Company details for:
Paramount Precision Engineering Ltd
42 Wellington Crescent,
New Malden,
Surrey,
KT3 3NE,
United Kingdom
Quick Links:
Products / Services
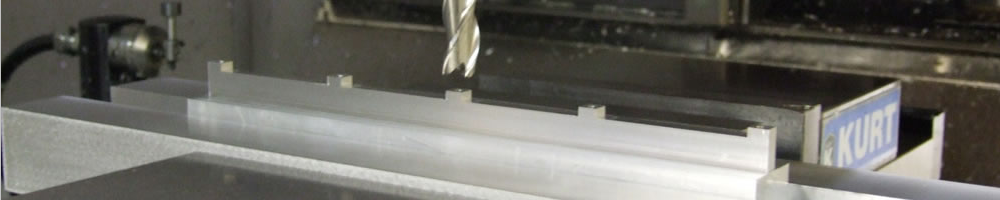
CNC Machining Services
Our capacity includes state of the art modern machinery capable of high precision machining to the highest standards with repeatability and quality assurance through a dedicated inspection room.
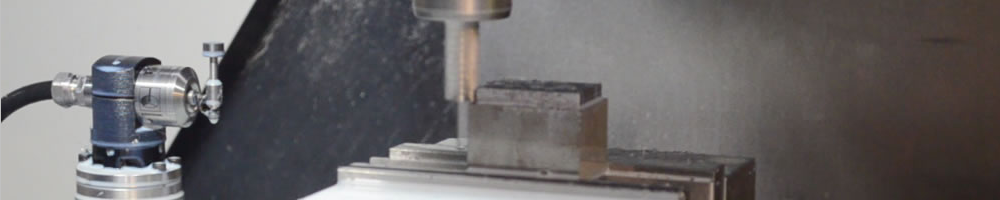
CNC Milling
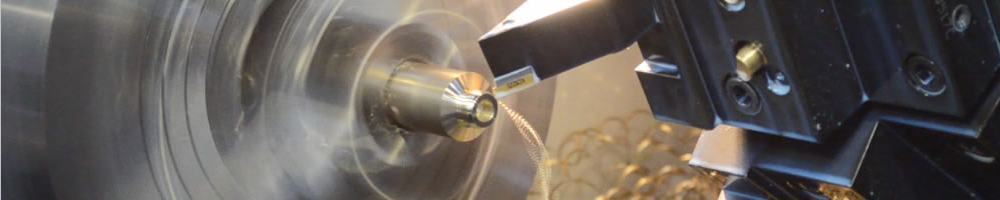
CNC Turning
Our machine is fully networked and capacle of accepting solid models.
Travel
Carriage specifications are:
X axis: 255mm (185+70)
Z axis: 790mm
C axis: 360 degrees
Capacity
General capacity specifications are:
Maximum turning diameter: 370mm
Maximum workpiece length: 765mm
Maximum weight on spindle (chucking work): 220kg
Maximum weight on spindle (shaft work): 370kg
C Axis Turning
Our Doosan Lynx 300m CNC lathe offers a c-axis which allows for mill-turn functionality and single hit machining of complex components that would otherwise require multiple machines.
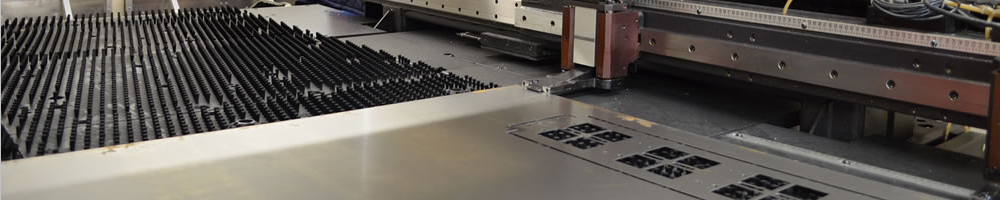
CNC Sheet Metal Punching
We offer sheet metal punching upto 3.2mm and sheet sizes of 2500mm X 1270mm.
High Speed
Our state of the art machine offers a high rate of 480 hits/min or 900 hits/min in marking mode.
Accuracy
Accuracy can be achieved to ±0.1mm without repositioning and ±0.07mm in high accuracy mode.
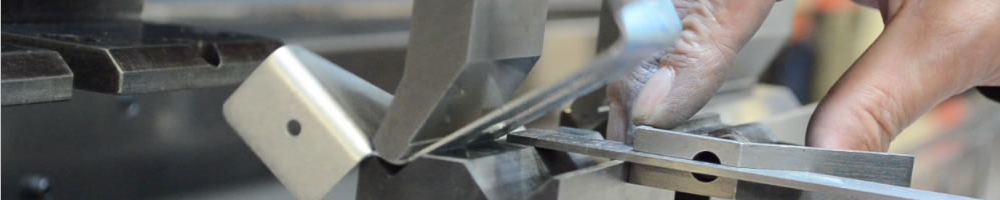
CNC Sheet Metal Forming
Using the latest technology we are able to offer high precision forming with consistent repeatability.
We operate the latest 7 axis 80-ton capacity AMADA promecam brake press with independent control of 'Y-axis' each side of the beam allowing for off centre and taper bending to be accurately executed. This allows us the following cababilities:
Bend Length: 2570 mm
Throat Depth: 420 mm
Open Height: 470 mm
Stroke Length: 200 mm
Ram Repeatability: +/- 0.01 mm
The 7 Axis 80-ton AMADA brake press is also equipped with an automatic angle correction gauge.
We have a large tool library for a wide range of fold types including:
Dutch Folding
Roller V's - for flanges
Deep Box Swan Neck folding blades
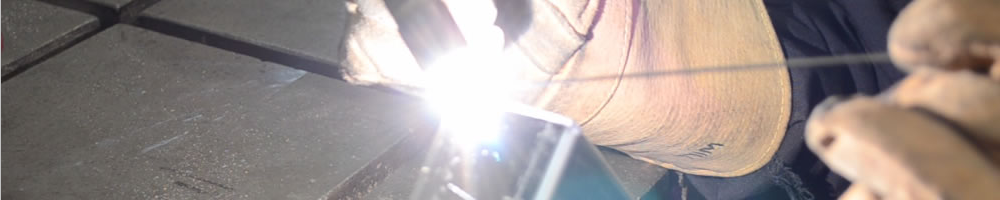
Welding Services
TIG Welding
TIG welding is ideal for both ferrous and non-ferrous materials. We fabricate specialist jigs where required and have a range of fillers to suit requirements. Most weld joins can be undertaken including fillet & butt welded joints as well as single & double V joints. Our welders have years of experience and can work most other mehtods as required. Our welders are particularly skilled with thin section welding.
Spot Welding
Our 150kVA Meritus Autoforge Spot Welders allow us to offer aluminium resistance spot welding of sheetmetal upto 3mm thick. Spot welding is ideal for large sheetmetal enclosures and boxes as well as other more intricate work.
Oxy-Acetylene Welding
For larger fabrications we are equipped with Oxy-Acetylene welding facilities suitable for mild steel and other steel alloys.
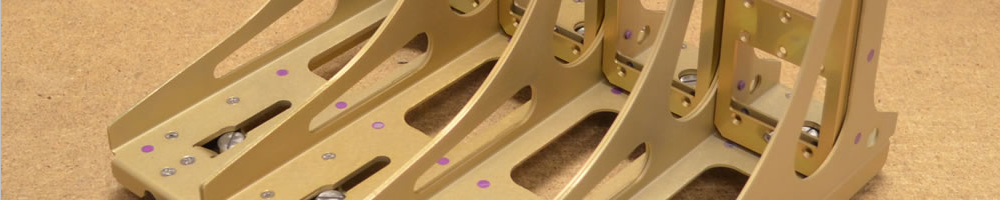
Precision Fabrication
Paramount Precision Engineering undertake precision fabrication to customer specification.
Our fabrication services incorporate in-house machining, sheetmetal punching & forming and assembly as well as sub-contracted services such as powder coating and the sourcing of standard components including hinges, clasps and general fixtures & fittings.
Skilled Engineers
We have the capacity and skill sets to undertake a wide range of projects to the highest specifications and regularly carry out work for the scientific and process engineering sectors. The item above is a parts washer for degreasing mechanical components. The fabrication below is a tubular chassis with nylon mounting features, a mechanical mechanism, mounting pins and painted decals.
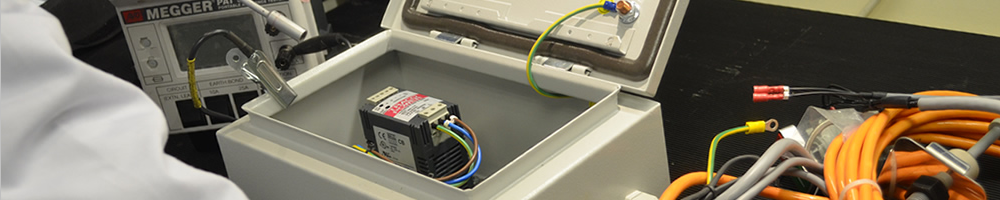
Assembly
Electrical Components
We offer full assembly of electrical components with wiring and testing of basic circuits. Full machine testing can be carried out to ensure product integrity.
Bench Top Assembly
We offer full assembly service including hydraulic and pneumatic components
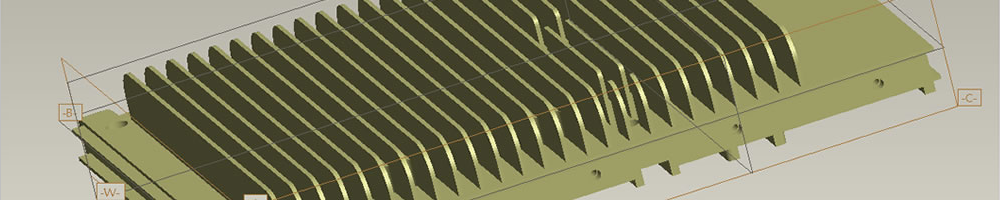
CAD Design
Our primary CAD facilities includes Parametric technology pro/engineer 3D solid modelling, Edgecam solid CAD/CAM and Sheetworks 3D solid model & unfold CAD. Other systems include CGTECH vericut NC simulation and DXF & Iges translators. We also offer Electronic Data Transfer.
Solid Modeling
The principle strength of our CAD design department is our ability to handle Solid Models which allows for drawing free manufacture.
Design Collaboration
We aim to work directly with our customers engineers in order to provide the most cost effective solution to their manufacturing requirements.
Data FTP
For FTP details please ask. We offer dedicated client FTP folders for efficient data sharing and project collaboration.
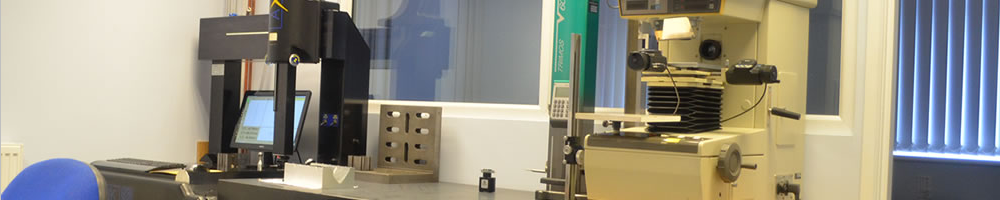
Inspection Services
Inspection is carried out using a state of the art Axiom 3 Axis Co-Ordinate Measuring Machine equipped with a kinematic MIP Renishaw Probe with repeatibilty of 1.5µm and integrated through the Aberlink 3D software suite.
We also have a full suite of Mechanical Inspection equipment including a Mitutoyo Heightmatic 600 height gauge, calibrated granite tables, veniers, comparators, micrometers and slip gauges.
Inspection Reports
Inspection reports can be in the form of fully dimensioned graphical representations as created on the screen, or tabulated reports in various formats that can show nominals, tolerances, errors, pass/fails, geometric tolerances etc. These reports can also be outputted as an Excel spreadsheet. Full offline programming is also available.

Plant List
The list is correct as of 03/05/13.
Design & Engineering
CNC Milling
CNC Turning
Sheet Metal
Fabrication & Welding
Fitting
Inspection
Manufacturing System
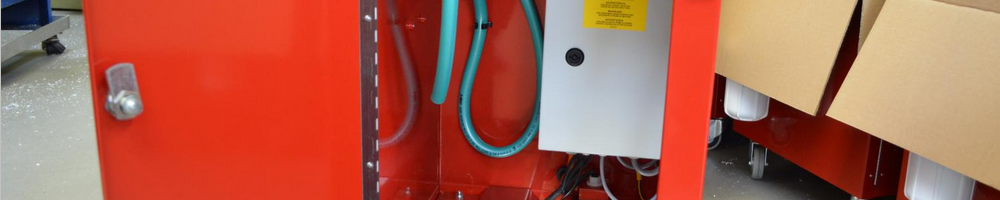
Case Studies - Kleen Cut 2
We have been manufacturing this item for several years in regular batches of 200 off which are then distributed throughout Europe.
The design was made in liaison with the customer by assessing and modernising the original model, the Kleen Cut 1. All drawings were produced by Paramount.
Paramount project managed the whole assembly from manufacturing in house components and purchasing both mechanical and electrical assembled items which were then assembled in house. Paramount then carried out PAT testing, inspection and certification as required.
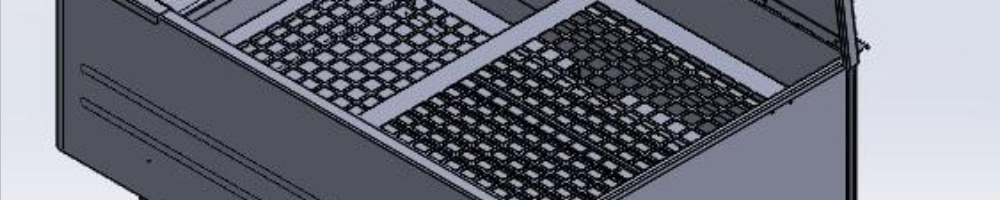
Case Studies - Resin Cleaner
Designed in liaison with the end customer, we produced a prototype for approval, integrated design changes and moved onto a preproduction run of 30. Design was carried out using solid works with all drawing and models being produced by Paramount. The system is a solvent tank for cleaning brushes manually by dipping and immersing into the 20 litre capacity tank with an optional centrifuge fitting for pneumatic powered spinning of brushes to remove any residual solvent.
All components were made from stainless steel 304 because of the caustic nature of the process with the bulk of sheet metal being 1.5mm thick.
The work was carried out on the CNC punch followed by CNC folding operations and tig welding where required. As with many projects of this nature there was a lot of assembly of fixtures and fittings such as hinges, pneumatics, lid stays, foot pedals, and labelling etc. The internal mesh tray was fully punched in-house and folded accordingly. The centrifuge housing was sheet rolled and seam welded.
Each tank was leak tested by filling with water and all seam welds were treated with a stain removal process to remove weld discoloration.
The design to preproduction stage took around 6 months as tanks were sent out for approval and testing/sampling in the industry.
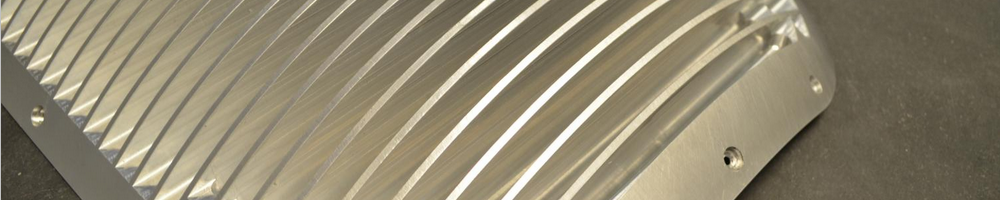
Case Studies - Heat Sink Cover
Job was for an existing blue chip company to which Paramount are a core supplier with a long and well established relationship. The job was competitively quoted for and won based on price and historic performance in quality and delivery. The job was initially being done by a company using a 5 axis machine but Paramount offered a manufacturing solution based on a 3 axis vertical mill with the added assurance of a higher quality of service. This was part of a larger package of work worth in excess of £60k.
Electronic model files were supplied in Step format accessed through a customer FTP portal which is a common project management requirement with many customers. Below can be seen Pro Engineer and EdgeCam screen shots of the programming operation.
The job lent itself to be manufactured on a 5 axis machine, however, due to the capabilities of the Paramounts in-house CAM system we were able to produce the component on a 3 axis machine with an auxiliary fourth axis. This allowed for the machining of the complex curved surfaces using a bullnose cutter to achieve the correct curved surface in a single setup. The outside shape was machined first and then the slots cut.
The component was inspected on the CMM using software to give a direct dimensional comparison to the original customer supplied model. With this particular customer we have a process approval for drawing free manufacture which stipulates that machining tolerances must be within +/-0.1mm all around unless otherwise stated on the drawing.
The component was then alocromed and stove enamelled to a Def-Stan using a local approved contractor, a process that was project managed by Paramount for quality assurance.
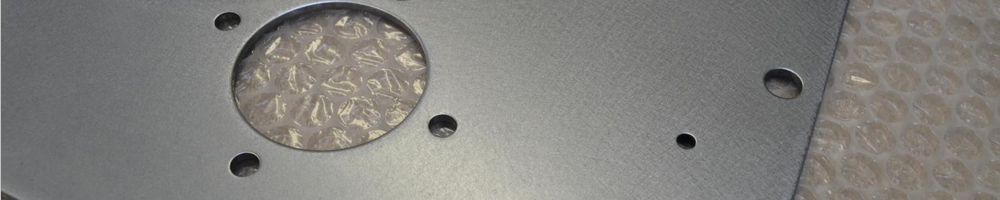
Case Studies - Base Plate
The component is about 450mm square with a large central hole that has been produced with a special segment punch on the Amada CNC AE255NT turret punch press.
Component is then vibro finished to remove burrs, degreased and then shipped to the customer.
Customer is a large manufacturing company involved with the fabrication of large scale air flow systems and this component represents a single item of multiple standard parts. Customer is a long term customer that has been using Paramount for components such as this for over 10 years.
About us
We maintain strong collaborations with the aerospace and defence industries while also providing an extensive array of subcontracting precision services. The business was acquired by the current owner, Chris Bowman, in 1984, and under his guidance, there has been a continuous commitment to reinvestment in the company's growth and development.
One of our notable strengths lies in our ability to provide a comprehensive manufacturing service, thanks to our expertise in fine limit CNC sheet metal work and CNC machining. We are proficient in handling a range of project requirements, including 3D Solid Modelling for larger blue-chip clients, while also being well-versed in accommodating 2D CAD files and traditional paper drawings
Our Services Include:
CNC Milling
We utilise a total of five advanced, fully-networked Doosan DNM vertical machining centres, complemented by two CNC Bridgeport Series II mills and a conventional Ajax universal mill.
CNC Turning
We provide multi-axis turning with powered tooling based on solid models, electronic files, or traditional paper drawings.
CNC Sheet Metal Work
We provide CNC punching and forming services based on solid models, electronic files, or traditional paper drawings.
CNC Forming
CNC forming is executed using an advanced 7-axis, 80-ton Amada press brake with a length of 2570mm.
CNC Punching
We run a cutting-edge Amada turret punch press with a size of 1270mm x 2500mm, capable of processing 3.2mm thick sheets and achieving a punch rate of 480 hits per minute.
Sheet Metal Fabrication
Our resources encompass TIG, MIG, and 150KAV spot welding capabilities, alongside oxy-acetylene welding capacity, all supported by a specialised 1500mm x 750mm welding table with comprehensive extraction. Additionally, we have a dedicated 2400mm x 1200mm fabrication table in our facilities.
CAD Design
Solidworks
Assembly
We have a spacious assembly zone equipped with an extensive array of bench-top resources and a production line layout suitable for mechanical fixture assembly, as well as the assembly of electrical and electronic components. Our assembly services extend to tasks like labelling, numbering, and overseeing outsourced services like metal finishing.
Our excellent track record in delivering top-notch products, coupled with our ISO 9001 quality certification maintained since 1998, has solidified our standing in the Defence industry as a prominent subcontractor. We've consistently invested in upgrading our machinery, IT infrastructure, and staff development, allowing us to uphold our reputation and provide a superior level of service.
We maintain positive and enduring connections with all of our customers, having nurtured longstanding relationships with most of them. We make it a point to know our clients on a personal level, ensuring a robust and cordial customer service interaction.
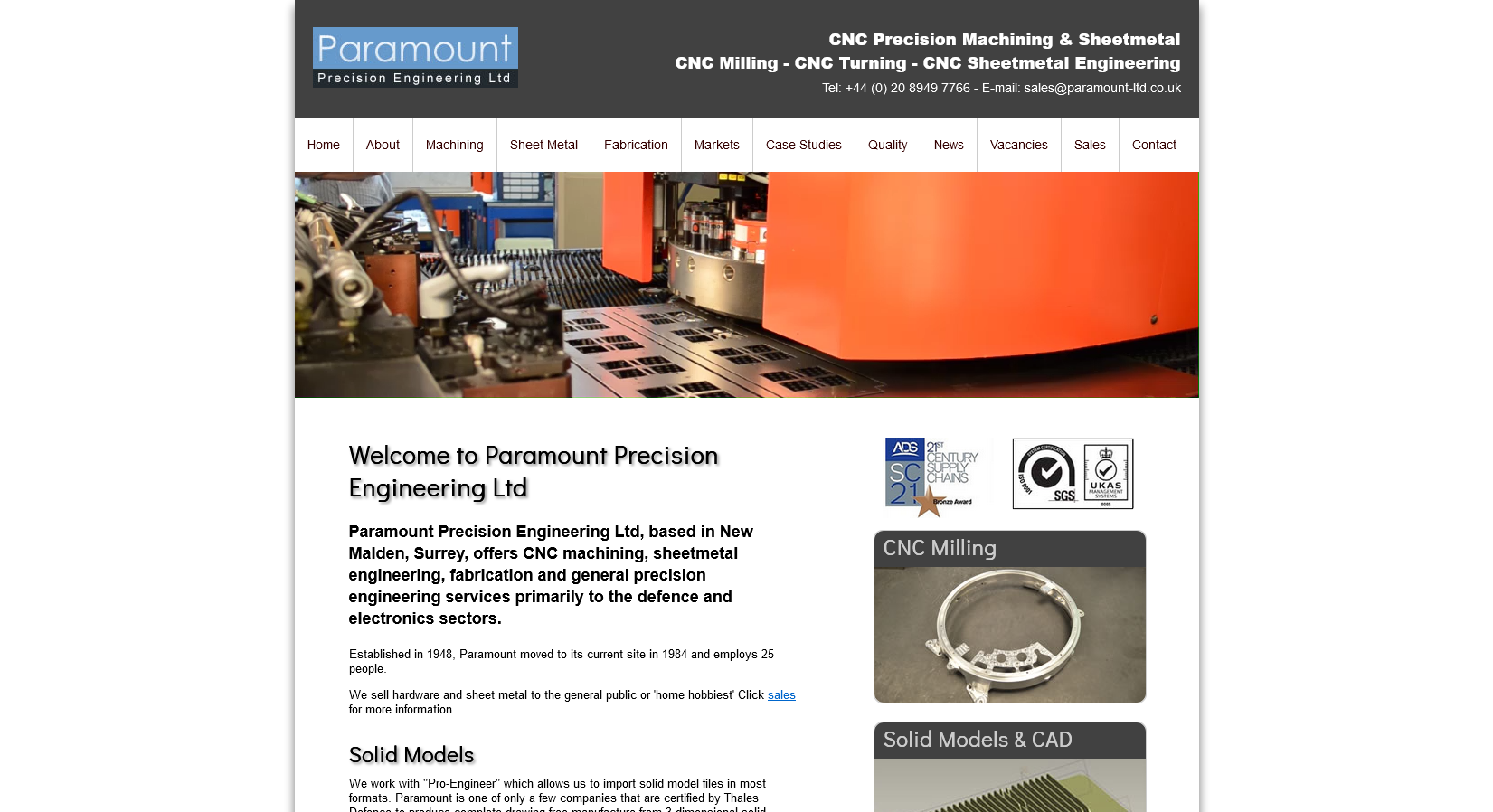