Company details for:
TriVista Engineering Ltd
Unit 53 Newhaven,
Enterprise Centre,
Denton Island,
Newhaven,
East Sussex,
BN9 9BA,
United Kingdom
Quick Links:
Products / Services

Design & Analysis
Client benefits include the following:
> Rapid product development and design validation before more costly physical testing
> Reduced prototype and test requirements
> Comprehensive product details not limited by test instrumentation
> Improved or optimised performance
> Reduced cost
> Competitive edge
> Improved reliability and durability
> Product innovation and patentability
> Additional engineering resource

Computational Fluid Dynamics (CFD)
CFD simulation of complex flow systems provides tremendous value by significantly increasing both the level of information available and also understanding of flow phenomena to companies either developing flow based products or tackling an existing fluid dynamics problem.

CFD Internal Flows
CFD analysis provides comprehensive flow data therefore giving a significant advantage when it comes to quantifying performance or optimising a new design. Projects performed by TriVista cover a wide range of aerodynamic and hydrodynamic applications but typically have objectives such as:
> Quantifying or improving the pressure loss for a new complex geometry or system.
> Evaluation of flow or temperature distributions and improving uniformity.
> Visualisation of flow features for improved understanding of system flow phenomena.
> Quantifying product performance.
> Calculating heat transfer rates or temperature fields in heating or cooling flows.
> Evaluating and adjusting induced fluid dynamic forces (drag, lift and pitching moments).
> Identifying poor flow regions (e.g. separation) causing loss and reducing the effects.
> Minimising flow instabilities to reduce noise and vibration.
> Maximising flow rate or air change rates.

CFD External Flows
Full-scale CFD simulations can be performed over complex geometries generating comprehensive data for evaluating flow features and performance parameters. This provides significant advantages when it comes to validating or optimising designs. External flow projects performed by TriVista cover a wide range of aerodynamic or hydrodynamic applications but typically have objectives such as:
> Quantifying flow induced loading forces and moments under worst case aerodynamic loading for structural integrity evaluations. This can also be fully coupled with FE analysis to evaluate structural behaviour under load (FSI analysis).
> Visualisation of surface flow features for improved understanding.
> Prediction of emission dispersion and advising on problematic pollutant concentration locations.
> Vehicle aerodynamics in reducing drag.
> Evaluating wind induced fluid dynamic forces (drag, lift and pitching moments).
> Calculating heat transfer rates or temperature fields.
> Identifying poor flow regions (e.g. separation) causing loss and reducing the effects.
> Open channel or drainage system flows.
> Airborne particle deposition studies.

CFD Conjugate Heat Transfer Analysis
The CHT approach has an advantage over FE thermal analyses in that wall heat transfer coefficients and their local variations on surfaces are directly calculated within the model rather than based on simplified empirical calculations. The CHT approach therefore has benefits for those applications where heat transfer is either non-uniform or difficult to calculate empirically.
The heat transfer projects performed by TriVista have covered a wide range of aerodynamic and hydrodynamic industrial applications but projects typically had objectives such as:
> Quantifying or improving the temperature distributions.
> Calculation of wall heat flux rates or heat transfer coefficients.
> Visualisation of heat transfer features for improved understanding of system flow phenomena.
> Identification of localised ‘hot spots’ or heat sinks in checking against specified requirements.
> Evaluating variation in temperature peaks for different operating conditions/ failure modes.
> Assessing insulation or heat shield effectiveness and optimising of material selections.
> Coupling CHT with FE analysis to evaluate thermally induced stresses, expansion or fatigue.

CFD Transient & Moving Mesh Analysis
> Examining time varying component concentrations over an industrial process cycle to either ensure concentrations remain within criteria or confirm contaminant removal times.
> Quantifying the performance of products with moving or variable geometry (e.g. positive displacement devices, products with stationary and rotating parts). For these analyses, a moving numerical mesh can also be required in the CFD model.
> Visualisation of transient flow features for improved understanding. Animations can be readily generated from transient solutions to assist with greater understanding.
> Evaluating temperature distribution variation and ‘hot spot’ peak temperatures in systems with time varying thermal loading conditions. For example, heaters operating in failure modes.
> Quantifying pressure loss and flow distributions in systems with operational time varying flow. For example, in medical equipment patient respiration simulations.
> Prediction of the oscillating mechanical loading on structures owing to flow induced vibrations or transient pressure fluctuations e.g. vortex shedding. The CFD simulations can also be fully coupled with an FE solver to evaluate the structural integrity and behaviour under transient load (FSI analysis) e.g. sloshing in a tank.

CFD Particle or Droplet Tracking
> Optimisation of nozzle spray design parameters for improved uniformity of droplet distribution.
> Investigation of the various size particle trajectories and identification of high deposition areas.
> Visualisation of droplet and particle flow paths for improved understanding of flow phenomena.
> Investigation of device or system contaminant removal performance.
> Erosion analysis based on particle to surface impacts.
> Assessment of primary and secondary break up in droplet sprays.
> Evaluation of particle concentrations and ‘flow through’ times.
> Particle motion evaluated under both hydrodynamic and electromagnetic forces.
> Verify effectiveness of hot gas flow cooling from fluid jets spraying droplets with phase change.

CFD Free Surface Flows
TriVista has performed various free surface flow analyses for clients across a range of industrial applications and these projects have typically had aims such as:
> Calculating flow rate distribution and drainage efficiency of open channel flow systems.
> Free surface tank analyses to evaluate sloshing. This can be coupled with FE analysis (FSI) for assessment of structural integrity or structure behaviour under sloshing loads.
> Quantifying product performance e.g. separator vessels.
> Tank free surface models with rotating impellers for mixing effectiveness and velocity distribution evaluation.
> Vessel filling and expulsion analyses.

CFD Combustion & Reacting Flows
Computational Fluid Dynamics (CFD) can be used to simulate flows in which combustion reactions occur. Combustion analyses are amongst the most demanding of CFD applications with: multiple chemical species, multiphase flow and particle tracking (depending on fuel type), chemical reactions, turbulent reacting flows, combustion models and the large corresponding complex release of heat.
A wide range of industrial analysis applications exist such as: combustors, engines, furnaces, burners and heaters. Combustion models can be defined with both single and multiple reaction steps during the combustion process. Typical objectives of these project analyses have been:
> Prediction of performance and optimisation.
> Calculation of the temperature fields and heat transfer rates (convection and radiation) resulting from combustion and design adjustments to improve uniformity.
> Visualisation of the ‘flame zone’ and predicted corresponding flow phenomena.
> Quantification of the resultant downstream pressure loss.
> Evaluation of mixed species distributions, composition and properties of the burnt mixture.

CFD Rotating Systems & Turbo Machines
For rotating machines, CFD offers significant advantages by providing:
> A quick route to comprehensive flow data, flow visualisation and performance predictions.
> Validation of designs before expensive testing and therefore reduced prototyping.
> Performance prediction over a range of operating conditions.

FEA & CFD Fluid Structure Internation (FSI)
Multi-physics analyses enable reality to be more accurately predicted and are essential for products where either their operation involves the coupling of physics or where their physical testing maybe complex and expensive. FSI simulations enable the full interaction between deformable bodies and their adjacent flows to be solved. The resultant structural stresses or deformation of a body under a changing flow induced loading can be readily quantified therefore providing an effective tool to avoid harmful resonances or evaluate structural fatigue life under a cyclic fluid induced loading (e.g. vortex shedding).
Likewise for the CFD simulations, the deformation of a body under flow induced loading and the subsequent modification of the flow field under this loading can be computed iteratively for more accurate calculation of the relevant fluid mechanics.
FSI has a range of applications especially on those structures subject to high or cyclic fluid loading (e.g. localised vortex shedding or waves) and include products as follows: aerofoils, building and industrial structures, valves, sloshing in tanks, aero-elastic instabilities such as flutter and compressor rotor-stator interaction in compressors.

FEA & CFD Advanced Thermal Stress Analysis
The accuracy of a structure stress or deformation analysis results is directly dependent on how representative applied boundary conditions are of reality. The Multi-physics thermal stress analysis approach has an advantage over standardFE thermal stress analyses in that wall heat transfer coefficients and their local variations over surfaces are directly calculated by the coupled CFD solver rather than based on empirical calculations and results therefore reflect reality more accurately.
This multi-physics approach has benefits for those applications where heat transfer is either non-uniform or difficult to calculate empirically where the product geometry is complex. Static or transient thermal cyclic stressing from flows can also be analysed to evaluate thermal fatigue where the changing thermal boundary conditions are calculated using CFD and are exported to FEA for the thermal stress/ fatigue analysis.

Finite Element Analysis (FEA)
Typical applications of the FE method include:
> Structural (stress, strain, deformation, fatigue)
> Thermal (conduction, convection and radiation)
> Dynamic (modal, harmonic, transient dynamic, rotordynamic)

FEA Static Stress Analysis
Structural loads are typically one, or a combination, of the following:
> External forces such as clamping force in subsea connectors.
> Surface loads, e.g. pressure loading in pressure vessels
> Body forces (gravity, acceleration such as centrifugal force in rotating machines)
The structural response to more complex loads, for instance those arising from thermal analysis, can also be simulated using the multi-physics approach.

FEA Thermal Analysis
> Temperature distributions.
> Heat flux paths − important information in evaluating insulations.
> As a boundary condition for the analysis of thermal stress.
Thermal analyses provide very useful information in the following applications:
> Chemical plants
> Burners and combustors.
> Heat exchangers.
> Undersea insulation systems.
Thermal analyses have become increasingly important as designers push for higher performance machines. This means that a good understanding of temperature distribution and thermal loads can often be vital. An incorrect constraint in a system working under elevated temperature can lead to unexpected high thermal stress which may lead to failure.
The accuracy of thermal analyses is highly dependent on correct boundary conditions being defined. Engineers in TriVista Engineering have experience in calculating thermal boundary condition using classical 1D calculation or alternately using CFD to find out more accurate boundary conditions.
Thermal analysis can be performed using FEA or CFD. FEA method is often preferred when evaluating thermal stress is the main purpose of the analysis or the boundary conditions are well defined. CFD is a better method in estimating flow boundary conditions (heat transfer coefficient and fluid temperature) when the flow or structure geometry is complex.Fluid-Structure Interaction (FSI) can be used for flow simulation first to give accurate thermal boundary condition then followed with stress analysis. FSI will be more demanding on computing resources.

FEA Dynamic Analysis
As experienced development engineers our contribution to a dynamic evaluation rarely stops at the analysis output.
We routinely work alongside clients to find design solutions that are realistic and offer genuine commercial benefits:
Vibration testing is expensive. Carry out dynamics analysis at design stage can avoid or reduce of the requirement and the cost for rig testing.
Failure under dynamic loading can be dramatic and damaging. To evaluate the structure at design stage can avoid expensive mistakes in real use of the product.

FEA Assemblies & Coupled Fields
The FE models of components are generally smaller and can have quick feedback from analysis. However, it can be tricky in determining the boundary conditions of a component if its connections to the adjacent components are complicated.
Assembly FE models are generally larger but they enable components to be analysed as part of the system in which they are intended to function. This has a number of benefits such as:
> More realistic representation of a real machine.
> The Component interaction can be explored.
> Improved accuracy relative to individual component analysis.

Rotating Systems
> Rotordynamics
> Bearings, seals and lubrication
> Turbomachinery
High speed rotation (of the order of 100,000 rpm) is particularly well served. This includes direct-drive systems, incorporating high speed electrical machines, as well as geared systems. Experience has been gained in the development of a range of devices, including:
> Turbochargers
> Motor-assisted turbochargers
> Compressors, turbines, pumps and fans
> Turbo-alternators
> Micro gas turbines

Pressure Vessel & Piping
There are two approaches in pressure vessel designs: Design by code and design by analysis.
The vessel can be sized and design based on the rules and formula specified in the standards. The design following the relevant codes provide a vessel which is safe to work under the design pressure.
More recent development in pressure vessel design is design by analysis, which is often used in the cases where the structure involved not covered by the design codes.
TriVista’s engineers have experience in design pressure vessel following design code and more often provide consulting service on pressure vessel is linked to design by analysis. Generally speaking, the pressure vessel design codes are conservative. When the engineer want to push the limit set by the design code, the design by analysis approach also be used as design by analysis is carried out using FE analysis which will give more accurate stress results. The relevant stress components (membrane stress, bending stress or membrane stress intensity, bending stress intensity) are assessed by the criteria set by relevant standards (Hopper Diagram).

Motion Analysis
Motion analysis can be used to check whether there is an over constraint in the design which may prevent the intended component movement.
The information of acceleration of a moving component can be important so that the assessment can be made to judge whether it is safe to have equipment to be linked to that component. If the moving part is a seat and these is a passenger sit on it, the motion analysis will be able to provide information on safety assessment or implication on health.
The components in motion analysis is assumed to be rigid bodies. The information from motion analysis can be fed into FE structural analysis as loads or boundary conditions so that further stress analysis can be carried out under these dynamic boundary conditions.

Electronic Motor Design Mechanical
During the mechanical design of electrical motors, wide range of design and analysis subjects were involved:
> Mechanical design of general assembly and components.
> Stress analysis of the components at high rotational speed.
> Thermal analysis to evaluate the heat dissipation of the electrical motor especially when the power density become increasingly higher in recent electric motor designs.
> Rotordynamics to achieve a good design so that the motor rotor does not run at or near its critical speeds.

Manufacture Outsourcing
TriVista is your UK based link to China manufacturing outsourcing and we offer a range of services to help companies access the benefits and opportunities that China has to offer including..
> Outsourcing of both large and small manufacture projects to China.
> Consulting support to manufacturing and engineering projects in China. This includes:
> Support in communication of both commercial and technical issues.
> Problem solving in outsourcing projects.
> Quality control audit and inspection assistance.
> Assistance in establish business partnership with Chinese companies, including…
> Researching and identifying suitable business partners in China.
> Factory and exhibition visit assistance.
> Relevant commercial and technical negotiations.
> Technical information service including…
> Sourcing Chinese technical and industrial standard documentation.
> Research on information in relevant industrial sections.

Manufacture Outsourcing to China
TriVista is your UK based link to manufacturing outsourcing in China and we offer you the following advantages: significant experience in doing business in China; extensive engineering knowledge and an established network of quality manufacturers offering a wide range of services.
TriVista has assisted many UK businesses with outsourcing their product and component manufacture to Chinese manufacturers including:
> Precision machined components for aerospace applications.
> Railway equipment.
> Medical equipment.
> Electric motors.
> Casting metal components.
> Metal fabrication.
> Plastic and rubber components.

Manufacture Outsourcing Consulting
China is a large country with many manufacturers with varying capabilities and quality standards. TriVista have found it is important to work with manufacturers who are competitive, maintain good quality standards and are also good in communication.
In larger and more complicated manufacturing projects, many requirements have to be communicated well to the manufacturing partners especially quality control. We have found that effective communication of the quality requirements is the key to achieving good results.
There are culture differences and different business negotiation styles between UK and China. Certain local business practices need to be understood and international standards have to be achieved by the manufacturer.
TriVista supports clients in: identifying good manufacturing partners, communicating technical requirements, commercial discussions, contract negotiations, quality control, intellectual property and compliance to relevant industrial regulations etc.
TriVista can also assist with arranging logistics and quality inspections.
If you think that outsourcing a manufacture project will help your business to lower manufacture costs and improve competitiveness, we will be glad to help. Contact us now to find out how we can assist with your next manufacturing project.
About us
Our expertise lies in the field of Finite Element Analysis (FEA) ad Computational Fluid Dynamic (CFD) software which is coupled with our Engineering Design skills and capabilities. Common to all analysis projects is the use of strong analytical skills combined with substantial practical engineering experience.
Here at TriVista Engineering our highly qualified team of engineers have a good mix of production and development backgrounds enabling them to provide strong analytical and practical skills and deliver solutions that are of real commercial value to our clients.
In addition to engineering analysis and design support we also have strong links with a number of large China Manufacturers and can assist with outsourcing manufacture as well help with engineering products. TriVista Engineering has the experience with both large complex engineering systems and smaller component manufacturing projects.

Sponsored Links
Trade Associations

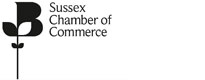