Spiroflow and the 'Dream Machine.'
18 August 2008
A ‘Spiroflow’ Big Bag Discharger is a key component in a system that packs deliquescent material into pouches that absorb moisture and prevent deterioration of America’s ‘dream machine’ motorcycles.
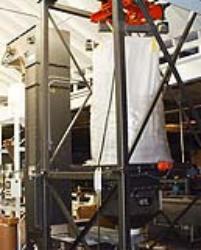
For overseas shipments to Europe, Asia, Africa, Australia and other parts of the world, the American motorcycle is strapped to an aluminium pallet, poly-bagged and cartoned for shipment that, at times, takes up to eight weeks and sometimes even longer.
Before the solution was developed by Spiroflow in collaboration with other top manufacturers and developers, moisture in the air caused rust spots, mildew or mold to form on the motorcycles which resulted in many hours of repair work by the receiving dealership, before delivery to the customer.
To solve the problem, the motorcycle manufacturer approached a custom designer and manufacturer of moisture absorbing pouches. These pouches contain a granular mineral clay (Montmorillonite Clay Mineral). Located in the Eastern United States, this manufacturer provides moisture-absorbing solutions for keeping compressed air, hydraulic oil and shipment spaces moisture free.
The mineral clay is delivered in 1,000kg Big Bags and has to be repackaged in 1.5kg and 2kg pouches. To accomplish this, the ‘East Coast manufacturer’ contacted Gough Econ, Inc. of Charlotte, North Carolina a specialist supplier of bucket elevators, belt conveyors and vibratory feeders. Charlotte, North Carolina is also home of Spiroflow Systems Inc, the US operation of Spiroflow Ltd of Clitheroe, Lancs.
Gough and Spiroflow have co-operated on projects before.
The challenge was to design and install a material handling system that is extremely gentle that can handle the very fragile granular mineral clay and deliver it to a special pouch making machine, developed by the East Coast manufacturer, and to install it into a confined space within their factory.
The system began operating in August 2007. The pouch manufacturer confirms that the Big Bag Discharger and the transfer system operate flawlessly. The motorcycle manufacturer is also very pleased with the end product since very little moisture now forms during shipment and the motorcycles arrive at their overseas destinations in excellent condition thus, eliminating the headaches and making big savings in repair costs.
The system began operating in August 2007. The pouch manufacturer confirms that the Big Bag Discharger and the transfer system operate flawlessly. The motorcycle manufacturer is also very pleased with the end product since very little moisture now forms during shipment and the motorcycles arrive at their overseas destinations in excellent condition thus, eliminating the headaches and making big savings in repair costs.
To cater for the 1,000kg big bags and to assure a gentle material handling system for “kid glove” care of the mineral clay, the system includes a fully self-contained ‘Spiroflow’ Big Bag Discharger, a vibrating tray feeder and a Gough “Z” Shaped Swinglink® bucket elevator. The ‘Spiroflow’ Big Bag Discharger has an integral hoist.
This means that the pallet mounted 1,000kg bags can be brought to the discharger on a pallet truck and there is no need for a forklift truck to lift the bag into position. A sole operator lifts the bags into the discharger using a bag rigging frame, onto which the loops of the bag are properly secured. This frame is then raised by the hoist. The hoist runs along a fully-load tested integral “I” lifting beam enabling the raised bag to be traversed into position above the collection hopper. The collection hopper has an interlocked access door with viewing port to assure dust tight operation. The door is amply sized to enable the operator to untie and retie the bag sprout and liner as needed.
The discharger is furnished with unique bag tensioning supports that compensate for the weight of the bag. As the bag empties, it is stretched to ensure total and gentle discharge of the granules into the collection hopper.
The bag support dish around the top of the collection hopper houses massagers. These are operated manually in the event of material, that has become compacted during transportation or storage, being unwilling to discharge from the bag.
The bag support dish around the top of the collection hopper houses massagers. These are operated manually in the event of material, that has become compacted during transportation or storage, being unwilling to discharge from the bag.
The ‘Spiroflow’ Big Bag Discharger connects to an enclosed, electromagnetic, 1.3 metre long, vibratory metering feeder. From the conveyor, the granules are discharged on to a Gough Econ “S” Series Swinglink® bucket elevator. The buckets also overlapped to ensure there is no product spillage. The smooth bucket surface also eliminates any product trap areas. The Swinglink® system discharges the clay granules through a hopper to the especially designed polyester pouch making machine developed by the East Coast manufacturer.
Other Press Releases By This Company
- 14/10/2015 - Spiroflow's conveying solutions go on the road to Dubai
- 08/09/2015 - Spiroflow Will Unveil New Flexible Conveying System At Ppma - Ppma, Nec Birmingham, September 29-october 1, Stand G36
- 07/07/2015 - Spiroflow acquires food control solutions
- 12/02/2015 - New Technology Centre brings superior testing to spiroflow
- 03/10/2014 - Spiroflow's Robust Handling Equipment Built to Survive Stormy Seas
- 30/09/2014 - Spiroflow Takes New Angle with Equipment to Tackle Dust
- 30/09/2014 - Spiroflow Unveils New Bin Activator for Difficult Materials
- 30/09/2014 - Spiroflow Targets UK Ingredients Sector with New CTE Bulk Bag Filler
- 30/09/2014 - Safe Handling of Biomass Materials with Spiroflow
- 09/01/2013 - Spiroflow conveyors – fit as a Butcher’s dog!
- 03/07/2012 - Preview of Spiroflow Ltd’s participation in the PPMA 2012 Exhibition at the NEC, Birmingham, UK, September 25-27, 2012.
- 13/06/2012 - ‘Spiroflow’ Aero-Mechanical Conveyors – sweet success in Africa!
- 23/02/2012 - ‘Spiroflow’ Bulk Bag Filler – helping to make money from waste.
- 02/11/2011 - NEW Tilting Mobile Flexible Screw Conveyor from Spiroflow
- 12/07/2011 - Spiroflow Powder Handling & Processing Systems – Stand G16
- 29/03/2011 - New ‘Rise and Fall’ Bulk Bag Filler from Spiroflow
- 14/02/2011 - Sometimes life has to be a Drag!
- 18/12/2010 - Spiroflow joins the club at Liverpool biscuit factory
- 22/07/2010 - Bag to the future!
- 22/07/2010 - Spiroflow Ltd in joint venture with Horizon Systems Inc.
- 16/06/2010 - Spiroflow acquires Dynamet Inc.
- 16/03/2010 - United Utilities treats water to PAC Dosing System
- 17/02/2010 - Aero Mechanical Conveyor does sterling job for US coffee blender
- 02/02/2010 - Spiroflow dip dabs Tangerine Confectionery
- 27/01/2010 - Spiroflow helps recycle sulphur on Alaskas' north slope oil refinery
- 21/01/2010 - Aero-Mechanical Conveyors keep Tin Oxide moving
- 22/07/2009 - Aero-Mechanical Conveyor is no Red Herring in Orkney
- 14/05/2009 - Spiroflow Aero-Mechanical Conveyor spicing it up for Pataks
- 05/12/2008 - Highest accuracy ‘Spirofil’ Big Bag Filler to Date
- 11/11/2008 - ‘Spiroflow’ Bulk Handling Equipment at Dekura
- 09/07/2008 - Spiroflow Supply Tetley Tea with Big Bag Discharging Solution
- 30/11/2007 - ‘Spiroflow’ Bulk Bag Filling Machine at PET Processors (UK) L.L.C
- 30/11/2007 - ‘Spiroflow’ Big Bag Discharger – a gem of a job!
- 26/11/2007 - Nothing fishy about this discharger!
- 26/11/2007 - Spiroflow system transforms output
- 23/11/2007 - A ‘Spiroflow’ Bulk Bag Discharger and Flexible Screw Conveyor
- 23/11/2007 - Spiroflow on the road to success
- 22/11/2007 - Spiroflow conveyor gives more grist to the mill!
- 22/11/2007 - Weigh, weigh the best - time and time again!
- 22/11/2007 - ‘Spiroflow’ conveyors – to cap it all!
- 22/11/2007 - Spiroflow’ Flexible Screw Conveyors – BALly good job!