Company details for:
Knight Strip Metals
Linkside Business Centre,
Cranborne Industrial Estate,
Summit Road,
Potters Bar,
Hertfordshire,
EN6 3JL,
United Kingdom
Quick Links:
Products / Services
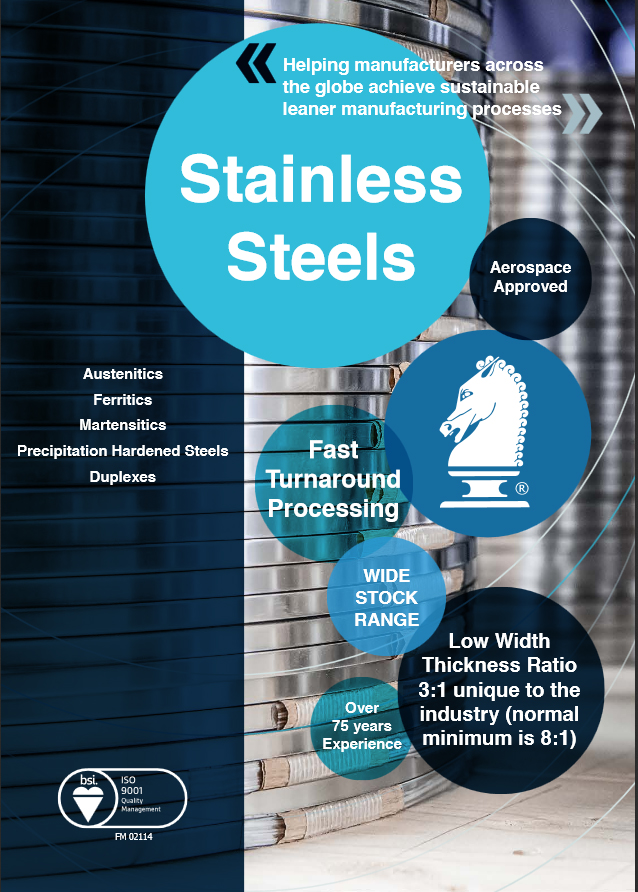
Austenitic Stainless Steels
The most common Stainless Steel among Manufacturers are the Austenitic 300 Series Alloys. These alloys offer the full range of possibilities available when altering alloying levels. In the fully annealed condition, they are essentially non-magnetic. Nonetheless, cold working of the less alloyed grades will induce structural changes leading to increased levels of magnetism. Grades with a lower Carbon content are identifiable with the addition of the “L” after their name. The cost of 300 Series fluctuates due to the availability and cost of Nickel.
200 Series Alloys contain a lower Nickel content and additional Nitrogen. Consequently, this makes 200 Series Stainless Steels a lower cost alternative to the 300 Series.
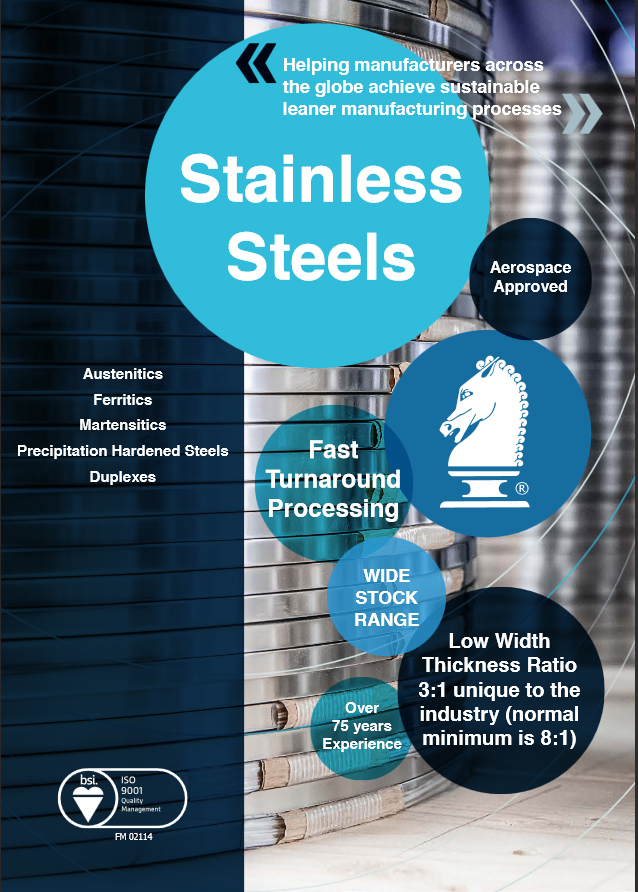
Ferritic Stainless Steels
Nonetheless, Ferritic Stainless Steels are the ideal solution for high volume applications, particularly in domestic environment where moderate corrosion resistance is acceptable. Application include hinges and stays in the UPVC window hardware industry, domestic appliances such as washing machines, cutlery and kitchen utensils. Ferritic Grades can also be found in a range of Automotive applications, including exhaust systems and trims.
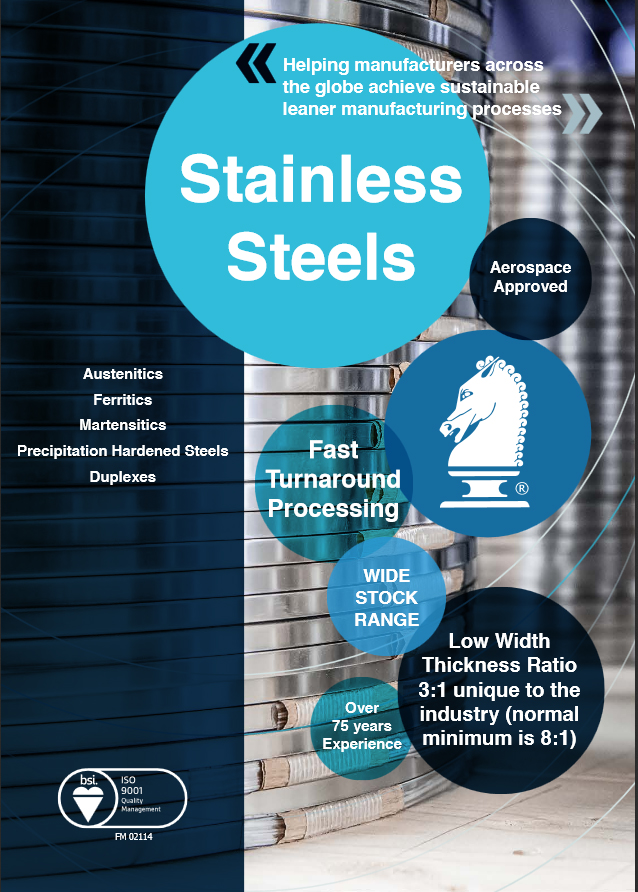
Martensitic Stainless Steels
Martensitic grades equally share similarities with some Carbon Steels. To improve toughness and ductility, they undergo a hardening process of quenching then tempering. Ultimately, it is the Carbon content of the alloy increases the strength properties. However, increasing Carbon to increase strength, consequently comes at the expense of toughness and ductility.
As a result of its low cost and moderate corrosion resistance, this group is ideal for many applications. In fact it was the first to be commercially developed as cutlery steel. However, it is its high strength and toughness properties that result in Martensitic grades being found across multiple industry sectors. Uses include surgical instruments within hospitals, valves, pumps and other components for the Oil and Gas industry, through to turbines and gears in Aerospace manufacturing. Furthermore, these grades are highly useful for manufacturing complex spring shapes, requiring a soft steel for forming.
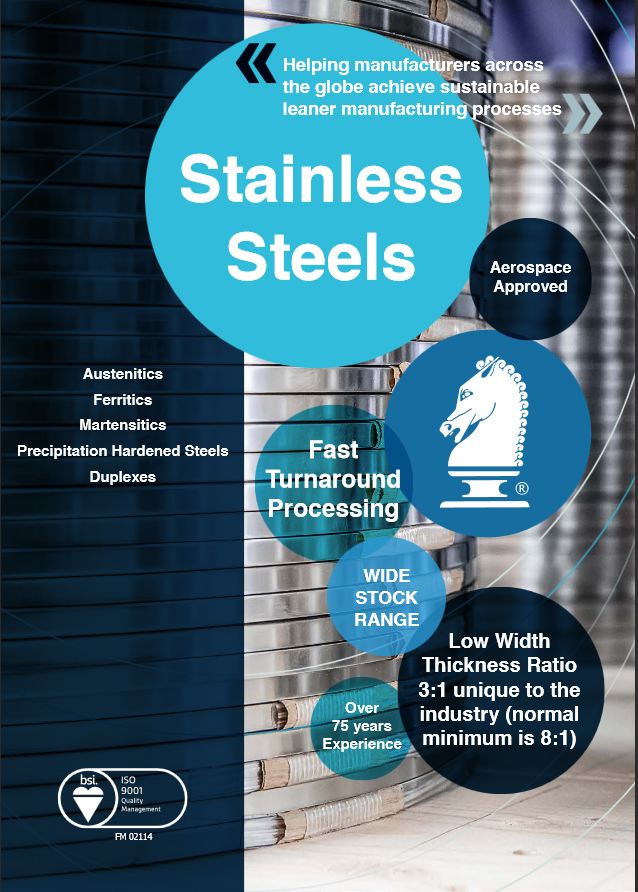
Precipitation Hardened Alloys
Other key alloying elements include Aluminium, Titanium, Niobium and Molybdenum, either in combination or on their own. Consequentially, this alloy grade offers manufacturers many superior properties, combining high work hardening rates and very high strengths, superior fatigue properties, good corrosion resistance. Equally there is minimum distortion when heat treated. In addition to these properties, this group of Stainless Steel Alloys, offer good formability.
There are three further subdivisions of Precipitation Hardened Stainless Steel, low carbon martensitic, semi-austenitic and austenitic. The most common alloy grade 17/4PH falls into the Martensitic category. Another common gradeis 17-7PH, a austenitic-martensitic type alloy, which is ideal for Aerospace applications, Spring manufacturing and Surgical instruments.
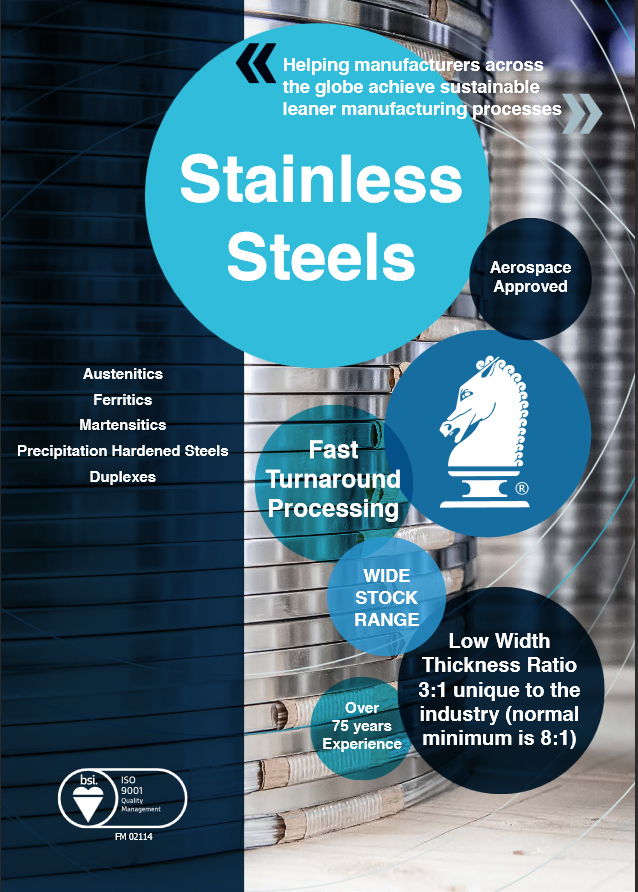
Super Alloys
As a result of their attractive combination of properties, it is common to describe Duplexes as Super Alloys. These Super Alloys can be strengthened by cold work and has lower thermal expansion and higher heat conductivity than Austenitic Steel strip. They also offer a low cost alternative to Austenitic Stainless Steels, owing to their lower Nickel content. Alternatively, Super Duplex has a higher Chromium content than standard Duplex, offering further mechanical and corrosion resistance. Due to superior corrosion resistance lends makes these alloys ideal for more demanding environments including Marine, Petrochemical, and Nuclear Power Generation.
Though in existence since the 1920s, advancements allowing greater control of the Nitrogen element have made Duplexes a more popular choice for modern manufacturing. As the applications for Super Alloys rises, demand increases and incentivises the development and release of additional grades. We work closely with the mills and therefore we are able to offer the latest innovations in material development, ensuring you keep your competitive edge.
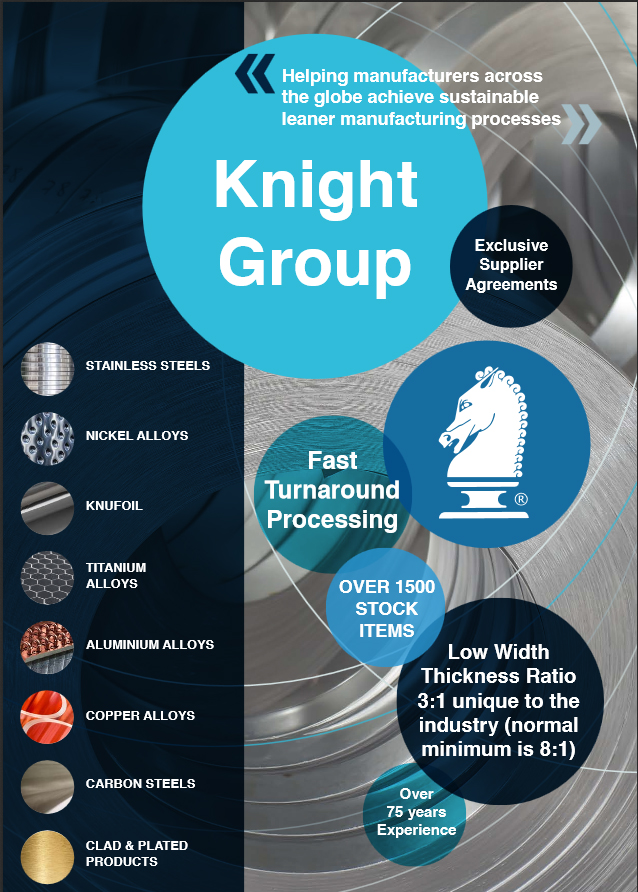
Stainless Steel Tool Wrap
Our Stainless Steel Tool Wrap provides a quick and low cost method of protecting the surface of tools, dies and other parts during the hardening process by preventing decarburization (scaling). Protecting the surface of your tools is simple using KNUFOIL to create envelopes. These Tool Wrap envelopes lock out the air and as a result, eliminate the need for expensive protective atmosphere furnaces. Furthermore, this process only increases hardening time by two or three minutes.
A further major advantage is the option to use a faster quenching medium, − for example, using water rather than oil. This is due to the insulating effect of KNUFOIL in the quenching medium, which is sufficient to reduce the risk of cracking that is normally the result of using of a faster quench. Equally, it eliminates the need for encapsulating or coating the product in a protective material, which might be difficult to remove after hardening. By using our Tool Wrap, manufactures have a low cost alternative to using expensive protective atmosphere furnaces.
We supply KNUFOIL is our standard width of 610 mm. Other widths are available upon request, please contact our sales team for further information. You can purchase KNUFOIL directly from our sister website, KSM Direct. We offer bulk pricing on two or more rolls.
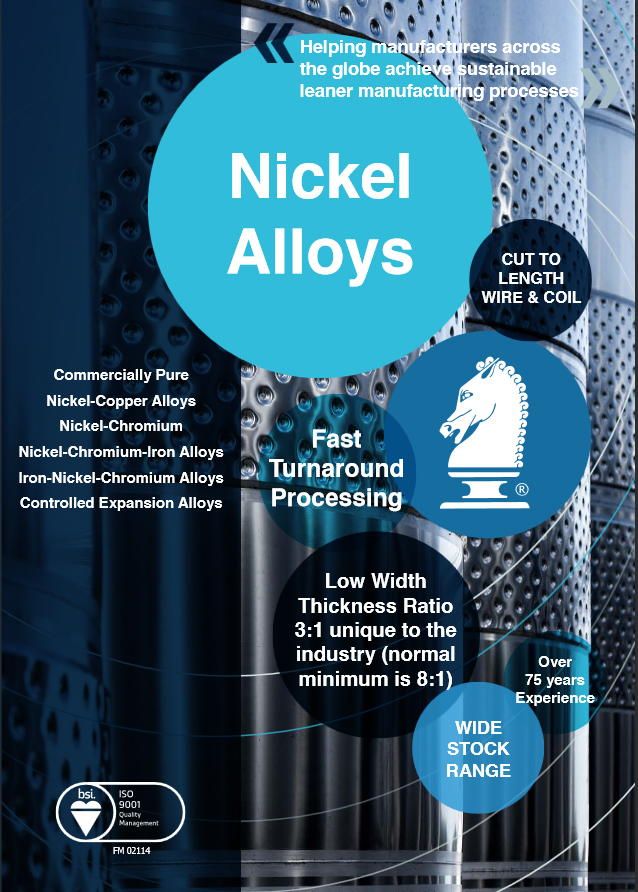
Nickel & Nickel Alloys
There are many commercial applications for Nickel Alloys, with extensive use in Aerospace, Nuclear Plants, Medial, Chemical and Petrochemical industries.
The most commercially popular forms of Nickel Alloys fall into the following categories:
> Commercially Pure Nickels
> Nickel-Copper Alloys
> Nickel-Chromium & Nickel-Chromium-Iron Alloys
> Iron-Nickel-Chromium Alloys (800 Series)
> Controlled Expansion Alloys
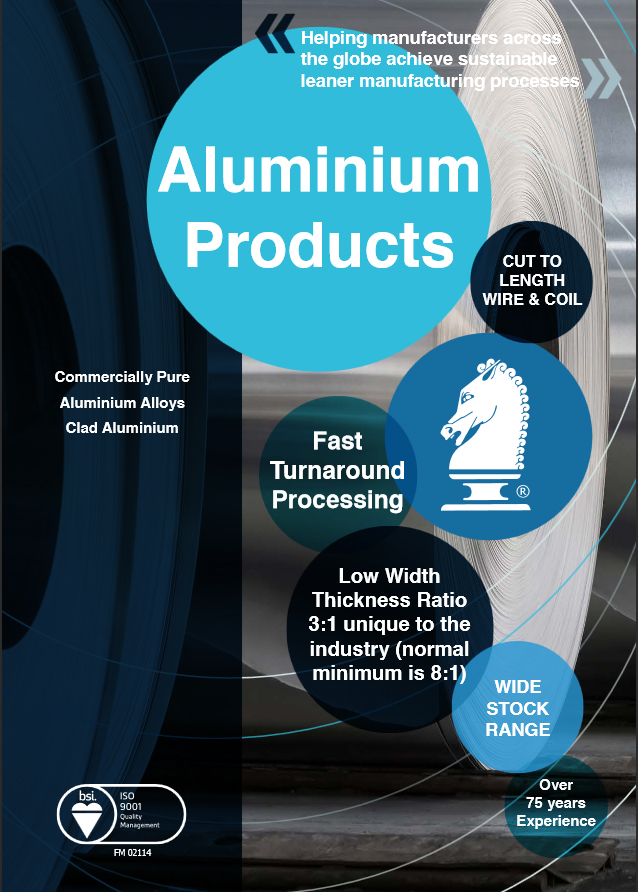
Aluminium
Though commonly found within the Construction industry, the physical properties of Aluminium and its alloys, make it an essential material for Aerospace Automotive and Transport sectors. These Alloys also offer significant environmental advantages with zero toxicity and ease of recycling without changing its integral properties. The low cost in conjunction with material availability, beneficial physical properties and ease of formability makes it an ideal choice for large volume production. This has made it a popular choice for beverage packaging, but also has wider use within Food and beverage production.
Aluminium is a lightweight, soft ductile metal with nonmagnetic and corrosion resistant properties. Furthermore, it has approximately a third of the density of steel, but this does not impact its strength. It is also more durable at lower temperatures and unlike Steels will not become brittle, but actually becomes stronger at low temperatures. However, when heated above 100°C, this can affect strength.
Alloys are available in a range of surface finishes, ranging from dull to reflective, making these alloys ideal for decorative features and metal products.

Titanium & Titanium Alloys
> Alpha
> Alpha/Beta
> Beta alloys
Pure Titanium has an alpha structure. However, this transforms to a beta form as a result of being heated above 882°C. The addition of alloying elements influences this transformation. Many alloys have been developed where the beta phase is retained at room temperature. This provides a material containing alpha and beta phases. The relative amounts of these phases give rise to variations in properties such as ductility, weldability and ease of forming.
Owing to its property strengths, Titanium has becoming a vital material across a number of industry sectors. Chemical process industries rely on outstanding corrosion resistance, consequently making Commercially Pure Titanium strip an ideal material choice. Other demanding applications within Aerospace, such as static and rotating gas turbine engine components, also require a combination of corrosion resistance, low weight and high strength. The ability to withstand some of the most critical and highly stressed conditions has made it ideal for use in civilian and military airframe parts.
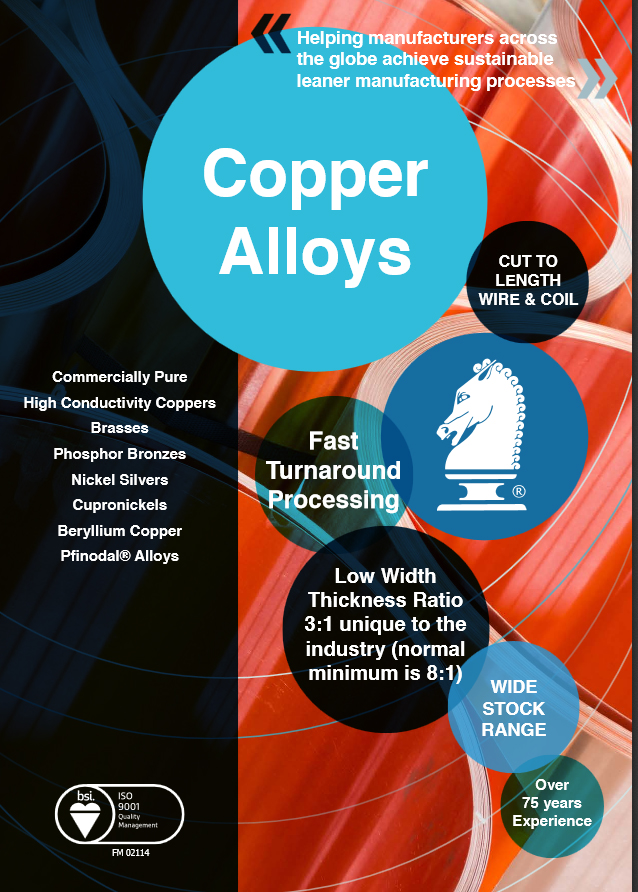
Copper & Copper Alloys
> Commercially Pure High Conductivity Coppers
> Brasses
> Phosphor Bronzes
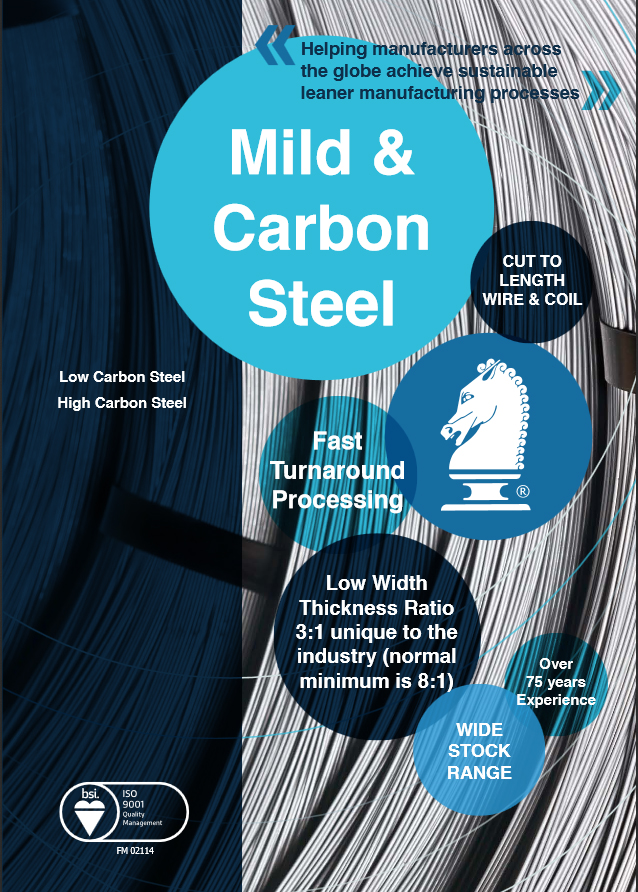
Mild & Carbon Steel
The Knight Group range of Carbon Steels can be broadly split into two categories:
LOW CARBON MILD STEELS
HIGH CARBON SPRING STEELS
Spring Steels are available in the annealed condition for hardening after forming, or in the hardened and tempered condition.
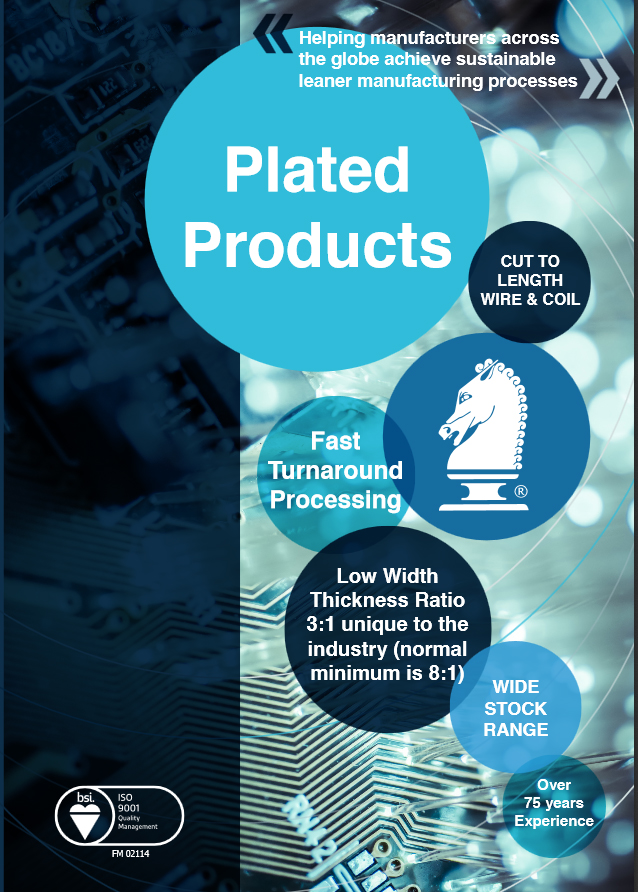
Plated Steel
Plated Strip Electrical Applications
There is a growing use of plated strip steel in electrical applications − driven by increasing metal prices of the traditional non-ferrous materials used by the electrical industry.
Typical applications include…
> CONNECTORS
> SWITCHGEAR
> CIRCUIT BREAKER ARC PLATES
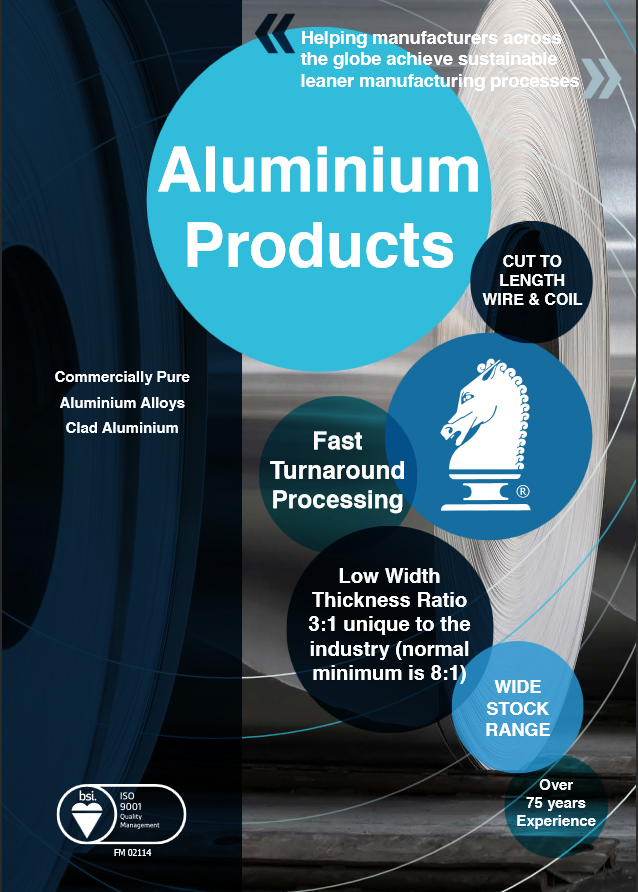
Clad Aluminium
Designers, engineers and manufacturers are increasingly turning to clad metals to provide material solutions, created by demanding environments and applications. The properties of Clad Aluminium lends itself to many such applications, including brazed heat exchangers for the Automotive and Aerospace industries.
In our current era of manufacturing, environmental concerns have become an increasing priority to both designers, manufacturers and end users. Clad Aluminium’s environmental benefits are similar to Pure and Alloyed Aluminium, as it is also easy, quick and cost effective to recycle.
Sourcing the right material for a wide range of products is our specialty. If you would like help in finding the right Clad Metal product for you, get in touch with our Sales Team today.
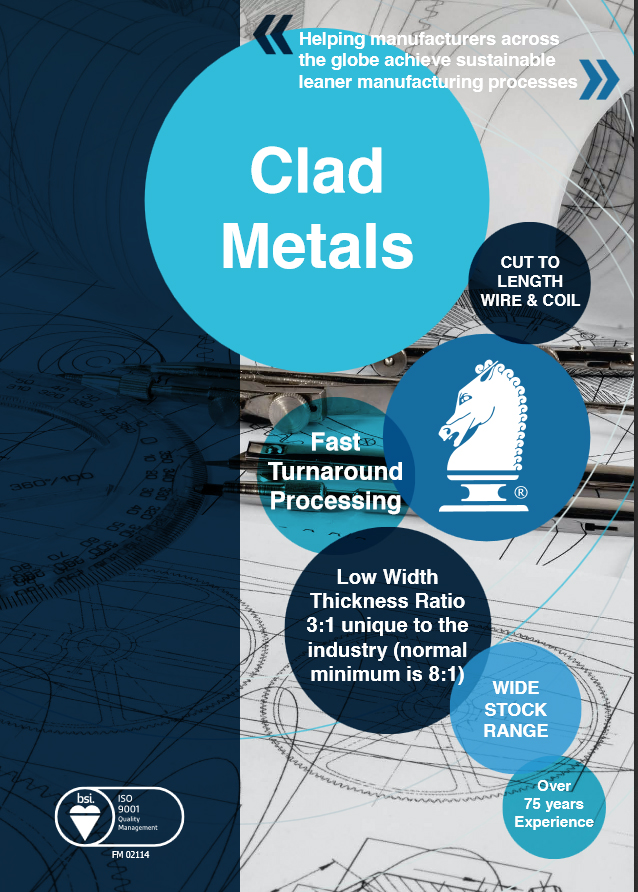
Clad Metals
As a result, Clad Metals offer designers, engineers and manufactures the freedom to create new solutions with targeted properties for even the most unique design challenges. This makes Clad Products an ideal material of choice for demanding and high stress environments. Sectors including: Aerospace, Petrochemical, Oil and Gas, Construction, Telecommunications, Domestic Appliances, Electronics, Medical and Defence, use Clad Metals for this reason.
As Clad Metals consist of a number of layers, there are a numerous combinations possible. In particular, Clad Aluminium, has become a popular choice as an alternative to Copper. In addition to cost savings, it has the added benefit of superior durability yet lighter weight in comparison to Copper, and increased strength compared to Pure Aluminium. However, among the most valuable properties of Clad Aluminium, are its superior heat transfer performance and corrosion resistance. This lends itself to many applications, including brazed heat exchangers for the Automotive and Aerospace industries.
Sourcing the right material for a wide range of products is our specialty. So if you would like help in finding the right product for you, get in touch with our Sales Team today.
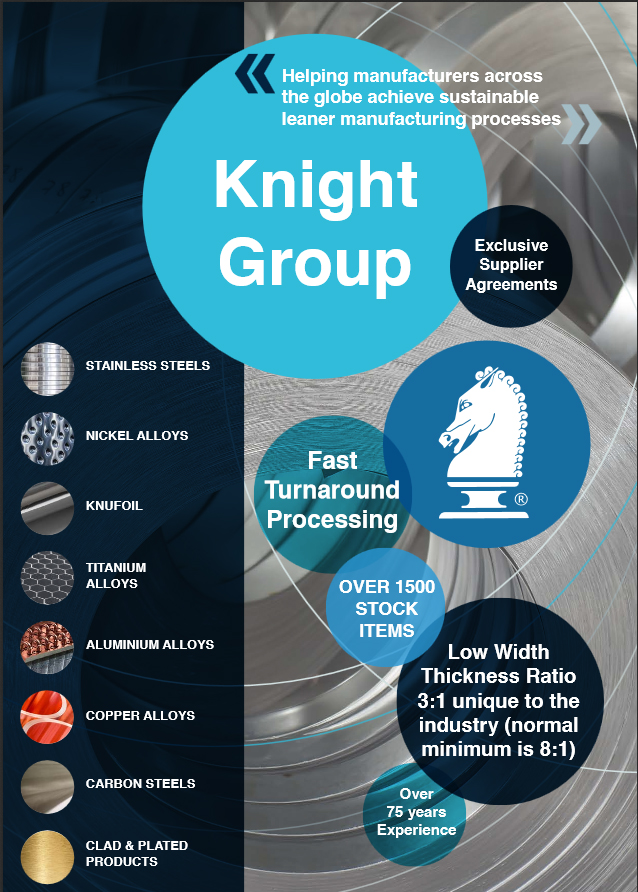
Recoiling
Recoiled metal strip material can be supplied in a wide range of coil size and weight options to facilitate your processing requirements with options that include:
> Pancake coils
> Traverse wound spools
> Open sided oscillate wound coils
> Up to 1000mm wide
> Low weight coils
> Coils on cardboard centres
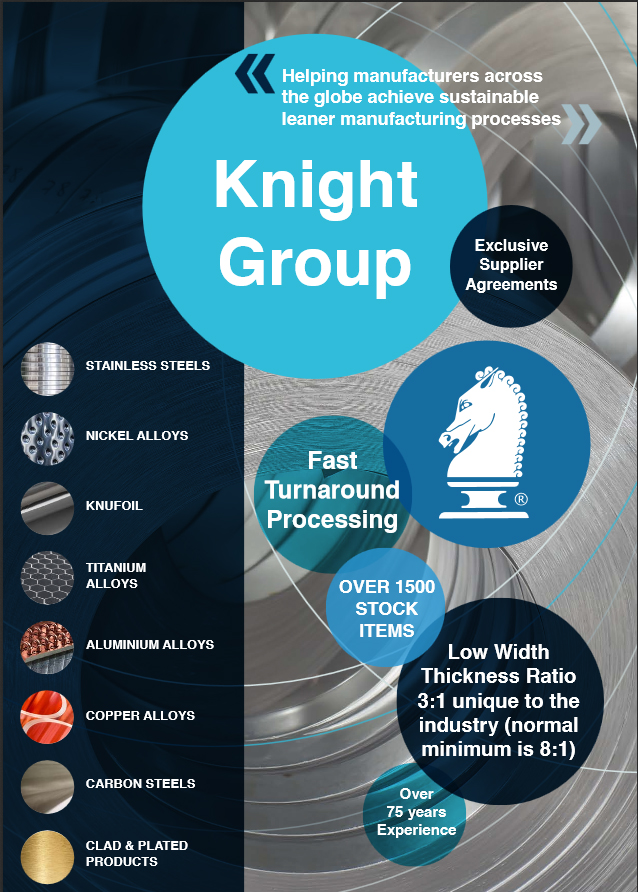
Slitting & Shearing
Our machines are state of the art, with ultrafine tolerances and a substantially superior width to thickness ratio of 3:1 compared to the industry standard of 8:1, capable of processing all material sizes and specifications.
We have a skilled team of experienced machine operators that ensure the efficient and safe running of our production facilities, with all materials handled with the care from arrival to dispatch.
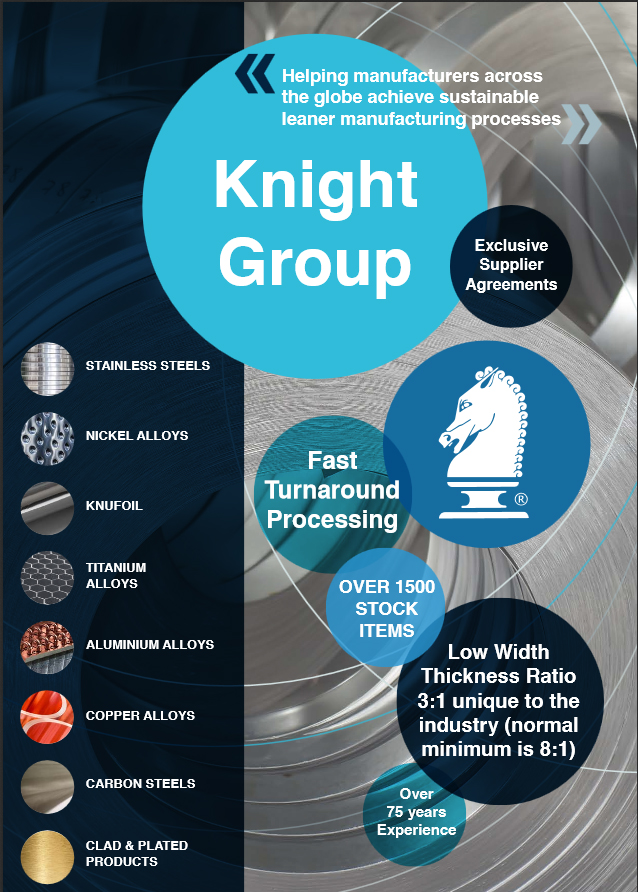
Traverse Winding
Traverse wound coils provide an alternative to single coil “pancake” form of feed supply, capable of holding up to ten times more material. Each traverse wound coil increases productivity and enables longer uninterrupted production runs, by reducing the number of coils needing to re reloaded, machine downtime and coil handling are minimised and storage and scrap can be dramatically reduced. We can offer traverse wound strip on your choice of spools from 20kg to 100kg max.
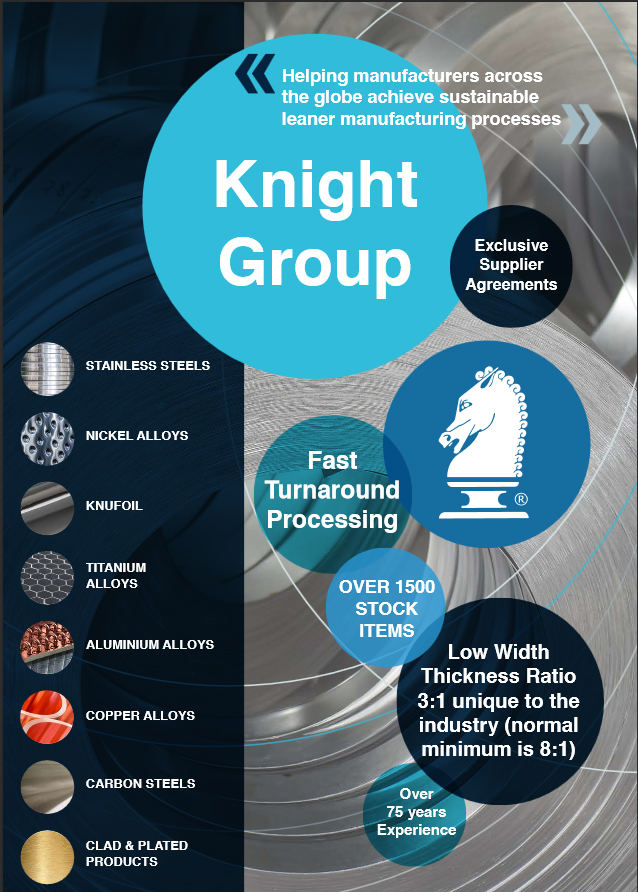
Cut to Length
By offering our customers material cut and packaged to their exact specifications, we help hundreds of our customers to achieve leaner manufacturing processes to maintain a sustainable and successful business. We have 8 cut to length lines, operated by a skilled and experienced team so you can rely on your material being cut quickly and with great accurately. We offer highly competitive rates to make cut to length an attractive cost and time saving decision. All material is quality checked and then carefully packed in bespoke packaging. Your material will then be available for collection from our Saltley site or you can choose a delivery to suit your business needs, with your material arriving machine ready.
Get a quote today and see how much time and money you could save.
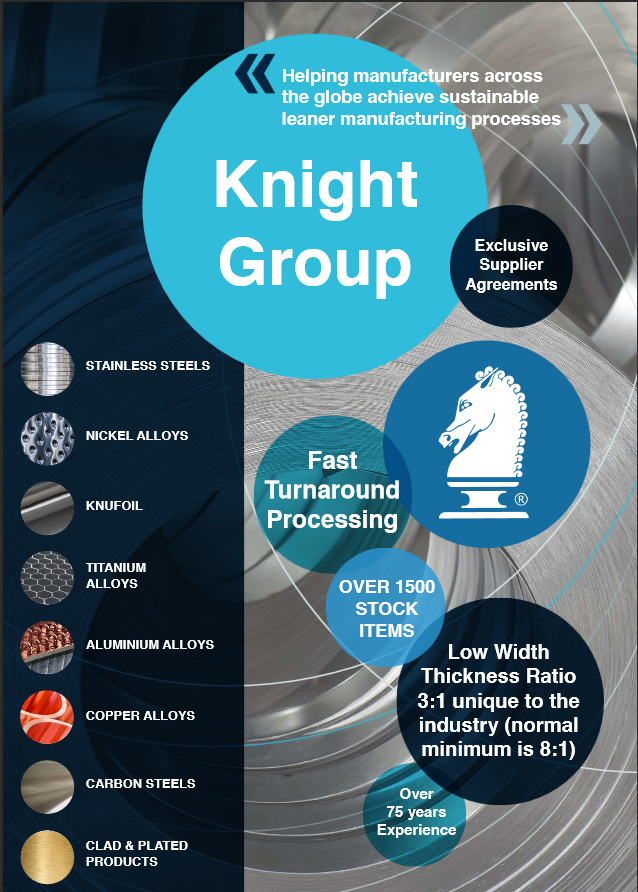
Edge Dressing
The Knight Group offers manufacturers the flexibility to choose the processing that meets your needs and we can supply material edge-dressed to your specifications. Whether you need the commonly requested rounded or square edge shapes or you need a contoured edge shape tailored specifically to you, we offer the Edge Dressing profile you need. We design and use Bespoke Tungsten Carbide Tooling to meet the most exacting Custom Edge Dressing requirements on Precision Strip.
With the heavy investment in our bespoke machinery and a wealth of experience in our team, our machines can offer precision processing in high volumes, with fast turnaround times.
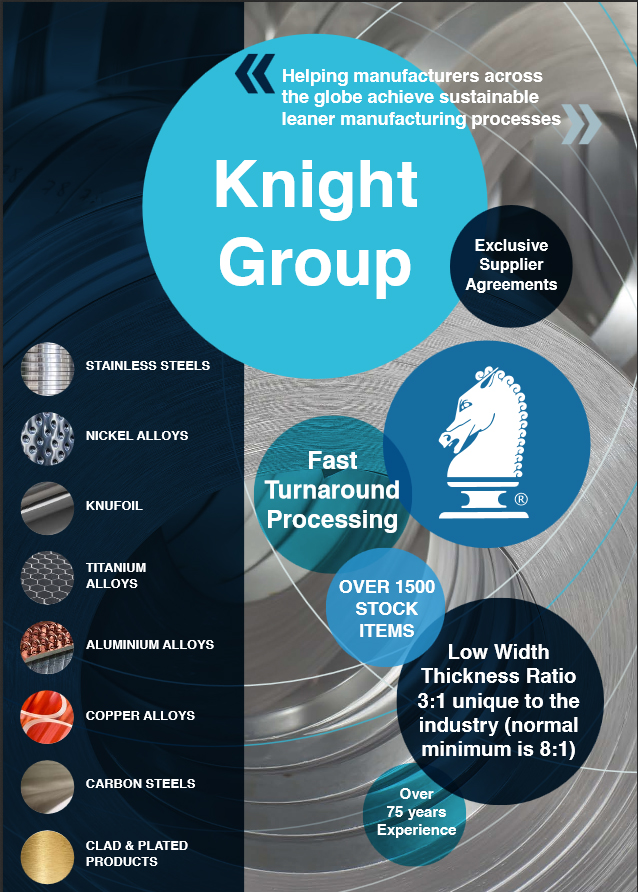
Precision Strip Metal Warehousing & Logistics
Our warehouse racking at our expansive facility in Birmingham, accommodates a range of coil sizes up to 5 tonnes in weight and up to 73” (1855mm) in diameter. Using turret trucks enables us to use the full height of the building and ensures a maximum level of stock can be stored. We use a computerized stock management system to ensure all incoming materials are accurately net weighed and given allocated positions. This is an an invaluable resource to our experienced Strip Metal Sales Team, giving them real-time information on stock levels. We have further facilities in Mechlen, Belgium, so wherever your business is located, we can ensure you are provided with accurate information and responsive customer service.
About us
Knight Strip Metal, also known as Knight Group are well established in the metal industry and as such are the supplier of choice for many global organisations throughout the world. Our success is built up by our core values ensuring that you get the very best from your metal and metal processing supplier. Our mission is to become not only a local manufacturer but also deliver results on a global scale providing you with the highest quality materials and processing services.
> Quality − Our commitment to all our customers it to provide them with the very best service and top quality products giving you the highest standards that you deserve.
> Efficiency − We work alongside our customers, offering the very best service and support, helping reduce production costs without compromising on quality as well as delivering on time.
> Innovation − We strive to provide the very best service to our customers, we embrace all new challenges, creating tailored solutions that exceed expectations.
> Trust − We want our customers to be completely satisfied with our work, we build long lasting relationships due to our focused approach on ethical, responsible and fair business practices.
> Partnership − We work alongside both customers, colleagues and suppliers and value their input on the best practices to achieve goals and maintain a sustainable business.
> Investment − We continue to invest time, effort and money to provide all business partnerships success not only for our customers but also on-going business growth.
In addition to the supply of the raw materials we are also recognised as industry leaders in the processing of strip, coil and wire. These services include;
> Recoiling − supplied in a range of coil sizes and weight options including pancake coils, traverse wound spools, open sided oscillate wound coils, up to 1000mm wide, low weight coils, coils on cardboard centres
> Slitting & Shearing − for ultrafine tolerances and substantially superior width thickness ratios of 3:1
> Traverse Winding − an alternative to single coil pancake coils, increasing productivity and enables longer uninterrupted production runs
> Cut to Length − raw materials cut to exact customer specifications
> Edge Dressing − material edge dressing to your specifications reducing the risks of injury and manufacturing time.
Why choose us your metal and metal processing supplier?
With a dedicated and experienced production team with years of experience in the metal industry, the Knight Group are well equipped to offer a full range of high standard and efficient metal processing services. Whether you require slitting, shearing, traverse winding, material cut to length or edge dressing then we can help. All processing is based on a competitive price and all work carried out is flexible so that you only get the services you require.
We stock Europe's largest and most comprehensive range of precision metal strip and wire, in a variety of different grades including stainless steel, mild steel, nickel and nickel alloys, titanium and titanium alloys, aluminium and aluminium alloys, bronze and copper alloys.
We can work with all requests, whether its large volumes of metal or test materials for prototypes we can provide you with the materials you need for your project without comprising on quality or cost.
The Knight Group has worked with a number businesses including Rolls-Royce, BAE Systems, Airbus UK, Westland Helicopters and HS Marston Aerospace Ltd to name a few.
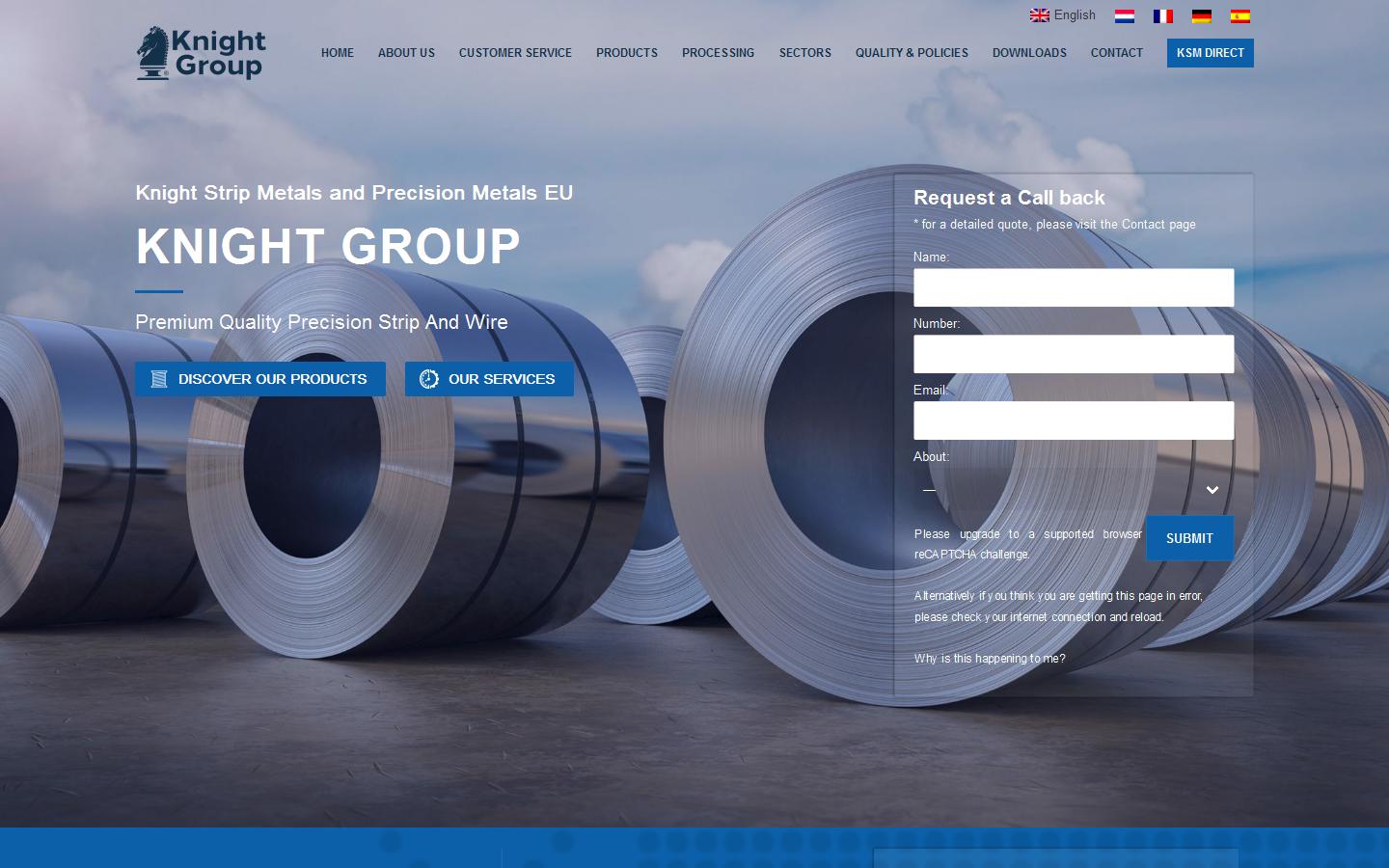
Sponsored Links
Trade Associations
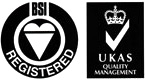
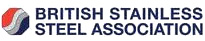