Company details for:
Laser Cladding Technology Ltd
Unit 1,
Coach Crescent,
Shireoaks,
Worksop,
Nottinghamshire,
S81 8AD,
United Kingdom
Quick Links:
Products
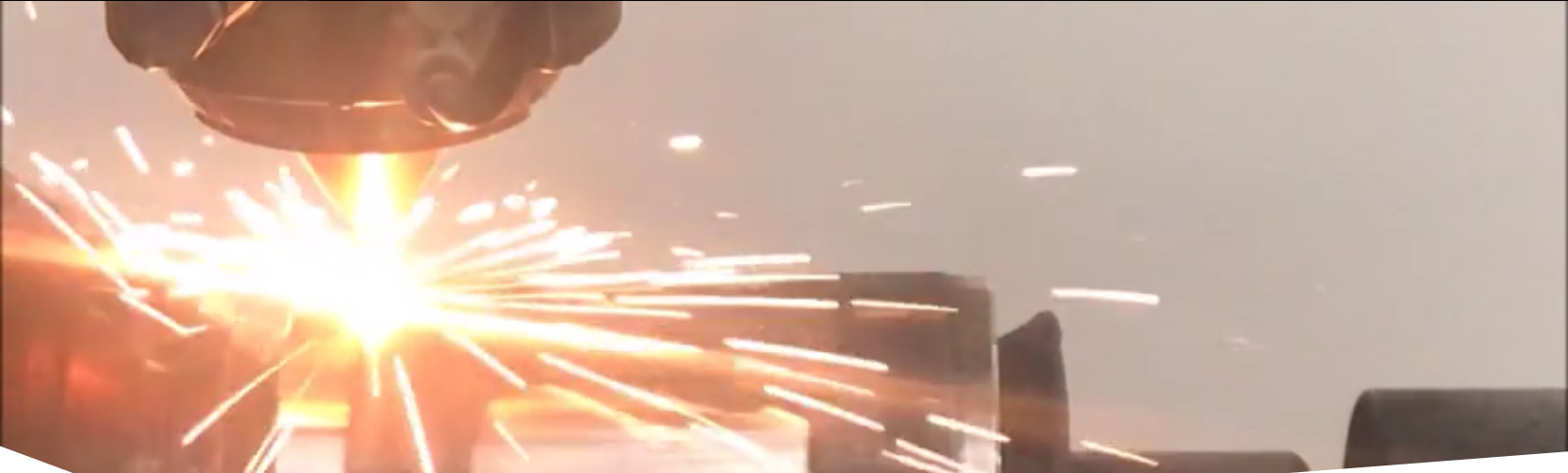
The Laser Cladding Process
A stream of a desired metallic powder is fed into a focused laser beam as it is scanned across the target surface, leaving behind a deposited coating of the chosen material.
This enables the applied material to be deposited selectively, accurately and with minimal heat input just where it is required.
Process Advantages
Additional material can be placed precisely where desired.
A very wide choice of different materials can be both deposited and deposited onto.
Deposits are fully fused to the substrate with little or no porosity.
Minimal heat input results in narrow HAZ (heat affected zone).
Minimal heat input also results in limited distortion of the substrate and reduces the need for additional corrective machining.
Easy to automate and integrate into CAD/CAM and CNC production environments.
Materials
With a large number of materials processed on a daily basis, Laser Cladding Technology is always looking to decrease overall costs and increase component life. Our contribution to this industry has been to provide customers with coating solutions tailored to suit their individual needs.
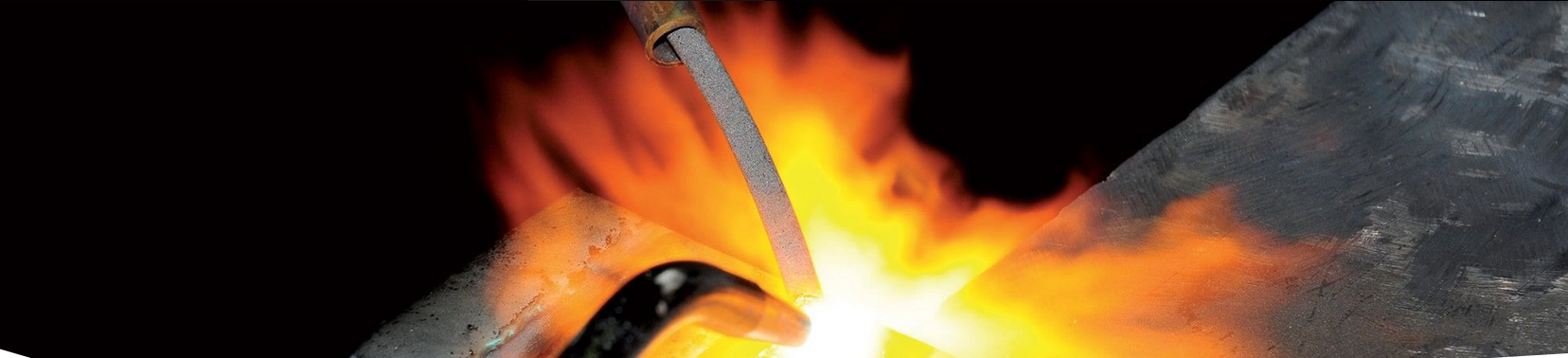
Hardfacing Wires
The difference between Technodur® and Technosphere® lies in the use of spherical Tungsten Carbide grains (Spherotene®).
The spherical shape and extreme hardness of Spherotene® gives Technosphere®, amongst other properties, two main advantages:
Good shock resistance
Unequalled wear resistance
This type of welding is easy, economic and also offers the major advantage of preserving the hardness of the Tungsten Carbide particles, which would not be the case if using other welding processes.
USE & PACKAGING:
Can be applied to all non-martensitic steels and weldable stainless steels. Can be welded easily onto itself for refurbishment of worn parts.
Can be applied in-house by our trained personnel to your free issue parts, or is available on 5kg or 20kg coils for your own application.
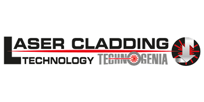
Premixed Carbide Powders
Applications: Thin hardfacing
Machining: Not possible
Grinding: Possible
Technopowder 40/40 Nickel base + crushed cast Tungsten Carbide 2000 HV +/-200 HV
Applications: Hardfacing, medium thickness, causes very few deformations. Crack-free hardfacing Recommended for stainless steel
Machining: Not possible
Grinding: Possible
Technopowder 4000 Nickel base + Spherotene® 3000 HV +/-500 HV Very high hardness spherical cast Tungsten Carbide
Applications: Very high performance hardfacing, low thickness
Machining: Not possible
Grinding: Possible
Technopowder 4040 S Nickel base + Spherotene® 3000 HV +/-500 HV Very high hardness spherical cast Tungsten Carbide
Applications: Very high performance hardfacing, medium thicknesses on base materials susceptible to deformation, e.g. stainless steels. Crack-free hardfacing
Machining: Not possible
Grinding: Possible
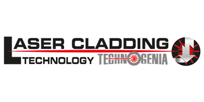
Nickel-Based Hardfacing Powders
Hardness: 40 Rc
Main application: Oxidation inhibiting underlayer for Technodur® and Technosphere®
Technopowder 60 Rc / TP 60 Rc
Hardness: 60 Rc Base
Composition: Ni Cr B Si: (12 to 16% Chromium)
Main application: Finishing or sliding coat for barrel extruder and screw conveyor faces.
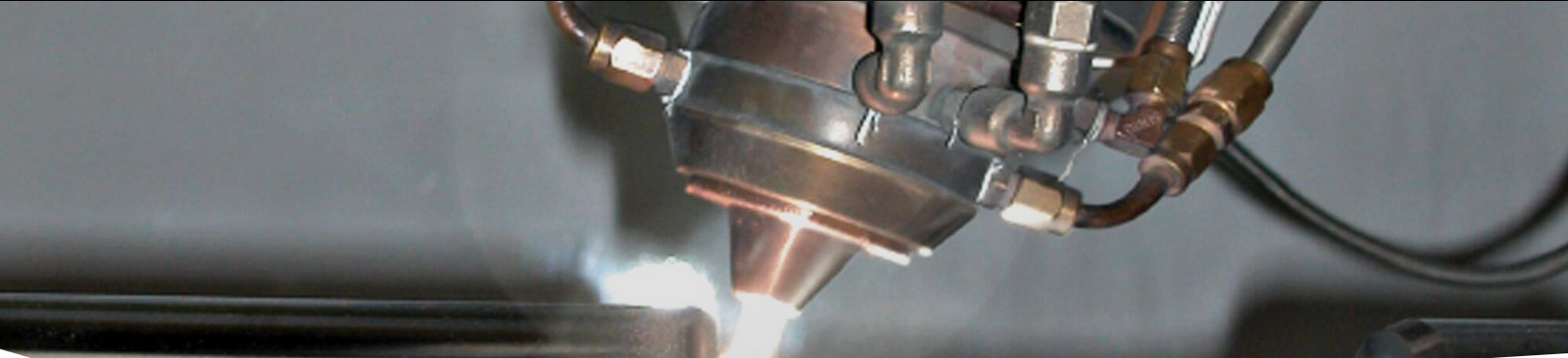
Repair & Remanufacture
The Laser Cladding process lends itself to the remanufacture of used parts as materials can be deposited specifically where required, whilst keeping distortion and final machining operations to a minimum.
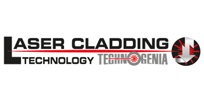
Research & Development
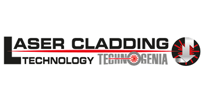
Hybrid Manufacture
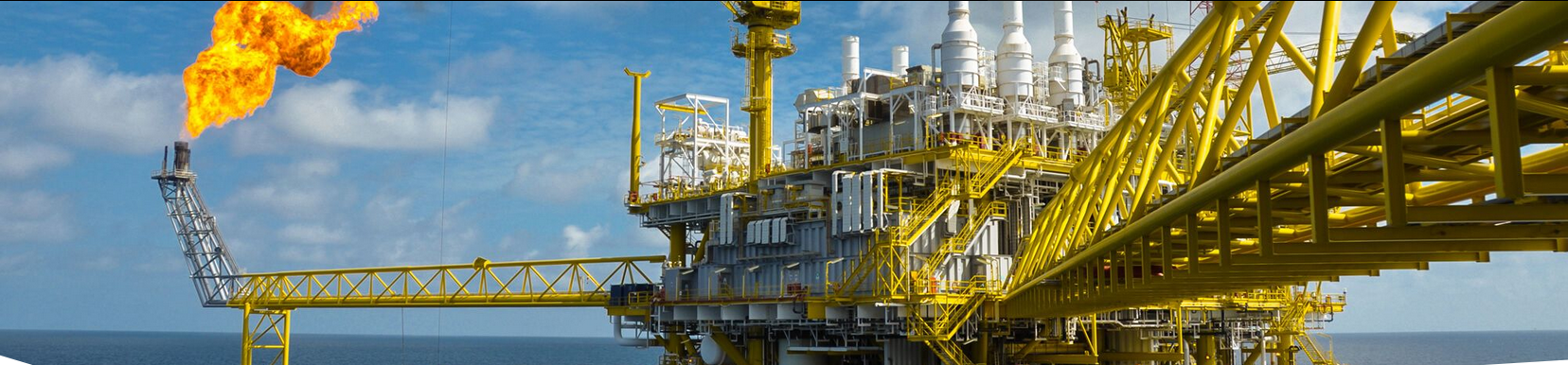
Down Hole Tooling
Technodur and Technosphere have been used for more than 20 years by the most demanding companies and workshops.Parts protected in this way are easy to repair.
Lasercarb:
The Lasercarb process is particularly recommended for protecting stabilizers and other drilling tools made of non-magnetic steel.
Coating thicknesses: 0,5 to 3 mm.
Technodur, Technosphere and Lasercarb may be ground to achieve exact size. This operation is simplified with the Lasercarb process, which yields an extremely close deposit and any grinding required to finish is minimal.
Applications:
Stabilizers
LWD & MWD tools
Drilling Heads
Wear Bands
Radial Bearings
Mud Motor Parts
Non-Magnetic Steel: the LaserCarb® process is particularly recommended for protecting stabilizers and other drilling tools made of non-magnetic steel.
Other Applications:
Customers facing challenges other than abrasion, such as erosion or corrosion, can feel secure in the knowledge that LCT can apply a large selection of materials to resolve customer specific problems.
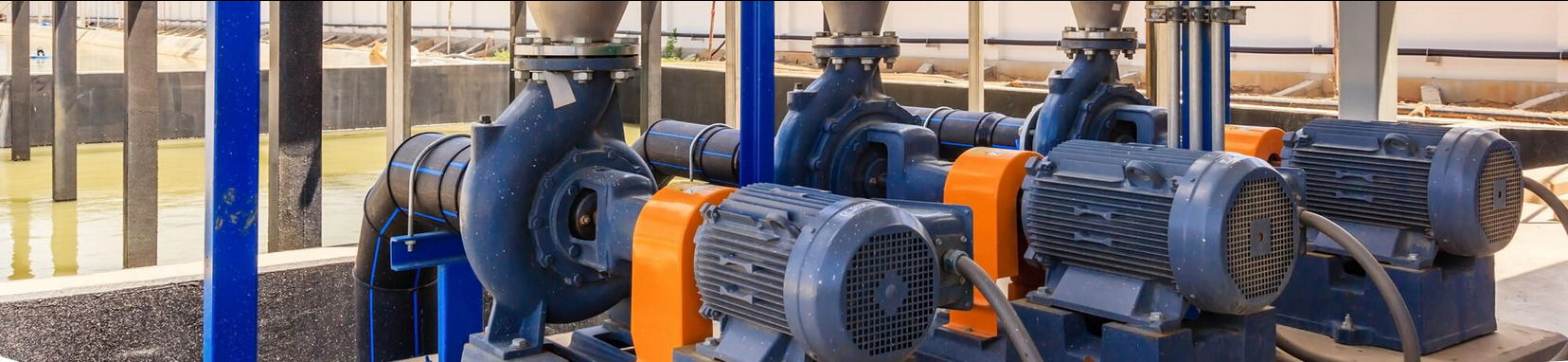
Pumps & Valves
Applications
Anti-corrosion/ erosion/ wear coatings for all types of Pump and Valve components.
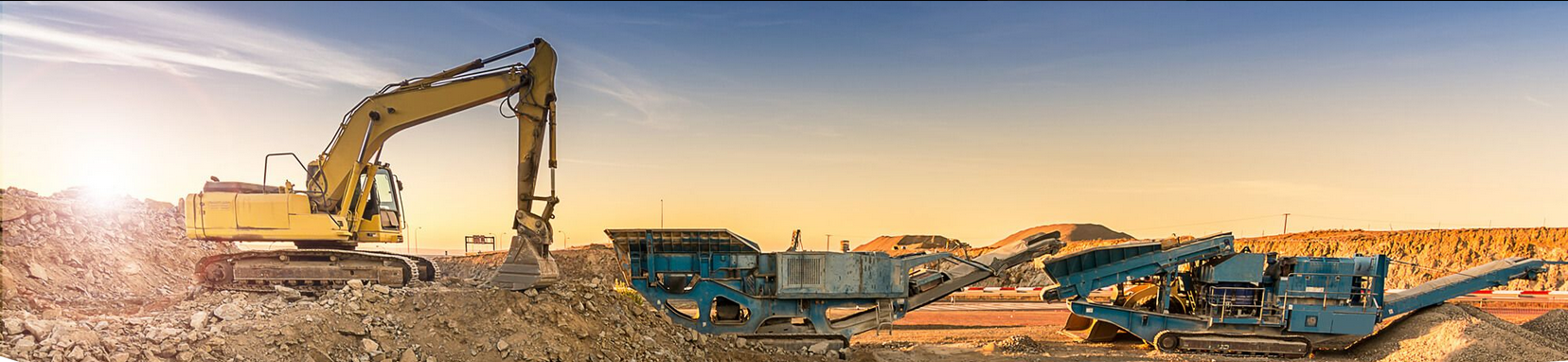
Material Processing
Industries to have benefited from using either our patented LaserCarb® or one of our manually applied hardfacing wires, Technodur® or Technosphere® include:
Refractory Processing
Fibre Glass production
Pulp & paper production
Wood Processing
Mineral processing
Cement Production
Applications:
Pulper Rotors
Mixer Knives
Hammer Mills
Classifiers
Pan Grids
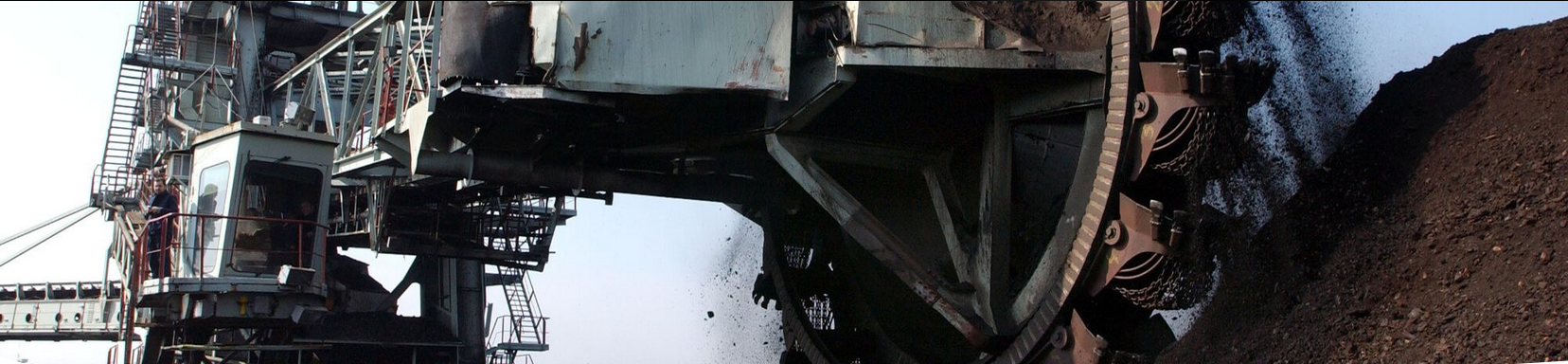
Mining / Tunnelling
Applications:
Cutter Teeth
Trenching Tools
Conveyor Screws
Sieves
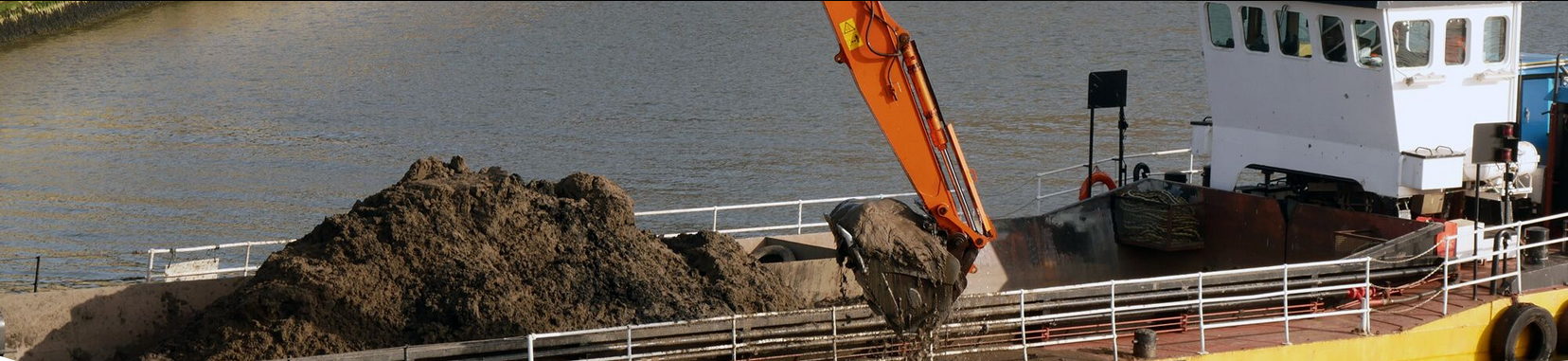
Dredging
The dredging sector is divided into two types of market. The first of these concerns dredging contracts, including not only the performance of dredging operations and associated maintenance but also backfilling operations. The second relates to offshore contracts (e.g. pipelines and platforms).
Whether using our laser cladding process “LaserCarb®” or our manually applied Technodur® or Technosphere® hard facing wires, Laser Cladding Technology can solve your wear problems where other hard facing techniques have failed.
Applications
Cutter teeth (flat, chisel, pick points)
Draghead teeth and wear plates
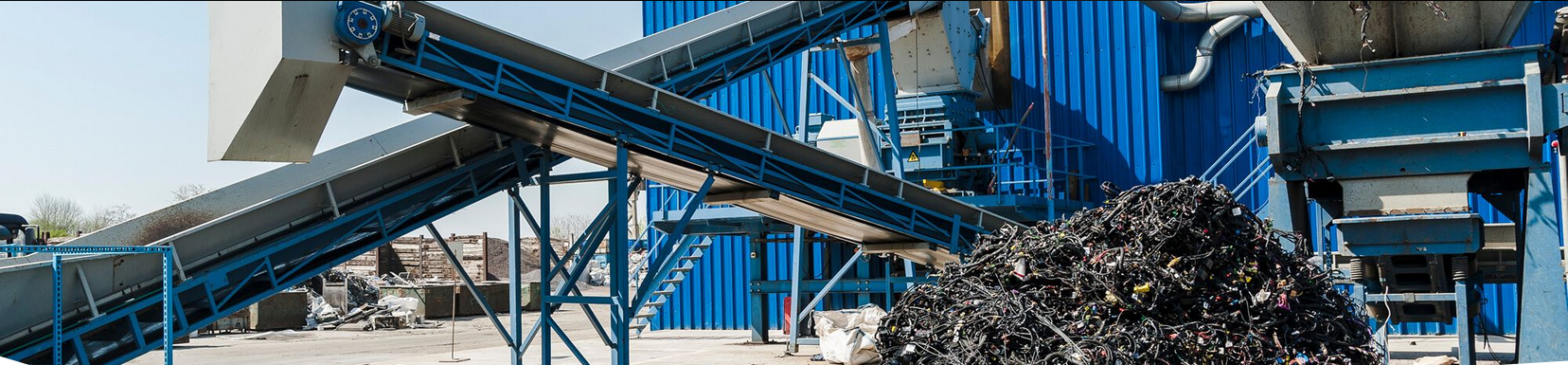
Recycling
Laser Cladding Technology can offer coatings that will increase the lifetime of components in service and decrease the need for costly un-planned and scheduled maintenance.
Whether using our laser cladding process “LaserCarb®” or our manually applied Technodur® or Technosphere® hard facing wires, Laser Cladding Technology can solve your wear problems where other hard facing techniques have failed.
Applications
Anti −corrosion / erosion coatings for waste to power boilers.
Hammer mills
Shredders
Glass recycling equipment
Tyre shredding
Conveyor Screws
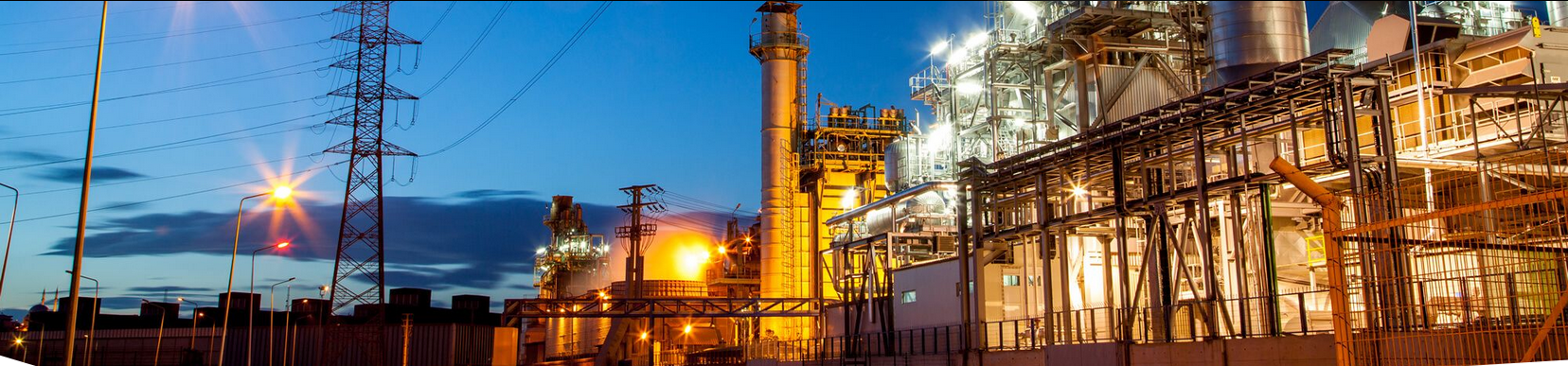
Power Generation / Renewables
Whether using our laser cladding process “LaserCarb®” or our manually applied Technodur® or Technosphere® hard facing wires, Laser Cladding Technology can solve your wear problems where other hard facing techniques have failed.
Applications:
Anti-corrosion / erosion coatings for Boiler pipes
Rebuild of critical gearbox components
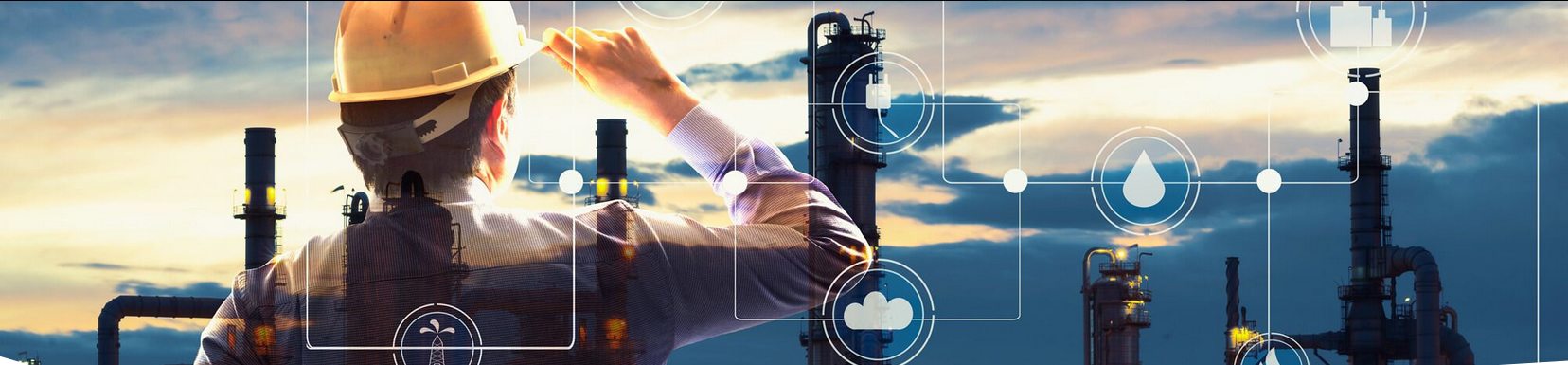
Other Industries Served
Whether using our laser cladding process “LaserCarb®” or our manually applied Technodur® or Technosphere® hard facing wires, Laser Cladding Technology can solve your wear problems where other hard facing techniques have failed.
Industries we service:
Concrete Manufacture
Brick and Tile Manufacture
Foundries
Food Industry
Iron and Steel Industry
Paper Manufacture
About us
Our reputation has been established through collaborations with prominent Blue Chip organisations in the UK, and we extend our services to numerous industries. The laser cladding process has proven to be a source of fresh and inventive solutions for our clients.
Laser Cladding Technology employs diode laser technology and utilises patented Tungsten Carbide wear-resistant materials from Technogenia, along with various other metallic compositions. This enables us to provide exceptional material deposition solutions that are precisely customised to meet our customers' specific and demanding needs.
The Laser Cladding Process
Laser Cladding, also known as Laser Deposition, is a controlled processing method employed to add one material onto the surface of another.
The process involves directing a focused laser beam across the target surface while simultaneously feeding a desired metallic powder into the stream. This results in the deposition of the chosen material as a coating on the surface.
As a result, the applied material can be selectively and accurately deposited with minimal heat input precisely where it is needed.
Process Advantages
It is possible to position additional material with precision exactly where it is intended.
A vast selection of diverse materials can be both applied and deposited onto the surface.
The deposits are completely fused to the substrate, exhibiting minimal or no porosity.
The limited heat input leads to a narrow heat-affected zone (HAZ).
Limited heat input also leads to reduced substrate distortion and decreases the necessity for additional corrective machining.
The process is easily automatable and can be seamlessly integrated into CAD/CAM and CNC production settings.
Industries That Have Experienced Advantages from Employing Laser Cladding Comprise of:
- Oil & Gas
- Pumps & Valves
- Materials Processing
- Mining & Tunnelling
- Dredging
- Recycling
- Power Generation / Renewables
- Refractory Processing
- Fibre Glass Production
- Pulp & Paper Production
- Wood Processing
- Cement Production
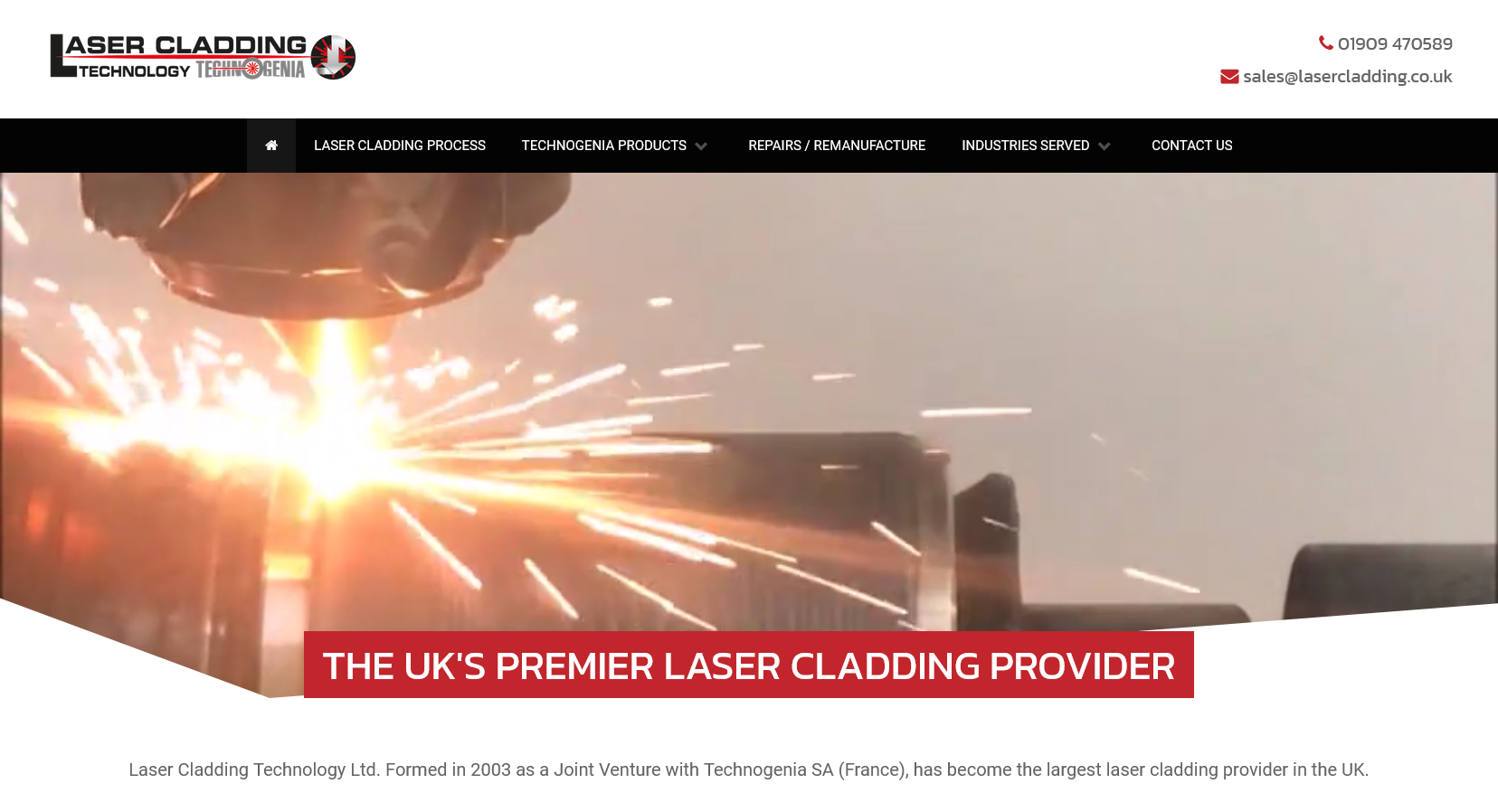
Sponsored Links
Trade Associations
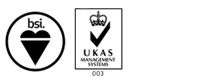