Understanding and preventing load cell overload
31 July 2024
Overload detection is crucial for maintaining the load cell’s integrity, accuracy, and health. Properly detecting and handling overload conditions can prevent permanent damage and ensure the sensor’s longevity.
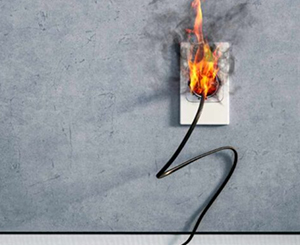
Overloading is not a new concept in measurement. You could say that overload protection is in Interface’s DNA. Interface founder and inventor Richard F. Caris patented a weighing apparatus with overload protection for off-centre loading in 1983. In 2004, Interface engineer and force measurement expert LaVar Clegg patented Interface’s load cells with overload protection. Interface’s engineering team of LaVar Clegg and Larry Burrow followed up by receiving a 2012 patent that protected the intellectual property of load cells for monitoring torsion and overload protection.
Overload protection is not just a theoretical concept; it’s a practical design feature of a load cell. At Interface, we’ve made it easy for you to identify load cells with overload protection. This feature is indicated in the model’s name and feature specifications, such as 3X overload protection or 10X overload protection. Whether you’re working in high-stress applications or simply want to ensure the longevity and accuracy of your load cells, this feature provides you with the peace of mind that your equipment is protected.
What Is Overload?
In simple terms, overload occurs when the load applied to a load cell exceeds its rated capacity. This can lead to permanent sensor deformation, disrupting the carefully balanced processing that ensures accurate data. The consequences of overloading are not just detrimental; they can be potentially catastrophic. Overloading can compromise the structural integrity of the load cell itself, leading to significant damage and potential system failure. This underscores the importance of understanding and managing overload conditions and the value of reliable overload protection in your load cells.
A computed zero offset greater than 20% clearly indicates overload. If the computed zero balance is between 10% and 20%, it indicates a probable overload. It’s important to note that such mechanical damage is typically irreversible. While it might be possible to electrically re-zero the load cell, this does not restore the affected performance parameters, underscoring the need for caution and proper handling.
Another type of potentially more dangerous overload is an impact load. Impact loads are sudden forces that can cause significant damage to load cells. If the live end of the cell moves more than 150% of its full capacity deflection relative to the dead end, the cell could be overloaded regardless of the impact duration. The forces generated by impact loads can be extraordinarily high, leading to potential overload and subsequent damage.
Handling Extraneous Loads
Extraneous loads, such as side loads, moments, or torques, can also affect a load cell’s performance. These off-axis vectors add to the on-axis load vector, potentially causing an overload condition in one or more gaged areas in the flexure. To determine the allowed on-axis overload capacity when extraneous loads are present, compute the on-axis component of these loads and subtract them from the rated overload capacity.
SMT Overload Protected S-Cell
SMT Overload Protected S-CellThe incorporation of overload protection is a significant innovation in Interface S-Cell design. By removing the large gaps at the top and bottom of the cell and replacing them with small clearance gaps and locking fingers, the whole cell can be made to “go solid” in either mode (tension or compression) before the deflection of the gaged area exceeds the allowed overload specification. The double-stepped shape of the gaps in an S-cell design is necessary to ensure that overload protection operates in both modes.
The SMT Series is ideally suited for applications that may generate forces as high as eight times the load cell’s rating. The two loading holes are vertically aligned, making the cell easy to design into machines that apply reciprocating or linear motion, either from a rotating crank or a pneumatic or hydraulic cylinder.
SMT SeriesThe covers provide physical protection for the flexure, but the cell is not sealed. Therefore, users should be cautioned not to use it in dusty applications that might build up dust collections in the overload gaps. Should a buildup occur, the overload protection would come into effect before the load reaches the rated capacity, thus causing a non-linear output.
The SMT Series is especially suited for laboratories or medical facilities where untrained or non-technical personnel could accidentally apply large loads.
Overload Preventive Measures
#1 Review Safe Overload Specification
Start with the basics by reviewing the specifications of every load cell to understand the capacity range of the sensor. Interface states the overload protection value in the product description, features, and specification datasheet. Reference the mechanical specification of Safe Overload – %CAP for the values.
#2 Use of Interface Overload Protected Load Cells
Interface offers load cells designed with overload protection. This feature limits the travel of the centre hub under load and prevents further deflection once a specific limit is reached. This is particularly useful in applications where high impact or sudden loads are expected.
#3 Regular Maintenance and Calibration
Regular checks using tools like ohm meters can help in the early detection of overload conditions. Insulation resistance tests can also identify potential issues that might indicate overload or other electrical problems.
TIP: Calibrate your load cells at least once a year for accuracy and performance maintenance.
Overload detection and management are essential for ensuring a load cell’s reliable performance and longevity. By understanding the signs of overload, managing impact loads, and employing preventive measures, users can maintain the integrity of their measurement systems. Regular maintenance and proper design considerations are vital to avoiding the detrimental effects of overload and ensuring accurate, long-term performance of load cells.
By adhering to these guidelines, industries can ensure their load cells continue to function accurately and reliably, thereby maintaining the overall integrity of their testing and measurement systems.
Other Press Releases By This Company
- 03/12/2024 - Accelerating excellence at an automotive testing lab
- 02/10/2024 - Revolutionise your calibration process With the 1800 Series Load Cell
- 03/09/2024 - Optimise textile manufacturing With precision load cells & force measurement
- 26/06/2024 - Experience precision:
- 23/05/2024 - Engineering & Manufacturing 2024 / Smart Factory Expo
- 08/04/2024 - How Cadbury solved the cracking Easter egg delivery problem
- 23/02/2024 - The new remote monitoring solution form Interface Force
- 24/01/2024 - Multi-axis sensors + DAQ systems go hand in hand
Released By
Interface Force Measurements Ltd