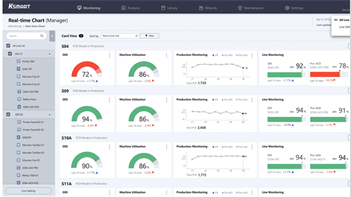
06 February 2024 | ESCATEC Mechatronics Ltd
Does AI boost efficiency in surface mount device production?
Recently we spoke to Dr Julia Traut, Head of Marketing and Product Management at SmartRep.
SmartRep is a technical distributor of manufacturing equipment and process systems for electronics production. Its headquarters are in Hanau, near Frankfurt in Germany. She elaborates on the role AI plays in today’s SmartFactories.Does the concept of SmartFactory conjure images of a barren, austere environment where machines solely cater to other machines? While it may sound like the premise of a dystopian science fiction novel, could the advancements in artificial intelligence (AI) make it an impending reality?
Ironically AI is not just becoming indispensable in surface mount device (SMD) manufacturing, it also underscores the value of skilled workers.
Prominent SMD equipment brands like Koh Young have integrated artificial intelligence to enhance production efficiency. Andreas Keller, CEO of SmartRep (a distributor for Koh Young in German-speaking regions and machine supplier for ESCATEC Switzerland), emphasises, "Using artificial intelligence in the SMD realm is not about replacing humans with algorithms and automation. The current state of AI also doesn't support such a replacement. But in the current shortage of skilled workers, algorithms and automation help to ensure that technical experts have time to make the important decisions with their expertise and based on data.”
AI Algorithms and SMD
In the SMD realm, AI is used in two ways: Machines decide on algorithm-based mathematical models and use machine learning technology. For example, an Automatic Optical Inspection System (AOI) checks a component on a PCB in 3D. Simple algorithms only check whether the measured values are within the process window. However, AI could recognise an emerging pattern and seek the underlying cause of deviations.
By analysing multiple data sources from other systems of the SMD line, AI can suggest actionable insights. For example, Koh Young's Process Optimizer can proactively identify areas of improvement before a process goes awry, ensuring consistent manufacturing quality.
AI detects a developing pattern
Let’s look at an example:
An Automatic Optical Inspection system (AOI) examines a component on a circuit board in 3D, verifying its placement, polarity, and dimensions. Although the solder rise may not be perfect, it's within the acceptable range, prompting the AOI to label it as 'Good' and advance the PCB to the subsequent stage. However, upon inspecting the next PCB, it notices the component nearing the upper limit of the acceptable process window. While basic algorithms might still give a 'Good' verdict, AI detects a developing pattern. It probes deeper to identify potential issues - could it be a dirty stencil in the printer, or perhaps an imprecise temperature in a soldering oven section?
Using extensive data analysis, AI discerns underlying causes and suggests corrective actions. In this scenario, as the PCB edges towards the process window's limit, Koh Young's Process Optimizer (KPO) steps in. Recognising the trend, KPO pinpoints areas for enhancement, preventing the manufacturing process from faltering. This proactive approach not only eases the workload for staff but also curtails costs by eliminating any production of defective boards.
Deep learning AI
Deep learning emulates human neural networks, enabling machines to learn and make independent deductions. Just as a child learns to differentiate between a cat and a dog after seeing multiple images, deep learning helps machines identify patterns.
In SMD manufacturing, this type of AI is exemplified in Koh Young's Auto Programming function. This allows AOI systems to autonomously program themselves for new assemblies, recognising components and determining tolerances based on historical data. It reduces the manual workload, freeing resources for more critical manufacturing tasks.
AI excels in spotting irregularities within this data deluge, identifying patterns, predicting errors, and alerting operators.
To break it down: What capabilities does AI bring to SMD, and where are its limitations? AI shines when handling vast quantities of data, a scenario often seen in SMD as every processing machine constantly collects information. Consider this illustration: Imagine a printed circuit board with 1000 pads. For each, the SPI measures five attributes: volume, area, height, and X & Y offsets, totalling 5,000 values. Post-assembly, the AOI assesses additional attributes, such as offsets, rotation, polarity, and so on. With roughly 400 components on the board, this translates to another 4,000 values. Factor in data from the printer, the pick-and-place machine, and the soldering oven, and you're looking at more than 20,000 data points for a single board - all in a cycle time of just 20 seconds.
Could a human process this in real time?
AI excels in spotting irregularities within this data deluge, identifying patterns, predicting errors, and alerting operators. Experience and know-how can't match this efficiency, and it's certainly beyond the capacity of manual calculations.
AI in SMD: What's feasible and what's not?
The SMD manufacturing process generates vast amounts of data. Just consider: a single printed circuit board can produce over 20,000 data points. Such massive datasets are where AI thrives. Its ability to discern manufacturing anomalies, predict errors, and raise alerts from this data is unparalleled.
Conclusion
In conclusion, while AI's proficiency in handling data explains its burgeoning presence in SMD manufacturing, it doesn't mean that humans are superfluous. Quite the opposite. AI gives people time to make the important decisions. Human intervention is still required at critical points. The AI takes care of the simple things. Machines are adept at crunching numbers, but skilled workers' nuanced understanding and expertise remain irreplaceable in manufacturing.