Spiroflow conveyor gives more grist to the mill!
22 November 2007
An Aero-Mechanical Conveyor supplied by Spiroflow Ltd
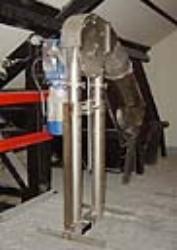
An Aero-Mechanical Conveyor supplied by Spiroflow Ltd has proved its worth for T & R Theakston Ltd, brewers since 1827. It was a supplier’s switch from 50 kg to 25 kg sacks that brought matters to a head for the family owned brewery.
Theakstons brew a range of quality beers of which their ‘Old Peculier’ is legendary! Although committed to upholding their traditional brewing methods, in a brewery building which is 136 years old: to meet ever increasing demand, Theaksons recognised that operational improvements would have to be made to those areas, such as materials handling, which would have no effect whatsoever on the quality of their beers.
Until early 2000, malt was delivered direct to the brew house door in 50 kg sacks. Every week 280 sacks were manually unloaded one at time and transported in a wheeled barrow to a storage area around a hoist. The manual hoist, which took two men to operate, was used to transfer enough of the sacks to a third floor in the roof space where they were stored ready to be opened and discharged into the grist mill – the start of the brewing process.
During 2001 the malt supplier switched all deliveries to 25 kg sacks meaning that each week 560 had to be manually hoisted in to the roof space! Given the time it took to unload each sack, barrow it to the hoist area and to hoist it up ready for use, the operation was effectively taking a full man week in its own right to meet the requirements of three brews a day on each of three days a week. In addition, the unloading process tied the delivery truck up for a whole morning!
Today, 25kg sacks of malt are delivered on one tonne pallets, unloaded by fork lift truck in less than half an hour and stored in a new warehouse area across the yard from the brew house. They are taken to what was the hoist area by electric pallet truck as required prior to each brewing.
The ‘Spiroflow’ Aero-Mechanical Conveyor, with its integral sack tip hopper, has replaced the hoist. Now sacks can be emptied at ground floor level at a rate commensurate with the performance of the grist mill. A high level alarm in the buffer hopper above the mill warns the operator if he is emptying sacks more quickly than the mill can accommodate. As head brewer, Bill Wilson, comments, “We prefer to use sacks as, that way, it is easy to control the weight of ingredients for each brew. One of the many things we like about the ‘Spiroflow’ Aero-Mechanical Conveyor is that what’s put in at the bottom, comes out at the top. There is no loss in the conveyor – essential to ensure each brew has the correct amount of each ingredient”.
The Aero-Mechanical Conveyor was installed by Theakstons’ own engineers in September 2001. This was no mean feat given the limited space available, the number of floors involved and the grist mill drive through which the conveyor had to pass! The completed installation was commissioned with the assistance of an engineer from Spiroflow. The malt required for each of the nine weekly brews is now taken to the top floor and charged in to the grist mill buffer hopper in around an hour a time. Bill Wilson reports that the only maintenance on the Aero-Mechanical Conveyor has been an annual check on the rope tension. Other than that he confirms that the conveyor and the service provided by Spiroflow are, “As good as it gets”.
Why an Aero-Mechanical Conveyor? Bill Wilson did his homework and had concluded that it was the cost effective solution compared to pneumatic conveying. This is because it achieves the same result at a lower capital cost. And, as there is no net displacement of air, the Aero-Mechanical Conveyor does not require any venting or filtration equipment. The conveyor, which has 80 mm diameter conveying tubes is 9 metres long, operates vertically with the drive motor at the top. It offers ample scope for a significant increase in capacity when the time comes. And when asked why he chose an Aero-Mechanical Conveyor from Spiroflow, Bill Wilson adds, “Because Spiroflow’s response was the best. In addition, we were able to take a sample of product to their test facility and prove first hand that they could achieve what we wanted”.
The Theakston brewery and its associated visitor centre are located in Masham (pronounced Massam) a very picturesque village on the River Ure in Wensleydale, North Yorkshire. From there, Theaston’s beers are not only distributed nationwide, they have a lucrative export trade too.
More information about T & R Theakston Ltd can be found at www.theaksons.co.uk.
Their products can be sampled at a pub near you!
To learn more about ‘Spiroflow’ Aero-Mechanical Conveyors, Flexible Screw Conveyors and their ranges of Big Bag Dischargers and Fillers, visit their web site at www.spiroflow.com or call them on +44 (0)1200 422525 to discuss your specific requirements.
Other Press Releases By This Company
- 14/10/2015 - Spiroflow's conveying solutions go on the road to Dubai
- 08/09/2015 - Spiroflow Will Unveil New Flexible Conveying System At Ppma - Ppma, Nec Birmingham, September 29-october 1, Stand G36
- 07/07/2015 - Spiroflow acquires food control solutions
- 12/02/2015 - New Technology Centre brings superior testing to spiroflow
- 03/10/2014 - Spiroflow's Robust Handling Equipment Built to Survive Stormy Seas
- 30/09/2014 - Spiroflow Takes New Angle with Equipment to Tackle Dust
- 30/09/2014 - Spiroflow Unveils New Bin Activator for Difficult Materials
- 30/09/2014 - Spiroflow Targets UK Ingredients Sector with New CTE Bulk Bag Filler
- 30/09/2014 - Safe Handling of Biomass Materials with Spiroflow
- 09/01/2013 - Spiroflow conveyors – fit as a Butcher’s dog!
- 03/07/2012 - Preview of Spiroflow Ltd’s participation in the PPMA 2012 Exhibition at the NEC, Birmingham, UK, September 25-27, 2012.
- 13/06/2012 - ‘Spiroflow’ Aero-Mechanical Conveyors – sweet success in Africa!
- 23/02/2012 - ‘Spiroflow’ Bulk Bag Filler – helping to make money from waste.
- 02/11/2011 - NEW Tilting Mobile Flexible Screw Conveyor from Spiroflow
- 12/07/2011 - Spiroflow Powder Handling & Processing Systems – Stand G16
- 29/03/2011 - New ‘Rise and Fall’ Bulk Bag Filler from Spiroflow
- 14/02/2011 - Sometimes life has to be a Drag!
- 18/12/2010 - Spiroflow joins the club at Liverpool biscuit factory
- 22/07/2010 - Bag to the future!
- 22/07/2010 - Spiroflow Ltd in joint venture with Horizon Systems Inc.
- 16/06/2010 - Spiroflow acquires Dynamet Inc.
- 16/03/2010 - United Utilities treats water to PAC Dosing System
- 17/02/2010 - Aero Mechanical Conveyor does sterling job for US coffee blender
- 02/02/2010 - Spiroflow dip dabs Tangerine Confectionery
- 27/01/2010 - Spiroflow helps recycle sulphur on Alaskas' north slope oil refinery
- 21/01/2010 - Aero-Mechanical Conveyors keep Tin Oxide moving
- 22/07/2009 - Aero-Mechanical Conveyor is no Red Herring in Orkney
- 14/05/2009 - Spiroflow Aero-Mechanical Conveyor spicing it up for Pataks
- 05/12/2008 - Highest accuracy ‘Spirofil’ Big Bag Filler to Date
- 11/11/2008 - ‘Spiroflow’ Bulk Handling Equipment at Dekura
- 18/08/2008 - Spiroflow and the 'Dream Machine.'
- 09/07/2008 - Spiroflow Supply Tetley Tea with Big Bag Discharging Solution
- 30/11/2007 - ‘Spiroflow’ Bulk Bag Filling Machine at PET Processors (UK) L.L.C
- 30/11/2007 - ‘Spiroflow’ Big Bag Discharger – a gem of a job!
- 26/11/2007 - Nothing fishy about this discharger!
- 26/11/2007 - Spiroflow system transforms output
- 23/11/2007 - A ‘Spiroflow’ Bulk Bag Discharger and Flexible Screw Conveyor
- 23/11/2007 - Spiroflow on the road to success
- 22/11/2007 - Weigh, weigh the best - time and time again!
- 22/11/2007 - ‘Spiroflow’ conveyors – to cap it all!
- 22/11/2007 - Spiroflow’ Flexible Screw Conveyors – BALly good job!