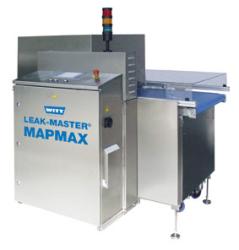
07 October 2009 | Witt Gas Techniques Ltd
Leaks in packages? Don''t get caught out!
Even the smallest leak in a package will reduce the shelf life of a product and it could turn into a very expensive return from the retailer.
Applications Specialist, Markus Mertens at Witt, the gas safety, control, mixing and analysis equipment supplier, in Witten, Germany advises food processors and producers using Modified Atmosphere Packaging (MAP), not to get caught out with leaks in packaging.Mertens discusses the various options open to packaging companies: “It is a fact that companies that pack using MAP find it difficult to estimate the risk or quantity of defective packages, rather they rely on product quality and the efficiency of the packaging process. Solid and dry products present few problems; however crumbs, traces of sauce and grease can create leakage problems on the pack seals. A micro leak will allow MAP gases to escape. When using flow wrapped packs, the risk is even higher.
Most packaging processes are reliable, however it is nearly impossible to totally eliminate all leaks. For example packaging film can develop pores either during transportation or during storage. Capillaries, which are virtually invisible to the naked eye, can form as a result of deposits on the sealing tool in the packaging equipment. Prevention is near enough impossible without monitoring the product, however quality control is the ultimate tool to ensure that leaks are found before the product is sent to the retailer.”
Mertens continues; ”Costs to undertake random sampling do remain reasonable. The equipment required is neither difficult to operate nor expensive to purchase. Using a WITT ‘PACK-VAC’ Leak Detector, the operator only has to place the package to be tested in a chamber filled with water close the lid and the equipment then removes the air above the surface of the water, which places the package under pressure and air bubbles will tell the operator, if there is a leak.
Another method of checking for leaks is using CO2, where an individual package is placed into a chamber and a vacuum is generated. The result is a pressure difference between the pressure on the inside of the chamber and the pressure in the package. If there is a leak in the package, the protective gas escapes and is instantly recognised by sensitive sensors. Carbon dioxide sensors are used, being the gas that is most frequently used in MAP packaging. This system is extremely accurate and also give the user a number of evaluation options. LEAKMASTER® is a non destructive micro-leak detection system based on this CO2 detection technology that is also capable of testing complete outer packs or E2 crates, enabling larger quantities to be randomly checked.
For automatically testing for leaks on the entire throughput of a packaging line, users can install ‘in-line’ testing systems, which - although technically more demanding - are designed primarily for high volume packaging operations as well as products that are more sensitive to leakages. The Witt LEAK-MASTER® MAP-MAX is a fully automatic detection system that is capable of operating at up to 15 cycles per minute and can check the complete throughput from a thermoforming packaging line. It is also able to test complete cases of form, fill and seal packages.”
As far as the costs are concerned, some producers might decide to leave out leak tests altogether. Here Mertens has a very defined view: “If the processor wants to take the risk that is OK, however experience and time has shown that sooner or later he will get caught short. It is a simple question of probabilities. The issue is not the cost for the leak tests. Everyone knows the value of a batch. The value and quality of the brand is paramount. If a leak detector prevents one single rejected delivery, it has paid for itself immediately. At Witt we recommend that if anyone does do not have any leak detector system in operation, that they should at least start with simple water immersion test equipment, to give them some assurance. Every quality check, however small, increases the brand value in the market.”