Space saving bearing for compact machine tool
31 March 2009
Deliberately restricting the size of component that its VECTOR machine handles was a shrewd move for Colchester-based Curtis Machine Tools.
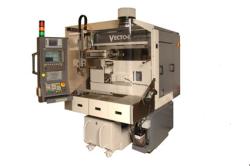
It has effectively cornered the market in small parts grinding by creating a highly efficient and compact machine, with short distances between grinding and loading, to cut cycle times. In particular, the VECTOR machine is now seen as an automotive industry standard but it is also being used for applications such as cutting parts of power tools.
Now with even greater focus on minimising unit costs Curtis has introduced a variant to its highly successful VECTOR series. For very high volume production the VECTOR can be specified with a twin spindle workhead which allows concurrent loading and grinding. It also makes a range of other applications available including in-cycle gauging.
At the end of the grinding cycle the workhead drum rotates through 180° alternating the positions of the two spindles. Critical elements of this mechanism are KAYDON® thin section bearings. “We needed a precise, low friction bearing that occupied minimum space but was still stiff,” explained Chairman Rick Curtis. “The KAYDON® bearing was ideal and gives us accuracy better than 1 micron.”
A wire race bearing was considered but although it satisfied the low weight need and was attractively priced the running accuracy was not adequate. This is a very important factor as final component accuracy and the consistent quality of a batch of components is determined by the consistent positioning accuracy of the workhead.
Ultimately Curtis Machine Tools designers Roger Marriott and Sarah Allard chose a precision class 3 KAYDON® four-point contact bearing and a radial contact bearing for this application. This is a classic combination selected by designers seeking dependable performance. Pre-load on the bearings is factory-set, minimising assembly time and assuring its consistency.
The KAYDON® four-point contact bearing can accept a combination of radial, thrust and moment loads. This is thanks to the unusual geometry of the ball grooves that creates a ‘gothic arch’ configuration making it possible for two grooves to contact the ball at four points.
High thrust and moment capacity is obtained in a four-point contact ball bearing by its deep raceway grooves. These allow high initial contact angles between the balls and raceways and increase the thrust and moment capacity. The deep grooves also accommodate the contact angle increase which results from ring stretch and ball deflection under load.
The company who Curtis Machine Tools turned to who provided the best bearing solution was R.A. Rodriguez. Factory representatives for KAYDON® Corporation for more than forty years, this Letchworth based supplier of precision engineering components has extensive applications knowledge. Rick Curtis concluded, “R. A. Rodriguez fully understood what we needed to achieve and have supplied a quality product that is working well in the field.”
Other Press Releases By This Company
- 26/01/2010 - Rodriguez appoints military & aerospace specialist
- 17/12/2009 - All Slewing Ring Bearings great and small
- 01/12/2009 - Robot helps glass maker to keep prices keen
- 30/10/2009 - Rodriguez introduces new gear products
- 22/10/2009 - Economical, flexible robot found after ten year search
- 07/10/2009 - Compact Slide System delivers long term reliability for PCS
- 13/08/2009 - EasyLINE Linear Motion package for clean room applications
- 04/08/2009 - Linear actuation for Turbo Compressors
- 24/07/2009 - Component Palletisers demonstrate IEF Werners' expertise
- 09/07/2009 - New compact geared motor with double brake from RA Rodriguez
- 22/06/2009 - RA Rodriguez takes a stand at DESi 2009
- 21/05/2009 - New catalogue details expanded range from RA Rodriguez
- 21/05/2009 - Smaller Module Gears from RA Rodriguez
- 27/04/2009 - Power Transmission takes the stage
- 09/04/2009 - Simple, flexible and highly economical Robotic Arm
- 26/02/2009 - New motor driven linear Actuator from RA Rodriguez
- 05/02/2009 - Slewing ring and turntable bearing catalogue boasts enhanced KAYDON® product range
- 07/02/2008 - MACHINE BUILDING 2008, 13th and 14th February, NEC
- 05/02/2008 - HIGH PRECISION SPIRAL BEVEL GEARS
- 05/02/2008 - COMPACT GEARED MOTOR ROTARY ACTUATORS
- 05/02/2008 - EASY-FIT COMPACT LINEAR GUIDEWAY
- 05/02/2008 - COMPACT AND MODULAR LINEAR ACTUATOR