Company details for:
Sinotech Ltd
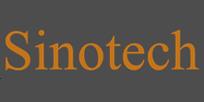
Unit B1,
Sovereign Park Industrial Estate,
Lathkill Street,
Market Harborough,
Leicestershire,
LE16 9EG,
United Kingdom
Quick Links:
Products
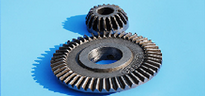
Sourcing Sintered Components Globally
Powder blending enables a uniform mixture, provides the appropriate material properties and ensures minimum friction during compaction.
Powder compaction permits a wide range of design flexibility in the radial aspect.
Sintering bonds the powder particles through diffusion, improving a component's mechanical properties.
Sizing and Coining (sometimes referred to as calibration) increases both precision and density and reduces the Powder Metallurgy part's roughness.
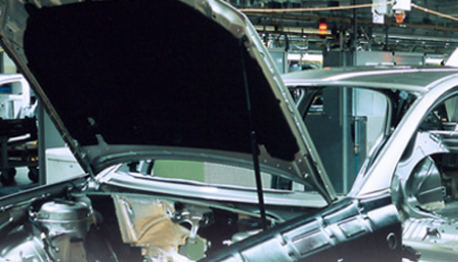
Castings
Investment Casting
This process allows the manufacture typically of small components, up to around 35Kg in weight to a very high degree of accuracy, 0.5% of length.
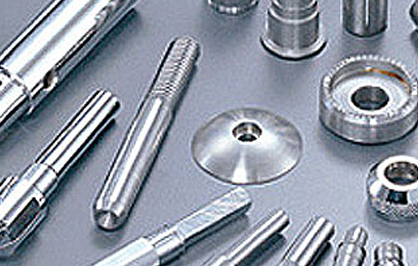
Precision Machined Components
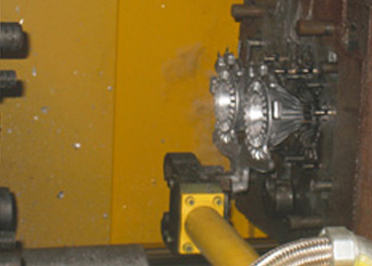
Die Casting
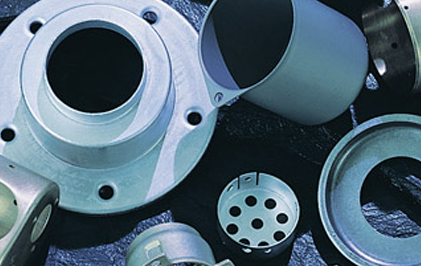
Pressings, Stampings & Assemblies
Prototype components can be produced to help the decision process arrive at the optimised final tooling design.
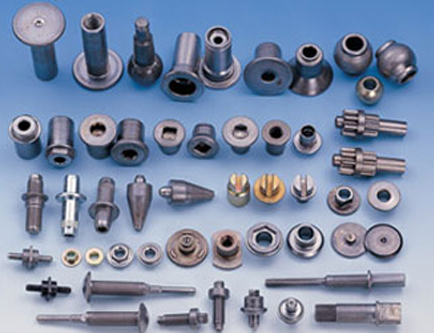
Cold Formed Parts
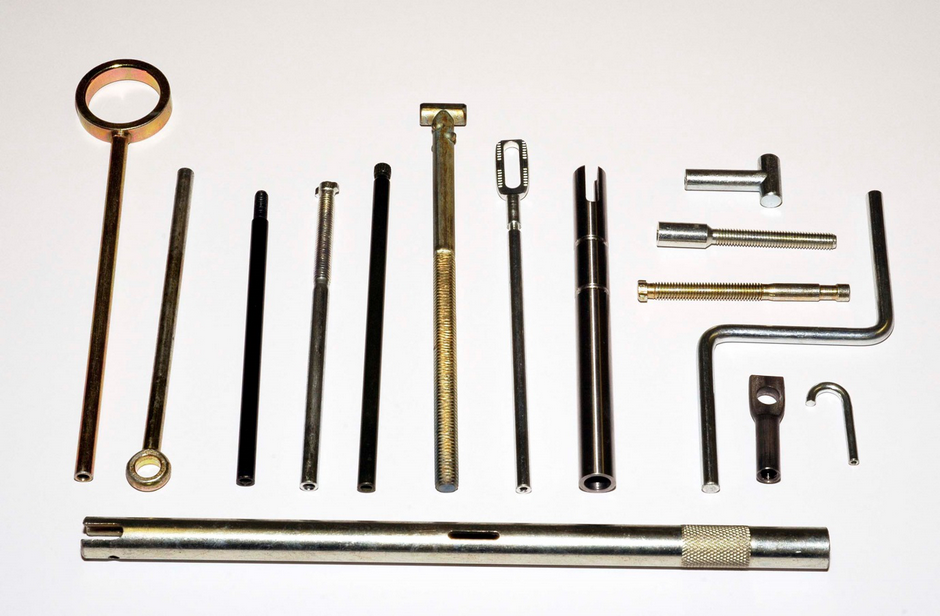
Push-Pull & Control Cable Components
Push Pull Cables are a type of flexible cable used to transmit mechanical force by movement of an inner cable relative to an outer cable − conduit.
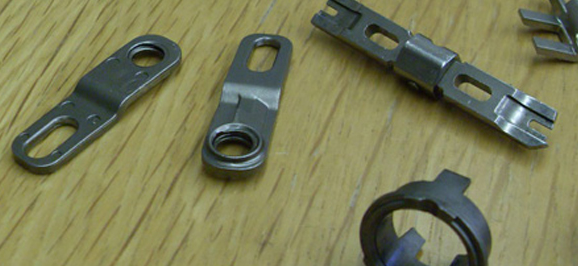
Metal Injection Moulding
MIM is a manufacturing process which is able to deliver near net-shape metal components by compressing metal powder in a special sintering process.
MIM offers significant cost savings compared to the use of conventional machining or electrical discharge machining. Used especially in the medical and automotive sectors, it can offer significant savings to customers.
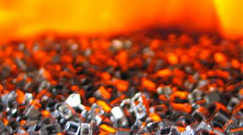
Additional Processes & Treatments
Controlled Atmosphere Heat Treatment
Vacuum Heat Treatment
Annealing
Solution Annealing
Quench and Temper ( Hardening)
Normalising
Induction Hardening
Case Hardening
Carbonitriding
Surface Treatment
Electroplating
Electroless Nickel Plating
Painting
E-Coating
Powder Coating
Phosphating
Zinc Alloy Plating
Zinc Flake Plating
Polishing
Electro Polishing
Mechanical Polishing

Optical Sorting
Automated Optical sorting is used to sort manufactured parts at very high speeds. This technology replaces error prone visual inspectors with a virtually fool proof software and camera driven system that can check up to a 1,000 parts per minute and record all dimensions and surface defects and push parts into GO and NOGO bins.
About us
Located in Market Harborough, Leicestershire, UK, we have many years of experience leading advancements in the production of complex metal components for a diverse international clientele.
Sinotech has grown into a "virtual manufacturer," overseeing the entire production process in detail without owning any manufacturing facilities. Instead, we coordinate and manage production through a network of carefully selected factories, with whom we maintain strong, long-standing relationships−one of our key strengths.
Our Products & Services Include:
Sintered Components
Powder Metallurgy involves several processes to produce sintered components. The conventional method includes four main steps: powder blending, which ensures a uniform mixture with desired material properties and minimises friction; powder compaction, allowing design flexibility in the radial direction; sintering, which strengthens the material by bonding particles through diffusion; and sizing or coining, which enhances precision, density, and surface smoothness of the final part.
Castings
Sinotech provides castings through a range of processes, including investment casting (lost wax/lost foam), silica sol casting, and sand casting.
Precision Machined Components
Sinotech has become a fast and flexible supplier of precision components, specialising in the automotive, fluid power, and general engineering industries, with over 70% of our turnover coming from exports. We take pride in delivering ISO 9001:2008 certified precision machined components to meet customer specifications. Our reputation is built on supplying precision turned parts efficiently and cost-effectively, from prototypes to mass production, making us the preferred choice for customers with new requirements. If you need turned parts, we would welcome the opportunity to provide a quote.
Die Casting
Gravity die casting uses cast iron moulds, enabling more precise and cost-effective production of aluminium and zinc castings compared to sand casting. Tooling costs for gravity die casting are significantly lower than those for high-pressure die casting. The rapid cooling process enhances mechanical properties, while the smooth filling minimises turbulence, resulting in heat-treatable castings with reduced porosity.
Pressings, Stampings & Assemblies
Sinotech collaborates with customers during the design phase, leveraging our extensive expertise in metal forming and tool design. We can produce prototype components to support the decision-making process and achieve the optimal final tooling design.
… And more.
Our customers expect absolute precision, quick response times, and the highest standards of product integrity regarding component characteristics, along with exceptional product quality and logistical support. As a result, it is essential to establish a trustworthy and reliable relationship with a supplier.
If you seek cost-effective components paired with top-tier service, consider Sinotech Ltd as your primary partner for the future.
All inquiries are handled professionally, and we strive to provide a quote within 72 hours of receiving your request.
Images
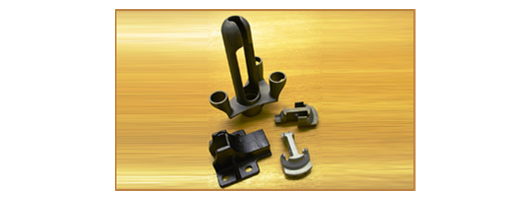
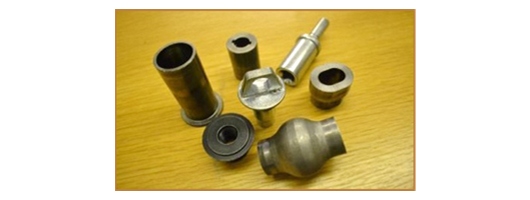
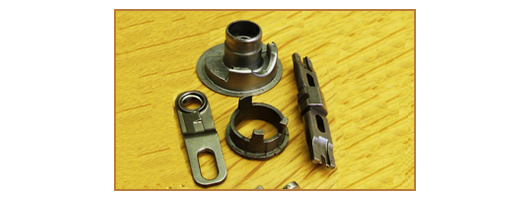
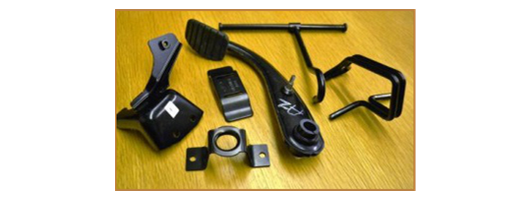
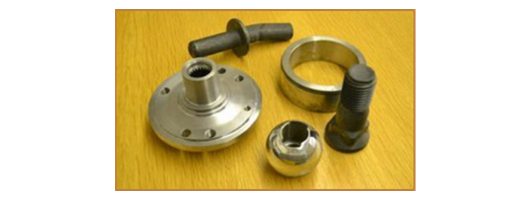
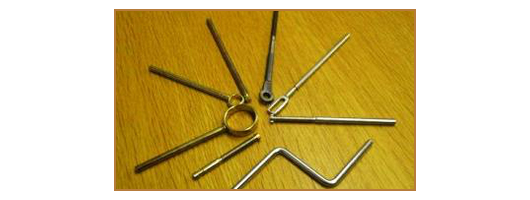
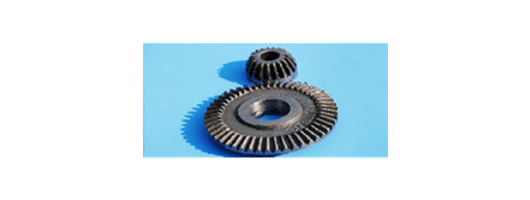
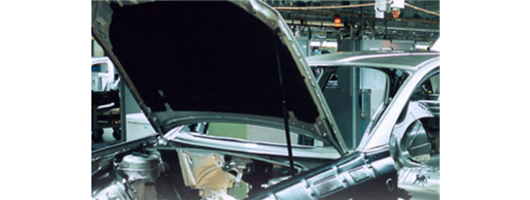
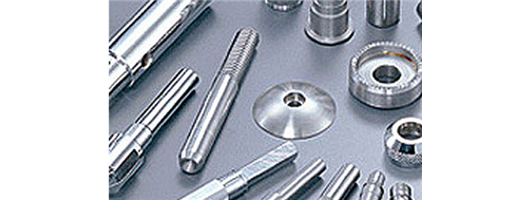
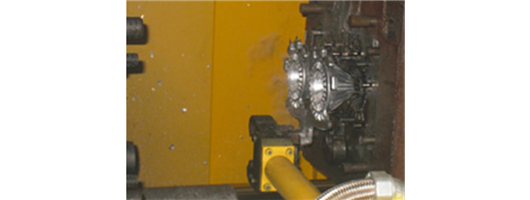
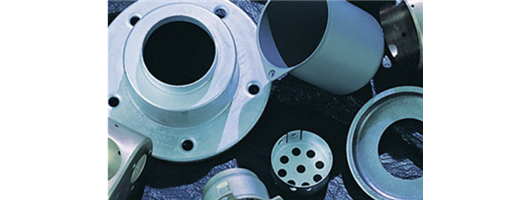
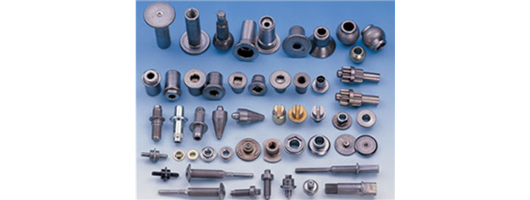
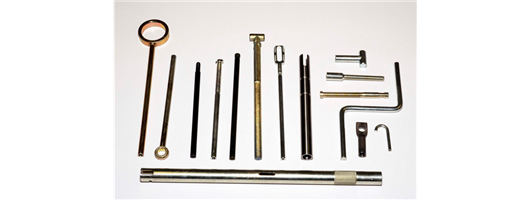
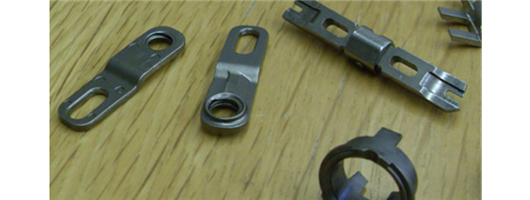
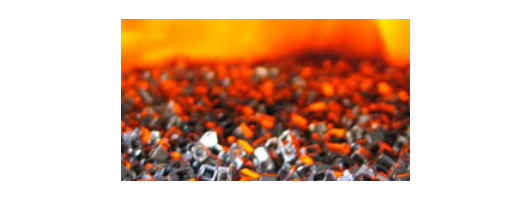
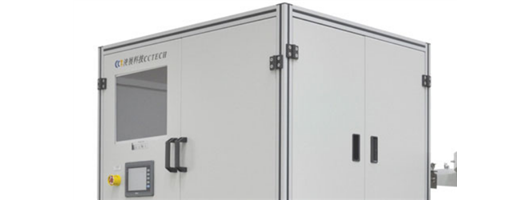
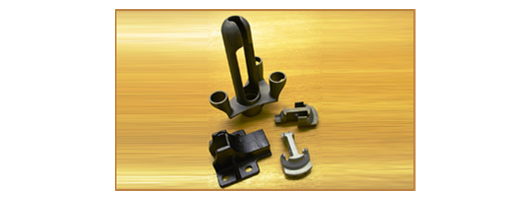
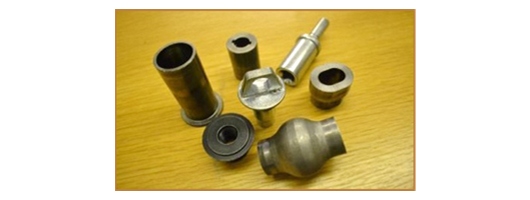
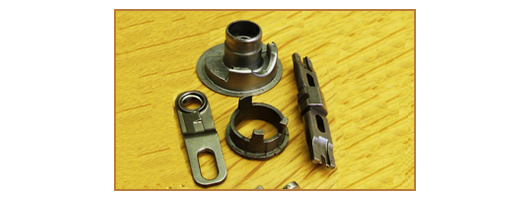
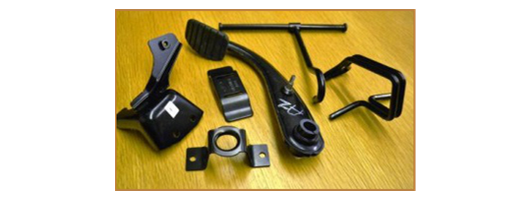
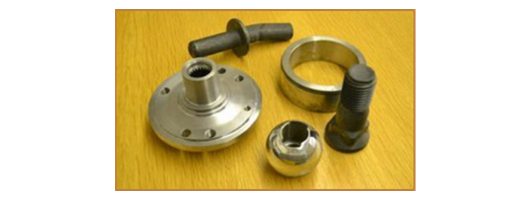
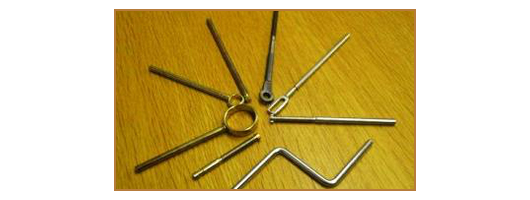
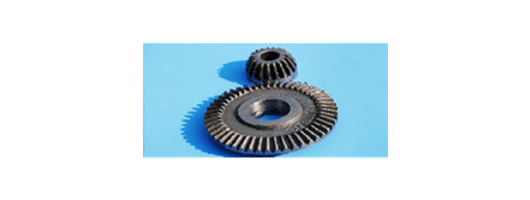
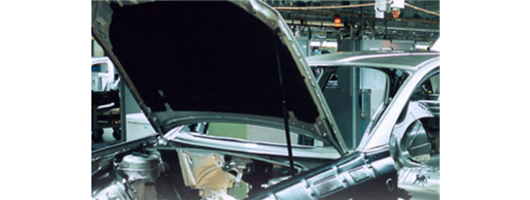
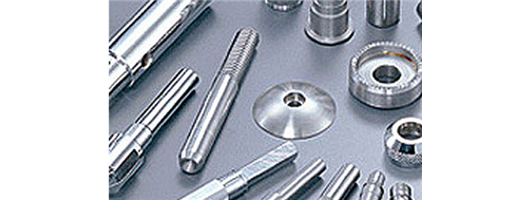
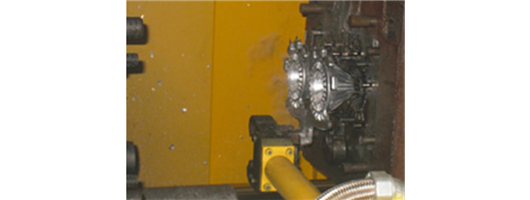
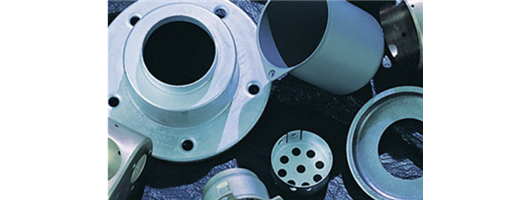
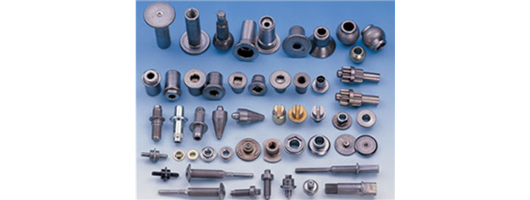
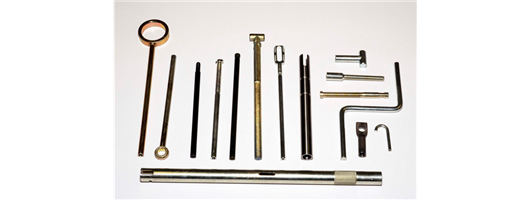
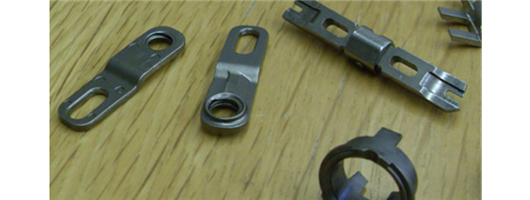
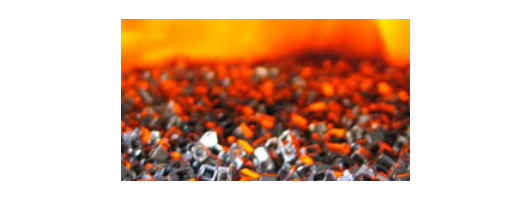
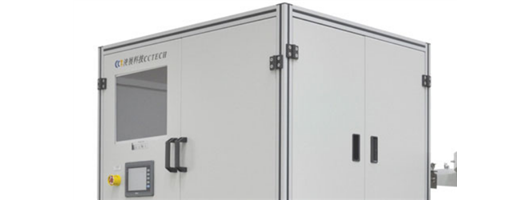
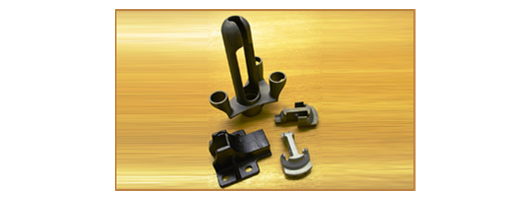
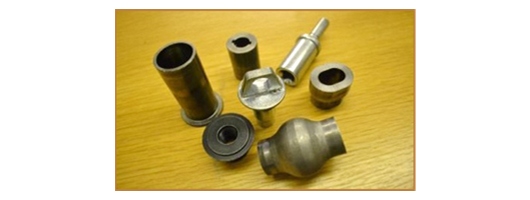
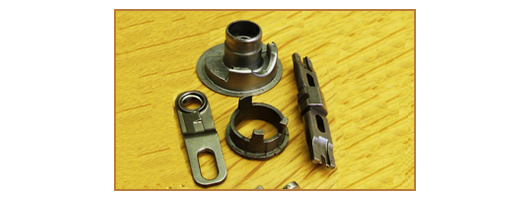
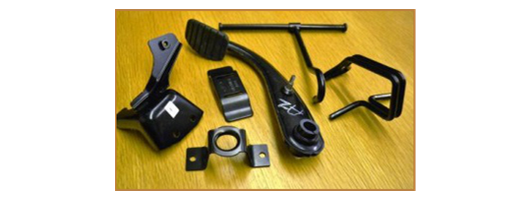
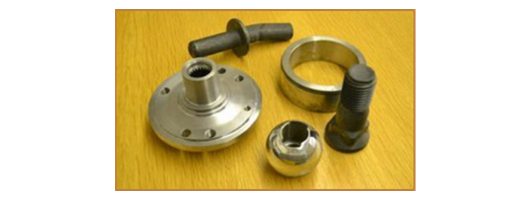
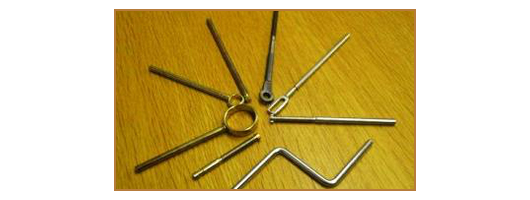
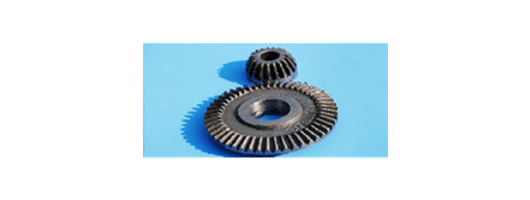
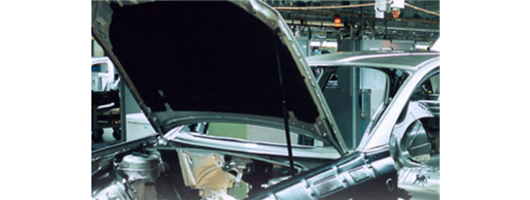
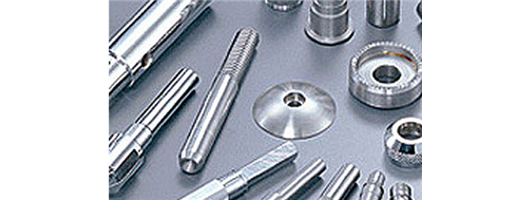
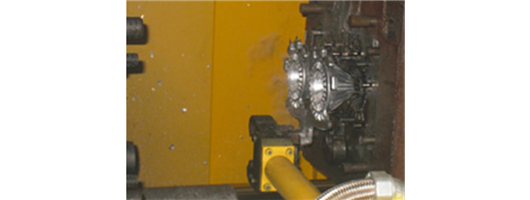
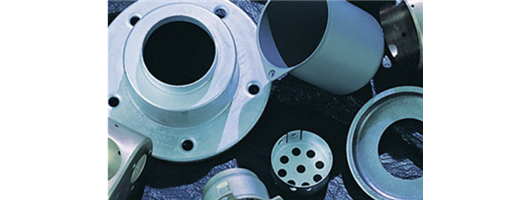
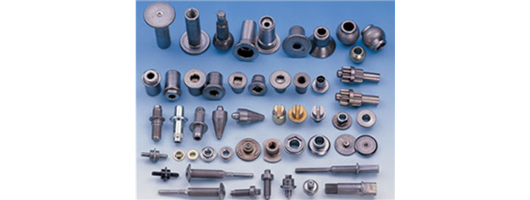
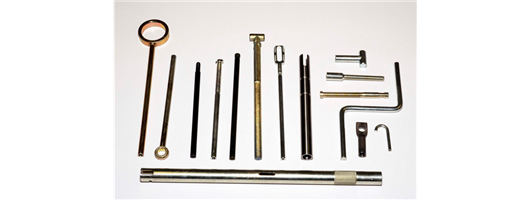
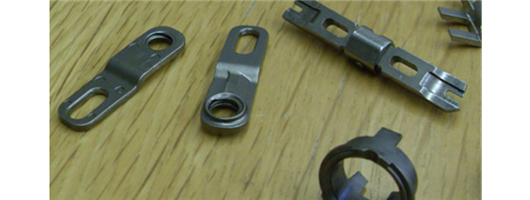
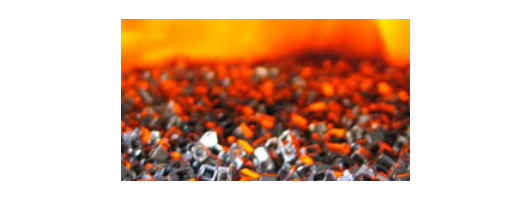
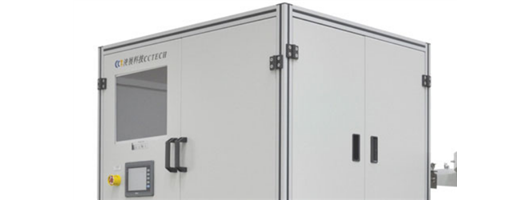
Brochures
Reviews
Trade Associations
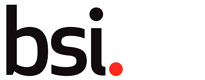
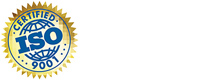