Quick Links:
Products
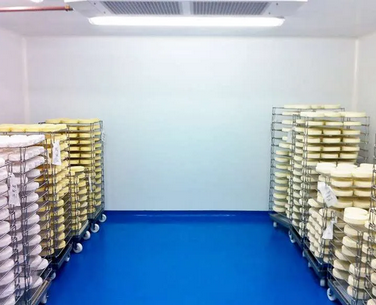
Food Facilities
Thanks to our 75 years of experience in building all kinds of food production factories, we can guarantee you a first-class nationwide installation, from initial enquiry right through to final handover on site, helping you return to production with minimal disruption. We pride ourselves on delivering on time, on budget and safely.
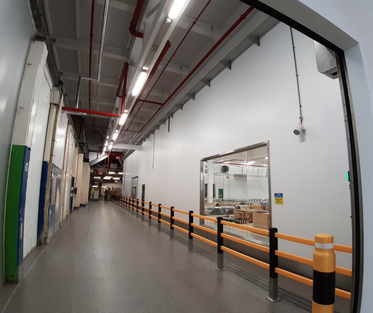
Food Manufacturing Factories
As an independent contractor, Stancold will only use market-leading materials from suppliers that we trust, many of whom we have had a long-standing relationship of over 20 years. We pride ourselves in working with a supply chain that is UK-based and selecting materials, such as Kingspan QuadCore, that will meet your operational specification and budget needs.
Our approachable and trustworthy team include a dedicated project manager for your contract, an experienced installation team and an in-house co-ordination team that will make sure that every element of your food factory build is completed efficiently and to your expectations.
We will work with your architect or design team as well as other appointed contractors to provide a coordinated solution, including refrigeration, racking, wall protection and flooring, while ensuring that your facility is fully operational as soon as possible.
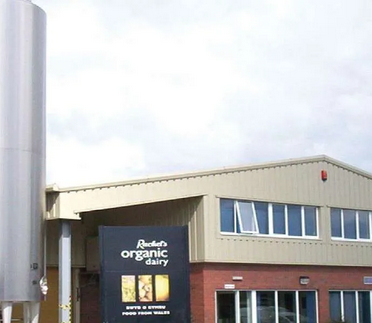
Processing Facilities
We have a strong team with excellent technical design knowledge, where a trustworthy member of our friendly project management team will be your dedicated contact to ensure you are kept up-to-date with progress.
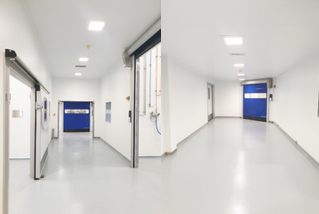
Cleanrooms & Labs
We are the leading go-to specialist subcontractor for walls, ceilings, vision panels and doors for any cleanroom or technology environment, where, for over half a decade, we have gained intimate knowledge from the UK’s leading suppliers of specialist cleanroom systems. Unlike many competitors, we are completely independent to ensure we select the perfect system for your project.
To discuss your upcoming architectural cleanroom envelope construction project, get in touch on 0117 316 7000.
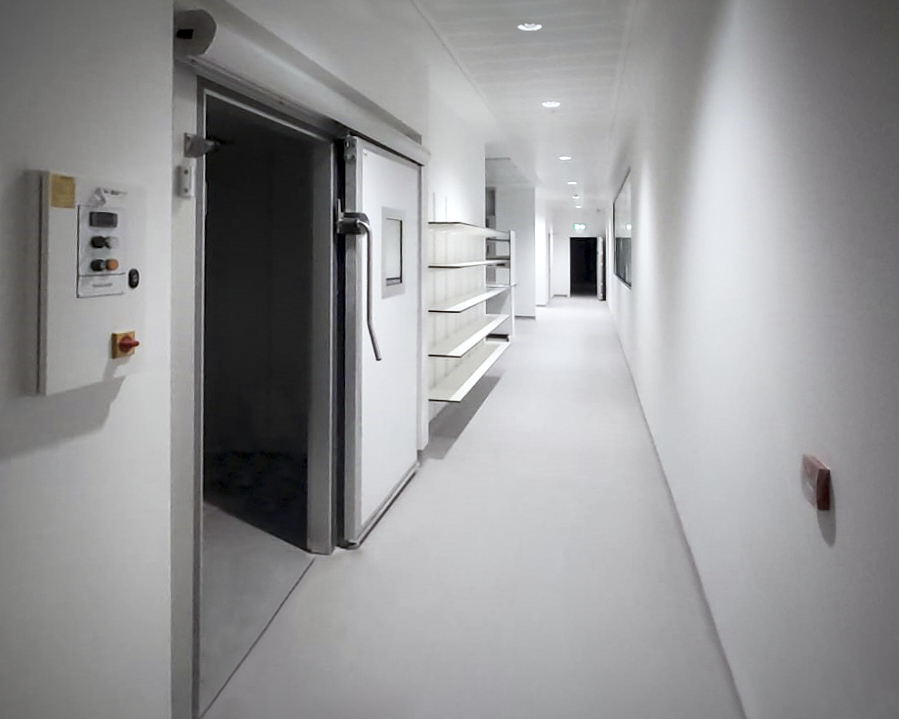
Pharmaceutical Cold Storage
The high-value and critical nature of pharmaceutical products must be maintained when constructing new environments, so we will work closely with you to achieve the required pull-down period or holding temperature relevant to the product. For an N+1 specification, our solutions will integrate a 100% back-up refrigeration system to guarantee product integrity.
Thanks to 75 years of experience in the UK cold chain, CREST can assist with your pharmaceutical chilled storage project right from inception. To discuss your plans in more detail, please get in touch with Mark Kendrick on 07585 301 425 or send us an enquiry.
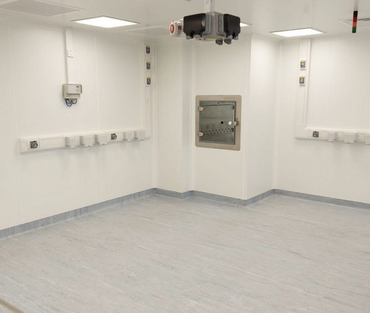
Level 3 Containment Laboratories
A high specification ‘clean’ environment, only the most suitable insulated panel system should be used for Level 3 containment (CL3) laboratories, where CREST’s superior expertise in cleanroom systems ensure that these facilities are built to our client’s exact specification.
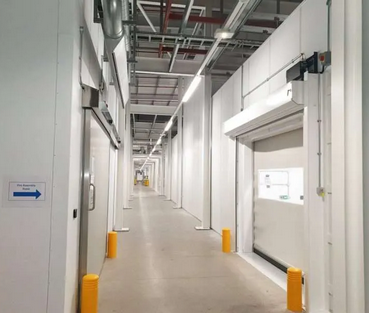
Battery Manufacturing Suites
Anode & cathode mixing and coating
Drying and calendering
Electrolyte filling and sealing
Testing and quality control
Thanks to our multi-discipline history within controlled environments, Stancold’s Clean Room Envelope Specialist Team offer unrivalled expertise and experience when it comes to the construction of demanding installations such as battery manufacturing facilities.
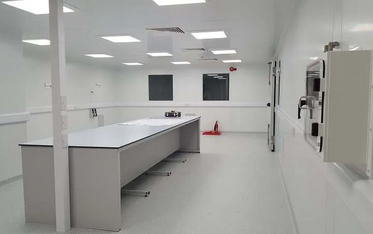
Low Humidity Dry Rooms
Particularly where battery production, assembly and testing are concerned, including that of lithium-ion, their vulnerable properties make them extremely sensitive to moisture, temperature and humidity, making a dry room the ideal environment to maintain such complex standards.
CREST’s unrivalled expertise and experience in composite panel builds for critical environments ensure that we are well-positioned to undertake responsibility for the specification and installation of dry room envelopes across the UK.
We pride ourselves in our pro-active and flexible approach, and the team have developed a specialist detailing solution that passes the rigorous commissioning and testing procedures for this type of cleanroom construction. We will also work collaboratively with your appointed contractors to recommend products and co-ordinate works in line with the construction schedule.
Our portfolio in this area is growing, so whether you require a dry room environment or the internal fit-out of a dedicated battery manufacturing centre, The Clean Room Envelope Specialist Team are on hand to discuss your requirements and how we can assist.
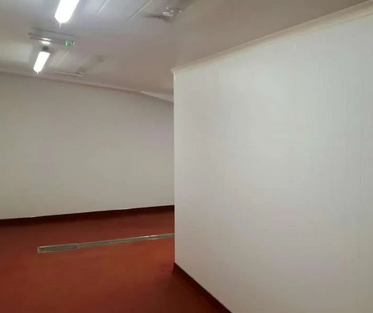
Factory Partitioning
Stancold’s fire-rated composite partitioning systems meet the applicable performance criteria and are highly certified to meet , LPS 1208 and LPS 1181, where we can design and construct a solution to provide complete fire resistance from 30 to 240 minutes.
As leading specialists, Stancold’s team can confidently offer a turnkey package for factory partitioning, including all elements of the wall construction, fire protection including firestopping and/or fireboarding, warranties and third-party fire certification.
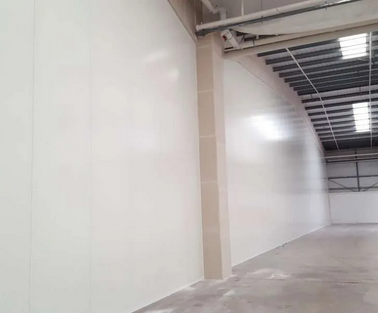
Warehouse & Industrial Partition Walls
Highly certified to meet BS476 part 22, LPS 1208 and LPS 1181, Stancold’s warehouse and industrial dividing walls allow you to manage your work environment in multiple ways, from creating storage enclosures through to office spaces. They provide 30 to 240 minutes of complete fire resistance and can be adapted to suit specific building regulations, as approved by the Loss Prevention Certification Board (LPCB).
We are one of a few installers in the UK holding the LPS 1500 certification from LPCB (Loss Prevention Certification Board) to install LPS 1208 approved fire-resisting compartmentation systems.
About us
Since 1946, we have created temperature controlled, hygienic, and fire-resistant environments. We are ISO 9001 certified and members of the International Association of Cold Storage Contractors.
Among Stancold's services are the design and installation of hygienic and fire-rated areas such as cold storage, cleanrooms, laboratories, industrial firewall partitions, and food production facilities.
Our Products & Services Include:
- Food Facilities
- Food-Safe & Pharmaceutical Coldrooms
- Cleanrooms & Labs
- Battery Manufacturing Facilities
- Firewalls & Industrial Partitions
Over the past 70 years, we have provided custom-fitted solutions for a wide range of industries, including food and drink, medicine & pharmaceuticals, warehousing & distribution, and information & communication. We have designed and built chilled loading bays, pharmaceutical storage facilities, fish processing plants, and warehouse walls.
Due to the fact that every project is bespoke, we conduct full site surveys and produce drawings for our clients as well as assign dedicated project managers who oversee the entire installation process. It is possible for us to be on site in as little as 3 weeks and to install over 500m2 of panelling per week, which ensures that deadlines are met.
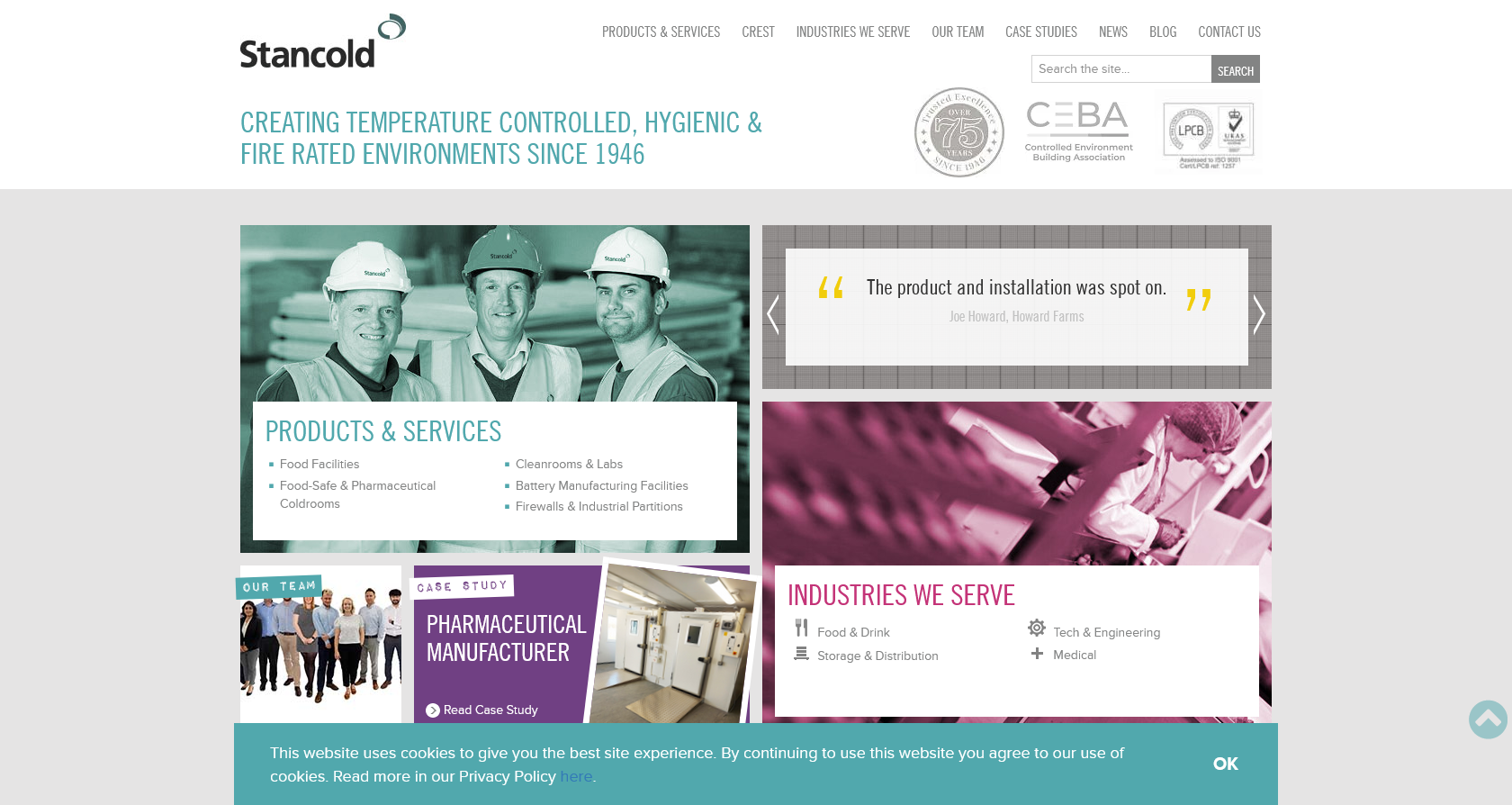