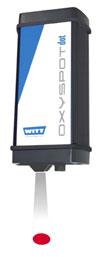
16 April 2015 | Witt Gas Techniques Ltd
Optical measurement of oxygen in packaging
Oxygen analysis with "Oxyspot"
Determining the oxygen content in packaging quickly and precisely merely using light? − the new product series "Oxyspot" from Witt makes this possible. Using a special optical sensor, the German gas technology specialist is offering a modern and powerful alternative for the quality control of oxygen-sensitive products. Depending on the application, Oxyspot is available in three versions: dot, needle and line."Oxyspot" is equipped with a new type of optical sensor, which measures the concentration of oxygen in rigid or flexible packaging. "The measurement is extremely precise and fast", states Alexander Kampschulte, Head of Marketing at Witt. The manufacturer is offering an accuracy of +/- 1 percent in the measurement range 0 to 5 percent oxygen or +/- 2 percent in the measurement range 5 to 25 percent.
MEASUREMENT PRINCIPLE: OPTICS
The measurement is effected using the principle of optical fluorescence, and basically comprises three components: an LED, a dye carrier (dot) and a photodiode. The dot is stimulated by the LED. The colour layer absorbs the light energy and emits this again with a time lag. The photodiode determines the oxygen concentration from the emitted light energy. "Depending on the oxygen content, more or less light is reflected back. The more oxygen molecules, the lower the return beam energy", explains Kampschulte.
THREE TYPES TO CHOOSE FROM
Three Oxyspot versions are available and cover a broad application field: From non-destructive analysis for long-term observation, random sample analysis of small-volume packaging through to continuous in-line monitoring of packing processes.
In the "Oxyspot dot" version, the measurement does not involve any contact and is hence non-destructive. The small dye carrier is bonded in the packaging, but can also be integrated as a fixed component. As gas is not consumed, this type of device is perfectly suitable for long term observations and shelf-life trials. If the device is installed permanently on the packing line, automatic residual oxygen testing of the entire production is also possible.
ALSO WITH MINIMAL GAS VOLUME
For the random sampling of products with very irregular or light-impermeable surfaces, Witt has developed the variant "Oxyspot needle". All of the key components are focused here in a fine needle that is introduced into the product. The determined values are sent to the device via a glass fibre cable. The analysis is carried out directly at the measurement site. There is no need to take a gas sample. Alexander Kampschulte: "Even the smallest packaging with minimal gas volume, such as coffee capsules or blister packages and vials in the pharmaceutical industry can now be tested."
MOBILE AND IN-LINE
Oxyspot is controlled via a conventional PC using a USB cable. Special software allows automatic reporting and evaluation of measuring data. Measurements can be visualised graphically in the real time exported for processing with MS Excel and for archiving. That means all measurements effected for quality assurance can be validated at any time. On request, Oxyspot can also be operated with a tablet PC via Bluetooth, for example in mobile applications.
"Oxyspot line" is available for the in-line testing of tubular bags: the measuring system is integrated into the packing machine via a lance plus glass fibre cable. The oxygen content can be monitored automatically during the packing process. Here too, no gas is consumed for analysis.
The new analyser is supplied together with software and USB cable in a practical case. The Oxyspot dot version comes with a high-quality table stand made from stainless steel.
With the new device series, Witt is extending its broad range of analysis systems for quality control. For more information, please visit www.wittgas.com.