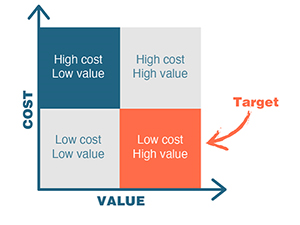
05 May 2021 | ESCATEC Mechatronics Ltd
Value Analysis and Value Engineering (VA/VE) explained for OEMs
Value Analysis and Value Engineering (VA/VA) needs to be more than a crude cost-cutting exercise led by a crusading procurement department. For OEM''s it should open up opportunities to build better value solutions that answer customer needs more creatively and efficiently.
What is Value Analysis and Value Engineering (VA/VE)?Value Engineering today is a highly evolved process for end-to-end product analysis and adaptation. It seeks to drive increased value for customers through multi-discipline, systematic, and intelligent cost reduction.
Where did VA/VE originate?
Although it’s now used in many sectors, particularly the construction industry, it was a methodology originally pioneered for the manufacturing industry by the General Electric (GE) engineer Laurence Miles during World War II.
VA/VE began as a way to source alternative materials to manufacture vital products in times of chronic, national shortage. But Miles soon discovered that his system for re-engineering products not only maintained functionality - it also saved money and, even, improved performance.
After the war he went on to perfect this approach - which he christened 'Value Analysis' (VA) as a strategic tool for manufacturers to bolster competitive advantage. VA soon become known as VA/VE - and is now referred to by practitioners simply as Value Engineering (VE).
What can Value Engineering do for OEMs today?
VE today is a defined engineering methodology that cuts the cost and improves the value of a project, product, or process through the detailed analysis of its functions.
What do we mean by value, function, and cost?
Value = What the product is worth to the customer
Function = Properties and qualities of the product
Cost= Cost of goods sold (aka COGS)
How do you calculate value?
The value of a product is calculated using a simple equation
How is value maintained or increased for a customer?
You can increase the value of a product to a customer by increasing or maintaining the function, or by reducing the cost, or by a mixture of both:
But what defines the ‘function’ of a product?
Good question.
A products’ functions are its properties and qualities. It’s what a product does for a customer, rather than its specific features. This distinction is important because it can help companies be more creative and radical in the way they reimagine their products and processes in the future.
If we think about what the customer wants and gets from the product (rather than how the product itself works), then we are free to rethink what it is made from, how it carries out its functions and even the entire way it is manufactured.
So, what’s the objective of VA/VA?
VA/VE weighs the cost/benefit ratio of every single function and component of a product. It brings in specialists from across your organisation to propose alternative materials, designs, manufacturing and more - it reduces costs while maintaining and (often) improving functionality.
Why is VE so important for OEMs right now?
In the wake of Covid-19, Brexit, and other natural and geo-political ‘earthquakes’, vulnerabilities have been exposed in supply chains and the way markets operate throughout the world.
These vulnerabilities have destroyed agility and increased costs for producers and consumers alike.
Meanwhile, automation, AI, and all the extraordinary developments of Industry 4.0 and 5.0 are dramatically eroding the profitability of traditional business models - and the products many OEMs have been happily building for years.
VE can help OEMs survive and thrive
To survive and thrive in these challenging times, therefore, OEMs can’t simply carry on developing, manufacturing and products in the same old way. They need to understand exactly where the unnecessary costs lie in their products and eliminate them - but they also need the tools to find economies in the most creative and innovative ways possible.
Dealing with the complexities of modern electronics and the contingencies of global supply chains means costs can be hidden deep inside product designs, processes, and logistics arrangements. And the multi-discipline approach of a Value Engineering project can tease out these issues, wherever these may be, and make recommendations for appropriate adaptation.
Done right, VE projects can generate spectacular cost savings through smart material substitution and process transformation, making products more competitive and commercially attractive in the process.
The challenge for many OEMs, though, is finding the time and expertise to develop the VE processes that will lever its benefits across the product life-cycle.