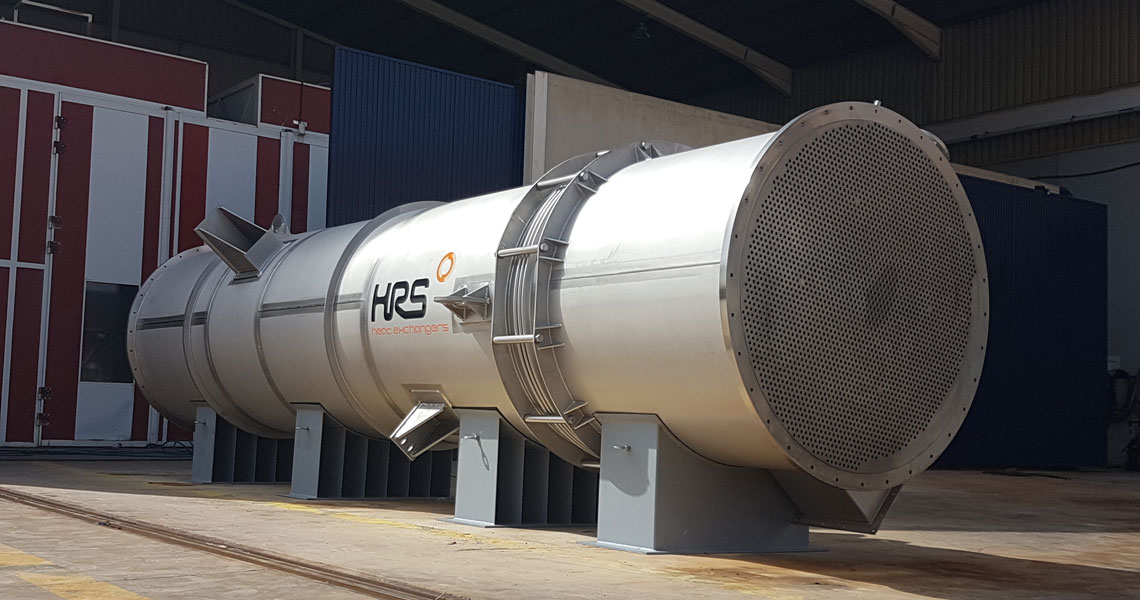
Industrial Multitube Heat Exchangers − HRS K Series
Expansion bellows are fitted to absorb the differential expansion between the shell and the inner tubes and multiple units can be interconnected for larger applications. Options include frame mounting, insulation and stainless steel cladding.
The HRS K Series is suitable for applications with low to medium viscosities, CIP heating and general industrial applications.
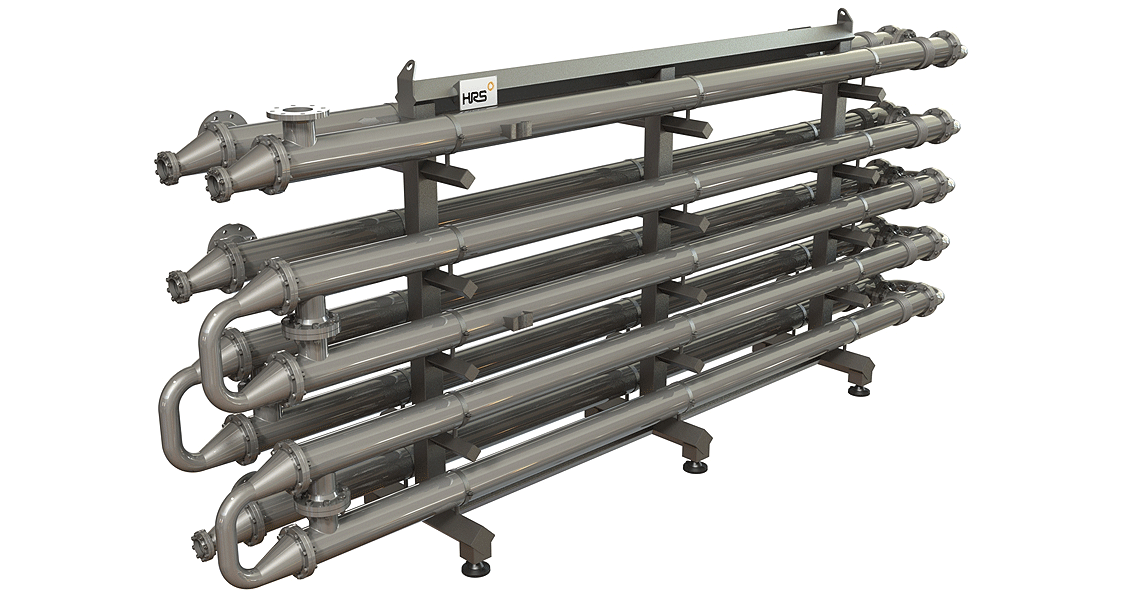
Hygienic Multitube Heat Exchanger − HRS MI Series
Expansion bellows are fitted to absorb the differential expansion between the shell and the inner tubes. Multiple units can be interconnected for larger applications. Options include frame mounting, insulation and stainless steel cladding.
The HRS MI Series is suitable for products with low to medium viscosities in hygienic applications.
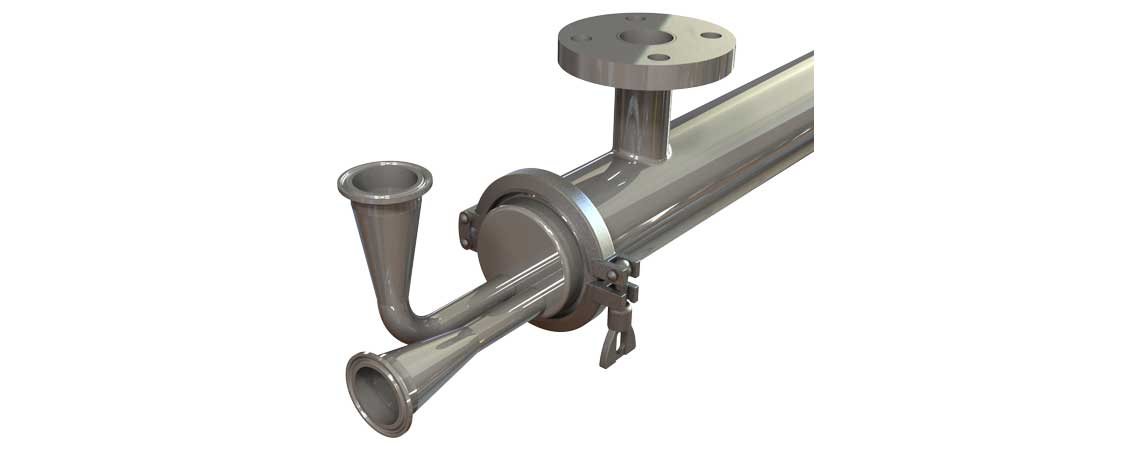
Multipass Heat Exchangers − HRS MP Series
The unique design creates longer thermal length within the same module, avoiding designs with multiple modules and interconnecting bends. Using HRS corrugation technology, both heat transfer and efficiency are increased over standard smooth tube heat exchangers. In addition, potential fouling is minimised.
Expansions bellows are fitted to absorb the differential expansion between the shell and the inner tubes. Multiple units can be interconnected for larger applications. Options include frame mounting, insulation and stainless steel cladding.
The HRS MP Series is suitable for applications which has low to medium viscosity fluids in food industry.
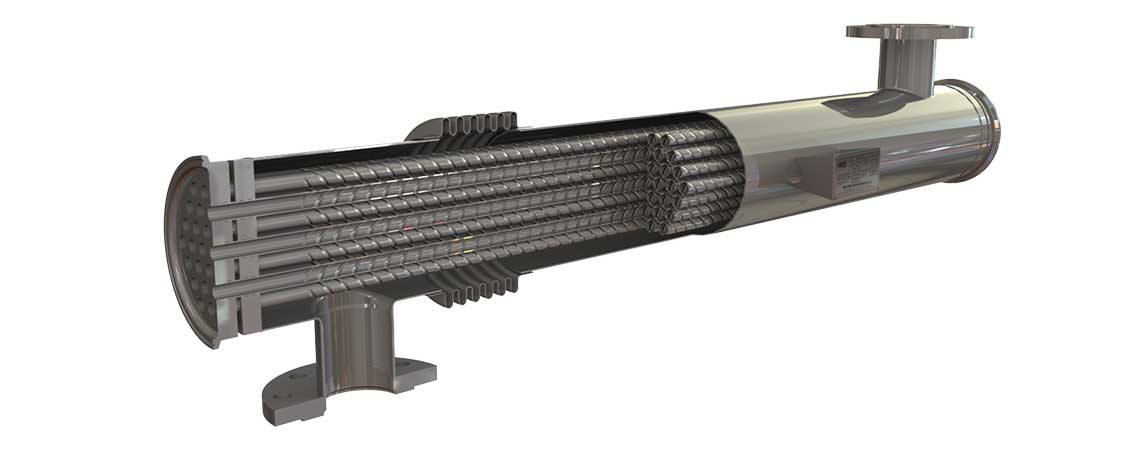
Double Tubeplate Hygienic Heat Exchangers − HRS SH Series
Using our corrugation technology, heat transfer and efficiency are increased over standard smooth tube heat exchangers. In addition, potential fouling is minimised.
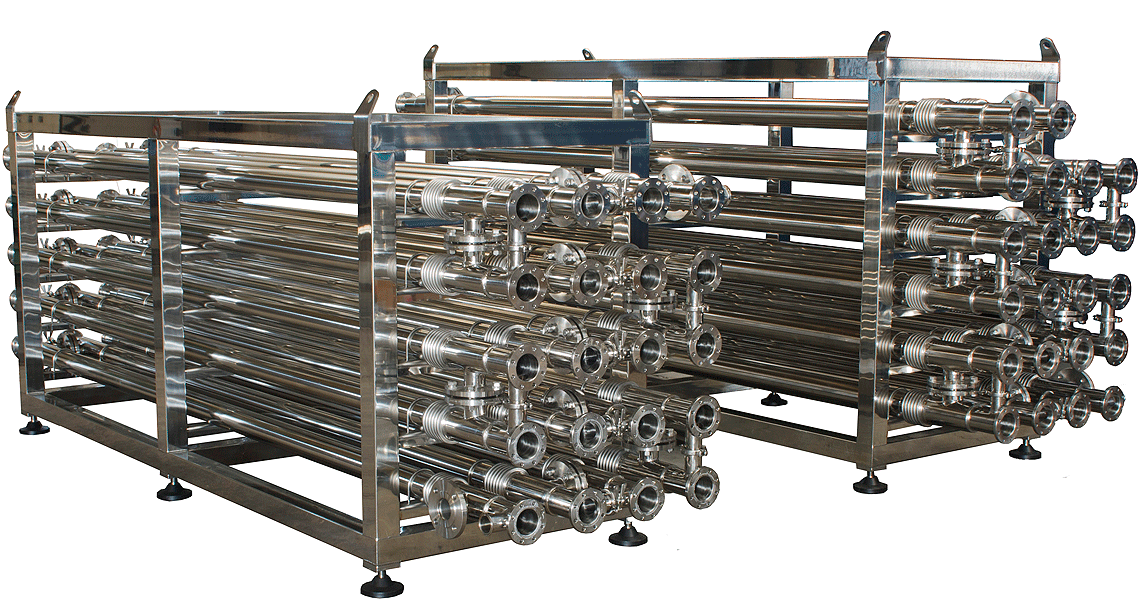
Annular Space Heat Exchangers − HRS AS 3 Series
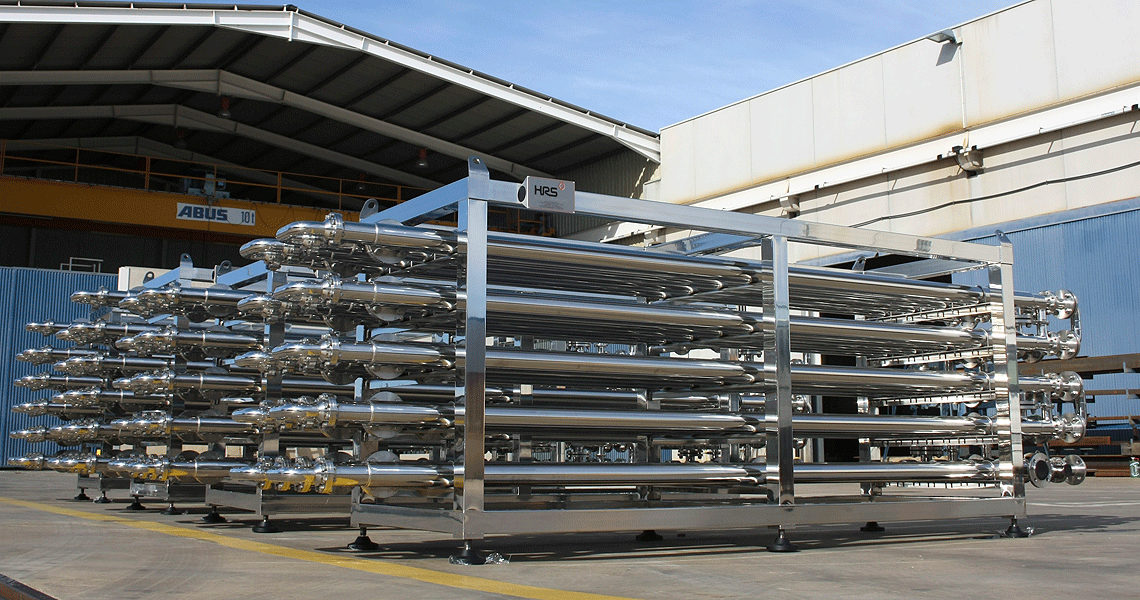
Annular Space Heat Exchangers − HRS AS 4 Series
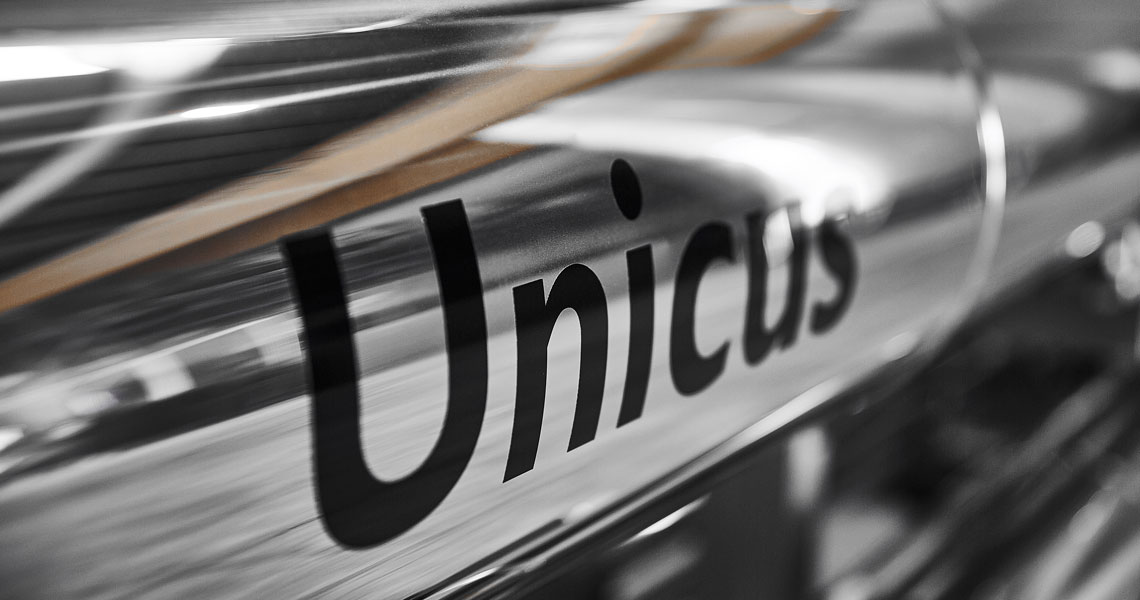
Reciprocating Scraped Surface Heat Exchangers − HRS Unicus Series
This design makes the Unicus Series the ideal heat exchanger for applications where fouling or low heat transfer is a limiting factor. The Unicus Series can be applied in industrial and hygienic applications.
The gentle movement of the scrapers allows the system to be used with delicate products, such as whole fruit or vegetable pieces, without destroying the product integrity.
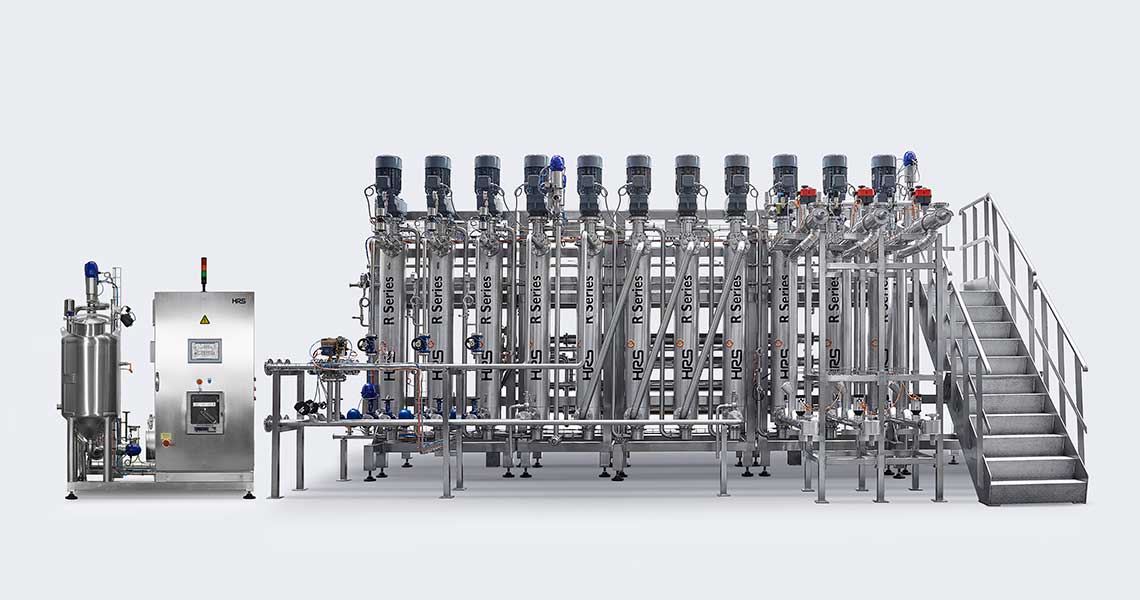
Rotating Scraped Surface Heat Exchangers − HRS R Series
Unlike the HRS Unicus Series, where the scraper movement is reciprocal, the HRS R Series technology uses a rotary scraper rod. This scraper rod can reach velocities up to 300 rpm resulting in very high levels of shear and mixing at the heat transfer surface; dramatically increasing the heat transfer rate.
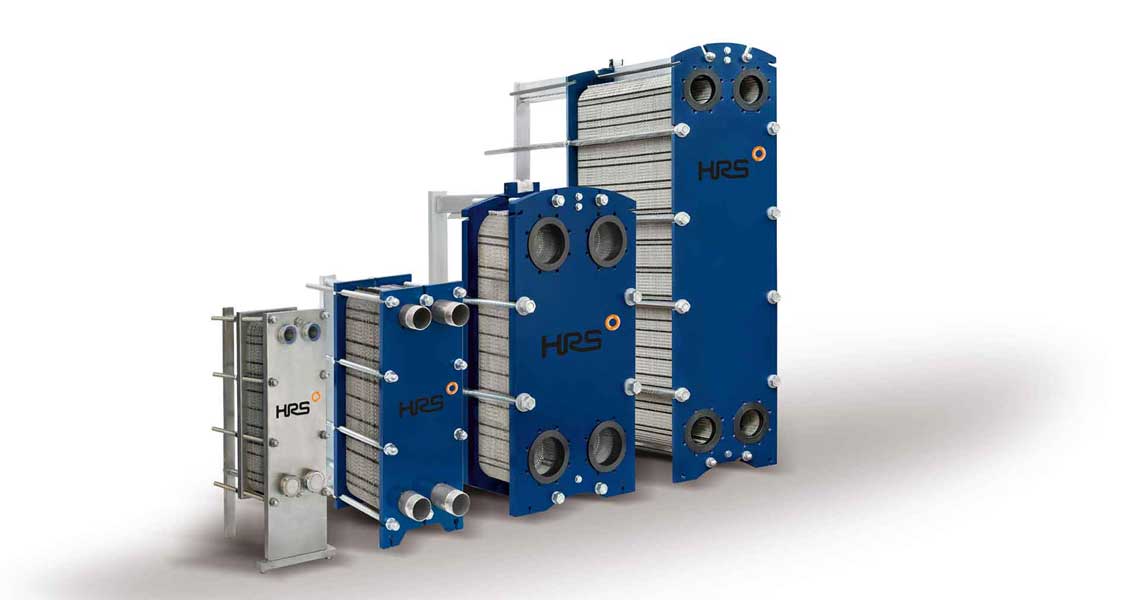
Plate Heat Exchangers, Gasketed
An extensive range of sizes of plate heat exchanger is available ranging from those models, which deliver flow rates of 0.7 litres per second to the largest units which are capable of flow rates of up to 819 litres per second (2,950,000 litres per hour). The range is designed for flexibility enabling the number of plates, the type and the number of flow paths to be varied, so that a heat exchanger can be manufactured according to a particular application in terms of power rating, operating temperature and pressure drop.
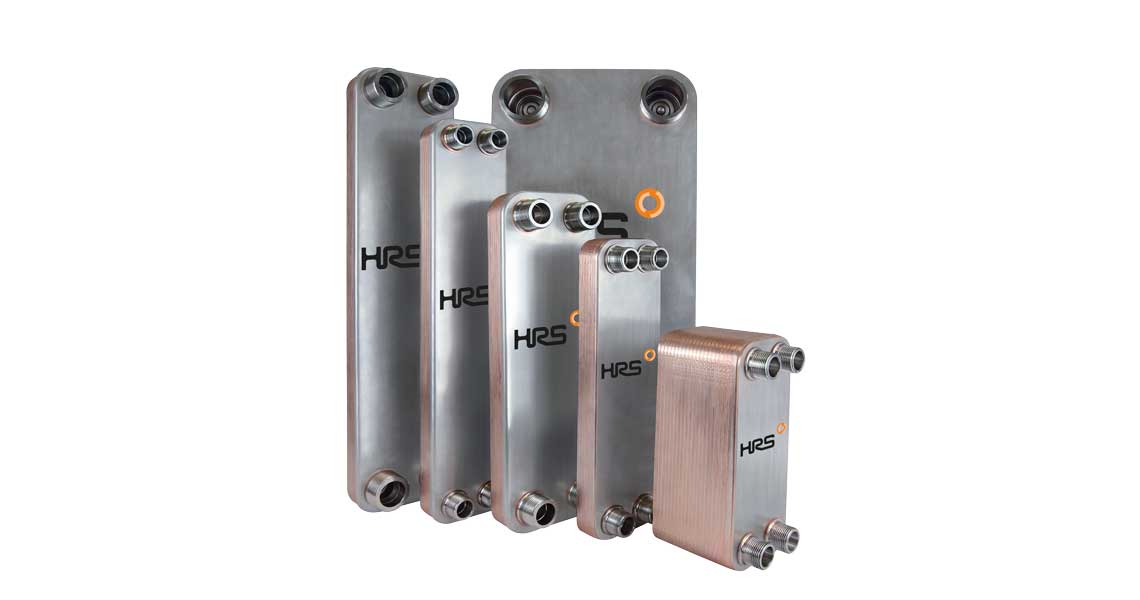
Plate Heat Exchangers, Brazed
Typically the units are copper brazed, however for applications where the medium is aggressive to copper, or for where temperatures range from 225°C to 400°C, then nickel is used. The plates are manufactured as standard from high-grade AISI 316 acid resistant steel with a thickness of either 0.35mm or 0.4mm dependent on the model type.
HRS brazed plate heat exchangers are suitable for heat recovery in the chemical, pharmaceutical, biotechnology and power generation industries, environmental processes and other industries.
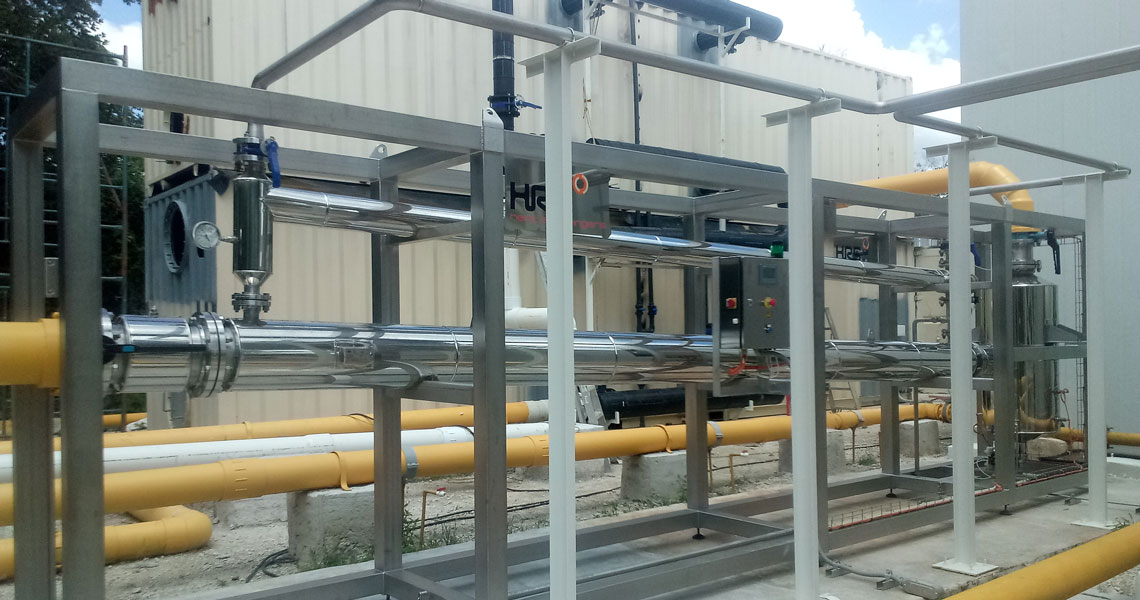
Biogas Dehumidification System (BDS)
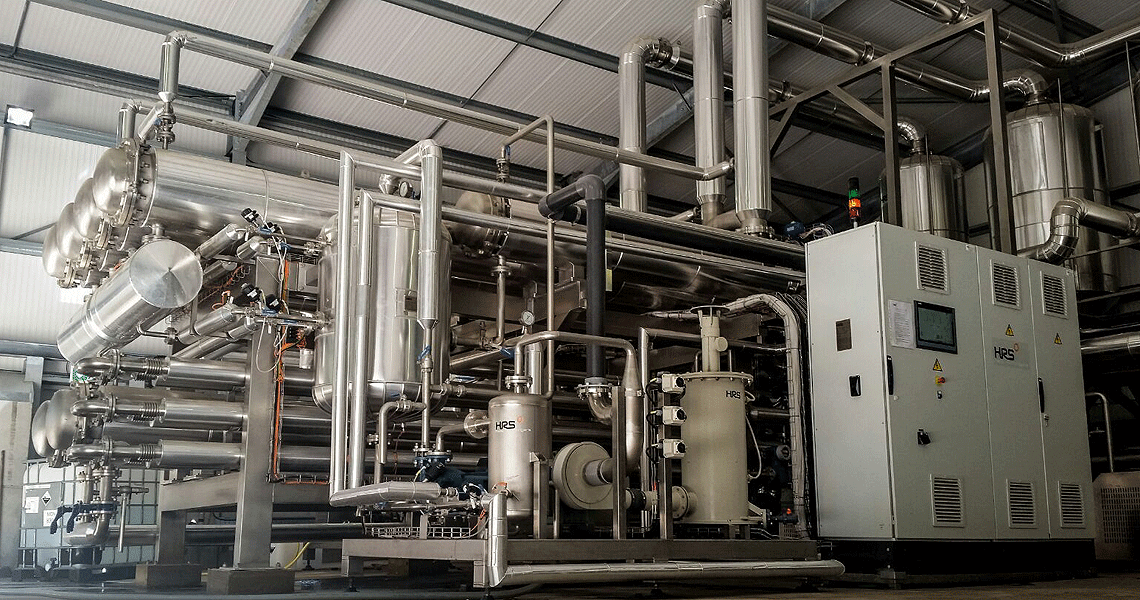
Concentration and Evaporation Systems
Where possible we aim to integrate our evaporation systems with waste heat sources to achieve an effective sustainable process.
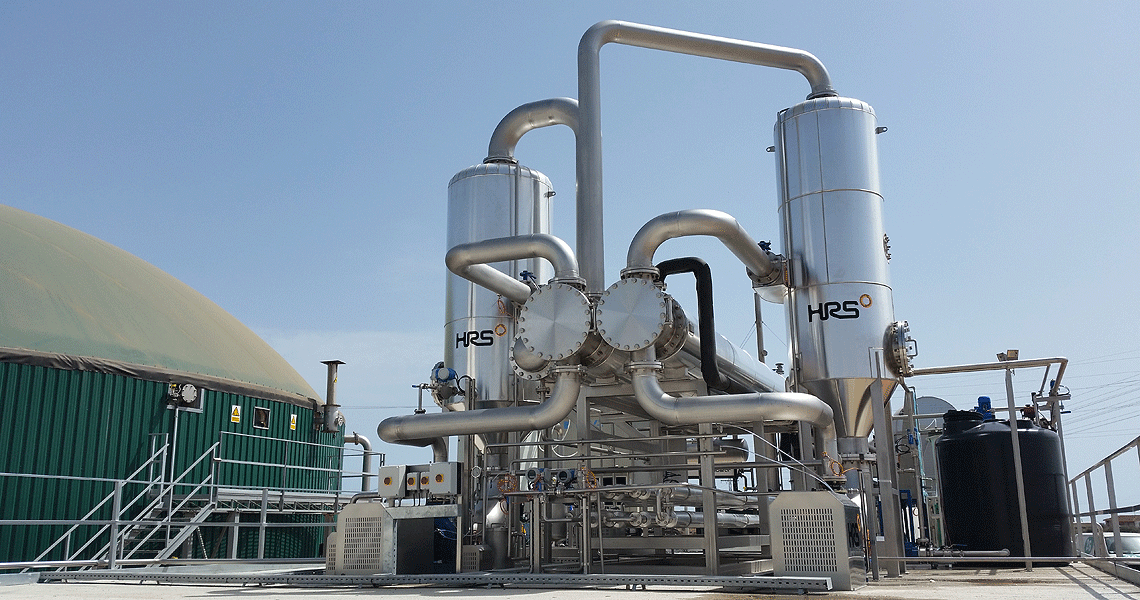
Concentration of Environmental Waste for Renewable Energy (DCS)
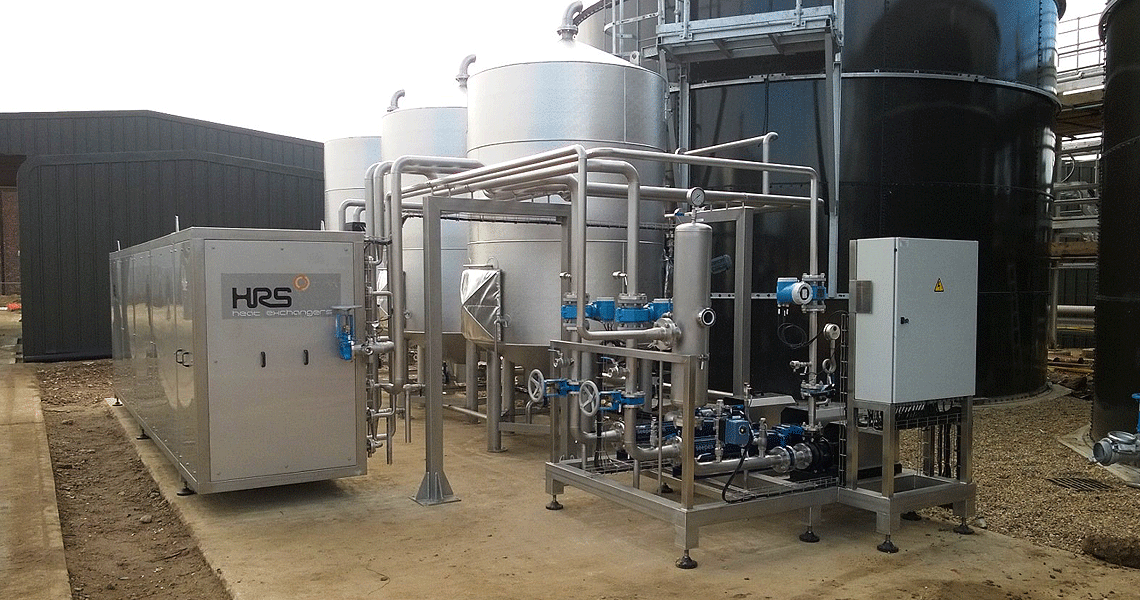
Digestate Pasteurisation for Renewable Energy (DPS)
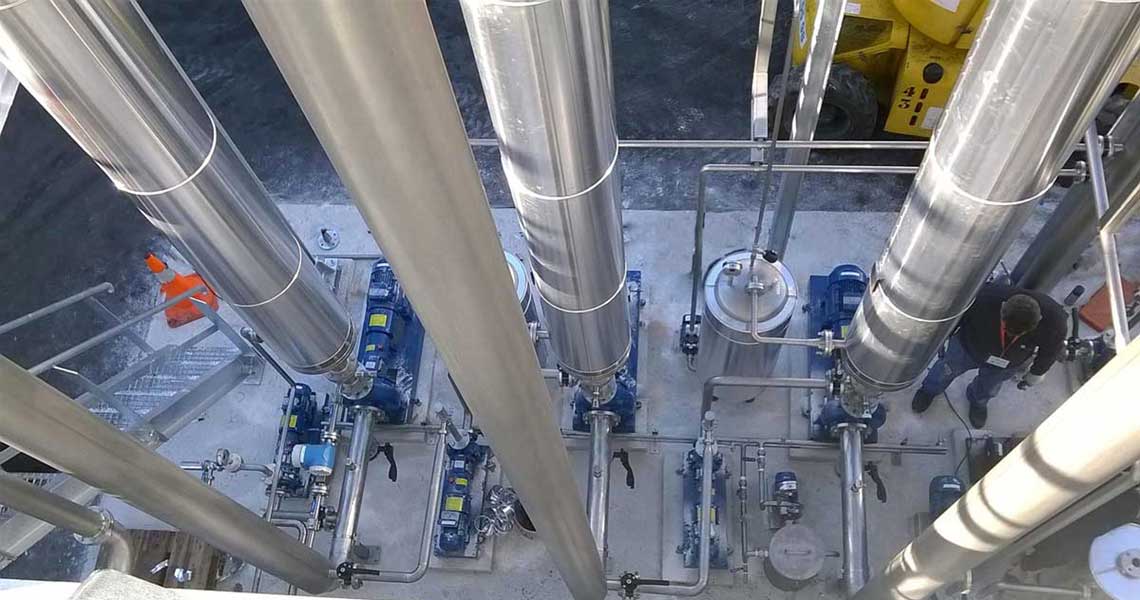
Zero Liquid Discharge (ZLD)
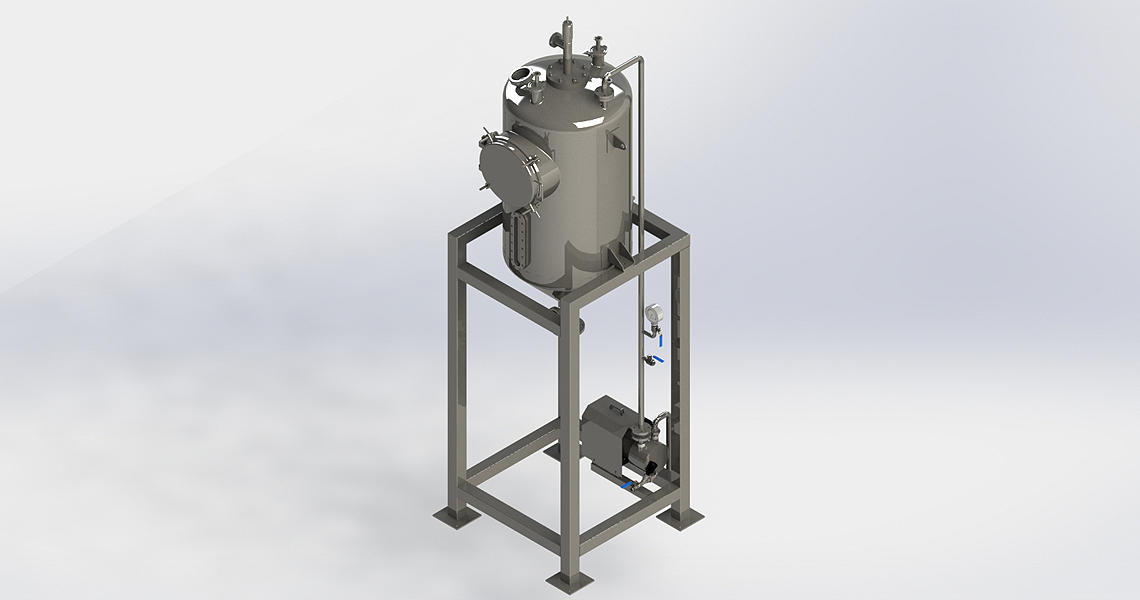
Air Removal (Deaeration) Systems
HRS has developed an air removal (deaeration) module which can be fitted into the production line before thermal treatment takes place.
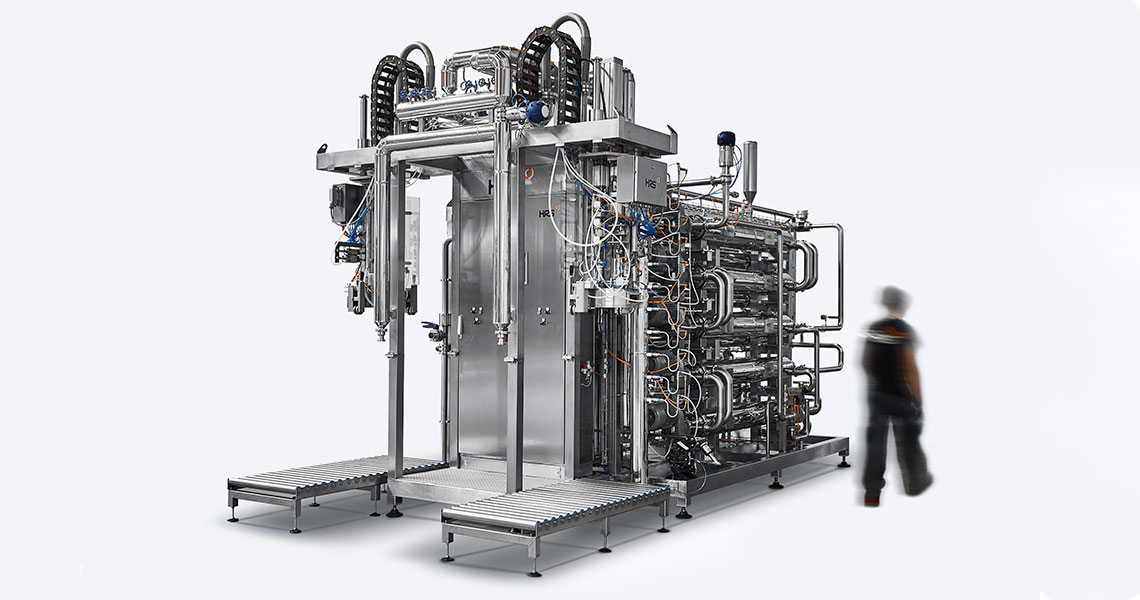
Asepticblock Pasteuriser/Steriliser
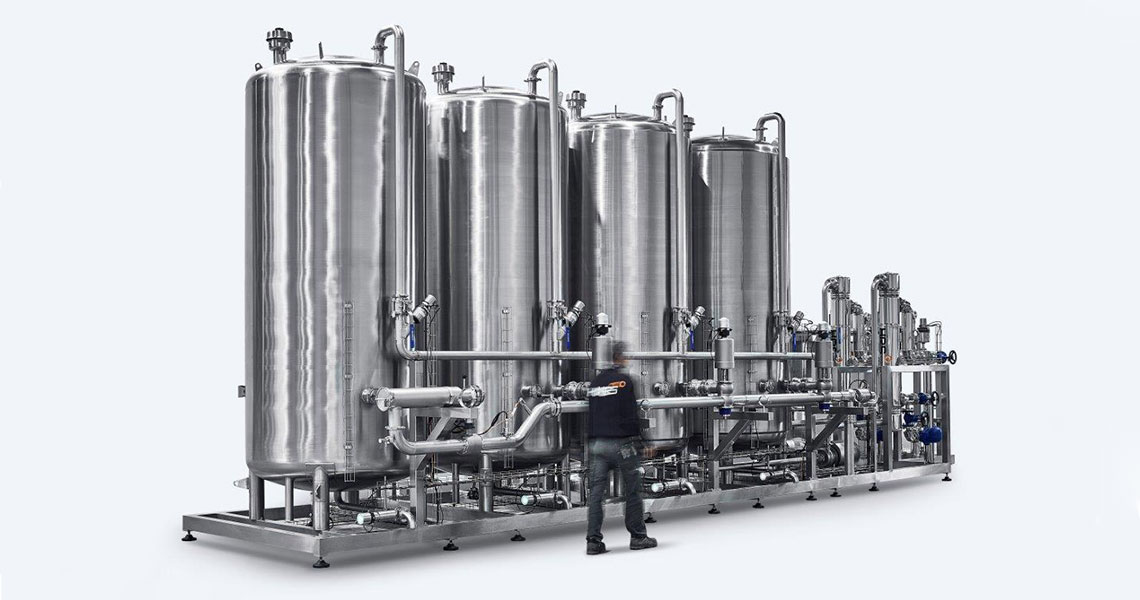
Cleaning Systems (CIP & SIP)
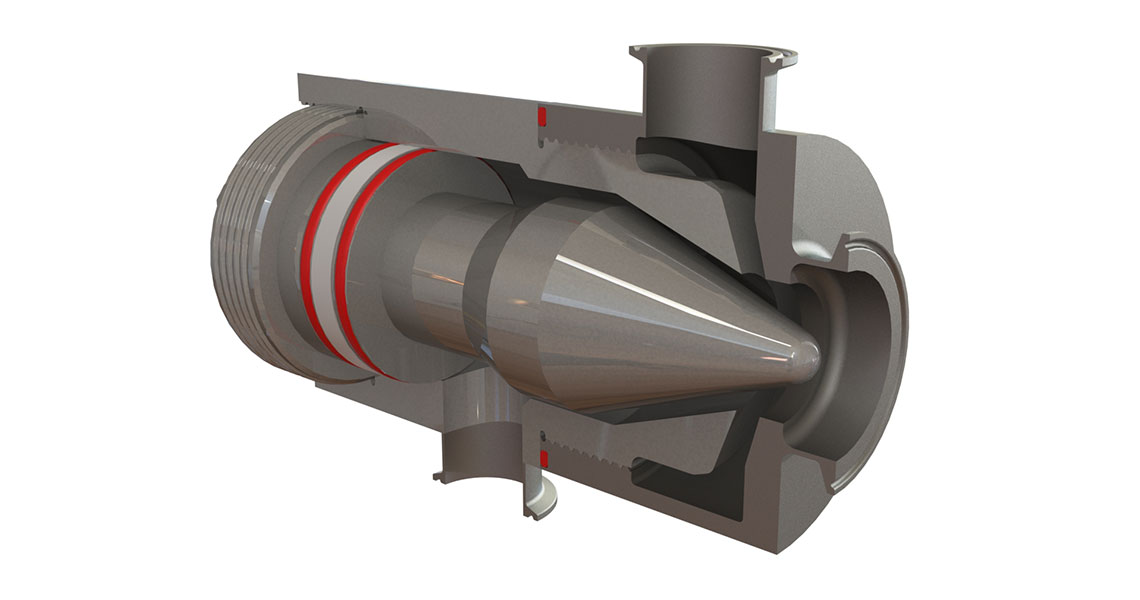
DSI (Direct Steam Injection) Steriliser
Using direct steam injection for continuous UHT treatment is commonly used for heat-sensitive low-acid products such as plant-based milks, ESL (extended shelf life) products, cream, desserts, and many other dairy products. The process is also suitable low viscosity products with small particulates such as soups and sauces, non-dairy creams, and starch-based products.
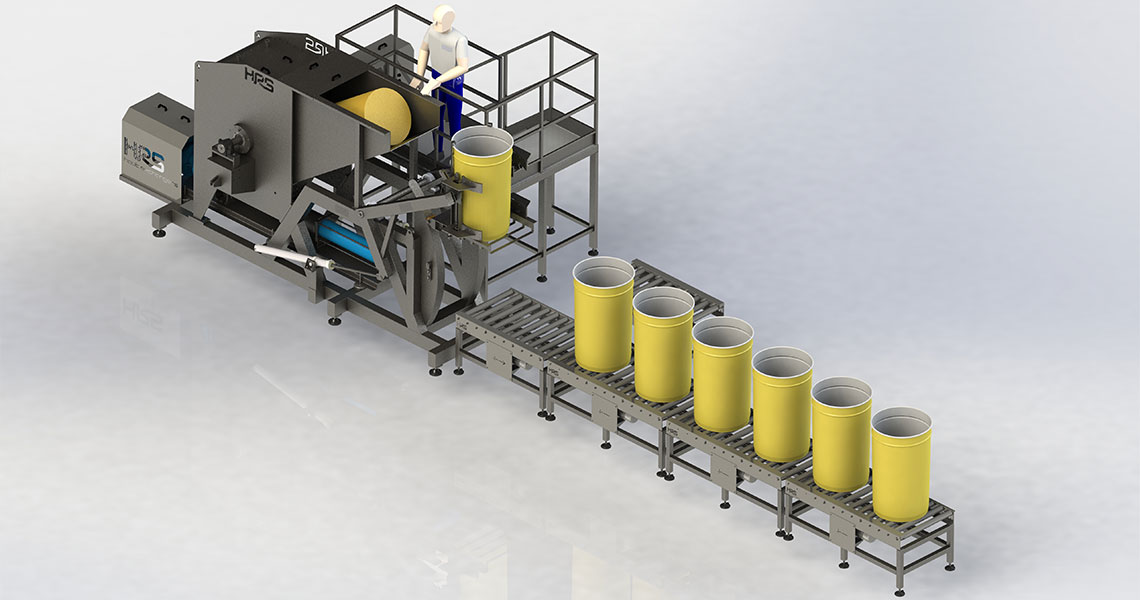
I Series (Ice Crusher & Melter)
About us
Over the years, we at HRS have offered a broad range of products, some of which include double tube heat exchangers, multitube heat exchangers, annular space − HRS AS series, scraped surface heat exchangers, plate heat exchangers, environmental systems, food processing systems, product and process trial systems, fillers, pumps and more. We as a company are fully committed to working closely with our customers in order to ensure that they are getting the best value for money when providing high-end energy recovery and process systems. We take great pride in our ability to deliver step by step improvement, save energy, reduce waste and reduce CO2 emissions.
Here at HRS Heat Exchangers, we combine our many years’ worth of knowledge and experience to provide industry-proven heat exchanger products that are second to none. Our production capacity in Europe and Asia allows us to deliver exceptional solutions on a worldwide scale, including locations such as Spain, the UK, Russia, the USA, India, Malaysia, Australia and New Zealand. Our mission is to ensure the effectiveness and continue to improve our heat exchanger systems, our vision is to minimise warranty and uphold quality production, and our objective is to comply with all legal requirements and regulations, as well as the specifications of our clients.
Our 40 years of service allows us to provide continuous improvement and outstanding product quality to a vast array of clients across the globe. Heat exchangers are used in both heating and cooling processes, and enable thermal energy from a liquid or gas to pass to another liquid or gas without the two coming into direct contact with each other. Our heat exchangers and systems are specifically designed to maximise energy efficiency, reduce any form of contamination and maximise valuable end products. Our distributor network spans across France, Sweden, Finland, Netherlands, Turkey and Germany.
We at HRS Heat Exchangers also offer a variety of services including cleaning in place systems, direct steam injection sterilisers, ice crushers and melters, deaeration, zero liquid discharge, digestate management and biogas dehumidification.
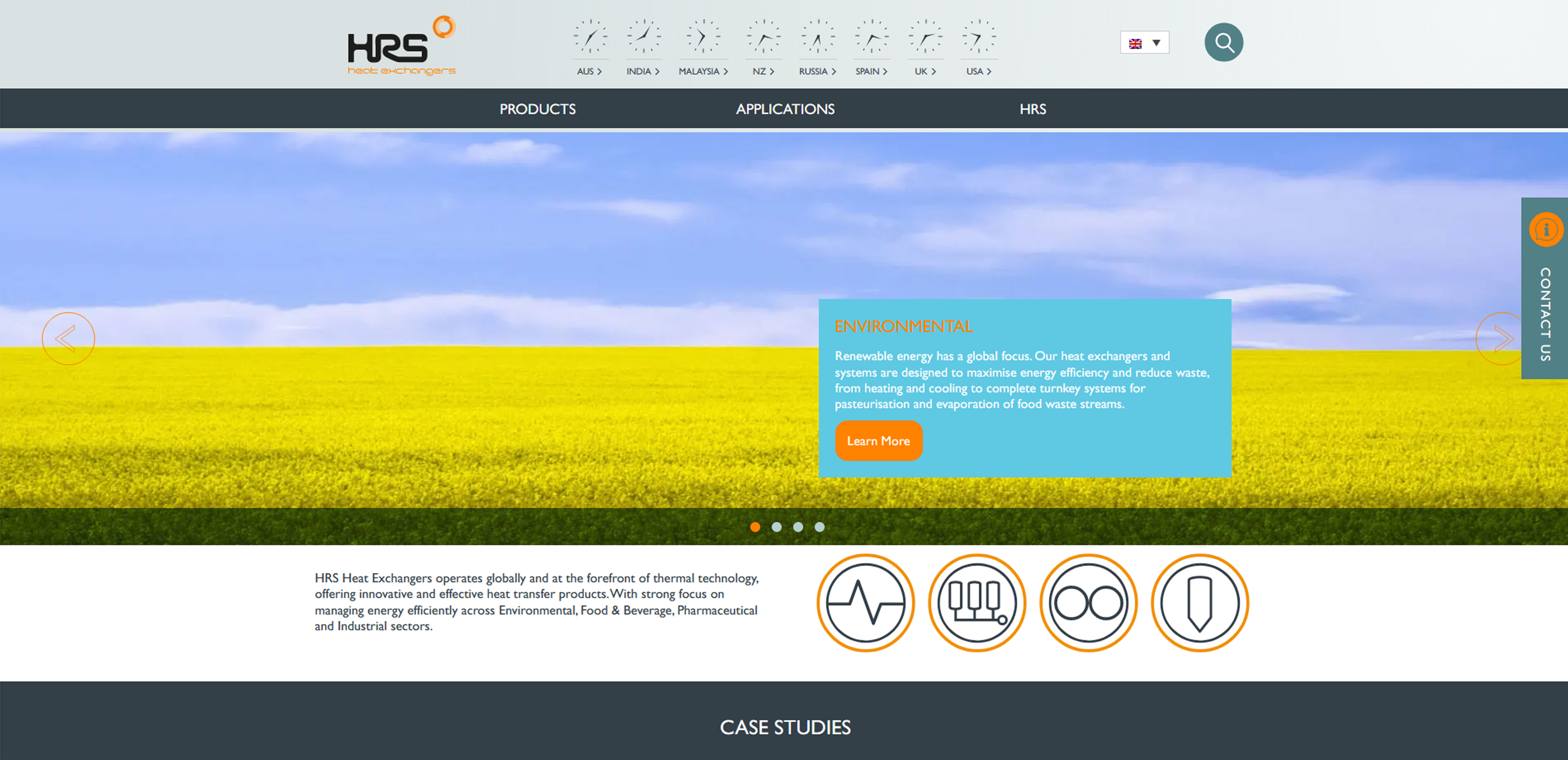