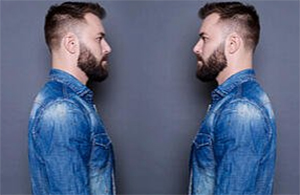
05 March 2020 | ESCATEC Mechatronics Ltd
How can digital twinning benefit electronics manufacturing?
As electronic devices get ever more complex and data-driven, the worlds of manufacturing, IoT, artificial intelligence and data analytics are becoming increasingly interconnected.
The leading-edge technology of digital twinning is just one example of how electronics manufacturers are using real-time data analytics to visualise, understand and improve upon their manufacturing processes.
In this blog post we explore the origins and development of digital twinning, and its range of potential applications within electronics manufacturing.
What is digital twinning?
A digital twin is essentially a computer programme that collects and interprets real-world information about a physical item, system or process and then uses that data to create a simulation of how a product is likely to behave in a real life environment.
The value of digital twinning is that it can be used throughout a product's lifecycle - from design and manufacturability to logistics and usage - enabling engineers to validate their models, plan their production processes and predict future technical failure in the field.
At the heart of digital twinning is IoT sensor technology that uses predictive models to track an object's behaviour in real-time.
Using the input gathered from the sensors of its real-world counterpart, the digital twin is then able to generate insights into a product's future performance as well as its potential pitfalls.
Predictive maintenance is one example of the use of sensor technology, in which machine data is continuously collected and then used to calculate component wear rate, production loads and product life span.
With the help of digital twinning, the machine operator is also able to predict the best time for maintenance and to avoid the risk of costly repair work.
Using the immense volume of information that is collected, it is also then possible to predict how real-time machine behaviour may be affected in any number of specific environmental conditions.
The origins and development of digital twinning
The applications of digital twinning within a manufacturing context were first raised at a Society of Manufacturing Engineers annual conference in 2002, when Dr. Michael Grieves from the University of Michigan presented his research into the data flow between real space and virtual space.
Although the technology underpinning Grieve's research was still relatively new, the potential opportunities of digital twinning had been explored many decades previously.
As early as the 1960s, researchers at NASA's space programme were building true-to-scale mockups of early space capsules at ground level, to enable them to simulate the behaviour of the systems operating above them in space.
Fast-forward to 2017 and the potential of digital twinning received a further boost, when global research and advisory company Gartner named it as one of the top ten strategic technology trends of the coming year.
Gartner predicted that billions of objects would be represented by digital twins within the subsequent three to five years, with an estimated "21 billion connected sensors and endpoints by 2020."
In a later study, released in early 2019, it also revealed that 75 percent of organisations who had implemented IoT had already used digital twinning within their processes, or had plans to do so within the next year.
How does digital twinning differ from CAD?
For manufacturing, a 3D rendering of a computer-aided design (CAD) model has long been one of the most cost-effective methods of constructing a virtual product prototype.
Where digital twinning differs however is that it is able to replicate not just the physicality, but also the dynamics, of a product or process.
Another differentiation of digital twinning is that it facilitates two-way communication between the virtual object and its real-life counterpart, enabling manufacturers to virtually test, and modify the parameters of their product.
Importantly too, a digital twin can be applied to each stage of a product's life-cycle, helping manufacturers build up a reservoir of data that is visible to all departments from sales and marketing to logistics and the supply chain.
For electronics manufacturers the applications of digital twinning are immense - providing the opportunity to boost efficiency, improve productivity, manage assets and test final products.
By choosing to first optimise their products in a virtual world, designers can create a replica digital equivalent of an actual device well before a physical version is ever put into production.
And with the help of the data that is gathered manufacturers can improve the efficiency of manufacturing, minimise downtime and continue to enhance a product even after its release.