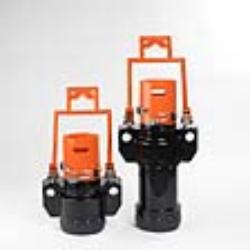
11 June 2008 | Norbar Torque Tools Ltd
High accuracy torque multiplier for wet valve application
Norbar Torque tools has developed an innovative torque multiplier for the subsea tools market.
Designed as an adapter to allow API 17D Class 4 intervention torque tools to generate the torque required to handle Class 7 applications, the new torque multiplier delivers a higher level of accuracy than alternative solutions, and increased flexibility in use through its added-value features and its ability to be configured in two standard lengths.
The gear unit has been designed as an adapter for torque tools used on subsea Christmas trees – the assemblies of control valves, gauges and chokes that control oil and gas flow at a well head. Installed on the ocean floor at depths of up to 3000m, these ‘wet trees’ provide the ultimate challenge for the torque tools designed to actuate the various valves.
The valves come in various sizes with different torque requirements, with the typically used subsea products ranging from Class 1 valves with maximum torques of 68Nm up to Class 7 with torques of 34,000Nm. Clearly it would be impractical to hold different tools for each valve, or to standardise only on the largest tool on the off-chance of having to accommodate a Class 7 valve now and again. So the gear adapter has become popular as a means of extending a Class 4 tool (which would generate up to 2,700Nm of torque) up to Class 7.
To date, the trade-off for this added convenience has been accuracy, with extended Class 4 tools failing to offer the precise torques of dedicated Class 7 tools. But Norbar’s innovative design has overcome this problem, enabling a Class 7 torque output to be generated from a Class 4 torque input to an accuracy of better than ±5%.
“Our Norwegian customer came to us to see if we thought we could improve on the existing designs,” says Norbar’s Tim Bloor. “We looked at the problems with the existing products, and went back to basics. The result was two prototype units that we believe deliver far greater accuracy than the current gear adapters on the market.”
The function of the gear is to operate as a torque multiplier, but the ratios have to be exactly right to achieve the correct torque and the specified speed from the Class 4 tool. At the same time, the gear has to be able to function reliably in a subsea environment at extreme temperatures and pressures. It also has to be easy to handle. Norbar was able to meet all of these requirements.
The design of the gear to match the accuracy requirements was no trivial matter. Inherent gearbox inefficiencies mean that the number of turns that the input has to make to achieve one revolution of the output is not the same as the torque multiplication ratio. A key aspect of the design, then, was to engineer each gear stage to give an exact velocity ratio which would deliver the required torque multiplication at an accuracy of better than ±5%.
The company’s newly developed torque multiplier is designed to withstand the corrosive environment and is pressure compensated to allow operation at typical subsea pressures. It is designed to be suitable for use with the standard Class 4 torque tools that, operated by ROVs, are used to remotely actuate the wet valves. There is also a restriction on the weight that ROVs can manipulate so considerable design work has gone in to keeping the tool weight down to an acceptable level.
The design recognises that there are two standard tool lengths in general use, with different companies preferring either one or the other. With the Norbar design, the nominal length can be quickly changed from short to long by adding or removing an adjustment shaft under the adapter sleeve. The result is a tool that is highly versatile.
As well as the improved accuracy and length options, the multiplier builds in a host of special features that will make it even more attractive in the subsea torque tools market. These include a lifting handle that has been developed from the ground up to make the tool as easy as possible to manoeuvre. Attention to detail is also demonstrated in the fact that the tool is coloured orange – the last colour to fade at increasing depths of water.
The new torque multiplier is currently under test with Norbar’s Norwegian customer serving the North Sea Oil market, but the expectation is that the product will prove an ideal solution in this demanding application. “It’s been a significant investment on our part, but if we get it right then the market potential is huge,” says Bloor. “It seems to have been favourably accepted, and we’re confident that the extensive testing it is currently undergoing will prove our design.”
Norbar will then be able to offer a standard, high accuracy solution to the various subsea valve tool manufacturers worldwide, enabling those companies in turn to offer tools of significantly superior performance and accuracy to the multitude of oil and gas companies across the globe with subsea operations.