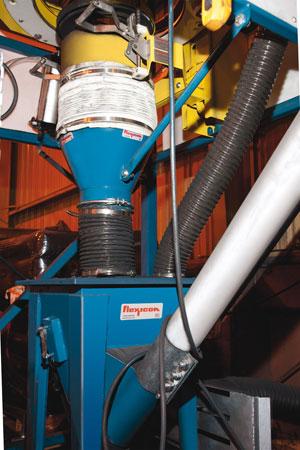
11 October 2012 | Flexicon Europe Ltd
Bulk Bag handling system cuts Carbon Black inventory and keeps compounding line clean
Elastomer manufacturer Kirkhill -TA Co has slashed inventories of carbon black and improved plant cleanliness, replacing a large silo storage system with a Flexicon bulk bag discharging system.
It has enabled the company to cut inventory by 90 percent, while preventing carbon black dust from contaminating the plant environment. The overall outcome has been very significant cost savings, greater production efficiency and improved competitiveness.The bulk handling system is the latest upgrade for this company that began making gaskets, seals and other elastomeric products in 1919, and gradually shifted production from general industrial products to highly engineered silicone parts for commercial and military aircraft, missiles and even the Space Shuttle.
“During the mass production era railcars delivered 136 tonnes of carbon black pellets at a time,” said Larry Pierce, Vice President of Technology at Esterline Technologies, Kirkhill’s parent company. “We only received shipments a few times per year and were tying up close to $250,000 in inventory with each shipment.” Product diversification resulted in lower volume production which made it unnecessary and costly to maintain large quantities of carbon black in silos.
The move to using Flexicon bulk bags and discharge system has also enabled Kirkhill -TA to comply with Esterline Technologies’s wish of placing a premium on controlling inventory costs, reducing inventory by a factor of 10. The bulk off-loading system improves efficiency and competitiveness and brings our costs in line.”
Bulk Handling Priorities
Kirkhill -TA had several priorities for its new materials handling system. With its parent company, Esterline Technologies putting a premium on controlling inventory costs, the company had to improve inventory efficiency, keeping costs in line. It needed to use as much of the existing infrastructure as possible. Finally, it had to prevent carbon black dust, caused by the friable pellets rubbing against one another, from escaping into the plant or processing equipment.
Carbon black is one of Kirkhill -TA’s main processing materials. Adding carbon black to an elastomer reduces its rate of thermal expansion, thereby enabling it to maintain an airtight seal in high temperature applications. It can also modify elongation, rigidity and other physical properties, and impart conductivity to prevent static discharge. Carbon black is produced by burning heavy oil or tar to form soot-like particles. When airborne, they can penetrate operating equipment. “Carbon black tends to soak up lube oil,” Pierce said. “If it gets into the bearings and rollers, they will wear out prematurely.” It can also cause short circuits.
Carbon black is a petroleum product therefore California classifies it as a hazardous material. Since it is shipped as 1-3 mm diameter pellets, to reduce the likelihood of airborne release, manufacturers must remain vigilant to prevent spills and the cleanup that would follow.
Railcar System Handled Bulk Deliveries
Kirkhill-TA had a significant infrastructure to handle carbon black, with a rail offloading station incorporating screw conveyors, bucket conveyors and two large storage silos.
Carbon black pellets flowed from the silos to the company’s Banbury mixers two ways: by pneumatic conveyor and when weight in the silo fell below 22,675 kg by large steel totes that hold approximately 900 kg of carbon black. These are moved by forklift, the carbon black gravity fed into a weighing container, with an integrated weigh scale, on a mezzanine above the mixers. When the container and pellets reach the required weight, the container’s chute opens, discharging material into the mixer for compounding with elastomers prior to molding into finished seals.
Since material delivery to the site by rail is no longer possible, coupled with lower volume requirement, there was no longer need for silo storage and associated pneumatic conveyors but the steel totes and weighing system remain as part of the new bulk handling installation.
During this shift in production requirements the city of Brea where Kirkhill-TA is located decided to tear up the railroad tracks that supplied the plant to expand its park space. “We were the only industrial facility left in the city, and agreed to it," says Pierce." In return, the city gave us a loan to buy the new bulk off-loading system.”
New Bulk Bags Simplify Handling
Bulk bags were a clear choice for receiving carbon black. First, they are available in 450 and 900 kg sizes, large enough to receive bulk discounts. While vendors charged less for bulk railcar shipments, the savings were largely offset by higher rail transportation costs. By switching, Kirkhill-TA would pay only a fraction of a cent per kilo more for bulk bag deliveries. Add in the savings from the actual lower inventories and elimination of silo maintenance, the bulk bag system pays for itself.
The bulk bag discharger also improves site cleanliness since it moves bulk material handling operations inside the facility, so any accidental leaks are contained within the plant. The discharger also uses dust-tight connections to fully contain carbon black until final addition to the mixer.
Trucks deliver 10 to 12 palletized bulk bags at a time. A forklift raises each bag by its straps and delivers it to a storage site on the mezzanine. When carbon black is needed, the forklift operator attaches the bag straps to a detachable bag lifting frame and then lifts the frame into the cradle on the bulk bag discharger.
The Flexicon discharger unloads carbon black pellets from the bulk bag into a purpose-built hopper, from which a 4.5m long model 14.5 flexible screw conveyor transfers the material to a steel tote. At this point the operation proceeds as it did originally using the steel totes. A forklift transports the tote along the mezzanine to the container above one of the mixers, where it releases its load.
Air-tight System Yields Cleaner Plant
The Flexicon bulk bag discharger is engineered to fully contain the material being unloaded, preventing contamination of the product and plant environment. The bag spout is attached to a Spout-Lock® clamp ring, which forms a sealed connection between the clean side of the bag spout and clean side of a Tele-Tube® telescoping tube (through which the material is discharged). The tube pneumatically raises the clamp ring, allowing the operator to make a dust-tight connection with the bag spout. The tube then lowers, elongating the bag to fully discharge the pellets. Also promoting full discharge, Flow-Flexer® bag activators -- two plates located under the bag -- raise and lower opposite bottom edges into a ‘V’ shape, directing material toward the bag spout.
Above the clamp ring, a Power-Cincher® flow-control valve encircles the upper portion of the bag spout to allow retying of partially empty bags. When the bag is empty, the operator actuates the Bag-Vac® dust collector, which generates vacuum within the sealed system, collapsing the empty bag dust-free for retying and removal.
The conveyor incorporates a flexible stainless steel screw with specialised geometry to minimize compression of materials like carbon black that tend to compress in conventional conveyors. As the screw rotates, it self-centres within the plastic tube, providing clearance between the screw and tube wall, allowing sufficient space for pellets to flow without damage.
The intake end of the conveyor attaches to the outlet of the hopper. At the discharge end, a 5 hp (4 kW) motor drives the screw as the material passes from the conveyor outlet, through a 6 in. (15.2 cm) diameter flexible downspout into the steel tote. Being fully enclosed, the conveyor further assures plant cleanliness. A batch timing control activates the conveyor for a repeatable time interval to fill the tote.
Whether there is a requirement for a totally new bulk handling configuration or one that needs to adjunct to an existing plant, as in the case of the Kirkhill -TA site in Brea, Flexicon has the engineering expertise and products to undertake such projects, with system capabilities for carefully handling powders, granules, etc.