Quick Links:
Products / Services
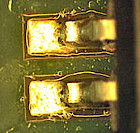
PCB Cleaning
Even though in many low-end production processes the use of "no-clean" works well, high-end assemblies that will be employed in industries such as automotive, telecommunications, military, and aerospace, require the use of a specific PCB cleaning agent.
The targeted use of a PCB cleaning agent substantially affects all subsequent process steps such as wire bonding and conformal coating since it primarily removes the resin and activator residues. If left on the assemblies, residues can cause the improper adhesion of bonds which can lead to failures such as heel cracks or lift-offs. During the coating process, remaining residues can result in poor wettability and the delamination of the conformal coating which is known to cause assembly failures, i.e. in-field failures.
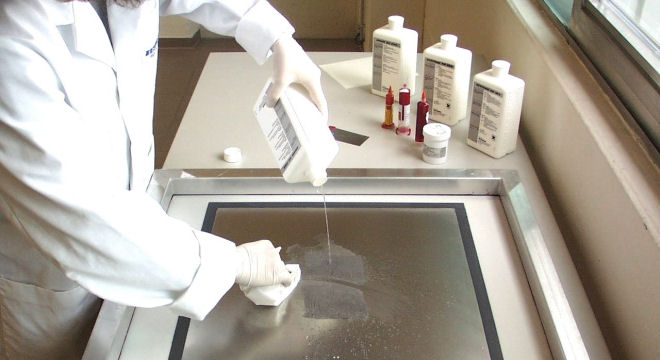
Stencil & Screen Cleaning
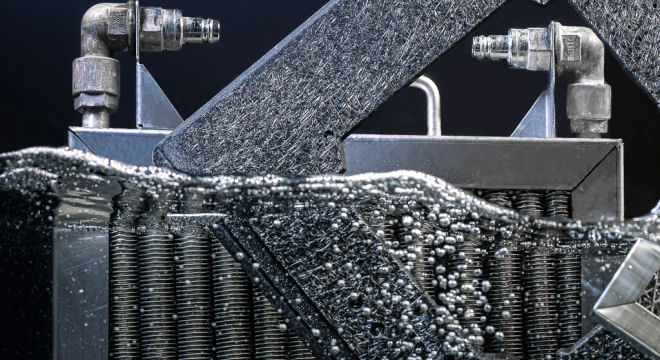
Maintenance & Tool Cleaning
Other areas of maintenance cleaning include the cleaning of solder pallets and condensation traps, conveyor fingers as well as the reflow ovens and wave solder systems. Furthermore, the cleaning of dispensing needles is another application within maintenance cleaning.
ZESTRON offers aqueous based FAST® cleaning agents and modern solvents for maintenance and tool cleaning applications in the electronics manufacturing industry. These maintenance cleaning products can be used manually as well as in ultrasonic and spray equipment.
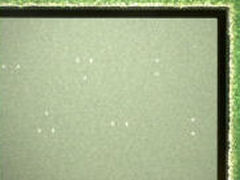
Power Module Cleaning
There are two main requirements for this cleaning process:
Complete removal of flux residues and in particular flux spatter from substrates and chips
Visually flawless and spot-free substrate surfaces and chips, i.e. free of oxide layers
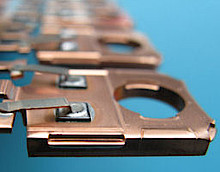
Cleaning of Leadframes & Discrete Components
Complete flux removal from the soldering process
Removal of all inorganic stains and activation of the copper surfaces
Material compatibility of the cleaning agent with all materials, e.g. copper and chip passivations
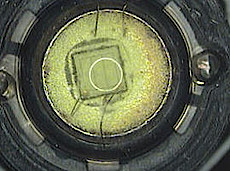
Power LED Cleaning
If flux residues on the substrate and specifically flux spatter from the soldering process on the chip surfaces are not completely removed, they can lead to unfavorable bonding conditions. These often result in heel cracks and even chip defects due to unnecessary high bonding power.
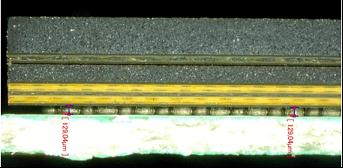
Flip Chip Cleaning
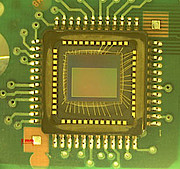
CMOS Cleaning
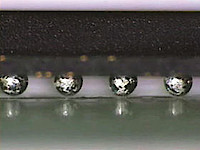
BGA Cleaning After Balling
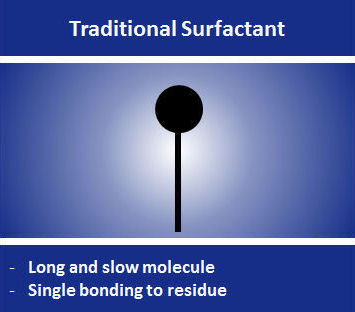
FAST® Technology
This new cleaning technology features shorter and more agile surfactant structures which allows them to move faster on the surface than traditional surfactants.
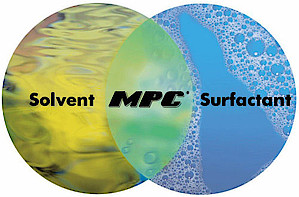
MPC Technology
The unique feature of MPC® Technology is that it combines the advantages of traditional solvents and surfactants without their drawbacks.
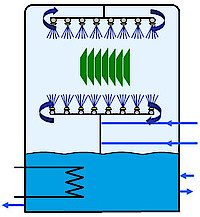
Spray Process
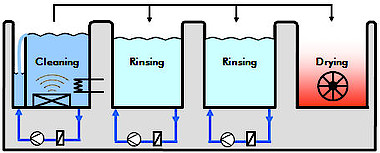
Dip Tank Process
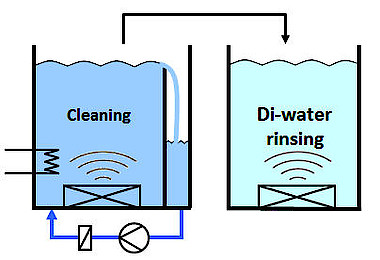
Ultrasonic Cleaning
Typical cleaning frequencies range from 35 kHz to 45 kHz. Through ultrasonic transducer elements attached to or directly fixed in the cleaning tank, under-inflation and overpressure waves spread in the cleaning bath. Cavitation creates a pressure jet (microjet) that helps remove the dirt particles from the surface.
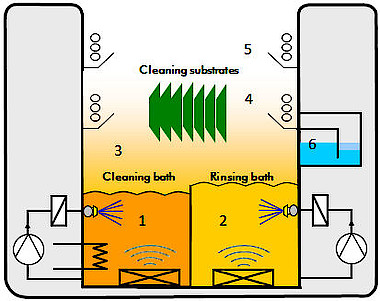
HFE Co-Solvent Cleaning Process
Together with a co-solvent, the HFE is used in a cleaning bath with spray-under-immersion or ultrasonic agitation in order to dissolve persistent residues. The rinsing step takes place in a bath with HFE only and subsequently with steam rinsing. Finally, the PCBs are dried by intensive cooling. This process must be carried out in a cleaning machine with efficient cooling technology, preventing evaporation of the HFE.
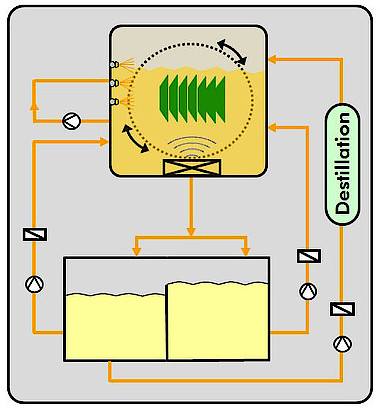
One-Chamber Vacuum Process
Most solvents have long bath life and due to their efficient drying properties, short process times can be achieved. For one-chamber vacuum processes, the cleaning machine must be explosion-proof.
If you have questions regarding the different cleaning mechanics/ process types or would like to conduct cleaning trials with different cleaning machines at our Technical Center, please contact our Process Engineers.
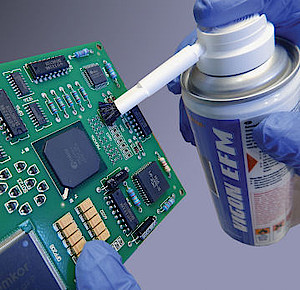
Manual Cleaning
Manual cleaning is often a popular alternative if the throughput is low, e.g. when building prototypes, or during PCBs / electronic component rework or repair. Manual cleaning can be performed immediately and without investing in equipment. If a production facility with medium / high throughput and several shifts requires excellent cleaning results, an automated cleaning process is then preferred.
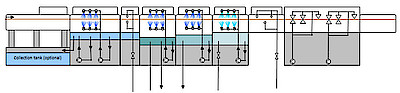
Inline Process
Before deciding on an inline process, its necessary to consider the footprint. Inline machines require larger floor space in comparison to batch cleaning machines. An inline system can only be integrated into the production line when the entry and exit of the assemblies as well as the cleaning itself are fully automated.
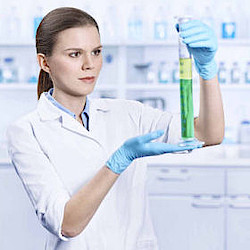
Cleaning Bath Monitoring
Regular wash tank monitoring is necessary to ensure consistent results in cleaning processes of electronic assemblies or power electronics. There are manual and automatic methods available.
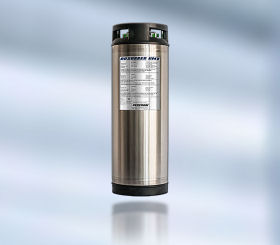
Cleaning Agent Regeneration & Recovery
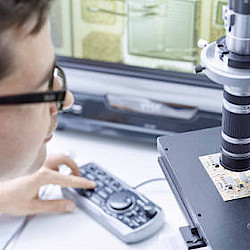
Cleanliness Analysis / Surface Analytics
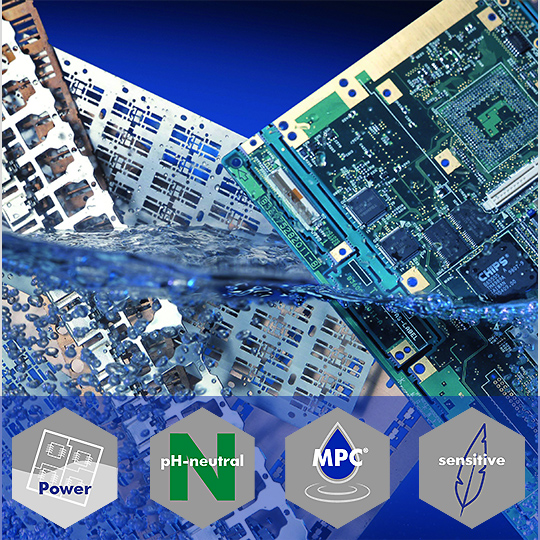
Cleaners for Power Electronics
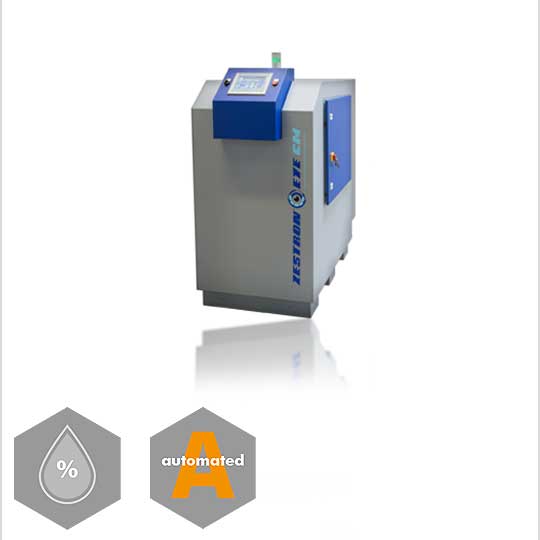
Process Control
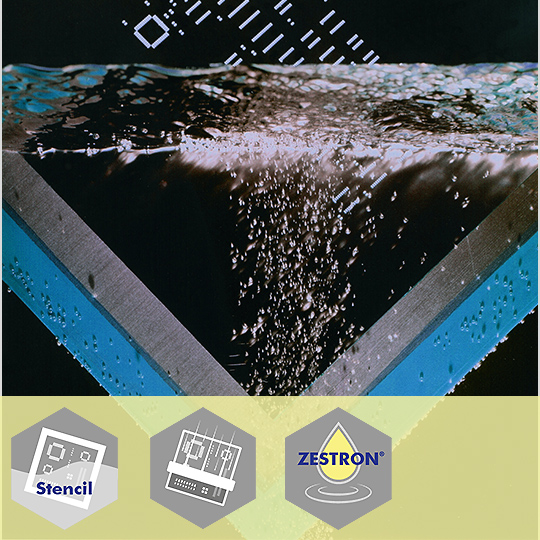
Stencil Cleaners
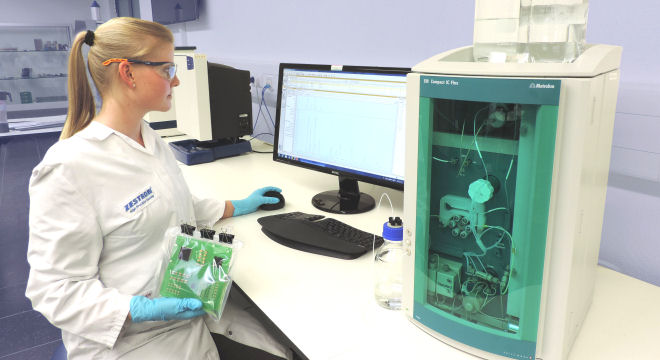
Cleanliness & Surface Qualification
The available processes can be divided into visual, chemical and physical test methods. Thus, all cleaned substrates, such as power modules, PCBs, stencils and tools, as well as the quality of your cleaning bath itself can be analyzed using various techniques.
About us
Leading specialists in SMT electronics cleaning, power electronics and semiconductor cleaning, our team of experienced process engineers have the ability to develop new and innovative solutions and cleaning processes that allow for a fully functioning optimal cleaning system. Our services are reliable, cost effective and highly recommended all over the world.
Here at Zestron, we offer a variety of cleaners for various applications, including printed circuit boards, power modules, semiconductor packages, flip chips, stencils, screens, solder pallets, reflow ovens, wave solder systems, squeegees and many others. Our main aim as a company is to help customers avoid flux activator residues, resin residues to gain the optimum cleaning results for reliable products.
Our impressive range of products help with cleaning agent regeneration and recovery as well has wash bath monitoring (e.g. the ZESTRON EYE) for the best performance and control of the cleaning process.
Zestron Europe not only offers high quality cleaning solutions for SMT and Semiconductor production; we also provide in-depth training and coaching which has allowed individuals to gain more of an understanding of surface cleanliness, conformal coating requirements and optimization of the cleaning process.
With over 3000 successfully installed cleaning process around the world for various industries, e.g. automotive, aviation, telecommunication, medical and others our engineers have the expertise to find the right solution for your specific requirements. Reliability is our driver in every aspect of our work!
We offer a variety of training formats depending on the requirements of the client, such as technology coachings, in-house training and online training. Our training courses have been highly recommended by our loyal customer base for many years, who have praised our hands-on, flexible approach to learning about electronics cleaning.
Our philosophy is to develop our extensive research to the highest possible standard and following environmental and safety procedures. Our company is ISO:9001 certified and ensures high quality and environmentally friendly working processes.
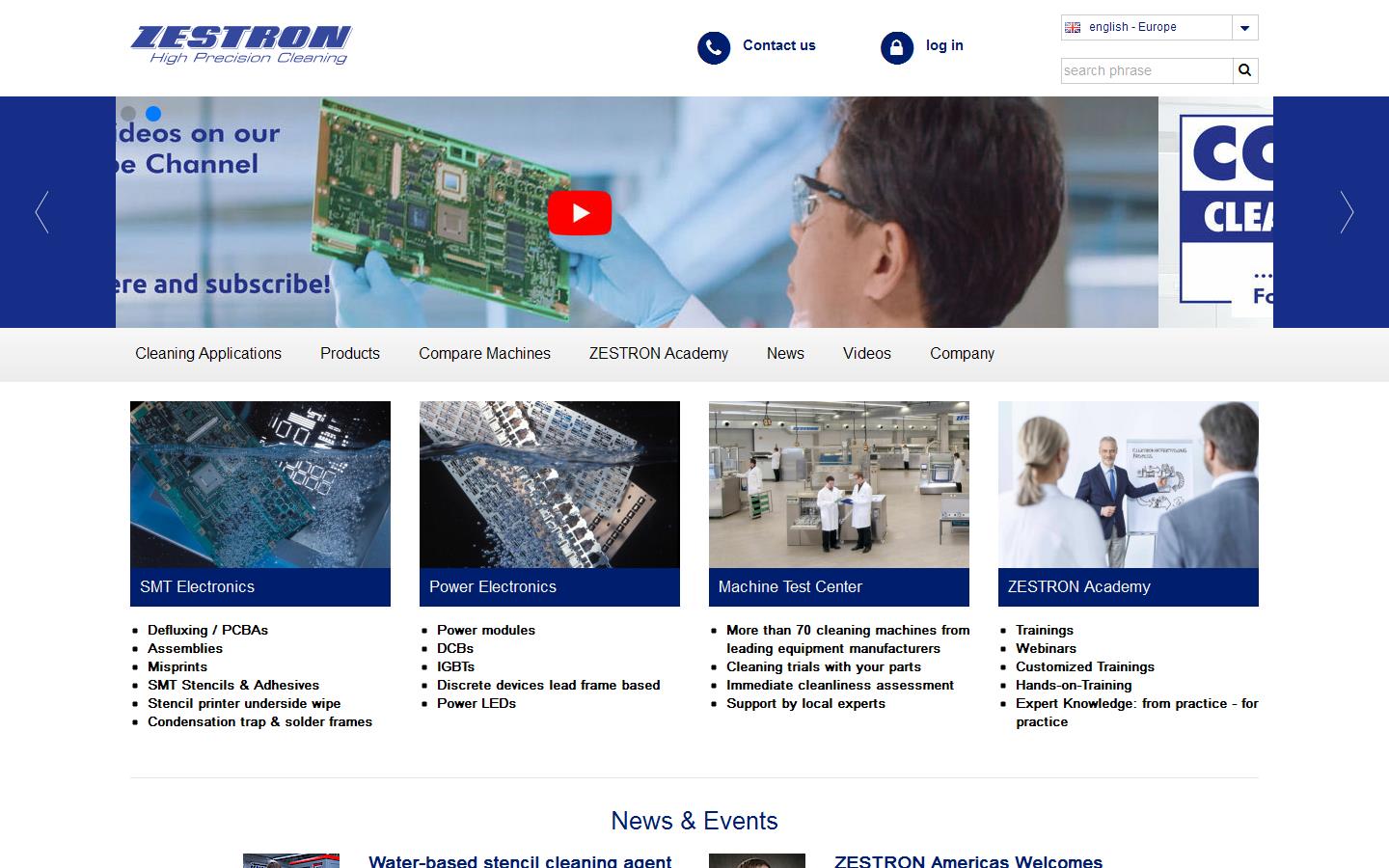