Company details for:
Inglewood Engineering Consultancy
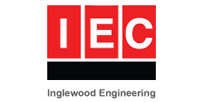
Sycamore House,
Springwood Way,
Macclesfield,
Cheshire,
SK10 2ND,
United Kingdom
Quick Links:
Products / Services
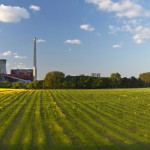
BS EN 60079 Hazardous Area Electrical Inspections
The British Standard BS EN 60079 Part 18 covers Inspections and Maintenance of Electrical Installations in Hazardous Areas. In order to comply with the standard a hazardous area inspection programme must be established. The employer must ensure that a competent body independent of the maintenance programme completes periodic inspections.
The programme is the basis for protecting against ignition sources in hazardous areas. It demonstrates good intent and is a core defence should one be needed. Within that regime every single ignition source must be accounted for, and inspection protocols put in place to demonstrate due diligence.
There are a number of inspection protocols detailed in BS EN 60079 Part 18. It refers to four inspection types − Initial, Periodic, Sample and Special (for movable apparatus); three inspections grades Visual, Close and Detailed; and a variety of inspection schedules for flameproof, intrinsically safe etc.
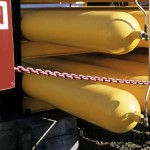
DSEAR Training
Regulation 9 states that the employer shall provide his employees with:-
’suitable and sufficient information, instruction and training on the appropriate precautions and actions to be taken by the employee in order to safeguard himself and other employees at the workplace’
Our DSEAR training modules place more emphasis on the specific needs of the workplace. We tailor these courses to suit the particular requirements of the participants. For example, technicians are typically more interested in the installation requirements of BS EN 60079 Part 14, whilst engineers would be more interested in the hazardous area design considerations.
For further information on how we can help to train your employees please use our Contact Us form or call 01625 410100.
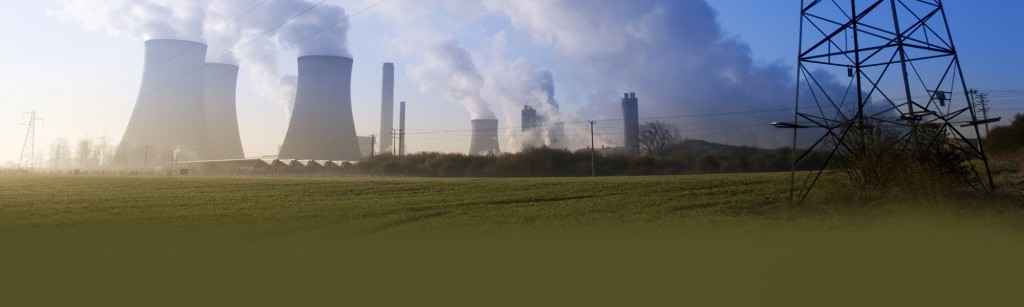
Area Classification & Risk Assessment
Our purpose is to reduce the extent of the classified areas and eliminate them if possible. We advise on ventilation, housekeeping, handling, etc where it makes a difference.
Regulation 5 of DSEAR requires that where a dangerous substance is or is liable to be present at the workplace, the employer shall make a suitable and sufficient assessment of the risks to his employees which arise from that substance.
Part of Regulation 7 of DSEAR requires that the employer classifies places at the workplace where an explosive atmosphere may occur into hazardous or non-hazardous places i.e. a hazardous area study must be completed.
It is vital that an accurate area classification study is completed. For instance, it is undeniably dangerous if an area is classified safe when it is actually hazardous. Much less appreciated are the consequences of getting it wrong the other way. An area that is over-classified will drain profits from your company for as long as it remains so; initially in the form of an overly expensive installation, thereafter in costly maintenance and inspection.
We classify areas in line with the harmonized standard BS EN 60079-10, also with the model code of practice if there is a connection with a particular industry e.g. Energy Institute EI15, Institute of Gas Engineers IGE SR25 etc.
A formal report is provided for your records along with the area classification drawings and supporting calculations that go with it.
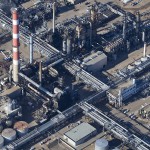
DSEAR Services
Should you need specific assistance our experts will help you determine the hazard level by guiding you through the formalities of Risk Assessment and Area Classification. Our engineers will check that your plant is suitably protected against ignition sources in hazardous areas. Our engineers will also address any issues that may arise and offer remedial design solutions.
We also advise on work place training and the establishment of an ongoing DSEAR regime to demonstrate continuing compliance. Should you need support we can represent you in discussions with the HSE.
Our overall purpose is to ensure that you are able to achieve and demonstrate compliance with the relevant DSEAR and BS EN 60079 codes of practice. We do this in the most expeditious way by providing practical advice and support, so that you are not left with a list of further problems following our intervention. Subsequently you can face up to any regulatory scrutiny with confidence.
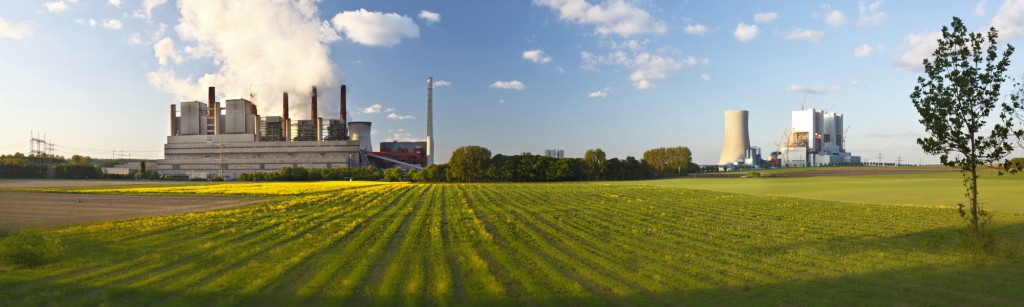
Hazardous Area Compliance
During this time we have built up an enviable client list of blue chip national and international companies that employ us for our specialist knowledge in hazardous areas (now regulated by DSEAR). Due to the variety and breadth of that list we have an experienced workforce that’s ideally suited to advising individual clients as to their industry’s best practice.
Our experience pre-dates DSEAR and the current harmonised standards by many years and by a number of previous standards. A lot of our work is still on sites that were built pre-ATEX, and our knowledge enables us to cut through the legacy that typifies older installations. We offer pragmatic solutions to DSEAR non-conformances, from straightforward advice to expert redesign.
Proof of competency is a basic requirement, and to this end we ensure our engineers hold a recognised certificate of such, notably by way of the Comp’Ex and IECEx accreditations.
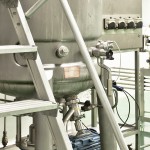
Post Inspection Support Services
We advocate using your own staff to sort things out where possible; the gains are more likely to become embedded. Sometimes though even your control/electrical engineers will be put to the test and you will need to call on expert help.
In this respect our engineering credentials are second to none. We are professional engineers by qualification and training, and have spent most of our working lives designing control, electrical and instrument installations in hazardous areas. We know what constitutes compliance and we know what has to be done to achieve it.
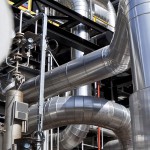
Static Earthing Compliance
If you are unsure what your position is we will audit your installation and make recommendations based on the code of practice. We can advise and assist with the scheduling of static earth bond tests for fixed and portable equipment, and help you set up a periodic inspection and testing regime. Inglewood Engineering are proficient practitioners and have the necessary certified test equipment to validate your static earth systems out on the plant in hazardous areas.
The Code of Practice for the avoidance of hazards due to static electricity is PD CLC/TR 60079-32-1:2015.
The accumulation of electrostatic charge, on equipment or personnel, can give rise to all sorts of problems in a wide range of premises. A static discharge can be the source of an ignition and explosion. So wherever DSEAR applies static must be brought under control, in chemicals, pharmaceuticals, petroleum and food processing industries etc.
The safe management of static requires an understanding of both the physics and the engineering of the actual circumstances. Earthing and bonding typically play a role in charge suppression but a misunderstanding of the process can lead to questionable results. Often there is inherent equalization of potential via the building structure and additional bonding is unnecessary. This is not the case where there are non-conducting structural components and dedicated bonds will need to be considered, or other anti static mechanisms.
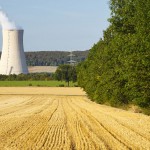
Non-Electrical Equipment Risk Assessments
Typical examples of existing non-electrical equipment that require risk assessment are solenoid valves, pumps, conveyor belts, hoists, gearboxes, brakes etc.
Inglewood complete the site audit, inspection work and risk assessment reports to ensure the client Dutyholder meets his compliance duties in respect of non-electrical equipment.
The risk assessment process takes into account the nature of the zone that the equipment is positioned in, the properties of the dangerous substance, risk of ignition due to the type of non-electrical equipment and the guidance given in standards.
The equipment manufacturers’ technical specifications, drawings, operating information and any associated maintenance records (including records of any failures relating to the equipment concerned) are reviewed as part of the risk assessment.
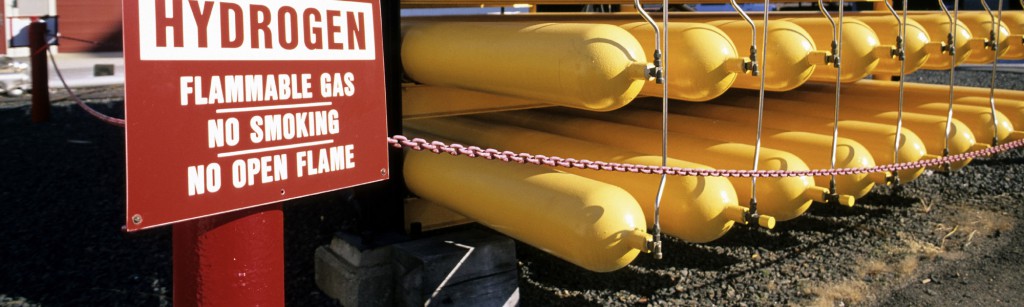
Design / Engineering in Hazardous Areas
Our expertise has proved invaluable in the early stages of new builds, at a time when expensive mistakes can be avoided. It also comes to the fore when engineering solutions to problems that arise in existing installations.
Regular inspections of existing installations are a means of highlighting any irregularities. Often the non-conformances that come to light during an inspection are minor and simple to rectify. Sometimes equipment that at first sight is unsuitable may pass the risk assessment that comes from the Essential Safety and Health Requirements, and be permitted to remain in situ. But where non-conformances are found that cannot be justified with an equipment risk assessment or rectified by a simple remedial action, we will advise on equipment replacement or redesign that part of the installation, as appropriate.
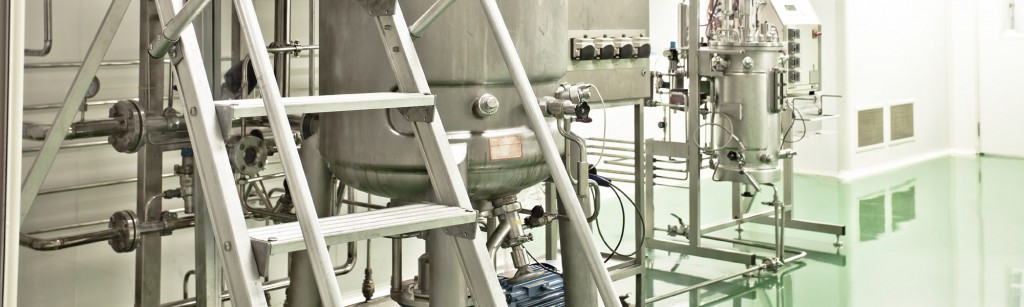
Intrinsically Safe Descriptive System Documents
An Intrinsically Safe Descriptive System Document demonstrates compliance by proving that the energy limiting device, the barrier, is compatible with the field device in terms of power, capacitance and inductance values.
These are documents that are often hard to come by, particularly in older establishments. In keeping with their importance it is necessary at times for us to rewrite them using information gathered from the installation itself.
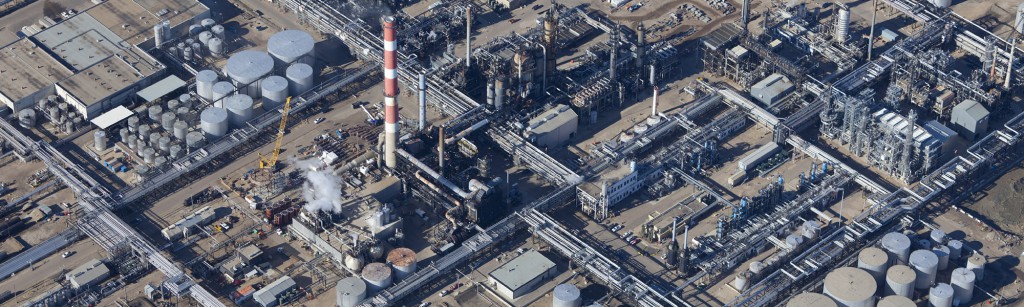
Explosion Protection Document
Article 8 of ATEX 137 details the exact requirements of the EPD. Its completion follows on from the risk assessment and area classification actions.
A number of companies in the UK have gone down the EPD route and drawn on our skills and experience to assemble this quality document.
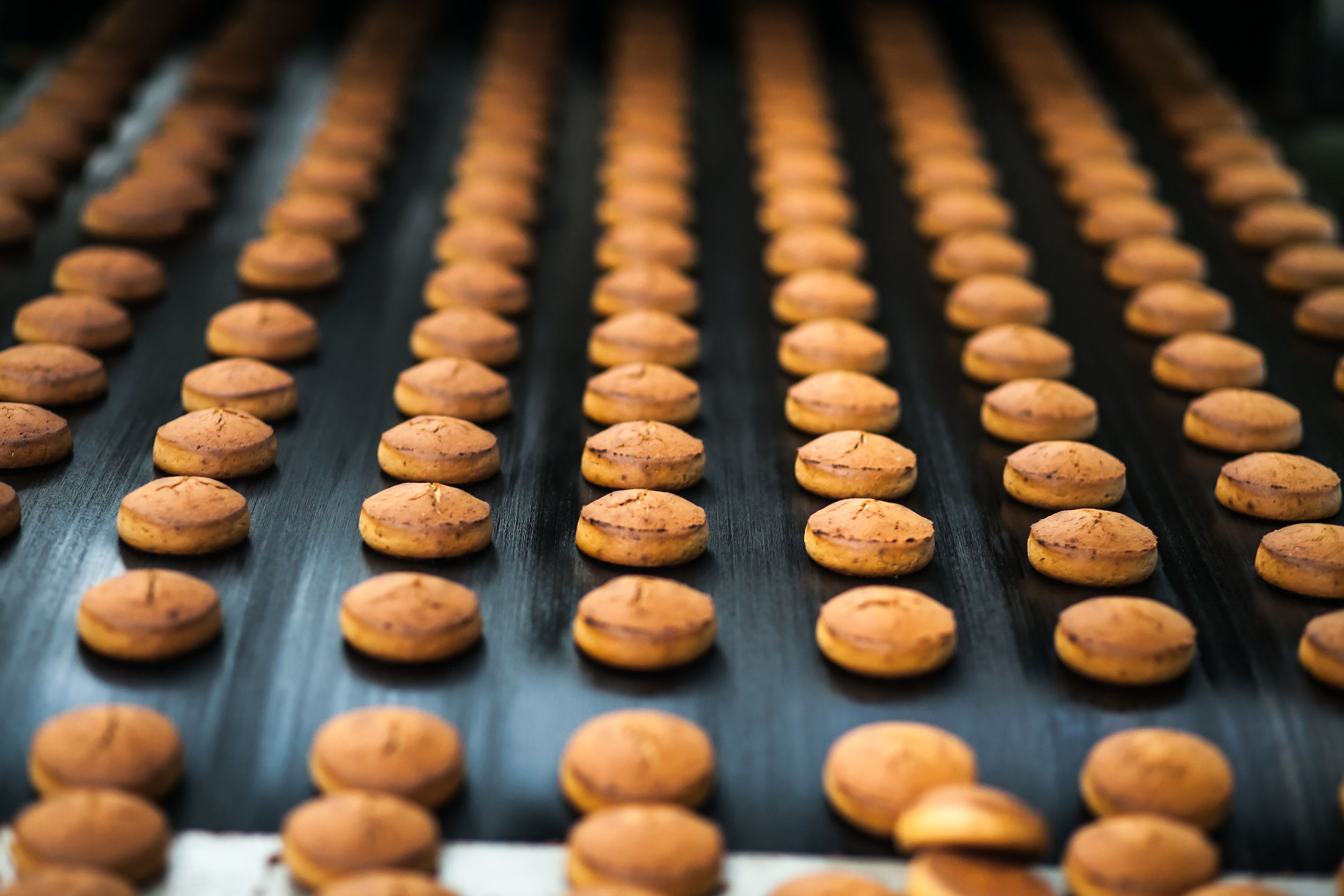
BS 7671 Inspection & Testing Audits
Chapter 62 in the IET Wiring Regulations covers Periodic Inspection and Testing requirements. Regulation 621-01 states that periodic inspection and testing of an electrical installation shall be carried out to determine, so far as is reasonably practicable, whether the installation is in a satisfactory condition for continued service.
Regulation 622-01 stipulates that the scope of the periodic inspection and testing shall be decided by a competent person, taking into account the availability of records and the use, condition and nature of the installation.
Table 3.3 in the IET Inspection and Testing Guidance Note 3, indicates which periodic tests are to be carried out on existing installations. The person carrying out the testing is required to decide which of the tests are appropriate by using their experience and knowledge of the installation being inspected and tested and by consulting any available records.
It is important that any periodic inspection and testing regime put in place meets the standards of the codes of practice but at the same time is a practical operation which can be completed efficiently and with minimum disruption to the business. The ability of the company to clearly demonstrate compliance is a key requirement of any new periodic inspection/testing package.
Periodic inspection and testing is necessary because all electrical installations deteriorate due to a number of factors such as ageing, excessive electrical loading, corrosion and general wear and tear.
A periodic test and inspection may be less onerous than an initial one. Completing unnecessary periodic testing can be dangerous, disruptive and costly. This is often misunderstood by companies wishing to achieve legal compliance.
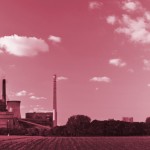
Safety Instrumented Systems Capability
Inglewood Engineering has worked continuously for a number of these companies since its formation in 1983. Our engineers have lived with the standards as they have evolved and are as familiar as any practitioners with what is required to comply. However, it is important that those engineers who are practising in this field are independently assessed and validated so that customers can have true confidence in their abilities. To this end our personnel seek and have attained the coveted accreditation of TÜV Functional Safety Engineer.
At Inglewood, we are involved with initial hazard analysis, determination of risk reduction, production of the safety requirements specification, defining the safety integrity levels, safety instrumented system design, system reliability calculations and site trip testing.
We regularly audit existing plant alarm and trip systems to ensure compliance with the latest standards.
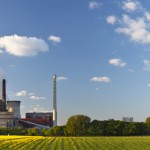
DSEAR Site Audit
The audit takes the form of a formal step-by-step review of your installation, policies and procedures against the provisions imposed by DSEAR. An engineer leads the review and their findings are reported to you in terms of practical recommendations that point the way to full compliance.
We undertake this service throughout the UK wherever DSEAR applies, in new builds, at existing sites that are still not compliant, and following plant modifications.
And of course, we agree a fixed price up front before work commences.
It is essential to get your DSEAR response right. Overdoing it can be unnecessarily costly; doing too little can turn out more so. We offer an independent audit that is straightforward and authoritative, and one that promises a constructive route to compliance right from the outset.
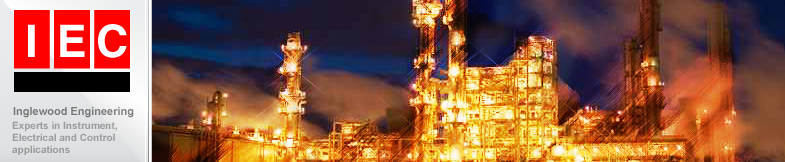
Non-Conformance Management
Non-Conformances, or snags, are categorised as Critical, Major or Minor during site inspections in order to prioritise the resulting actions. The Corrective Action Schedule report then presents our findings in a form that collates the issues for easy handling.
Typically we would advise the client on the most effective way to deal with the non-conformances. This may best be done by the client’s own workforce. If that is not feasible we will provide the means to expedite the remedial work.
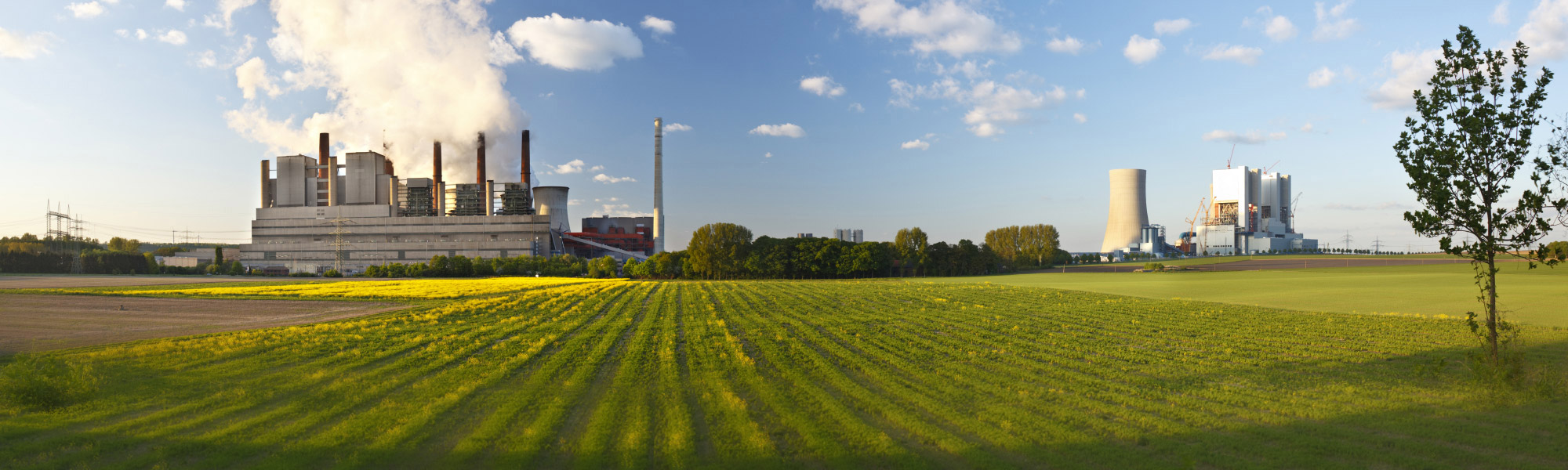
EAWR Electrical Compliance − Experience
Our design office specialises in electrical building services and cut-and-carve modifications to control and electrical plant. We use the latest design verification software and AutoCAD for drawings, to support our engineers and designers. Our inspectors are fully qualified and have generally progressed from a design background.
We have completed Electricity at Work Regulations (EAWR) audits and BS 7671 inspection and testing services for all types of premises. These include hazardous areas, safe areas, industrial areas, laboratories, office buildings etc. We draw on a proud history of service to many organisations, both national and international, to advise our clients and help make their premises compliant.
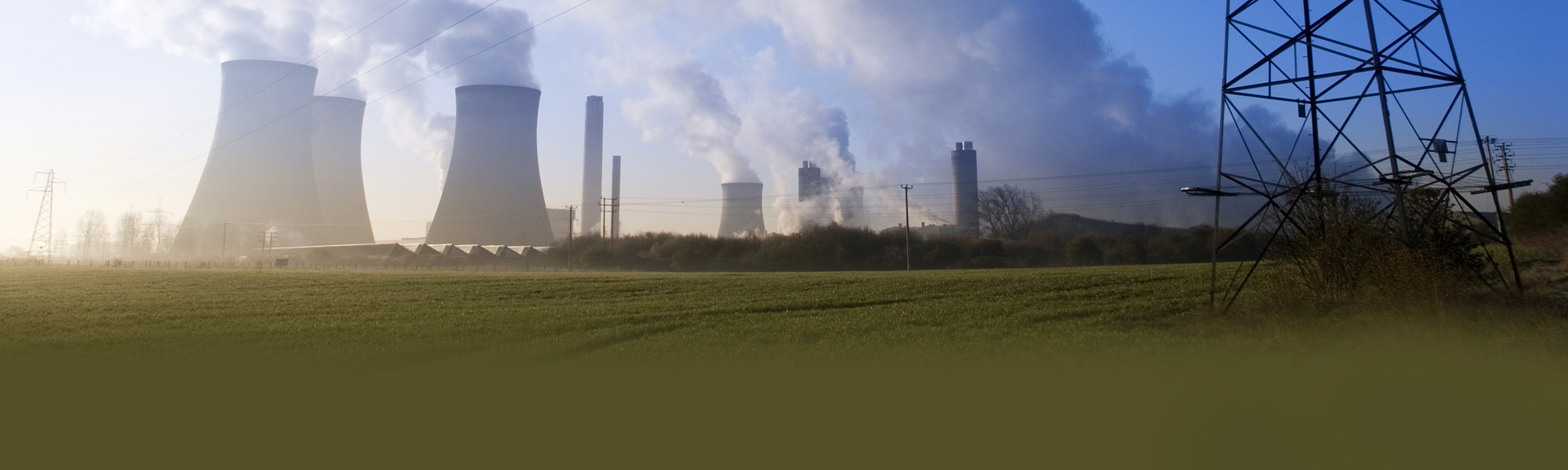
EAWR Compliance − Services
Should more be needed we provide a full inspection/testing service. This is backed up by a team of professionals, headed by a Chartered Electrical Engineer, who will advise on any issues. Electrical distribution can easily get out of control and cause supply problems, especially in large networks. Pinpointing improvements in maintenance and design can save both time and money.
We always seek the best way of working with our clients. This invariably means working closely with the local technicians who are familiar with the particularities of the site.
Ultimately we aim to ensure that the client is able to achieve and demonstrate compliance with the relevant parts of the Electricity at Work Regulations, whilst operating a dependable electrical distribution network.
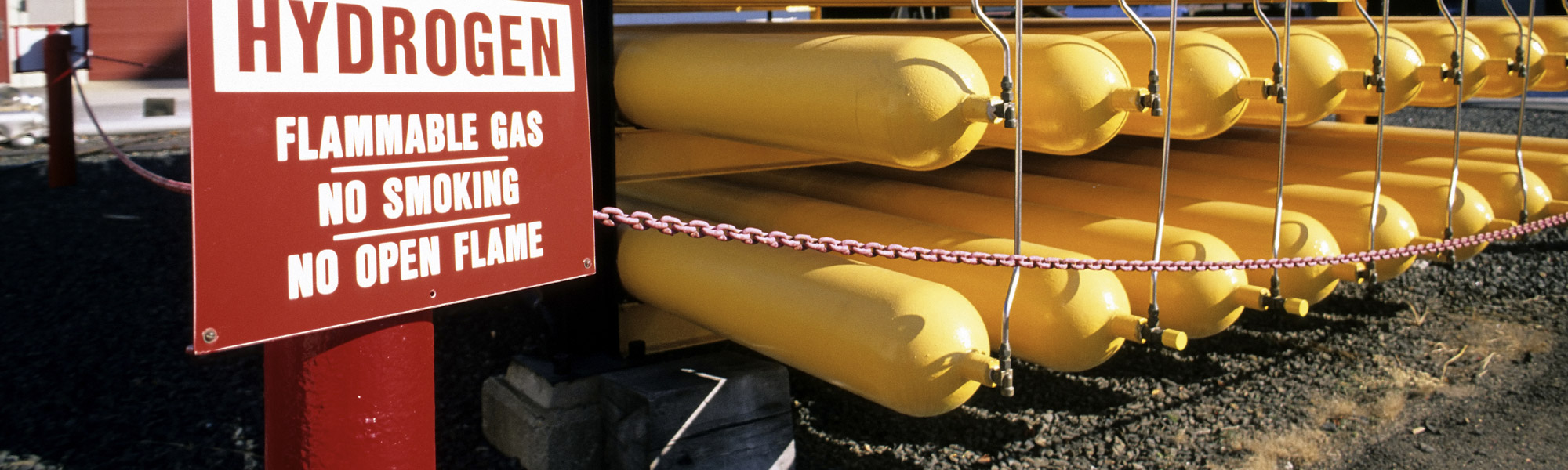
EAWR Audits
Our compliance engineers conduct a thorough review of the physical state of the installation, and the relevant documentation records. This covers electrical distribution equipment as required by the EAWR. The audit report then details what needs to be done to achieve compliance.
Inglewood carry out audits on new installations, existing buildings and plant modifications, and agree a fixed fee before work commences.
An independent assessment by a competent body offers additional assurance to your company. It’s a statement of how effective your current practices are. And it gives you time to get your house in order. Unfortunately that’s something you wouldn’t necessarily get after a surprise visit from the HSE.
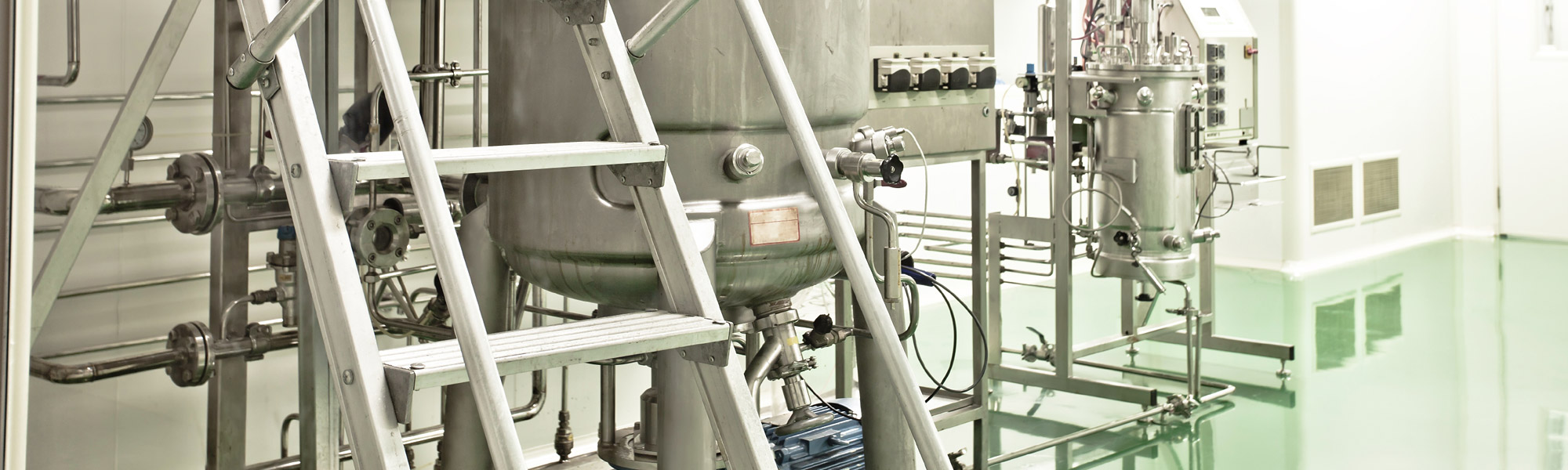
Single Line Diagram & Record Compliance Documentation Updates
It is vital that items of sub-distribution have unambiguous labelling that corresponds with the master site electrical single line diagram. Our engineers verify which circuit is which by test, and fit new labels as required.
It is also important that final circuits are properly identified. Where this is not the case, we will ascertain the final circuit arrangement and provide new electronic schedules for inclusion with your site documentation.
Depending on the size of the installation you may hold a variety of electrical record drawings, motor schematics, lighting and small power layouts etc. And if these need to be brought up to date we will take care of that back at our office.
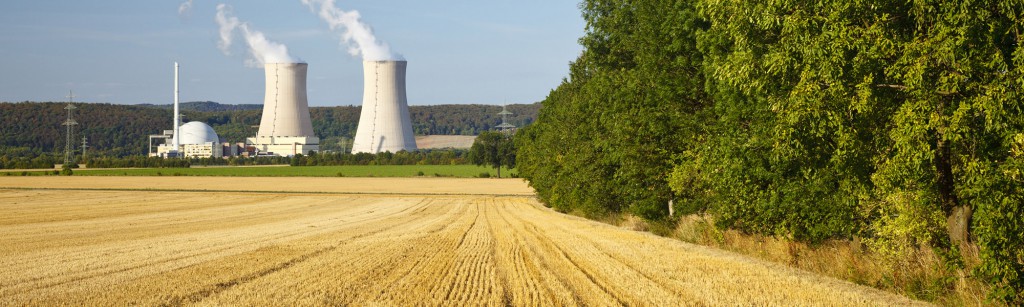
Instrument & Control Design
We are familiar with Scada systems, PLC control and relay logic and are used to developing control packages from initial concept to final installation. Modifications to existing plant is a frequent requirement and one with which we are skilled.
Our scopes of work are tailored to the needs of the task. As appropriate we produce User Requirements Specifications and Instrument Specifications, and design the Control Loops, Control Panels, and Plant Layouts etc that are characteristic of a well designed job.
Following on from design it is normal for us to carry out the functional testing of the completed installation and support our client with his commissioning.
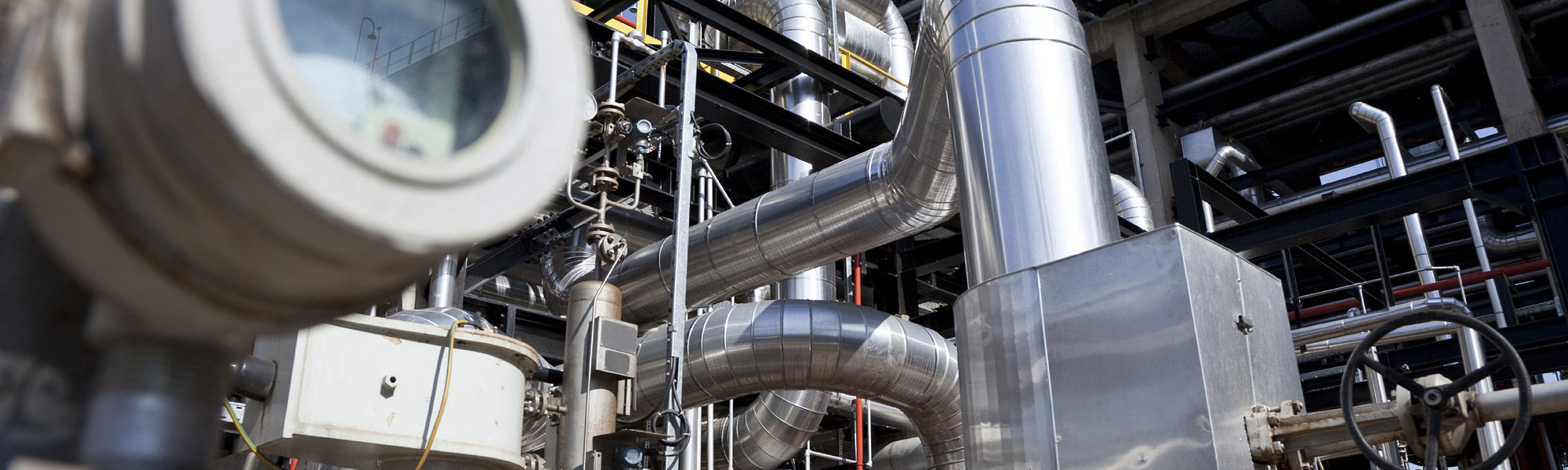
Building Services Electrical Design
Our design capability includes lighting and small power design, emergency lighting design, earthing system design, HVAC electrical and control design and uninterruptible power system packages.
In addition to mains power design, we design building fire alarm systems, data and telephone infrastructure, security system and building access solutions.
To learn more about our building design services and the assessments we carry out fill in our contact form or call 01625 410100 and speak to a member of our team.
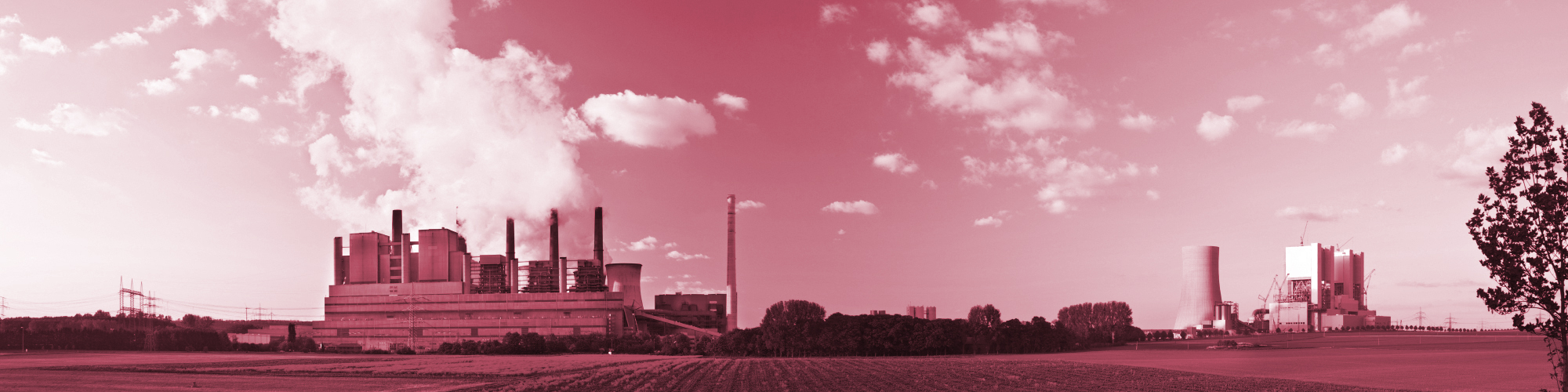
Electrical Distribution Design
We are equally comfortable producing full office/industrial design packages or minor modifications to existing distribution systems depending on the client’s requirements.
Past work includes high integrity supply arrangements for powering computer centres and other critical load installations that may require uninterruptible power systems, generator back-up facilities or mains changeover options.
Our design solutions come complete with the necessary technical backup; connected load calculations, discrimination checks, cable design details, earthing philosophy etc.
Drawings are produced in Autocad and include layouts as required for clarity, e.g. switchroom, cable containment, together with record drawings such as Single Line Diagrams and schematics.
To learn more about our electrical distribution design services and the assessments we carry out fill in our contact form or call 01625 410100 and speak to a member of our team.
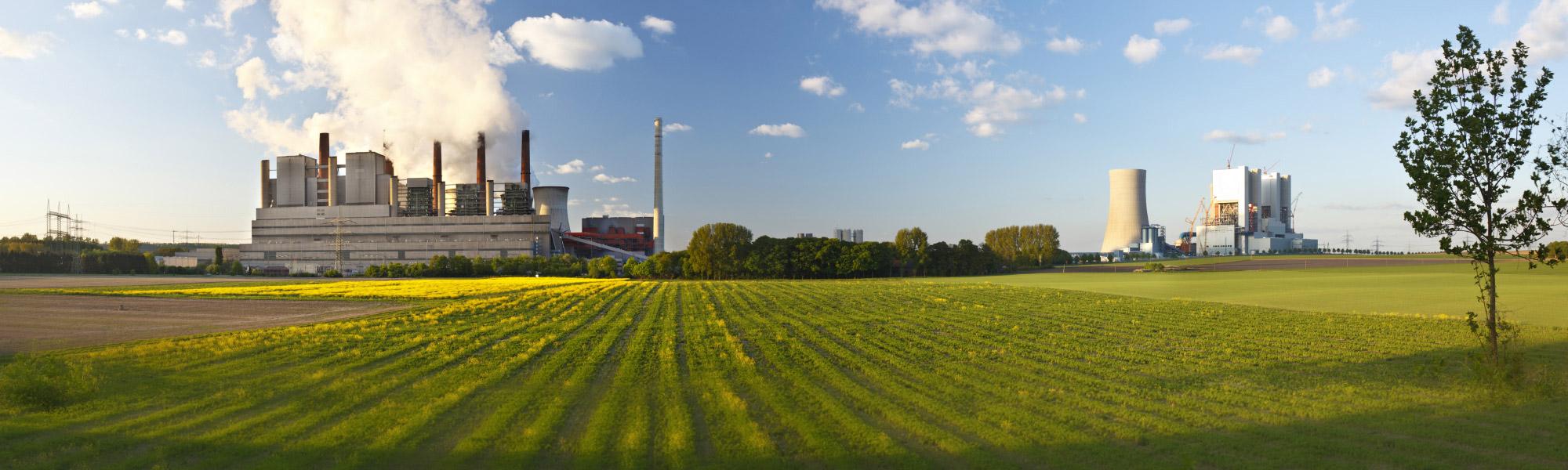
Control Panel Design
We work closely with our client, observing any limitations imposed by the site and establishing the functional and operational needs of the job. Typically this will entail some site investigation and assessment of existing documentation.
We offer a complete service in conjunction with recommended panel manufacturers for those clients who prefer to outsource delivery to a single supplier. This includes factory acceptance tests, functional testing in situ and commissioning support. For panels situated in hazardous areas this would also include detailed inspections required by DSEAR for new installations.
To learn more about our control panel design services and the assessments we carry out fill in our contact form or call 01625 410100 and speak to a member of our team.
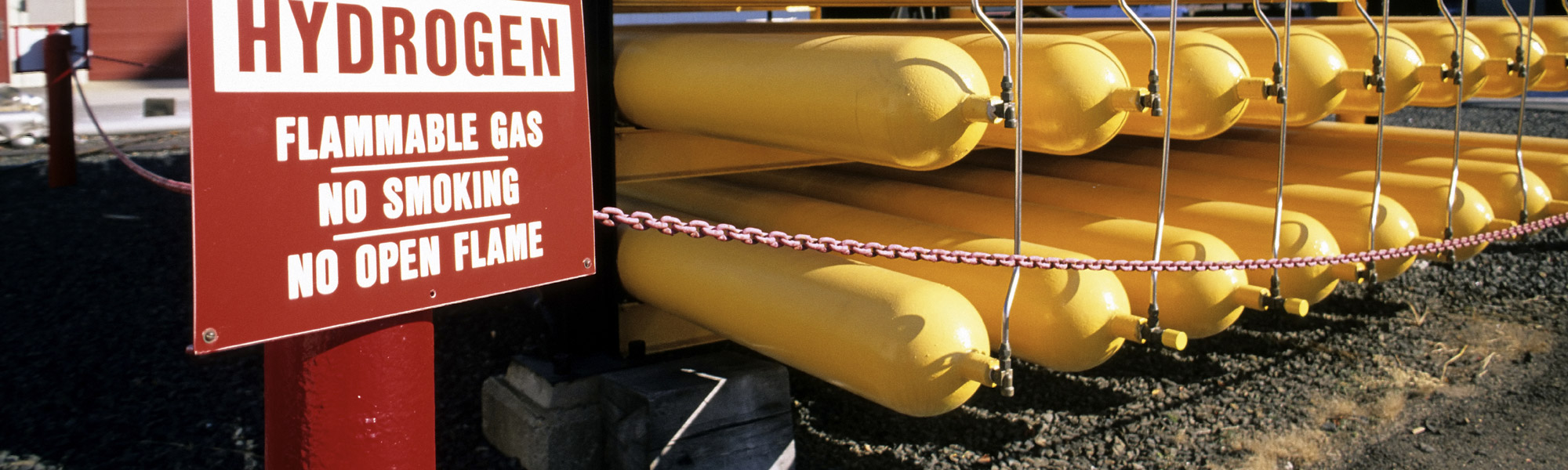
Loop Drawings
As part of our inspection work we check that what is installed matches the existing drawings. If there are discrepancies, we bring these to your attention and can revise them as part of the process.
Our interest in terms of DSEAR will primarily be related to the hazardous area. An Intrinsic Safety Diagram may be the most effective way of depicting and recording the safety essentials of a full instrument loop.
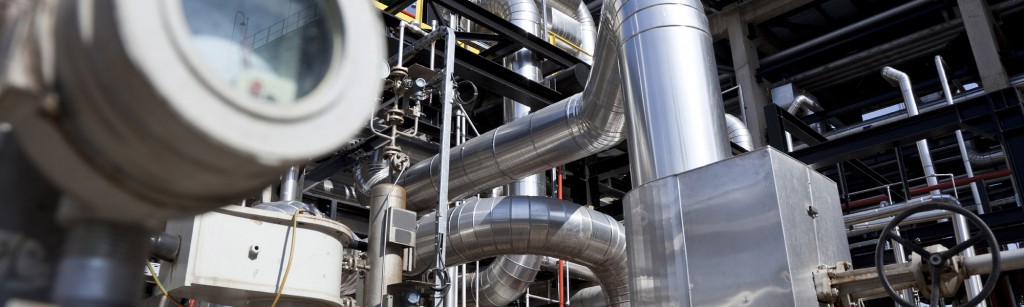
DSEAR Management Tool − Complied Electrics
That’s the safety and regulatory aspect. But it also makes sense economically; to use the information gained during the verification of a new plant, now mandatory under DSEAR, as the platform for an inexpensive compliance regime.
Complied Electrics, exclusively on offer through Inglewood, is designed to answer any regulatory concerns and to keep you in efficient control.
Its features include:-
Web based system − it can be accessed from anywhere in the World using a standard Web browser.
Any registered user may access or update information as required.
No special software required.
Inventory focussed. Register of all equipment ignition sources in the hazardous area.
Unlimited number of items of equipment.
Unlimited number of users.
Remote access to previous inspections of an item of equipment, demonstrating signed-off compliance with appropriate 60079 protocol.
Timeline of inspections, demonstrating on-going compliance regime in place.
Access to applicable hazardous area equipment certificates.
Search & retrieve facilities.
Built-in Audit trail and change control.
Non-conformance tracker tools.
About us
Based in Cheshire, our company follows specific regulations and legislation that relate to hazardous areas, electrical equipment and safety instrumented systems.
Over the years, we at Inglewood have built our reputation by distributing our high quality solutions to a wide variety of industries and sectors. Some of these include laboratories, cement works, airports, food manufacturers, power stations, office buildings, fuel depots, petrol stations, chemical plants, stores, pharmaceutical sites, nuclear facilities and ministry of defence sites.
Inglewood Engineering have developed a number of new and innovative electrical solutions that are each carefully designed to meet the requirements of our clients. Many organisations scattered across the country have benefitted from our service as well as our bespoke systems that are guaranteed to last.
We as a company specialise in assessment, inspection and design of instrument, electrical and control equipment, resulting in us becoming leading experts in industrial electrical compliance. Working closely with companies to discover the best fit for them, we at Inglewood can determine the extent of any risk and establish any long term practices to make sure everything is in working order.
Some of the services we offer here at Inglewood Engineering include;
DSEAR Compliance − Hazardous Area Compliance, Hazardous Area Legislation, DSEAR Services, DSEAR Site Audit, Area Classification & Risk Assessment, Loop Drawings, Post Inspection Support Services, Equipment Risk Assessments, Static Earthing Compliance, Complied Electrics.
EAWR Compliance − Electrical Compliance, Compliance Management, Electricity at Work Regulations, Electrical Inspection & Testing.
Safety Instrumented Systems
Design − Instrument & Control, Building Services Electrical, Control Panel, Electrical Distribution.
Articles / Press Releases
Trade Associations
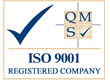
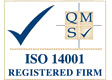
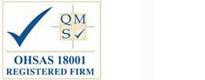